EM827 Materials PCB Manufacturer
EM827 Materials PCB Manufacturer,EM827 Materials PCB represents a pinnacle in printed circuit board (PCB) technology, engineered with precision and performance in mind. Crafted from advanced materials bearing the EM827 designation, these PCBs offer unparalleled electrical characteristics, thermal stability, and mechanical integrity. Designed to excel in high-frequency, high-speed, and demanding environments, EM827 Materials PCBs deliver exceptional signal integrity, minimal loss, and reliable performance under challenging conditions.
These PCBs find application across a spectrum of industries, from telecommunications and aerospace to automotive and medical devices. Whether facilitating data transmission in telecommunications infrastructure, powering critical systems in satellites, optimizing engine control units in automobiles, or enabling life-saving medical equipment, EM827 Materials PCBs set the standard for reliability and performance.
Manufactured with cutting-edge fabrication processes and stringent quality controls, EM827 Materials PCBs ensure consistency, precision, and durability. They represent the culmination of innovation and expertise, providing engineers and designers with the confidence to push the boundaries of technology and achieve breakthroughs in their respective fields.
What is EM827 Materials PCB?
The EM827 Materials PCB is likely a type of printed circuit board (PCB) designed for electronic applications. PCBs are used to mechanically support and electrically connect electronic components using conductive pathways, tracks, or signal traces etched from copper sheets laminated onto a non-conductive substrate. The EM827 Materials PCB could refer to a specific model or type of PCB designed with particular materials, possibly with enhanced electrical properties, thermal conductivity, or durability.
The designation “EM827” might indicate a specific product line or model within a manufacturer’s catalog. The choice of materials in a PCB can significantly affect its performance, especially in terms of signal integrity, electromagnetic interference (EMI) shielding, and heat dissipation. For example, high-frequency applications might require specialized materials with low dielectric constant and loss tangent to minimize signal loss and distortion.
Without more context, it’s challenging to provide precise details about the EM827 Materials PCB. However, it’s common for PCB manufacturers to offer various material options to suit different application requirements. These materials could include traditional FR-4 (a type of flame-retardant fiberglass material), as well as more advanced options like polyimide, PTFE (Teflon), or ceramic substrates.
In summary, the EM827 Materials PCB likely refers to a specific type of PCB optimized for certain performance characteristics or applications, with the designation “EM827” possibly indicating its model or series number. Understanding its exact specifications would require consulting the manufacturer’s documentation or specifications.
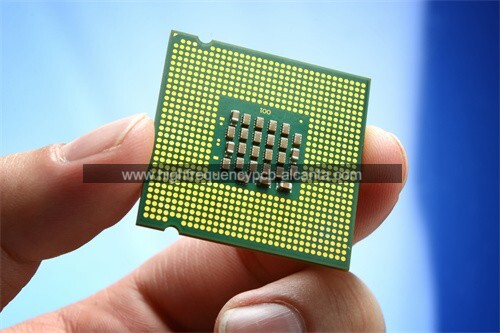
EM827 Materials PCB Manufacturer
What are the EM827 Materials PCB Design Guidelines?
Without specific information about the EM827 Materials PCB, it’s challenging to provide precise design guidelines. However, I can offer some general PCB design principles that would likely apply:
- Layer Stackup: Determine the appropriate layer stackup based on the circuit complexity, signal integrity requirements, and impedance control. Consider factors like signal propagation delay, controlled impedance for high-speed signals, and power distribution.
- Material Selection: Choose the appropriate substrate material based on electrical, mechanical, and thermal requirements. Consider factors like dielectric constant, loss tangent, thermal conductivity, and coefficient of thermal expansion (CTE). Ensure that the selected material is compatible with the manufacturing processes and environmental conditions.
- Trace Width and Spacing: Determine the trace width and spacing based on the current-carrying capacity, impedance requirements, and manufacturing capabilities. Follow industry-standard guidelines or use PCB design software to calculate the optimal trace geometries.
