CSP Package Substrate Manufacturer
CSP Package Substrate Manufacturer,A CSP (Chip-Scale Package) Substrate is a critical component in miniaturized electronic packaging, designed to support and connect integrated circuits (ICs) directly. It enables the IC to be mounted in a package that is nearly the same size as the chip itself, optimizing space efficiency. Comprising multiple layers including insulating, conductive, and metal layers, CSP Substrates ensure reliable electrical connections and effective thermal management. This technology is essential for high-density applications in smartphones, wearables, and other compact electronic devices, where space-saving and performance are crucial. CSP Substrates facilitate advanced miniaturization and integration in modern electronics.
CSP Package Substrate refers to a packaging technology utilized in the integration of semiconductor chips. CSP, an acronym for Chip Scale Package, embodies a packaging approach that seeks to minimize the package size to align closely with the chip’s functionality. The Package Substrate serves as the fundamental substrate supporting the chip and other components within the package.
The chief advantage of CSP Package Substrate lies in its compact and lightweight design, facilitating the integration of additional features within confined spaces. This technology is gaining prominence in applications such as mobile devices, Internet of Things (IoT) devices, and other scenarios with stringent size and weight constraints. The reduction in package size not only meets these requirements but also contributes to heightened performance and reliability of electronic devices.
Moreover, CSP Package Substrate plays a role in diminishing power consumption, enhancing heat dissipation efficiency, and fostering increased integration. These attributes hold significance in the contemporary design and manufacturing processes of electronic devices, particularly in the pursuit of products that are smaller, lighter, and offer superior performance.
It’s noteworthy that ongoing technological advancements may introduce new developments and changes beyond the scope of my knowledge cutoff date.
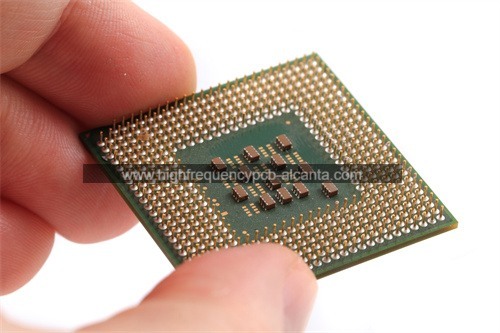
CSP Package Substrate Manufacturer
What functions does CSP Package Substrate serve?
CSP Package Substrate serves as a cornerstone in the packaging and integration processes of semiconductor chips, fulfilling a spectrum of crucial functions:
Size Optimization: The primary objective of CSP Package Substrate revolves around fine-tuning packaging dimensions. This holds particular significance in applications where space constraints, such as those in mobile devices and IoT scenarios, demand meticulous size considerations.
Facilitating Seamless Chip Integration: The Package Substrate acts as a robust foundation, ensuring the seamless integration of the semiconductor chip alongside other essential components within the package. This involves meticulous attention to alignment and connectivity.
Sleek and Efficient Design: CSP aspires to achieve a chip-scale design philosophy, aiming for a packaging size that harmonizes closely with the dimensions of the semiconductor chip. This results in an aesthetically streamlined and operationally efficient package.
Elevated Integration Density: CSP Package Substrate empowers higher integration density, enabling the inclusion of an expanded array of features and functionalities within a confined spatial envelope. This proves particularly advantageous in applications demanding extensive capabilities within a limited form factor.
Weight Reduction: The inherent compactness and lightweight attributes of CSP contribute significantly to an overall reduction in the weight of electronic devices. This renders CSP technology well-suited for applications imposing stringent weight limitations.
Performance Enhancement: Through meticulous size reduction and optimized packaging design, CSP Package Substrate plays a pivotal role in elevating the electrical performance of both the semiconductor chip and the overarching electronic device.
Power Efficiency: CSP technology is engineered to play a role in curtailing power consumption, thereby fostering heightened energy efficiency in electronic devices.
Efficient Heat Dissipation: The design of CSP Package Substrate is often crafted with considerations for efficient heat dissipation, ensuring that the semiconductor chip operates seamlessly within optimal temperature ranges.
In essence, CSP Package Substrate emerges as a linchpin in the creation of electronic devices characterized by compactness, lightness, and operational efficiency, achieved through meticulous size management, adept chip integration support, and performance optimization.
What are the different types of CSP Package Substrate?
CSP Package Substrate comes in a diverse array of types, each meticulously crafted to cater to distinct requirements across various applications. Let’s delve into some prominent variations:
BGA (Ball Grid Array): Notable for its grid of solder balls beneath the package, BGA excels in optimizing both thermal and electrical performance.
WLCSP (Wafer-Level Chip Scale Package): Taking packaging to the wafer level before chip separation, WLCSP delivers a compact package ideal for ultra-compact designs.
LGA (Land Grid Array): Sharing similarities with BGA, LGA employs a grid of flat pads for electrical connections, offering enhanced mechanical stress relief.
CSP PoP (CSP Package on Package): Introducing the concept of stacking CSP packages, CSP PoP allows for expanded functionality without a proportional increase in overall footprint.
Flip-Chip CSP: In this innovative approach, the chip is strategically flipped, enabling direct connection of its active side to the substrate and thereby enhancing thermal and electrical performance.
