Embedded Cavity Substrate Manufacturer
Embedded Cavity Substrate Manufacturer,Embedded Cavity Substrate integrates recessed areas within the substrate, offering a compact and efficient packaging solution for electronic devices. These embedded cavities provide space for mounting components or modules, optimizing space utilization and supporting miniaturization. By housing components within the substrate, this design reduces the overall footprint of the package while enhancing thermal management and protecting sensitive components. Embedded Cavity Substrates are crucial for high-density applications in sectors such as telecommunications, automotive, and aerospace, where space constraints and performance are critical considerations. This technology enables advanced miniaturization and integration, driving innovation in modern electronic device manufacturing.
“Embedded Cavity Substrate” refers to an innovative technology commonly employed in the realms of microelectronics and radio frequency (RF). Its core purpose is to introduce an embedded cavity structure within integrated circuits (IC) or RF modules, aiming to elevate performance levels while concurrently mitigating the impact of electromagnetic interference.
In the conventional landscape of electronic devices, the close proximity of electronic components often gives rise to undesirable phenomena such as signal interference and power losses. Embedded Cavity Substrate counteracts these challenges by ingeniously integrating a cavity or hollow structure into the substrate. This structural augmentation serves to effectively isolate different circuits or components, thereby minimizing mutual interference. The resultant benefits encompass a reduction in electromagnetic interference, an enhancement of signal integrity, and a partial optimization of RF performance.
The implementation of this technology involves the creation of a three-dimensional space within the substrate to accommodate specific components or circuits. This process may necessitate the utilization of specialized materials or design techniques to ensure optimal performance within the desired frequency range. By embedding circuits within the cavity, the sensitivity of the overall system to its surrounding environment is diminished, contributing to an improved stability and reliability profile.
Embedded Cavity Substrate finds versatile applications across domains such as communication devices, radar systems, and wireless communication modules. This technological paradigm shift empowers engineers to craft designs that are not only highly integrated but also characterized by enhanced reliability and performance.
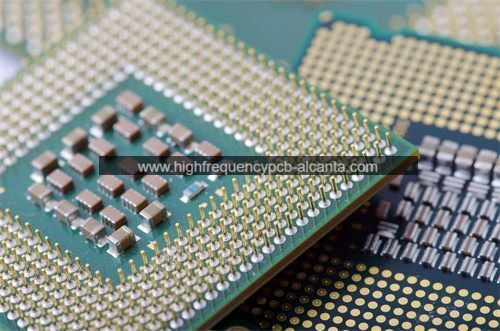
Embedded Cavity Substrate Manufacturer
What are the Functions of Embedded Cavity Substrate?
Embedded Cavity Substrate serves as a multifaceted solution within the realm of electronic systems, delivering a range of essential functions:
EMI Mitigation:
A core function is the reduction of Electromagnetic Interference (EMI). Through the integration of an embedded cavity structure, the technology effectively isolates circuits and components, curbing disruptive electromagnetic signals.
Signal Fidelity Enhancement:
Another critical role is the enhancement of signal integrity. By minimizing the impact of noise and interference, Embedded Cavity Substrate contributes to maintaining the quality and reliability of signals circulating within electronic systems.
Power Efficiency Optimization:
The technology plays a role in improving power integrity by creating a controlled environment for power distribution. This aids in stabilizing power delivery and minimizing losses associated with closely arranged electronic components.
RF Module Performance Boost:
In radio frequency applications, the embedded cavity structure optimizes the performance of RF modules. This is achieved by isolating RF components from external interference, leading to superior transmission and reception characteristics.
Efficient Thermal Regulation:
Utilizing the three-dimensional space it creates, Embedded Cavity Substrate contributes to enhanced thermal management. This capability facilitates more effective heat dissipation, crucial for preventing overheating and ensuring the consistent operation of electronic components.
Isolation for Sensitivity:
The technology enables the isolation of sensitive components or circuits from external factors, safeguarding their functionality against environmental conditions or adjacent electronic elements.
Augmentation of Stability and Reliability:
By minimizing interference and optimizing operating conditions for electronic components, Embedded Cavity Substrate significantly enhances the overall stability and reliability of electronic systems. This is particularly pivotal in applications where unwavering performance is paramount.
In essence, Embedded Cavity Substrate emerges as a strategic design element, adept at addressing challenges tied to electromagnetic interference, signal fidelity, power distribution, thermal dynamics, and the overarching stability of electronic systems. Its versatile applications extend across industries where high-performance and dependable electronic systems are imperative.
What are the Different Types of Embedded Cavity Substrate?