- Signal Integrity: Minimize signal distortion, reflections, and electromagnetic interference (EMI) by carefully routing high-speed signals, avoiding sharp bends, and maintaining controlled impedance for critical transmission lines. Use ground and power planes effectively to provide a low-impedance return path and reduce electromagnetic emissions.
- Thermal Management: Ensure adequate thermal dissipation by using thermal vias, thermal pads, or heatsinks for components generating heat. Design the PCB layout to facilitate efficient heat transfer and avoid thermal hotspots that could degrade performance or reliability.
- Component Placement: Optimize component placement to minimize signal crosstalk, reduce trace lengths, and simplify routing. Follow best practices for placing critical components, such as high-speed ICs, connectors, and decoupling capacitors.
- Design for Manufacturability (DFM): Consider manufacturability throughout the design process to minimize production costs and avoid manufacturing issues. Follow PCB fabrication and assembly guidelines provided by the manufacturer, including panelization, solder mask clearance, and copper feature limitations.
- Electromagnetic Compatibility (EMC): Design the PCB to comply with electromagnetic compatibility requirements by minimizing emissions and susceptibility to external interference. Use proper grounding techniques, shielding, and filtering to mitigate EMC issues.
- Testing and Validation: Plan for testing and validation of the PCB design to ensure functionality, reliability, and performance. Perform design rule checks (DRC), signal integrity analysis, and thermal simulations as part of the design verification process.
These are general guidelines that apply to PCB design in general. For specific design guidelines for the EM827 Materials PCB, you would need to refer to documentation provided by the manufacturer or consult with their technical support team.
What is the EM827 Materials PCB Fabrication Process?
Without specific information on the EM827 Materials PCB fabrication process, I can outline a typical PCB fabrication process that might be applicable:
- Design Preparation:PCB fabrication begins with the creation of a design file using PCB design software. This file includes the layout of copper traces, component placement, drill holes, and other necessary features.
- Material Selection: Choose the appropriate substrate material based on the requirements of the EM827 Materials PCB. This could involve selecting a specific type of laminate material with desired electrical, mechanical, and thermal properties.
- Layer Stackup Design: Determine the layer stackup configuration based on the PCB’s complexity and requirements. This involves deciding the number of layers, copper thickness, and dielectric materials for each layer.
- Prepreg and Core Lamination: Prepreg (pre-impregnated fiberglass cloth) and core materials are prepared and laminated together to form the PCB substrate. This process involves applying heat and pressure to bond the layers into a single rigid panel.
- Drilling: Holes for component leads, vias, and mounting are drilled into the PCB panel using precision drilling equipment. Small diameter drill bits are used for vias, while larger bits are used for component holes.
- Copper Deposition: Copper is deposited onto the surface of the panel using a process such as electroplating or chemical deposition. This creates a thin layer of copper over the entire substrate, which will be patterned to form the conductive traces.
- Etching: A photoresist layer is applied to the copper surface, and the PCB layout pattern is transferred onto the photoresist using a photographic process. The exposed copper is then etched away using an etchant solution, leaving behind the desired copper traces.
- Surface Finish: Surface finish is applied to protect the exposed copper traces and provide solderability for component attachment. Common surface finishes include hot air solder leveling (HASL), electroless nickel immersion gold (ENIG), and immersion silver.
- Silkscreen and Legend Printing: PCB components, polarity markers, and other identifying information are printed onto the PCB surface using a silkscreen printing process. This helps assembly technicians identify components and reference designators during assembly.
- Testing and Inspection: The fabricated PCBs undergo electrical testing to verify continuity, impedance, and insulation resistance. Visual inspection is also performed to check for defects such as missing traces, shorts, or solder mask errors.
- Routing and Separation: Individual PCBs are routed and separated from the larger panel using CNC milling or routing equipment. This process removes excess material and leaves the finished PCBs ready for assembly.
- Quality Control and Packaging: Final inspection is conducted to ensure that the fabricated PCBs meet quality standards and specifications. The PCBs are then packaged and prepared for shipment to customers or assembly facilities.
