Embedded Components PCB Manufacturing
Embedded Components PCB Manufacturing,Embedded Components PCBs revolutionize traditional circuit board designs by integrating electronic components directly into the layers of the board itself. Unlike conventional PCBs where components are surface-mounted, Embedded Components PCBs embed resistors, capacitors, and even some active components within the substrate material during fabrication. This innovative approach offers numerous advantages, including space-saving designs, enhanced reliability, improved signal integrity, and potentially lower assembly costs. By eliminating the need for bulky surface-mounted components, Embedded Components PCBs enable more compact and lightweight electronic devices without compromising functionality or performance. Additionally, embedding components within the layers of the PCB provides protection against environmental factors such as vibration, moisture, and temperature fluctuations, ultimately enhancing the durability and longevity of electronic products. With their versatility and efficiency, Embedded Components PCBs are increasingly favored in various industries, including consumer electronics, automotive, medical devices, aerospace, and telecommunications.
What is an Embedded Components PCB?
An Embedded Components PCB (Printed Circuit Board) refers to a type of circuit board where electronic components are directly embedded within the substrate material of the board itself, rather than being mounted onto the surface of the board as discrete components.
In traditional PCB manufacturing, electronic components such as resistors, capacitors, and integrated circuits are soldered onto the surface of the board. However, in Embedded Components PCBs, these components are integrated into the layers of the PCB during the manufacturing process. This integration offers several potential advantages:
- Space Saving: By embedding components within the layers of the PCB, the need for surface-mounted components is reduced or eliminated, allowing for more compact designs and potentially smaller overall product sizes.
- Reduced Assembly Time: Since many components are already integrated into the board during manufacturing, assembly time can be reduced, as there are fewer components to place and solder onto the board.
- Improved Signal Integrity: Embedding components within the PCB can reduce parasitic effects such as inductance and capacitance, potentially improving signal integrity and reducing electromagnetic interference.
- Enhanced Reliability: Embedding components can protect them from environmental factors such as vibration, moisture, and temperature fluctuations, potentially enhancing the reliability and durability of the finished product.
- Cost Savings: While the initial cost of manufacturing Embedded Components PCBs may be higher due to the complexity of the process, savings may be realized in terms of reduced assembly costs, lower component costs (since fewer discrete components are needed), and potentially fewer defects during assembly.
Overall, Embedded Components PCBs offer a way to achieve more compact, reliable, and potentially cost-effective electronic designs by integrating components directly into the structure of the circuit board itself.
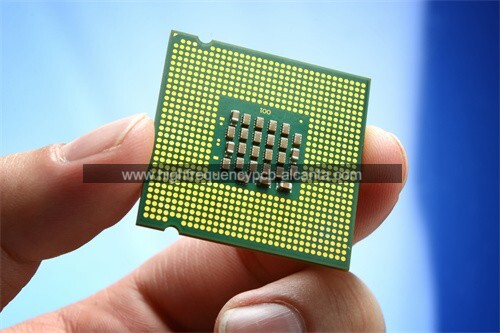
Embedded Components PCB Manufacturing
What are the PCB Design Guidelines?
PCB design guidelines are a set of principles and best practices followed by engineers and designers during the process of creating printed circuit board layouts. These guidelines aim to ensure the functionality, reliability, manufacturability, and performance of the PCB. Some common PCB design guidelines include:
- Component Placement: Proper placement of components on the PCB to minimize signal interference, optimize signal paths, and ensure efficient use of board space.
- Routing: Careful routing of traces to minimize signal distortion, noise, and crosstalk. This includes considerations such as trace length matching, impedance control, and avoiding sharp corners or right angles.
- Power and Ground Planes: Designing adequate power and ground planes to provide stable power distribution, reduce noise, and minimize signal return paths.
- Signal Integrity: Ensuring signal integrity by maintaining controlled impedance, minimizing signal reflections, and avoiding signal coupling between traces.
- Thermal Management: Implementing strategies for efficient heat dissipation, such as adding thermal vias, thermal pads, and proper placement of components to avoid hot spots.
- Design for Manufacturability (DFM): Following DFM guidelines to ensure that the PCB design can be easily manufactured with high yield and minimal defects. This includes considerations such as minimum trace widths, appropriate annular ring sizes, and proper spacing between components.
