Embedded Cavity PCB/Substrate Manufacturer
Embedded Cavity PCB/Substrate Manufacturer,Embedded Cavity PCB/Substrate integrates recessed areas within the board, accommodating components or modules for streamlined assembly and enhanced functionality. These substrates optimize space utilization and support miniaturization in electronic devices, ideal for compact designs in consumer electronics, automotive, and aerospace applications. Embedded cavities offer protection and shielding for sensitive components while enabling efficient heat dissipation. Manufacturing involves precise milling or etching processes to create the recessed areas. Embedded Cavity PCB/Substrate solutions cater to the evolving demands of modern electronics, providing a versatile platform for innovation in various industries where space optimization and performance are critical.
Embedded cavity PCBs, also recognized as printed circuit boards with incorporated voids, are intricately designed to seamlessly integrate electronic components into their framework. These voids serve as compact recesses strategically crafted to house diverse devices, fostering the amalgamation of the electronic system.
The infusion of embedded cavities into PCBs serves multifaceted objectives:
Dimensional Streamlining: Directly assimilating components into the PCB yields a perceptible reduction in the overall spatial footprint of the electronic system. This proves especially advantageous in scenarios where spatial limitations wield substantial influence.
Elevated Signal Fidelity: Placing designated components within these cavities functions to assuage electromagnetic interference (EMI) and curtail crosstalk between components. The consequence is an augmentation in signal fidelity and the holistic operational proficiency of the system.
Proficient Thermal Modulation: The embedded cavities act as adept conduits for proficient heat dissipation. Positioning components generating heat within these recesses allows the PCB material to dissipate heat with heightened efficiency.
Protective Encapsulation: Beyond functional utility, embedding components establishes a tangible barricade against external elements such as dust and moisture. This protective attribute assumes paramount significance in environments characterized by demanding conditions.
Aesthetic Enhancement: The design ethos of embedded cavity PCBs contributes to a refined and visually pleasing facade. Components discreetly ensconced within the board culminate in an electronic device that exudes a streamlined and aesthetically pleasing aura.
These specialized PCBs find application across a spectrum of electronic devices, spanning from smartphones and medical equipment to aerospace systems. The design and manufacturing processes for embedded cavity PCBs involve sophisticated techniques, and scrupulous material selection stands as an imperative to ensure optimal electrical performance, efficient thermal regulation, and the overarching reliability of the electronic system.
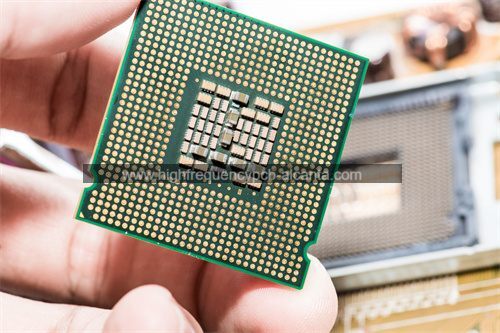
Embedded Cavity PCBs/Substrates Manufacturer
How Do Embedded Cavity PCBs/Substrates Fulfill Their Functions?
Embedded cavity PCBs or substrates execute their functions through a meticulous blend of design ingenuity and material curation. Let’s delve into how they carry out their roles:
Component Fusion: At the heart of embedded cavity PCBs lies the artful integration of electronic components directly into the board. This involves purposefully sculpting voids or cavities within the PCB structure to house specific components seamlessly.
Streamlined Dimensions: By internalizing components within the board, these PCBs contribute significantly to the reduction of the overall size of electronic systems. This elimination of the need for external housing or additional space makes them particularly conducive to applications constrained by spatial limitations.
Elevated Signal Purity: Nestling components within embedded cavities plays a pivotal role in mitigating electromagnetic interference (EMI) and minimizing crosstalk. This optimization translates to heightened signal purity, ensuring the transmission of electronic signals without compromise.
Effective Heat Harmonization: The embedded cavities double as efficient heat sinks, strategically accommodating heat-generating components. The surrounding PCB material acts as a proficient conductor, facilitating the effective dissipation of heat and contributing to meticulous thermal management.
Guardianship Against Elements: By encapsulating components within the PCB structure, embedded cavity boards act as protective shields against external elements like dust, moisture, and contaminants. This protective attribute becomes particularly invaluable in environments characterized by challenging conditions.
Aesthetic Finesse: The design philosophy of embedded cavity PCBs adds a touch of refinement by creating a sleek and visually appealing appearance. Components discreetly housed within the board contribute to an aesthetically polished electronic device.
Material Precision: The selection of materials, both for the PCB and embedded components, is paramount. Optimal materials must showcase superior electrical performance, thermal conductivity, and mechanical strength to ensure the enduring reliability of the electronic system.