MCM (Multi-Chip Module): Leveraging CSP technology, MCM integrates multiple chips within a single module, effectively minimizing the overall size.
3D IC (Three-Dimensional Integrated Circuit): A sophisticated packaging technique involving the stacking of semiconductor layers, 3D ICs benefit from CSP’s space-saving attributes.
Fan-Out WLP (Wafer-Level Packaging): Evolving from WLCSP, Fan-Out WLP incorporates additional components into the package, facilitating advanced system integration.
FOC (Fan-Out Chip on Substrate): Representing an advanced integration approach, FOC redistributes and integrates multiple chips onto a shared substrate, fostering compact designs with elevated integration levels.
These nuanced variations within CSP Package Substrate empower manufacturers with a versatile toolkit, enabling tailored choices based on application specifics, form factor considerations, and desired integration levels.
How is CSP Package Substrate related to IC packaging?
CSP Package Substrate is intricately tied to the field of IC (Integrated Circuit) packaging, representing a specialized approach within this technology. The relationship between the two can be understood through various aspects:
Packaging Technology Specialization: CSP Package Substrate serves as a dedicated packaging technology specifically designed for semiconductor chips. It operates within the broader scope of IC packaging, encompassing a variety of packaging methods.
Emphasis on Compactness: A distinctive feature of CSP is its commitment to minimizing package size, in line with the overarching trend in IC packaging to create compact packages that closely match the dimensions of the chips. Both CSP and general IC packaging share the goal of responding to the demand for smaller and space-efficient packages.
Optimizing Integration Density: CSP, along with IC packaging as a whole, shares the common objective of maximizing the integration density of electronic components within a given package. This involves strategically arranging and connecting components to make the most efficient use of space.
Ensuring Functionality and Reliability: Both CSP Package Substrate and broader IC packaging are united in their primary objective of ensuring the proper functionality and reliability of integrated circuits. This includes considerations for robust electrical connections, effective thermal management, and protection against external factors.
Application Diversity: CSP and IC packaging technologies find application across a broad spectrum of electronic devices, including mobile phones, IoT devices, consumer electronics, and industrial applications. The choice of packaging technology is determined by the specific requirements of each device and its intended use.
Continuous Technological Evolution: Both CSP and general IC packaging technologies undergo continuous evolution to meet the advancing demands of technology. This involves ongoing innovations in materials, design methodologies, and manufacturing processes, aiming to enhance overall performance, reduce power consumption, and cater to the diverse requirements of applications.
In essence, CSP Package Substrate stands as a specialized facet within the expansive realm of IC packaging. Its focus on creating compact, high-performance packages aligns with the shared goals of ensuring the functionality, reliability, and efficiency of integrated circuits in electronic devices.
How does CSP Package Substrate differ from traditional PCBs?
CSP (Chip Scale Package) Package Substrate and traditional PCBs (Printed Circuit Boards) are distinctive entities in the realm of electronics, each with its unique characteristics, functions, and areas of application. Let’s delve into the key differentiators between them:
Core Objective:
CSP Package Substrate: Specifically crafted for the streamlined packaging of integrated circuits (ICs), acting as a foundational platform for mounting and interconnecting semiconductor chips. The central focus lies in minimizing size and maximizing integration density.
Traditional PCBs: Serve as the fundamental architecture of electronic devices, providing a canvas for an array of components like resistors, capacitors, and ICs. PCBs facilitate essential electrical connections, supporting the holistic functionality of a device.
Approach to Component Mounting:
CSP Package Substrate: Specialized in mounting and interconnecting semiconductor chips, particularly in the domain of chip-scale packaging where the package closely mirrors the chip’s dimensions.
Traditional PCBs: Accommodate a diverse array of electronic components, leveraging methods such as surface-mount technology (SMT) or through-hole technology (THT) to ensure effective component placement.
Integration Density Emphasis:
CSP Package Substrate: Places a significant emphasis on achieving heightened integration density to create a compact package size, particularly crucial in scenarios where spatial constraints play a pivotal role.
Traditional PCBs: While capable of supporting high integration density, their design is adaptable, catering to various electronic components and diverse form factors.
Package Size Dynamics:
CSP Package Substrate: Recognizable for its reduced footprint, meticulously designed to closely match the size of the semiconductor chip it encapsulates.
Traditional PCBs: Available in diverse sizes, offering flexibility in layout and meeting the varied requirements of electronic devices.
Applications Range:
CSP Package Substrate: Frequently employed in contexts where miniaturization is pivotal, such as in mobile devices, wearables, and compact electronic gadgets.
Traditional PCBs: Universally applied across a spectrum of electronic devices, spanning computers, appliances, industrial equipment, and communication systems.
Design Complexity Considerations:
CSP Package Substrate: Designs are intricately crafted for chip-scale packaging, often integrating advanced manufacturing techniques to achieve an efficient and compact layout.
Traditional PCBs: Designs showcase significant diversity, contingent upon the complexity of the electronic system they support, potentially featuring multiple layers, intricate routing, and a variety of component types.
