Embedded Cavity PCB Manufacturing
Embedded Cavity PCB Manufacturing,Embedded Cavity PCBs, or Embedded Cavity Printed Circuit Boards, are specialized circuit boards that feature recessed areas within the board itself, designed to accommodate electronic components. These cavities, or embedded areas, allow for the integration of components directly within the PCB substrate, rather than mounting them on the surface. This innovative design approach enables the creation of compact and streamlined electronic devices by reducing overall size and improving durability. Embedded Cavity PCBs offer advantages such as enhanced thermal management, improved signal integrity, and increased mechanical stability. They are widely used in applications where space is limited, such as smartphones, wearables, automotive electronics, and medical devices. With their ability to house components within the PCB itself, Embedded Cavity PCBs contribute to the development of smaller, more efficient, and reliable electronic products.
What is Embedded Cavity PCB?
An Embedded Cavity PCB (Printed Circuit Board) is a specialized type of PCB that incorporates cavities or recessed areas within the board itself. These cavities are designed to house components, such as sensors, chips, or other electronic devices, within the body of the PCB itself, rather than mounting them on the surface.
The purpose of embedding components within the PCB is to reduce the overall size of the electronic device, enhance its durability, improve signal integrity, and potentially improve thermal management. By embedding components, the overall profile of the device can be made thinner, which is particularly beneficial in applications where space is at a premium, such as in smartphones, wearables, or other compact electronic devices.
Embedded cavity PCBs require specialized manufacturing processes and may involve the use of advanced materials and techniques such as laser drilling, sequential lamination, and controlled depth milling to create the cavities within the board. Additionally, careful design considerations are necessary to ensure that the embedded components are properly isolated and that the overall structural integrity and electrical performance of the PCB are maintained.
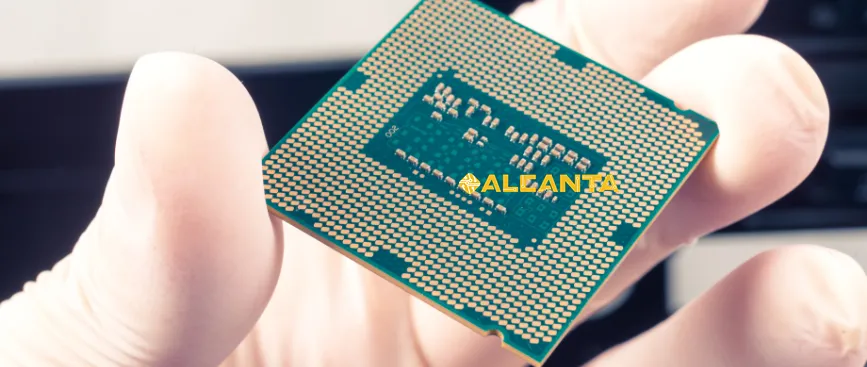
Embedded Cavity PCB Manufacturing
What are the Embedded Cavity PCB Design Guidelines?
Designing an Embedded Cavity PCB involves several important considerations to ensure proper functionality, reliability, and manufacturability. Here are some key guidelines for designing Embedded Cavity PCBs:
- Component Selection: Choose components suitable for embedding within the PCB, considering size, thermal characteristics, and electrical requirements. Components should be able to withstand the embedding process and operate reliably within the cavity.
- Cavity Design: Design cavities carefully to accommodate embedded components without compromising the structural integrity of the PCB. Consider factors such as component size, clearance, and thermal management. Ensure that cavities are properly isolated from surrounding conductive traces to prevent short circuits.
- Layer Stackup: Optimize the layer stackup to facilitate the embedding process and ensure signal integrity. Consider using controlled impedance layers for high-speed signal routing. Plan the layer stackup to accommodate the cavities and maintain overall board thickness requirements.
- Material Selection: Choose PCB materials suitable for embedding components and providing sufficient mechanical support. Consider materials with good thermal conductivity to assist with heat dissipation from embedded components.