Advanced Manufacturing Craftsmanship: The fabrication process of embedded cavity PCBs demands specialized manufacturing techniques. Precision takes center stage in creating the voids and embedding components, securing the overall functionality and performance of the PCB.
In essence, embedded cavity PCBs bring their functions to fruition by seamlessly integrating components, downsizing dimensions, refining signal purity, orchestrating heat dissipation, providing elemental guardianship, infusing aesthetic finesse, and leveraging advanced materials and manufacturing techniques. These attributes render them well-suited for a myriad of applications where imperatives of space efficiency, performance, and reliability hold sway.
What Are the Different Types of Embedded Cavity PCBs/Substrates?
Embedded cavity PCBs or substrates exhibit a myriad of types, each intricately fashioned to meet specific application requirements. Let’s navigate through diverse categories:
Cavity Stacked Microvia PCBs:
Features: Distinguished by stacked microvias within cavities.
Applications: Thrives in environments requiring high-density interconnects, where the fusion of miniaturization and advanced interconnection technology takes center stage.
RF/Microwave Embedded PCBs:
Features: Tailored with optimized cavities for seamless high-frequency signal transmission.
Applications: Carves its niche in telecommunications, radar systems, and wireless communication devices.
Power Module PCBs:
Features: Engineered with embedded cavities, carving out dedicated spaces for power components and modules.
Applications: Indispensable in power electronics applications that call for efficient heat dissipation.
Optoelectronic PCBs:
Features: Showcases cavities accommodating optoelectronic components like LEDs and photodetectors.
Applications: Plays a pivotal role in optical communication systems and related devices.
Medical Device PCBs:
Features: Leverages embedded cavities for the compact integration of components, ensuring reliability in medical applications.
Applications: Tailored for the unique requirements of medical devices.
Aerospace and Defense PCBs:
Features: Precision-crafted for harsh environmental conditions, ensuring reliability and performance in challenging scenarios.
Applications: Primarily designed for aerospace and defense applications.
Consumer Electronics PCBs:
Features: Cavities designed for space optimization and aesthetic considerations.
Applications: Finds its place within smartphones, wearables, and various other consumer electronics.
Automotive PCBs:
Features: Engineered to withstand the demanding conditions of automotive environments.
Applications: Integral to automotive electronics, contributing to functions like engine control, safety systems, and infotainment.
High-Speed Data Transmission PCBs:
Features: Tailored for data centers and networking equipment, excelling in high-speed data transmission.
Applications: Minimizes signal interference and preserves signal integrity in data transmission scenarios.
Industrial Control PCBs:
Features: Delivers compact designs, robustness, and efficient heat dissipation.
Applications: Deployed in industrial control systems, ensuring reliability in diverse industrial environments.
The choice of a specific type hinges on the unique demands of the application, encompassing considerations such as frequency, power requirements, miniaturization goals, and prevailing environmental conditions. Each type is intricately engineered to address specific challenges and performance benchmarks associated with its intended use.
How Are Embedded Cavity PCBs/Substrates Closely Connected to IC Packaging?
The intricate dance between embedded cavity PCBs or substrates and IC packaging unveils a dynamic relationship that significantly influences the integration and functionality of electronic systems. Let’s navigate through the nuances of this interplay:
Meticulous IC Integration:
Crafted Cavities: Embedded cavity PCBs boast meticulously crafted cavities, intricately shaped to cradle ICs with precision. This craftsmanship ensures a seamless integration of chips into the very fabric of the PCB.
Pioneering Miniaturization:
Spatial Optimization: By strategically nestling ICs within purpose-built cavities, these PCBs contribute substantially to the ongoing drive for miniaturization. This becomes particularly pivotal in an era where sleek and compact designs reign supreme.
Efficient Thermal Harmony:
Heat Ballet: Acknowledging the thermal ballet of ICs, embedded cavity PCBs act as choreographers for effective heat management. The incorporation of thermal solutions like heat sinks and thermal vias orchestrates a symphony of heat dissipation, safeguarding the virtuoso performance of the ICs.
Sentinels of Signal Integrity:
Interference Minuet: Embedded cavity PCBs are choreographed to preserve the delicate dance of signals. Proximity within dedicated cavities minimizes signal interference, allowing for a harmonious communication ballet between components.
Bespoke Designs for ICs:
Tailored Couture: Embedded cavity PCBs don bespoke designs, tailored to the unique specifications of different ICs. From dimensions to pin configurations, each element is meticulously stitched to align with the intricate tapestry of integrated circuits.
Versatility for Varied Applications:
Adaptive Choreography: Whether in the limelight of RF/microwave realms, power electronics, or the graceful domain of optoelectronics, embedded cavity PCBs showcase an adaptive choreography tailored to the distinct demands of ICs in these applications.