Embedded Cavity Substrate is an ingenious concept that takes on various forms, adapting to the unique demands of microelectronics and RF design. While not a rigidly defined technology, it unfolds in diverse types, each crafted with precision for specific applications:
Harmony in RF with Cavity-Backed Antennas:
Picture a dance between cavities and antennas in RF design. Cavity-backed antennas, with strategically embedded spaces beneath them, elevate the choreography, enhancing radiation efficiency and the overall performance of the antennas.
Frequency Precision in RF Filter Cavities:
Here, cavities step into the spotlight to create RF filters, akin to musical notes finely tuned for precision. These embedded structures isolate and filter specific frequencies, allowing electronic systems to play their unique frequencies with accuracy.
Thermal Ballet in Thermal Management Cavities:
In a ballet of heat dissipation, cavities take center stage in thermal management. Designed to waltz with temperature dynamics, these cavities gracefully dissipate heat, preventing overheating and ensuring the electronic ensemble performs in perfect harmony.
Protective Symphony with Shielding Cavities:
Imagine a protective symphony where cavities act as shields. These embedded compartments guard sensitive components, creating a shielded environment that deflects interference, ensuring a serene performance free from disruptive electromagnetic noise.
Resonance Elegance in Resonant Cavities:
Resonant cavities join the orchestra of RF and microwave circuits, adding an element of elegance. Tuned for specific resonances, these cavities contribute to a harmonious frequency response, creating a musical composition of precise electronic frequencies.
EMI Shielding Opera with EMI Shielding Cavities:
The drama unfolds as cavities take the stage for an EMI shielding opera. Strategically positioned, these cavities act as shields against the tumultuous waves of electromagnetic interference, ensuring an uninterrupted electronic performance.
Acoustic Sonata with Acoustic Cavities:
In the world of MEMS and sensors, cavities craft an acoustic sonata. Engineered to enhance sound, these cavities play a pivotal role in applications such as microphones, contributing to a symphony of finely tuned acoustic properties.
Power Distribution Waltz in Power Distribution Cavities:
Envision a waltz of power distribution, choreographed by embedded cavities. These cavities ensure a controlled and efficient flow of power, orchestrating a dance that powers different components within the substrate with grace and precision.
Embedded Cavity Substrate thus becomes not just a technology but a stage for innovation, where engineers compose intricate performances tailored to the unique demands of their applications. Like a versatile conductor, it orchestrates a symphony of functionalities, each playing its part in the grand performance of electronic systems.
What is the Relationship Between Embedded Cavity Substrate and IC Packaging?
Embedded Cavity Substrate and IC packaging engage in a collaborative dance, each contributing unique moves to the intricate choreography of electronic system design. Their relationship is more than mere coexistence; it’s a synchronized performance aimed at enhancing the efficiency, resilience, and functionality of integrated circuits within electronic devices. Let’s unravel the dynamic interplay between these two elements:
Packaging Fusion:
IC packaging serves as the protective shell for integrated circuits, and Embedded Cavity Substrate seamlessly integrates into this packaging framework. Together, they form a fusion that goes beyond mere encapsulation, creating a space where functionality and protection coalesce.
Heat Management Ballet:
Picture a ballet of thermal dynamics where Embedded Cavity Substrate takes the lead. Cavities strategically designed within the IC packaging choreograph an elegant dance of heat dissipation, ensuring the temperature stays in tune for optimal circuit performance without missing a beat.
Signal Integrity Waltz:
In the waltz of signals, Embedded Cavity Substrate and IC packaging perform a harmonious dance to maintain signal integrity. The cavities, like skilled partners, minimize interference and disruptions, allowing for a seamless waltz of data and frequencies, especially crucial in the realm of RF applications.
Tailoring for Application Spotlight:
IC packaging, adorned with Embedded Cavity Substrate, becomes a master tailor crafting bespoke designs for specific applications. The collaboration allows for customization, ensuring the packaging aligns perfectly with the unique demands of the electronic device, whether it’s creating resonance for RF or safeguarding delicate components.
Efficiency in Compact Choreography:
The duet of Embedded Cavity Substrate and IC packaging engages in a compact choreography of design efficiency. Cavities strategically placed within the packaging enable a synchronized integration of components, minimizing interference and maximizing the use of space, resulting in a performance that is both efficient and impactful.
Guardianship of Sensitivity:
Together, they play the role of guardians, ensuring the protection of sensitive components within the electronic ensemble. Embedded Cavity Substrate, as part of IC packaging, acts as a shield, creating a secure environment that fosters the optimal performance of delicate elements.
Symphony of System Synergy:
The collaborative efforts crescendo into a symphony of system synergy. Embedded Cavity Substrate and IC packaging, working in unison, address thermal challenges, optimize RF capabilities, and fortify the overall reliability and functionality of electronic devices with a harmonious blend of precision and coordination.