This process provides a general overview of PCB fabrication and may vary depending on the specific requirements and materials used for the EM827 Materials PCB.
How do you manufacture EM827 Materials PCB?
Manufacturing EM827 Materials PCB involves a series of steps tailored to the specific requirements of this type of PCB. While I don’t have specific information about EM827 Materials PCB, I can provide a general outline of how you might manufacture it:
- Design Preparation: Begin by creating a detailed design of the PCB using specialized PCB design software. Ensure that the design meets the required specifications for the EM827 Materials PCB, including layout, layer stackup, and material selection.
- Material Selection: Choose the appropriate substrate material for the EM827 Materials PCB based on its electrical, mechanical, and thermal properties. This could involve selecting a high-performance material optimized for specific applications or environments.
- Layer Stackup Design: Determine the layer stackup configuration based on the complexity and requirements of the PCB. Consider factors such as signal integrity, impedance control, and thermal management when designing the layer stackup.
- Circuit Imaging: Transfer the PCB design onto a substrate material using a process such as photolithography. This involves applying a light-sensitive material (photoresist) to the substrate, exposing it to UV light through a mask with the PCB pattern, and then developing the exposed resist to create the circuit pattern.
- Copper Deposition: Deposit a thin layer of copper onto the substrate surface using techniques such as electroplating or sputtering. This forms the conductive traces and pads of the PCB, following the pattern created during the imaging process.
- Etching: Use chemical etching to remove the excess copper from the substrate, leaving behind the desired traces and pads. This process involves immersing the PCB in an etchant solution that selectively dissolves the exposed copper while protecting the rest of the substrate with resist.
- Drilling: Drill holes for component mounting and interconnections using precision drilling equipment. These holes, known as vias and through-holes, allow electrical connections between different layers of the PCB.
- Surface Finish: Apply a surface finish to protect the exposed copper traces and provide solderability for component attachment. Common surface finishes include hot air solder leveling (HASL), electroless nickel immersion gold (ENIG), and immersion silver.
- Solder Mask Application: Apply a solder mask layer over the PCB surface, leaving openings for solder pads and vias. The solder mask protects the copper traces from oxidation and provides insulation between conductive elements.
- Silkscreen Printing: Print component labels, polarity markings, and other identifying information onto the PCB surface using a silkscreen printing process. This helps assembly technicians identify components and reference designators during assembly.
- Testing and Inspection: Perform electrical testing to verify the continuity, impedance, and insulation resistance of the fabricated PCBs. Visual inspection is also conducted to check for defects such as missing traces, shorts, or solder mask errors.
- Routing and Separation: Individual PCBs are routed and separated from the larger panel using CNC milling or routing equipment. This process removes excess material and leaves the finished PCBs ready for assembly.
- Quality Control and Packaging: Conduct final inspection to ensure that the fabricated PCBs meet quality standards and specifications. The PCBs are then packaged and prepared for shipment to customers or assembly facilities.
Throughout the manufacturing process, strict quality control measures are implemented to ensure the reliability and performance of the EM827 Materials PCB. Advanced techniques and equipment may be employed to meet the specific requirements of this type of PCB, such as impedance-controlled routing and high-temperature materials for harsh environments. Collaboration between PCB designers, manufacturers, and end-users is essential to optimize the manufacturing process and achieve the desired outcomes for the EM827 Materials PCB.
How much should an EM827 Materials PCB cost?
Determining the cost of an EM827 Materials PCB can be influenced by various factors including the complexity of the design, the size of the board, the number of layers, the choice of materials, and the quantity ordered.
Here are some factors that might influence the cost:
- Materials: The choice of materials can significantly impact the cost. Specialized materials with high-performance characteristics might be more expensive than standard FR-4 materials.
- Layer Count: PCBs with more layers tend to be more expensive due to the complexity of manufacturing processes involved.
- Size: Larger PCBs require more material and may involve additional manufacturing steps, leading to higher costs.