Guardians of Protection and Durability:
Shielding Ballet: The cavity structure takes on the role of a protective guardian, enveloping ICs and shielding them from the whims of external environmental factors. This not only safeguards the performers but also fortifies the endurance of the entire system.
Harmonious Hybrid Blends:
Diversity in Dance Styles: Beyond solo performances, embedded cavity technology seamlessly integrates into hybrid ensembles with other packaging approaches like flip-chip or system-in-package (SiP). This diversity allows for a multifaceted dance of advantages, including heightened performance and streamlined form factors.
In essence, embedded cavity PCBs emerge as the choreographers of electronic symphonies, creating an optimal stage for the graceful integration and performance of ICs. The dynamic connection lies in their ability to address thermal intricacies, provide structural support, and orchestrate a symphony of functionality within electronic devices.
How Do Embedded Cavity PCBs/Substrates Differ from Conventional PCBs?
Embedded cavity PCBs/substrates carve out a distinctive niche by diverging from the conventional norms of PCB design. Let’s unravel the nuances that set them apart:
Cavity Craftsmanship:
Embedded Cavity PCBs: Flaunt carefully crafted recesses or cavities within their structure. These purposeful indentations are intricately shaped to cradle components like integrated circuits (ICs) with meticulous precision.
Conventional PCBs: Contrastingly, adhere to a flat, uniform design sans the specialized recesses for component accommodation.
Championing Miniaturization:
Embedded Cavity PCBs: Champion the cause of miniaturization by ingeniously housing components within dedicated cavities. This spatial optimization contributes significantly to the pursuit of sleek and compact designs.
Conventional PCBs: May not prioritize spatial efficiency to the same degree, with components typically residing on the surface without the bespoke accommodations of embedded cavities.
Thermal Choreography:
Embedded Cavity PCBs: Conduct a thermal symphony by incorporating features like thermal vias, heat sinks, or other cooling solutions within the cavities. This choreography ensures an efficient dance of heat dissipation.
Conventional PCBs: Rely on more conventional methods for temperature control, employing thermal vias on the surface or external heat sinks.
Preserving Signal Harmony:
Embedded Cavity PCBs: Execute a meticulous plan to minimize signal interference. Components snug within dedicated cavities contribute to a harmonious communication ballet, ensuring reliable signal integrity.
Conventional PCBs: Navigate the realm of signal integrity without the structural advantage of dedicated cavities, potentially exposing them to a higher risk of interference.
Tailored for Component Couture:
Embedded Cavity PCBs: Offer a bespoke canvas for customization, allowing dimensions, shapes, and placements of cavities to align seamlessly with the unique demands of integrated components.
Conventional PCBs: Adhere to a more standardized design approach, lacking the tailored finesse often witnessed in the customized landscape of embedded cavity PCBs.
Application-Specific Choreography:
Embedded Cavity PCBs: Often choreographed for specific applications such as RF/microwave, power electronics, optoelectronics, where precision and compact designs take center stage.
Conventional PCBs: Embrace a broader spectrum of applications, finding a home in standard electronic devices where the specialized integration of components may not be a critical consideration.
Guardians of Protection and Endurance:
Embedded Cavity PCBs: Step into the role of guardians, shielding enclosed components from external environmental influences. This protective dance not only safeguards components but fortifies the overall endurance of the system.
Conventional PCBs: Extend a degree of protection to surface components but lack the cocooning effect provided by dedicated cavities.
Harmonious Hybrid Performances:
Embedded Cavity PCBs: Showcase versatility by seamlessly integrating with other packaging technologies. This versatility allows for hybrid performances that blend the advantages of embedded cavities with other packaging approaches.
Conventional PCBs: Typically follow standalone designs without the inherent integration capabilities inherent in embedded cavity PCBs.
In essence, embedded cavity PCBs emerge as avant-garde substrates, deviating from conventional designs to provide a stage for a bespoke dance of components. The dynamic differences lie in their specialized features that cater to miniaturization, thermal management, signal integrity, customization, and application-specific design. The choice between the two hinges on the specific needs of the electronic system and the desired level of integration and optimization.
What Is the Main Structure and Production Technology of Embedded Cavity PCBs/Substrates?
Embedded cavity PCBs or substrates stand out with a unique structure and production process tailored to house components within purposeful recesses. Let’s navigate through the intricacies of their main structure and the technology orchestrating their production:
Distinctive Structure:
Foundation Material:
The journey begins with a rigid substrate, often FR-4, chosen based on thermal conductivity, dielectric properties, and the specific needs of the application.
Cavity Craftsmanship:
What defines embedded cavity PCBs is the meticulous creation of cavities or recesses within the substrate. These pockets are strategically shaped to cradle components like integrated circuits (ICs) or connectors.
Electrically Charged Layers:
Conductor layers, formed through copper plating or thin-film deposition, weave a web of electrical pathways on the surface and within the cavities.