- Electromagnetic Compatibility (EMC): Designing the PCB to minimize electromagnetic interference (EMI) and ensure compliance with regulatory EMC standards. This includes proper grounding, shielding, and layout techniques to mitigate EMI.
- Assembly Considerations: Designing for ease of assembly by selecting components with suitable package sizes, optimizing component orientation for automated assembly, and providing adequate clearance for soldering.
- Testing Provisions: Incorporating test points, JTAG headers, or other testing provisions to facilitate PCB testing, debugging, and troubleshooting.
- Documentation: Providing comprehensive documentation including schematic diagrams, bill of materials (BOM), assembly drawings, and fabrication files to aid in manufacturing and assembly processes.
These guidelines help ensure that the PCB meets the requirements of the intended application while also considering factors such as cost, reliability, and time-to-market. Adhering to these principles can result in a well-designed PCB that functions reliably and can be manufactured efficiently.
What is the Embedded Components PCB Fabrication Process?
The fabrication process for Embedded Components PCB involves integrating electronic components directly into the layers of the PCB during manufacturing. Here’s an overview of the typical steps involved:
- Design: The process starts with the design of the PCB layout, including the placement of components and routing of traces. Designers must plan for the embedding of components within the layers of the PCB, considering factors such as component size, type, and orientation.
- Substrate Preparation: The base material for the PCB, usually a laminate composed of layers of copper and insulating substrate (such as fiberglass epoxy), is prepared. The layers are typically pre-bonded together to form a solid substrate.
- Component Embedding: Specialized equipment is used to embed electronic components directly into the layers of the PCB substrate. This process typically involves laser drilling or milling cavities within the substrate where components will be placed. Components such as resistors, capacitors, and integrated circuits are then inserted into these cavities.
- Connection Formation: Conductive traces are formed on the surface layers of the PCB substrate using techniques such as copper deposition, etching, or additive manufacturing processes like inkjet printing. These traces establish electrical connections between the embedded components and other external components.
- Layer Bonding: Once the components and conductive traces are in place, the layers of the PCB substrate are bonded together to form a single integrated structure. This may involve the application of heat and pressure to ensure proper adhesion between layers.
- Final Processing: After bonding, the PCB undergoes final processing steps such as surface finishing (e.g., solder mask application, copper plating), routing of outer layer traces, and drilling of mounting holes and vias.
- Testing and Inspection: The fabricated Embedded Components PCB undergoes rigorous testing and inspection to ensure that all embedded components are properly connected, and the board meets quality standards and specifications. This may include electrical testing, visual inspection, and functional testing.
- Assembly: Once the PCB passes testing and inspection, it is ready for component assembly. Additional surface-mounted or through-hole components may be soldered onto the PCB as needed to complete the circuit.
- Final Testing: The assembled PCB undergoes final testing to verify its functionality and performance in the intended application.
The fabrication process for Embedded Components PCBs requires specialized equipment and expertise due to the intricacies of embedding components within the layers of the PCB substrate. However, when executed successfully, it can result in compact, reliable, and high-performance electronic designs.
How do you manufacture an Embedded Components PCB?
Manufacturing an Embedded Components PCB involves integrating electronic components directly into the layers of the PCB during the fabrication process. Here’s a general overview of the manufacturing process:
- Design Stage: The process begins with the design of the PCB layout, including the placement of embedded components within the layers. Specialized CAD software is typically used for this purpose.
- Material Selection: High-quality substrate materials compatible with embedding components, such as epoxy-based or composite materials, are chosen for the PCB.
- Component Embedding: Components such as resistors, capacitors, and integrated circuits are embedded within the layers of the PCB during fabrication. This can be achieved using various techniques such as:
Semi-Additive Process (SAP): This involves selectively depositing conductive and dielectric materials to form circuit traces and embed components within the layers.
Laser Direct Structuring (LDS): Laser beams are used to activate special additives in the substrate material, allowing for the selective metallization of areas where components are to be embedded.
Sequential Lamination: Components are embedded between layers during the lamination process by placing them between pre-impregnated core materials before pressing them together under heat and pressure.