- Manufacturability: Design the PCB with manufacturability in mind. Ensure that the chosen fabrication processes, such as laser drilling or sequential lamination, can effectively create cavities without compromising board quality. Avoid complex cavity shapes or designs that may increase manufacturing complexity.
- Signal Integrity: Pay close attention to signal integrity issues, especially for high-speed signals. Minimize signal distortion and interference by carefully routing traces and maintaining controlled impedance throughout the PCB.
- Thermal Management: Implement effective thermal management strategies to dissipate heat generated by embedded components. Consider adding thermal vias or heat sinks to enhance heat dissipation within the PCB.
- Testing and Validation: Develop testing procedures to validate the functionality and reliability of embedded components. Conduct thorough testing, including electrical testing and thermal analysis, to ensure that the PCB meets performance requirements.
- Documentation: Document the design thoroughly, including cavity dimensions, material specifications, and fabrication guidelines. Clear documentation helps ensure consistency in manufacturing and facilitates future revisions or troubleshooting.
By following these guidelines, designers can create Embedded Cavity PCBs that meet performance requirements while ensuring reliability and manufacturability.
What is the Embedded Cavity PCB Fabrication Process?
The fabrication process of microvia substrates involves several steps to create the intricate interconnection structure required for high-density electronic packaging. Here’s an overview of the typical microvia substrate fabrication process:
- Substrate Preparation: The process begins with the preparation of the substrate material, usually a laminate composed of layers of copper and insulating material (such as epoxy resin or polyimide). The substrate material is typically in the form of large panels or sheets.
- Circuit Patterning: A layer of copper foil is bonded onto the substrate material. The desired circuit patterns are then transferred onto the copper foil layer using photolithography or direct imaging techniques. This involves applying a photoresist layer onto the copper foil, exposing it to UV light through a mask with the circuit pattern, and then developing the exposed resist to leave behind the desired copper traces.
- Via Drilling: Small-diameter holes, known as microvias, are drilled through the substrate material at locations where interconnections are required between different layers of the PCB. Microvias are typically created using laser drilling or mechanical drilling processes, depending on the substrate material and design requirements.
- Via Cleaning and Surface Treatment: After drilling, the microvias are cleaned to remove any debris or contaminants that may have accumulated during the drilling process. The surfaces of the microvias are then treated to promote adhesion and facilitate subsequent plating processes.
- Via Plating: A thin layer of conductive material, such as copper or electroless nickel, is deposited onto the walls of the microvias through an electroplating or electroless plating process. This forms the conductive pathways that establish electrical connections between different layers of the PCB.
- Circuit Lamination: Additional layers of substrate material and copper foil may be laminated onto the previously patterned layers to build up the required number of PCB layers. Each additional layer may undergo the same circuit patterning, via drilling, cleaning, surface treatment, and plating processes as described above.
- Final Processing: Once all layers and interconnections are formed, the fabricated panel undergoes final processing steps, including etching, solder mask application, legend printing, and surface finish application (such as immersion gold or HASL) to protect the exposed copper traces, provide insulation between conductive traces, and improve solderability.
- Quality Control and Testing: Throughout the fabrication process, various quality control measures and testing procedures are implemented to ensure that the microvia substrate meets the required specifications for dimensional accuracy, electrical performance, reliability, and overall quality.
By following these steps, manufacturers can produce microvia substrates with precise interconnections and high-density packaging capabilities suitable for advanced electronic applications.
How do you manufacture an Embedded Cavity PCB?
Manufacturing an Embedded Cavity PCB involves several specialized steps and processes. Here’s a simplified overview of the manufacturing process:
- Designing the PCB:
– Utilize computer-aided design (CAD) software to create a detailed layout of the PCB, including the placement and dimensions of the cavities for embedding components.
– Consider factors such as thermal management, signal integrity, and mechanical stability during the design phase.
- Selecting Materials:
– Choose suitable materials for the PCB substrate and the embedded components based on electrical, thermal, and mechanical requirements.