In this intricate dance of technology, Embedded Cavity Substrate and IC packaging create a performance that transcends functionality — it’s a symphony of innovation and resilience on the grand stage of electronic system design.
How Does Embedded Cavity Substrate Differ from Traditional PCBs?
Embedded Cavity Substrate and traditional Printed Circuit Boards (PCBs) are distinct entities in the realm of electronic design, akin to protagonists with different scripts in a theatrical production. Let’s explore the narrative of these two technologies, each playing a unique role:
Structural Composition:
Embedded Cavity Substrate: Imagine a canvas with intentional cavities, sculpted with precision to serve as the backdrop for an intricate play. These hollow structures are not just physical spaces; they are architectural elements designed for a specific purpose, such as the management of heat, the reduction of electromagnetic interference, or the optimization of radio frequency performance.
Traditional PCBs: In contrast, the traditional PCB takes on the role of a foundational platform, a reliable stage where electronic components perform without the intentional incorporation of complex hollow structures. It’s a canvas that supports the general choreography of electronic circuitry.
Functional Symphony:
Embedded Cavity Substrate: Stepping into the limelight, Embedded Cavity Substrate is the virtuoso, delivering a symphony of advanced functionalities. It caters to the demands of specialized applications, offering superior thermal dissipation, targeted reduction of electromagnetic interference, and finely tuned responses in radio frequency domains.
Traditional PCBs: The unsung hero, traditional PCBs play a vital but understated role, providing the rhythm and melody for a wide array of electronic devices. Their functionality is more generic, offering a reliable canvas for everyday electronic circuitry.
Performance Venue:
Embedded Cavity Substrate: Picture a grand stage where technological intricacies take center stage. Embedded Cavity Substrate is the star performer in applications that demand precision, such as RF and microwave circuits, communication devices, and radar systems, where the nuances of thermal and electromagnetic landscapes matter.
Traditional PCBs: Versatile and adaptable, traditional PCBs take on supporting roles across diverse applications. They contribute to the orchestration of electronic devices, whether in consumer electronics or industrial machinery, where reliability and simplicity are the main themes.
Cost and Complexity Choreography:
Embedded Cavity Substrate: The ballet of complexity unfolds, leading to a higher production cost. However, this investment is justified by the intricate dance of design and functionality that Embedded Cavity Substrate brings to the electronic performance.
Traditional PCBs: Masters of simplicity, traditional PCBs follow a well-established choreography in manufacturing, resulting in a cost-effective solution for standard electronic applications.
Design Flexibility Sonata:
Embedded Cavity Substrate: A soloist with a composition of design flexibility, Embedded Cavity Substrate allows engineers to compose a symphony of customization. The intentional integration of cavities enables a tailored performance, addressing the unique needs of sophisticated electronic systems.
Traditional PCBs: Part of the ensemble, traditional PCBs contribute to the overall harmony of design but may lack the soloist’s finesse when it comes to catering to specific functionalities like thermal management or RF optimization.
In the grand production of electronic systems, Embedded Cavity Substrate and traditional PCBs coexist, each playing a vital role in the intricate narrative of technology. The choice between them depends on the specific storyline and performance demands of the electronic composition at hand.
What are the Structure and Production Technologies of Embedded Cavity Substrate?
Embedded Cavity Substrate is an architectural marvel, its structure carefully crafted with intentional hollow spaces within a specialized substrate. The production of this technological wonder is a symphony of precision and innovation, involving a meticulous dance of structural elements and advanced manufacturing techniques. Let’s embark on a journey to unravel the intricacies of its design and the ballet of production technologies:
Architectural Symphony of Embedded Cavity Substrate:
Foundational Elegance:
At its core lies a substrate material carefully chosen for its unique properties. Whether it’s a high-frequency laminate or ceramic, the dielectric material serves as the canvas for the forthcoming technological masterpiece, offering a foundation that aligns with the specific requirements of the application.
Strategic Ballet of Cavities:
The defining feature is the deliberate integration of cavities within the substrate, akin to architectural nuances in a grand structure. These hollow spaces are not incidental; they are purposefully designed to play distinct roles—managing thermal dynamics, acting as shields against electromagnetic interference, or fine-tuning radio frequency intricacies.
Choreographed Placement:
The placement of these cavities is a meticulous dance, choreographed to perfection. Each cavity is strategically positioned based on its designated function. In applications where radio frequency nuances matter, they resonate in strategic locations, while in thermal management roles, their placement orchestrates a symphony of efficient heat dissipation.
Harmony of Conductive Elements:
On the surface of this technological canvas, conductive traces and electronic components take center stage. Their integration forms an intricate network, a harmonious arrangement that ensures seamless connectivity and functionality within the embedded electronic system.