- Lamination: The layers of the PCB, including the embedded components, are laminated together using heat and pressure to form a single multilayered structure.
- Drilling and Plating: After lamination, holes are drilled through the PCB to create vias for interconnecting layers. These vias are then plated with conductive material to establish electrical connections.
- Circuit Patterning: Circuit patterns are created on the outer layers of the PCB using processes such as etching or deposition of conductive material.
- Surface Finish and Coating: Surface finish is applied to protect exposed copper surfaces and provide solderability. A protective coating may also be applied to the PCB for additional protection against environmental factors.
- Final Inspection and Testing: The finished PCB undergoes thorough inspection and testing to ensure that embedded components are properly integrated, circuit connections are intact, and the PCB meets the required specifications.
- Assembly: After fabrication, the PCB may undergo assembly processes where additional surface-mounted components are soldered onto the board, depending on the specific requirements of the electronic product.
- Quality Control: Throughout the manufacturing process, quality control measures are implemented to identify and rectify any defects or issues that may arise, ensuring the final product meets quality standards.
By following these steps, manufacturers can produce Embedded Components PCBs that offer compact designs, improved reliability, and enhanced performance for various electronic applications.
How much should an Embedded Components PCB cost?
The cost of an Embedded Components PCB can vary widely depending on several factors:
- Complexity: The complexity of the PCB design, including the number of layers, the density of components, and the intricacy of the embedded component integration, can significantly impact the cost. More complex designs generally require more advanced manufacturing processes and materials, which can increase the overall cost.
- Materials: The choice of materials for the PCB substrate, embedded components, and surface finish can influence the cost. High-quality materials may command a higher price but can offer improved performance and reliability.
- Manufacturing Process: The specific manufacturing processes used to fabricate the Embedded Components PCB, such as semi-additive processes or laser direct structuring, can affect the cost. More sophisticated processes may require specialized equipment and expertise, contributing to higher manufacturing costs.
- Volume: The volume of PCBs being produced can impact the unit cost. Larger production runs typically result in lower per-unit costs due to economies of scale, while smaller runs may incur higher setup and tooling costs per unit.
- Lead Time: Expedited manufacturing or delivery options may come at an additional cost. Longer lead times may offer cost savings but could impact project timelines.
- Additional Services: Additional services such as design consultation, testing, and assembly can add to the overall cost of the PCB.
As a rough estimate, Embedded Components PCBs can range in cost from a few dollars for simple designs with low volumes to several hundred dollars or more for complex designs with high volumes or specialized requirements. It’s essential to work closely with a reputable PCB manufacturer to obtain an accurate cost estimate based on your specific design and production needs.
What is the Embedded Components PCB base material?
The base material for Embedded Components PCBs typically consists of specialized substrates that are compatible with embedding electronic components within the layers of the PCB. Common base materials used for Embedded Components PCBs include:
- Epoxy-based Materials: Epoxy resins are frequently used as the base material for Embedded Components PCBs due to their excellent adhesion properties, mechanical strength, and compatibility with embedding techniques such as laser direct structuring (LDS) or semi-additive processes (SAP).
- Composite Materials: Composite substrates, which combine epoxy resins with reinforcing materials such as glass fibers (FR-4) or woven aramid fibers (e.g., Arlon), are also commonly used for Embedded Components PCBs. These materials offer enhanced mechanical properties and dimensional stability while still allowing for embedded component integration.
- Ceramic-based Materials: Some advanced Embedded Components PCBs may utilize ceramic-based substrates for their excellent thermal conductivity, high temperature resistance, and dielectric properties. Ceramic substrates are particularly suitable for applications requiring superior thermal management or high-frequency performance.
- Polyimide-based Materials: Polyimide substrates, known for their flexibility, high-temperature resistance, and excellent electrical properties, can also be used for Embedded Components PCBs in certain applications where flexibility or resistance to harsh environments is required.
The choice of base material depends on factors such as the specific requirements of the application, the desired electrical and mechanical properties, thermal management considerations, and the compatibility with the chosen embedding techniques. It’s essential to select a base material that provides the necessary characteristics to achieve the desired performance and reliability of the Embedded Components PCB.