– Common materials for PCB substrates include FR-4 fiberglass, while components may be made of various materials such as silicon, ceramics, or plastics.
- Cavity Creation:
– Use specialized machining techniques like milling, routing, or laser drilling to create cavities or recessed areas within the PCB substrate.
– Ensure precise control over the dimensions and depth of the cavities to accommodate the embedded components accurately.
- Component Embedding:
– Place electronic components, such as chips, sensors, or passive components, into the cavities on the PCB.
– Secure the components in place using adhesives, encapsulation materials, or by molding the substrate around them.
– Ensure proper alignment and orientation of the components for soldering and electrical connections.
- Layer Stacking and Lamination:
– If the PCB requires multiple layers, stack them together, ensuring alignment of embedded components across layers.
– Use lamination techniques to bond the layers together, preserving the integrity of embedded components.
- Circuit Patterning and Etching:
– Apply a conductive layer (typically copper) onto the PCB substrate through processes like electroplating or chemical deposition.
– Use photolithography and etching techniques to create circuit traces, pads, and vias on the PCB, ensuring isolation between conductive traces and cavities.
- Surface Finishing:
– Apply surface finishes such as solder mask and surface coatings to protect exposed copper surfaces and facilitate soldering.
– Common surface finishes include HASL (Hot Air Solder Leveling), ENIG (Electroless Nickel Immersion Gold), and OSP (Organic Solderability Preservatives).
- Quality Assurance and Testing:
– Perform visual inspection, electrical testing, and mechanical testing to verify the integrity and functionality of the finished PCB.
– Check for proper connection of embedded components, absence of defects in cavities or circuitry, and adherence to specifications.
- Assembly and Packaging:
– If required, assemble the Embedded Cavity PCB into the final electronic device, incorporating additional components and enclosures.
– Package the electronic device according to specifications, ensuring protection and durability during handling and operation.
Throughout the manufacturing process, attention to detail, precision, and adherence to design specifications are crucial to produce high-quality Embedded Cavity PCBs suitable for various applications. Additionally, specialized equipment and expertise may be necessary for certain stages of the manufacturing process.
How much should an Embedded Cavity PCB cost?
Manufacturing an embedded cavity PCB involves a specialized process designed to create a recessed area within the PCB where components can be mounted, providing protection and potentially reducing overall system size. Here’s a general outline of the manufacturing process for embedded cavity PCBs:
- Design Phase: The process begins with the design of the PCB, including the layout of the embedded cavity area. Design considerations include the dimensions and shape of the cavity, as well as the placement of components and routing of traces.
- Substrate Preparation: The substrate material for the PCB is selected based on the specific requirements of the application. Common substrate materials include FR-4 epoxy or high-frequency laminates for RF applications. The substrate material is typically in the form of a panel or sheet.
- Cavity Formation: Using specialized equipment such as milling machines or laser cutters, the cavity is created within the substrate material according to the design specifications. This may involve removing material from one or both sides of the PCB to create the recessed area.
- Cavity Sealing (Optional): Depending on the requirements of the application, the cavity may be sealed to protect sensitive components from environmental factors such as moisture, dust, or vibration. This can be accomplished using sealing compounds, adhesives, or cover layers bonded over the cavity.
- Component Mounting: Electronic components are assembled onto the PCB using standard surface mount technology (SMT) or through-hole assembly techniques. Components may be mounted within the embedded cavity or on the surface of the PCB, depending on the design requirements.
- Trace Routing: Traces are routed on the PCB to establish electrical connections between components, including those mounted within the embedded cavity and those located elsewhere on the board. Careful attention is paid to signal integrity and impedance matching during trace routing.
- Via Formation: Vias are created to establish electrical connections between different layers of the PCB. These vias may be formed using mechanical drilling, laser drilling, or other methods depending on the design requirements.
- Final Processing: Once all components are mounted and traces are routed, the PCB undergoes final processing steps including solder mask application, legend printing, and surface finish application (such as HASL, ENIG, or immersion silver) to protect the exposed copper traces and provide solderability.