- Technology Requirements: If the design requires advanced features such as high-frequency signals, controlled impedance, or blind/buried vias, this could increase the cost.
- Quantity: Typically, the unit cost decreases with higher quantities due to economies of scale. Ordering larger quantities can often result in lower per-unit costs.
- Turnaround Time: Expedited manufacturing services may incur additional fees.
Given these considerations, it’s challenging to provide an exact cost without specificdetails about the EM827 Materials PCB in question. To get an accurate cost estimate, it’s best to consult with a PCB manufacturer or supplier. They can review your design specifications and provide a quote based on your requirements and desired quantity.
What is EM827 Materials PCB base material?
Without specific information about the EM827 Materials PCB, it’s difficult to determine the exact base material used. However, PCBs can be manufactured using various base materials depending on the specific requirements of the application.
Common base materials for PCBs include:
- FR-4 (Flame Retardant 4): FR-4 is the most widely used base material for PCBs. It is a composite material made of woven fiberglass cloth impregnated with an epoxy resin binder. FR-4 offers good electrical insulation properties, mechanical strength, and dimensional stability.
- FR-408: FR-408 is an enhanced version of FR-4 with improved electrical performance, particularly at higher frequencies. It is designed to meet the requirements of high-speed digital and RF applications.
- Polyimide (PI): Polyimide is a high-temperature polymer that can withstand elevated temperatures without degrading. PCBs made with polyimide substrates are suitable for applications requiring thermal stability, such as aerospace and automotive electronics.
- Rogers Materials:Rogers Corporation produces a range of high-frequency laminates specifically designed for RF and microwave applications. These materials offer low dielectric loss, stable electrical properties, and excellent performance at high frequencies.
- Isola Materials: Isola is another manufacturer of specialty laminates used in PCB fabrication. Their materials are engineered for specific performance requirements, such as high-speed digital, automotive, or military applications.
- Metal Core PCBs: Metal core PCBs have a metal core (usually aluminum or copper) sandwiched between layers of dielectric material. These PCBs offer excellent thermal conductivity and are commonly used in applications requiring efficient heat dissipation, such as LED lighting and power electronics.
Without more information about the EM827 Materials PCB, it’s challenging to identify the specific base material used. The choice of base material would depend on the electrical, mechanical, thermal, and environmental requirements of the PCB design. If you have access to documentation or specifications for the EM827 Materials PCB, that information might provide more clarity on the base material used.
Which company makes EM827 Materials PCB?
The manufacturer of EM827 Materials PCB is not clear yet. However, if your company has the technical expertise and capabilities in PCB manufacturing and wishes to produce EM827 Materials PCB, your company could potentially become one of the manufacturers.
To become a manufacturer of EM827 Materials PCB, your company would need the following capabilities and resources:
- Technical Expertise: Your company needs expertise in PCB design and manufacturing. This includes proficiency in PCB design software, material selection, laminate manufacturing, circuit imaging, chemical etching, drilling, surface treatment, and quality control.
- Production Equipment:Your company needs to have advanced PCB manufacturing equipment for processes such as imaging, etching, drilling, surface treatment, and inspection. These machines should meet the high precision and quality requirements of manufacturing.
- Material Supply Chain: Your company needs to establish a stable supply chain for materials such as substrate materials, copper foils, surface treatment materials, etc., meeting the requirements of EM827 Materials PCB.
- Quality Management System: Establish a robust quality management system, including developing standard operating procedures (SOP), implementing strict quality control and testing processes, and continuously improving the manufacturing process to ensure product quality and meet customer requirements.
- Certifications and Compliance: Ensure that your company complies with relevant certifications and regulations, such as ISO 9001 quality management system certification, UL safety certification, etc. This will enhance customer confidence in the quality and reliability of your company’s products.
As a company, we have advanced manufacturing equipment and an experienced technical team capable of meeting the requirements of manufacturing EM827 Materials PCB. We prioritize quality and customer satisfaction, committed to providing high-quality products and excellent services to our customers.