Which company makes Embedded Components PCB?
Our Manufacturing Embedded Components PCBs typically requires advanced technology and specialized equipment, thus only a few specialized PCB manufacturing companies are capable of producing such products. Among them, some internationally renowned PCB manufacturers and technology-leading companies have extensive experience and expertise in this field. Some famous Embedded Components PCB manufacturers include Mitsui Chemicals in Japan, TTM Technologies in the United States, and LPKF Laser & Electronics in Germany.
However, to stand out in the market, our company possesses top-notch technical teams and advanced production equipment, enabling us to undertake the manufacturing of Embedded Components PCBs. With years of experience in PCB manufacturing, our company enjoys a good reputation within the industry. We emphasize technological innovation and quality control, committed to providing customers with high-quality, high-performance solutions for Embedded Components PCBs.
Equipped with advanced production lines and equipment, we can meet various manufacturing requirements for complex PCBs. Our technical team has rich experience and professional knowledge to provide customers with customized Embedded Components PCB design and manufacturing solutions. Whether in material selection, process flow, or quality control, we ensure the high quality and reliability of our products.
Moreover, we also value customer service and communication, able to respond promptly to customer needs and provide comprehensive technical support and services. We understand that customer satisfaction is our greatest pursuit; therefore, we are committed to continuously improving product quality and service levels to provide customers with better Embedded Components PCB solutions.
In summary, our company has the technology and capability to manufacture Embedded Components PCBs and is dedicated to providing customers with high-quality, high-performance customized solutions. We are willing to work hand in hand with customers, achieve mutual development, and realize a win-win situation.
What are the 7 qualities of good customer service?
Good customer service is characterized by several key qualities that contribute to a positive experience for customers. Here are seven essential qualities:
1. Responsiveness: Good customer service involves being prompt and responsive to customer inquiries, concerns, and requests. Customers appreciate timely assistance and solutions to their problems.
2. Empathy: Empathy is crucial in understanding and addressing customers’ emotions, concerns, and needs. Customer service representatives who demonstrate empathy can build rapport and trust with customers, leading to better outcomes.
3. Clear Communication: Effective communication is essential for conveying information, providing instructions, and resolving issues. Clear and concise communication helps avoid misunderstandings and ensures that customers receive the assistance they need.
4. Professionalism: Professionalism involves maintaining a courteous and respectful demeanor when interacting with customers, regardless of the situation. It includes adhering to company policies, maintaining confidentiality, and striving to resolve issues efficiently.
5. Knowledgeability: Customer service representatives should have a thorough understanding of the products or services offered by the company. Being knowledgeable allows them to provide accurate information, answer questions, and offer helpful recommendations to customers.
6. Problem-Solving Skills: Good customer service involves effectively addressing customer concerns and resolving issues in a timely manner. Customer service representatives should be proactive in identifying solutions and taking appropriate action to ensure customer satisfaction.
7. Follow-Up: Following up with customers after resolving their issues or completing a transaction demonstrates care and commitment to their satisfaction. Following up can involve checking if the customer’s needs were met, seeking feedback, or providing additional assistance if necessary.
By embodying these qualities, businesses can deliver exceptional customer service experiences that foster loyalty, positive word-of-mouth referrals, and long-term success.
FAQs
What are Embedded Components PCBs?
Embedded Components PCBs refer to printed circuit boards where electronic components are directly embedded within the layers of the board itself, rather than being mounted onto the surface.
What are the benefits of Embedded Components PCBs?
Embedded Components PCBs offer advantages such as space savings, improved reliability, enhanced signal integrity, and potentially lower assembly costs.
How are components embedded into the PCB?
Components are embedded using specialized processes such as semi-additive processes (SAP), laser direct structuring (LDS), or sequential lamination during PCB fabrication.
What types of components can be embedded?
Various passive components such as resistors, capacitors, and inductors, as well as some types of active components like integrated circuits (ICs), can be embedded into the PCB.
What materials are used for Embedded Components PCBs?
Common base materials include epoxy-based substrates, composite materials (e.g., FR-4), ceramic-based substrates, and polyimide-based materials, depending on the specific application requirements.
How does the cost of Embedded Components PCBs compare to traditional PCBs?