- Testing and Inspection: The finished PCB undergoes rigorous testing and inspection to ensure that it meets the required specifications for electrical performance, reliability, and overall quality.
By following these steps, manufacturers can produce embedded cavity PCBs with precise cavity dimensions, reliable component mounting, and optimal electrical performance suitable for a wide range of applications.
What is Embedded Cavity PCB base material?
The choice of base material for Embedded Cavity PCBs depends on various factors such as thermal management requirements, electrical properties, mechanical strength, and cost considerations. Here are some common base materials used for Embedded Cavity PCBs:
- FR-4 (Flame Retardant-4): FR-4 is the most widely used base material for PCBs due to its affordability, good electrical insulation properties, and mechanical strength. It consists of woven fiberglass cloth impregnated with epoxy resin.
- High-Temperature FR-4: For applications requiring elevated operating temperatures, high-temperature FR-4 variants with improved thermal stability and lower coefficient of thermal expansion (CTE) may be used.
- Rogers and Taconic Materials: Specialized high-frequency PCBs may use materials such as Rogers or Taconic substrates, which offer excellent electrical performance, low dielectric loss, and high thermal conductivity.
- Metal-Core PCBs (MCPCB): Metal-core PCBs utilize a metal substrate (such as aluminum or copper) for enhanced thermal management. These are suitable for applications with high power dissipation requirements.
- Ceramic Substrates: Ceramic materials like aluminum oxide (Al2O3) or aluminum nitride (AlN) are used for applications requiring superior thermal conductivity, high-frequency performance, and reliability under harsh operating conditions.
- Flexible or Rigid-Flex PCBs: For applications requiring flexibility or compact form factors, flexible or rigid-flex PCBs may be used. These utilize flexible substrates such as polyimide (PI) or polyester (PET).
The choice of base material depends on the specific requirements of the Embedded Cavity PCB, including thermal management, signal integrity, mechanical stability, and cost constraints. Designers must carefully evaluate these factors and select the most appropriate material for their application. Additionally, it’s essential to consider the compatibility of the base material with the manufacturing processes involved in creating embedded cavities and integrating components within the PCB.
Which company makes Embedded Cavity PCB?
Several companies in the market offer manufacturing services for Embedded Cavity PCBs. Some well-known PCB manufacturers include Foxconn Technology Group, JLCPCB, Elecrow, as well as various specialized PCB manufacturing companies both domestically and internationally. These companies possess extensive experience and technical expertise to meet customers’ diverse needs for Embedded Cavity PCBs.
In our company, we also provide manufacturing services for Embedded Cavity PCBs. As a professional PCB manufacturer, we have advanced production equipment and a skilled technical team capable of achieving high-quality production of Embedded Cavity PCBs. Our manufacturing process includes:
- Design and Engineering Support: Our engineering team has rich experience and can provide design support and engineering consultation for Embedded Cavity PCBs to ensure compliance with customers’ design requirements and technical specifications.
- Manufacturing and Processing: We utilize advanced processing equipment and technologies such as precision CNC machines and laser drilling to achieve precise machining of embedded cavities, ensuring accurate embedding of components.
- Quality Control: We strictly adhere to quality management systems, conducting rigorous control and inspection at every stage from raw material procurement to production manufacturing to ensure stable and reliable product quality.
- 4. Customer Service: We prioritize communication and cooperation with customers, offering timely technical support and after-sales service to ensure customer satisfaction and trust.
Through our manufacturing services, customers can obtain high-quality and highly reliable Embedded Cavity PCB products to meet various application requirements. We are committed to providing customers with the highest quality products and services, working together with them to achieve success and development.
What are the 7 qualities of good customer service?
Good customer service is essential for building strong relationships with customers and ensuring satisfaction. Here are seven qualities that contribute to excellent customer service:
- Responsiveness: A key aspect of good customer service is being responsive to customer inquiries, concerns, and feedback in a timely manner. Promptly addressing customer needs demonstrates attentiveness and care, leading to improved satisfaction.