Dielectric Dance:
Interspersed with conductor layers are dielectric layers, orchestrating a dance of insulation and separation to prevent electrical short circuits.
Surface Elegance:
A surface finish, be it the grace of HASL, the sophistication of ENIG, or the natural allure of OSP, crowns the PCB, offering protection against oxidation and ensuring impeccable solderability.
Component Stages:
Designated areas within the cavities become the stages for component attachment, adorned with pads, solder paste, or other features to facilitate the seamless integration of electronic performers.
Thermal Ballet:
Addressing the heat generated by these performers, thermal vias, heat sinks, or other solutions join the production, performing a ballet of thermal management within the cavities.
Production Symphony:
Cavity Carving:
Precision milling, routing, or laser cutting techniques are the virtuosos that carve out the cavities, each note precisely tuned to the requirements of the design.
Layer Overture:
The overture begins with the deposition of conductor layers, copper plating unveiling the intricate circuitry. Simultaneously, dielectric layers are laminated, constructing the layered symphony.
Copper Etude:
The copper etude takes center stage as photoresist dons the spotlight. Exposing and developing the desired circuit pattern, the copper is etched away, leaving behind the harmonious traces.
Component Sonata:
Components join the symphony, attached to their designated areas within the cavities. Solder paste is the adhesive, and the reflow soldering process secures the components in their melodic positions.
Finale of Surface Euphony:
The grand finale features the application of the chosen surface finish, a harmonious conclusion enhancing solderability and shielding the PCB from environmental nuances.
Quality Crescendo:
Throughout this symphony, a crescendo of quality control measures ensures that the final composition of embedded cavity PCBs harmonizes with design specifications and performance standards.
The production technology for embedded cavity PCBs is a symphony of precision machining, layer deposition, and assembly processes. This orchestrated dance creates a substrate that not only houses but elevates the performance of components within purpose-built cavities.
Frequently Asked Questions (FAQs)
What defines an embedded cavity PCB or substrate?
An embedded cavity PCB or substrate is a specialized printed circuit board featuring strategically designed recesses or cavities within its structure. These cavities are crafted to accommodate specific components like integrated circuits (ICs) or connectors.
What advantages do embedded cavity PCBs offer?
Embedded cavity PCBs provide benefits such as efficient space utilization, superior thermal management, reduced signal interference, customization for specific components, and adaptability for various application-specific designs.
What is the production process for embedded cavity PCBs?
The production involves precision techniques like milling or laser cutting to create cavities, deposition of conductor and dielectric layers, copper plating and etching for circuit formation, component attachment through soldering, application of a surface finish, and stringent quality control procedures.
How do embedded cavity PCBs address thermal management?
Embedded cavity PCBs manage heat by incorporating features like thermal vias, heat sinks, or other solutions within the cavities. This ensures efficient heat dissipation, promoting optimal component performance.
In which applications are embedded cavity PCBs commonly used?
Embedded cavity PCBs find applications in diverse fields, including RF/microwave, power electronics, optoelectronics, and other areas where compact designs, thermal management, and specialized integration play a crucial role.
Can embedded cavity PCBs be integrated with other packaging technologies?
Yes, embedded cavity PCBs seamlessly integrate with other packaging technologies, allowing for hybrid solutions. This versatility enables the combination of advantages from embedded cavities with other packaging approaches like flip-chip or system-in-package (SiP).
What quality control measures are implemented during embedded cavity PCB production?
Quality control measures include inspections at various stages, ensuring that the final products meet design specifications and performance standards. Checks cover cavity dimensions, conductor integrity, soldering quality, and overall functionality.
Conclusion
In conclusion, embedded cavity PCBs or substrates represent a revolutionary stride in the realm of printed circuit board technology. Their unique structure, characterized by strategically designed recesses or cavities, unlocks a myriad of advantages, including space optimization, enhanced thermal management, and minimized signal interference. The production process involves precision techniques, layer deposition, and meticulous assembly, culminating in a substrate that seamlessly accommodates specific components with tailored customization.
These specialized PCBs find their stage in diverse applications, from RF/microwave to power electronics, showcasing their versatility and application-specific design capabilities. The orchestration of thermal management within the cavities, incorporating features like thermal vias and heat sinks, further positions embedded cavity PCBs as leaders in compact and efficient electronic systems.
The integration of embedded cavity PCBs with other packaging technologies opens the door to hybrid solutions, blending the advantages of embedded cavities with diverse packaging approaches. The choice of materials, surface finishes, and rigorous quality control measures during production underscore the commitment to precision and reliability.
As embedded cavity PCBs continue to redefine electronic design landscapes, their role as innovative substrates catering to miniaturization, customization, and thermal optimization becomes increasingly pivotal. This technological symphony, marked by precision, customization, and versatility, positions embedded cavity PCBs as key players in shaping the future of advanced electronic systems.