Production Ballet of Embedded Cavity Substrate:
Precision Crafting of Cavities:
The production process begins with the precision crafting of cavities. Whether through the artistry of CNC milling machines or the chemical ballet of etching processes, the cavities are sculpted with utmost precision, each carve contributing to the symmetrical beauty of the final structure.
Layered Tapestry:
The substrate layers, adorned with carefully crafted cavities, are layered together in a dance of structural integrity. This layering isn’t just a technicality; it’s a layer-by-layer composition that adds depth and strength to the final substrate.
Innovative Flourish with Additive Manufacturing (Optional):
In certain performances, additive manufacturing takes a bow. Techniques like 3D printing step onto the stage, offering an innovative flourish to the production process. This optional act allows for the creation of intricate cavity structures layer by layer, adding a touch of flexibility to the overall design.
Artistic Expression in Circuit Printing and Placement:
The substrate then becomes a canvas for circuit printing and component placement. Whether through the grace of screen printing, the precision of inkjet printing, or the finesse of surface mount technology (SMT), each element finds its place in a carefully choreographed arrangement.
Thermal Crescendo:
A thermal crescendo unfolds as the substrate undergoes thermal treatments. This act solidifies the bonds between layers, ensuring the stability and endurance of the structure—a final note in the technological symphony.
Validation Performance:
Before the grand finale, the finished substrate undergoes meticulous validation. Quality control takes center stage, with electrical measurements, thermal analyses, and RF performance testing ensuring that every element of the substrate performs harmoniously.
The production of Embedded Cavity Substrate is an artistic endeavor, where technology and craftsmanship converge in a ballet of innovation. The result is a technological masterpiece, ready to take its place on the grand stage of electronic applications, where precision and performance steal the spotlight.
Frequently Asked Questions (FAQs)
What characterizes an Embedded Cavity Substrate?
An Embedded Cavity Substrate is an advanced electronic platform featuring intentionally designed hollow spaces within the material. These cavities serve specific purposes, such as optimizing thermal management, mitigating electromagnetic interference, or refining radio frequency performance.
In which applications do Embedded Cavity Substrates excel?
Embedded Cavity Substrates find applications in sectors demanding advanced functionalities. This includes RF and microwave circuits, communication devices, radar systems, and scenarios where meticulous control over thermal and electromagnetic factors is critical.
How does Embedded Cavity Substrate differ from conventional PCBs?
Embedded Cavity Substrates distinguish themselves through intentionally designed hollow structures, a departure from traditional PCBs. These structures enable superior thermal management, reduced electromagnetic interference, and optimized RF performance, catering specifically to the nuanced needs of advanced electronic systems.
Is customization possible for Embedded Cavity Substrates based on specific applications?
Yes, Embedded Cavity Substrates offer a high degree of customization. Manufacturers can tailor the substrate design to precisely align with the performance criteria of diverse applications, ensuring optimal functionality.
What production technologies are integral to Embedded Cavity Substrate manufacturing?
The manufacturing process involves precision milling or etching for cavity creation, layer lamination for building substrate structure, and circuit printing techniques for integrating conductive traces and components. In certain cases, additive manufacturing methods, including 3D printing, may also be applied.
How does the cost of Embedded Cavity Substrates compare to traditional PCBs?
Embedded Cavity Substrates typically incur higher production costs than traditional PCBs. This is attributed to their specialized design, precision manufacturing requirements, and the use of advanced materials.
Conclusion
In summary, the journey through the realm of Embedded Cavity Substrates reveals a tapestry woven with precision and innovation. These substrates, adorned with intentional hollow structures, emerge as avant-garde solutions in electronic system design, catering to applications that demand nothing short of excellence.
At the heart of this technological saga are the artisans—the Embedded Cavity Substrate Manufacturers. Their mastery in material science, precision machining, and the integration of electronic components transforms the abstract concept of hollow spaces into tangible substrates. These substrates find their place in the intricate dance of industries, from RF circuits to communication devices and radar systems, each application a unique stage for their performance.
The manufacturing process unfolds as a symphony of techniques—precision milling, layer lamination, circuit printing—all orchestrated to create substrates that are not just components but technological compositions. Optional additive manufacturing methods add a touch of avant-garde, allowing for intricate designs layer by layer.
While the production cost of Embedded Cavity Substrates may command a premium, it’s an investment in the future of electronic design. The specialized design and performance advantages they offer justify this investment, positioning them as protagonists in a narrative of technological evolution.
The choice between Embedded Cavity Substrates and traditional PCBs becomes a nuanced decision, akin to selecting instruments for an orchestra. Each has its role, its unique contribution to the grand symphony of electronic systems.
As we navigate the ever-evolving landscape of technology, Embedded Cavity Substrates continue to stand at the forefront—a canvas for innovation, a stage for precision, and a testament to the perpetual pursuit of excellence in the face of technological challenges.