- Empathy: Empathy involves understanding and acknowledging the customer’s perspective, feelings, and concerns. Showing empathy helps build rapport and trust with customers, leading to more positive interactions and resolutions.
- Clarity and Communication: Effective communication is crucial for providing good customer service. Clear, concise, and transparent communication helps customers understand information, policies, and solutions, reducing confusion and frustration.
- Knowledge and Expertise: Customers expect assistance from knowledgeable and competent service representatives who can provide accurate information, answer questions, and offer solutions to their problems. Investing in training and development ensures that employees have the expertise needed to assist customers effectively.
- Problem-Solving Skills: Good customer service involves the ability to identify and resolve customer issues efficiently and effectively. Service representatives should demonstrate problem-solving skills, creativity, and resourcefulness to address customer concerns and provide satisfactory solutions.
- Professionalism: Professionalism encompasses various attributes such as courtesy, respect, integrity, and reliability. Maintaining professionalism in all interactions with customers helps build trust, credibility, and positive perceptions of the company.
- Consistency: Consistency in service delivery is essential for building customer loyalty and satisfaction. Customers expect a consistent level of service quality, whether they interact with the company online, over the phone, or in person. Consistency helps establish reliability and reinforces the company’s brand reputation.
By embodying these qualities and prioritizing customer-centric approaches, businesses can deliver exceptional customer service experiences that foster long-term relationships and drive success.
FAQs (Frequently Asked Questions)
What is an Embedded Cavity PCB?
An Embedded Cavity PCB is a specialized type of printed circuit board that features recessed areas or cavities within the board itself. These cavities are designed to house electronic components, such as chips or sensors, within the body of the PCB.
What are the advantages of using Embedded Cavity PCBs?
Embedded Cavity PCBs offer several advantages, including reduced overall size of electronic devices, improved durability, enhanced thermal management, and improved signal integrity.
What types of components can be embedded in Embedded Cavity PCBs?
Various components can be embedded in Embedded Cavity PCBs, including integrated circuits (ICs), sensors, microcontrollers, passive components, and more.
How are cavities created in Embedded Cavity PCBs?
Cavities in Embedded Cavity PCBs are typically created using specialized machining techniques such as milling, routing, or laser drilling. These techniques allow for precise shaping and sizing of the cavities.
What materials are commonly used for Embedded Cavity PCBs?
Common materials used for Embedded Cavity PCBs include FR-4 fiberglass, high-temperature FR-4, metal-core substrates (such as aluminum or copper), and ceramic substrates (such as aluminum oxide or aluminum nitride).
What are some applications of Embedded Cavity PCBs?
Embedded Cavity PCBs find applications in various industries, including consumer electronics, automotive, aerospace, medical devices, and telecommunications. They are used in devices where space-saving, durability, and thermal management are critical.
Are there any design considerations for Embedded Cavity PCBs?
Yes, designing Embedded Cavity PCBs requires careful consideration of factors such as component placement, thermal management, signal integrity, mechanical stability, and manufacturing feasibility.
Can any PCB manufacturer produce Embedded Cavity PCBs?
While many PCB manufacturers offer standard PCB fabrication services, not all may specialize in Embedded Cavity PCBs. It’s essential to choose a manufacturer with experience and expertise in producing such specialized PCBs.
What are the cost implications of using Embedded Cavity PCBs?
The cost of Embedded Cavity PCBs depends on factors such as design complexity, materials used, manufacturing processes involved, and order volume. Generally, Embedded Cavity PCBs may be more expensive than standard PCBs due to their specialized nature.
How can I determine if Embedded Cavity PCBs are suitable for my project?
To determine suitability, evaluate your project requirements, including size constraints, component density, thermal considerations, and performance needs. Consult with a knowledgeable PCB manufacturer to assess feasibility and discuss potential benefits for your application.