Our manufacturing process is carefully designed to produce high-quality PCBs that meet design requirements. We work with reliable material suppliers to ensure the supply of high-quality substrate materials and other materials. We have strict quality control procedures and conduct rigorous inspections and testing at every stage of production to ensure product quality and consistency.
As your partner, we will work closely with you to understand your requirements and provide customized solutions. We are dedicated to building long-term partnerships and supporting your business success.
What are the 7 qualities of good customer service?
Good customer service is characterized by several key qualities that contribute to a positive experience for customers. Here are seven qualities of good customer service:
- Responsiveness: Good customer service involves being prompt and responsive to customer inquiries, concerns, and requests. This includes answering phone calls and emails promptly, as well as addressing customer issues in a timely manner.
- Empathy: Empathy is essential for understanding and relating to customers’ feelings, needs, and concerns. Good customer service representatives demonstrate empathy by actively listening to customers, acknowledging their emotions, and showing genuine concern for their well-being.
- Clear Communication: Clear communication is crucial for ensuring that customers understand information, instructions, and solutions provided by customer service representatives. Good customer service involves using clear and concise language, avoiding jargon, and confirming understanding to prevent misunderstandings.
- Professionalism:Good customer service representatives maintain a professional demeanor and attitude when interacting with customers. This includes being courteous, respectful, and polite, regardless of the customer’s behavior or attitude.
- Knowledgeability: Good customer service requires having a thorough understanding of products, services, policies, and procedures. Customer service representatives should be knowledgeable and well-trained to provide accurate information, answer questions, and offer helpful solutions to customer issues.
- Problem-Solving Skills: Good customer service involves effectively resolving customer issues and concerns. This requires problem-solving skills, creativity, and the ability to think critically to identify root causes and develop appropriate solutions that meet the customer’s needs.
- Consistency: Consistency is key to providing good customer service across all interactions and touchpoints. Customers expect a consistent level of service quality, responsiveness, and professionalism every time they interact with a company, whether it’s online, over the phone, or in person.
By embodying these qualities, businesses can build trust, loyalty, and satisfaction among their customer base, ultimately leading to improved customer retention and positive word-of-mouth referrals.
FAQs
What are the key properties of EM827 Materials PCB?
The key properties of EM827 Materials PCB depend on the specific materials used but may include high electrical conductivity, low dielectric constant, excellent thermal stability, and resistance to environmental factors such as moisture or temperature fluctuations.
What applications are EM827 Materials PCBs suitable for?
EM827 Materials PCBs are suitable for a wide range of applications across industries such as telecommunications, aerospace, automotive, medical devices, and industrial equipment. They are often used in high-frequency and high-speed circuits, RF/microwave applications, and environments with demanding performance requirements.
How does EM827 Materials PCB differ from standard PCB materials?
EM827 Materials PCBs differ from standard PCB materials such as FR-4 in terms of their composition, properties, and performance characteristics. They are typically engineered to offer superior performance in specific areas, such as signal integrity, thermal management, or reliability.
Can EM827 Materials PCBs be manufactured using standard PCB fabrication processes?
Yes, EM827 Materials PCBs can typically be manufactured using standard PCB fabrication processes, although some adjustments or optimizations may be necessary to accommodate the unique properties of the materials involved.
Where can I find suppliers or manufacturers of EM827 Materials PCBs?
Suppliers or manufacturers of EM827 Materials PCBs may include specialized PCB fabrication companies, material suppliers, or distributors who offer custom PCB manufacturing services. It’s advisable to research and contact multiple suppliers to compare capabilities, pricing, and lead times.
What factors should I consider when choosing EM827 Materials PCB for my application?
When choosing EM827 Materials PCB for your application, consider factors such as electrical performance requirements, environmental conditions, budget constraints, and compatibility with existing components or systems. Additionally, consult with PCB design experts or material specialists to ensure the selected materials meet your specific needs.