In essence, CSP Package Substrate excels in chip-scale packaging, prioritizing miniaturization and integration density, while traditional PCBs serve as versatile platforms accommodating a broad range of electronic components and applications.
What is the main structure and production technology of CSP Package Substrate?
CSP (Chip Scale Package) Package Substrate is engineered with a distinctive structure and production methodology tailored for the seamless integration of semiconductor chips. While nuances exist across designs, here’s a broad overview of the core structure and production processes associated with CSP Package Substrate:
Core Structure:
Substrate Material:
Serving as the groundwork, the substrate is crafted from materials such as organic laminates, build-up films, or inorganic ceramics.
Solder Balls or Pads:
On the underside of the substrate, arrays of solder balls or flat pads are strategically placed, serving as pivotal connection points for electrical pathways and potential facilitators of thermal dissipation.
Die Attach Area:
This designated area witnesses the bonding of the semiconductor chip to the substrate, a process that may involve wire bonding or flip-chip bonding to establish secure connections.
Routing and Traces:
Intricate routing and traces adorn the substrate, creating pathways that facilitate electrical connections between the semiconductor chip and other integrated components.
Passive Components (Optional):
Some CSP designs may incorporate passive components, like resistors or capacitors, directly onto the substrate, elevating the integration level.
Encapsulation or Underfill (Optional):
As an additional layer of protection, an encapsulation layer or underfill material may be applied, safeguarding the semiconductor chip and enhancing overall mechanical stability.
Production Approach:
Wafer-Level Processing (for WLCSP):
In Wafer-Level Chip Scale Packaging (WLCSP), the packaging journey begins at the wafer level before individual chips undergo separation. Processes encompass redistribution layer (RDL) formation, die attachment, and the placement of balls or pads.
Stencil Printing (for Solder Deposition):
Solder balls or pads are artfully deposited onto the substrate using stencil printing or comparable deposition methods.
Die Attach and Bonding:
The semiconductor chip finds its place on the substrate through die attachment techniques, while bonding methods like wire bonding or flip-chip bonding establish vital electrical connections.
Plating and Etching (for Traces):
Metal plating and etching techniques come into play to craft routing traces on the substrate, carving out the necessary electrical pathways.
Encapsulation (for Protection):
Employing encapsulation techniques, such as molding, adds an extra layer of defense, shielding the semiconductor chip and integrated components from external factors.
Quality Control and Testing:
Stringent quality control practices and meticulous testing procedures are paramount to ensuring the reliability and functionality of the CSP Package Substrate. This entails electrical testing, thermal assessments, and comprehensive visual inspections.
The particulars of CSP Package Substrate, both in structure and production, pivot on design preferences, material selections, and the specific demands of the application. Continuous strides in semiconductor packaging technologies contribute to the ongoing refinement and evolution of CSP designs and production methodologies.
Frequently Asked Questions (FAQs)
What defines CSP Package Substrate?
CSP Package Substrate is a packaging technology designed for semiconductor chips, emphasizing compactness and efficient integration. It involves creating a substrate closely aligned with the chip’s dimensions.
What are the standout features of CSP Package Substrate?
Key features encompass a streamlined design, chip integration support, solder balls or pads for electrical connections, and optional integration of passive components. CSP enhances integration density, shrinks package size, and contributes to improved performance.
In which applications is CSP Package Substrate utilized?
CSP Package Substrate is employed in diverse electronic devices, such as mobile phones, IoT devices, consumer electronics, and industrial applications. Its compact size and high integration make it ideal for products with space constraints.
What materials are commonly employed in CSP Package Substrate?
CSP substrates can be fashioned from organic materials like laminates or build-up films, or inorganic materials such as ceramics. Material selection depends on factors like thermal requirements, electrical properties, and cost considerations.
What does the production process of CSP Package Substrate entail?
Production involves wafer-level processing (for WLCSP), stencil printing for solder deposition, die attach and bonding, plating and etching for trace creation, optional encapsulation for protection, and rigorous quality control and testing.
What advantages does CSP Package Substrate bring?
CSP offers benefits like size reduction, increased integration density, weight savings, enhanced performance, and support for applications with stringent size and weight limitations.
Are there different types of CSP Package Substrate?
Yes, various types exist, including BGA, WLCSP, LGA, CSP PoP, each with specific advantages based on application requirements.
How do I choose a CSP Package Substrate manufacturer?
Consider factors such as reputation, experience, production capabilities, technology offerings, and ability to meet specific requirements. Reviews, certifications, and past projects are valuable considerations.
What trends are influencing the future of CSP Package Substrate manufacturing?
Ongoing trends include material advancements, increased emphasis on 3D integration, improvements in thermal management, and efforts to enhance power efficiency and reliability in CSP Package Substrate designs.
Conclusion
In a nutshell, CSP Package Substrate emerges as a game-changer in the field of semiconductor packaging, providing an efficient avenue for integrating chips into electronic devices seamlessly. The core principles of this packaging approach revolve around compactness, heightened integration density, and superior performance. Major industry players, including Amkor Technology, ASE Group, STATS ChipPAC, Siliconware Precision Industries Co., Ltd. (SPIL), and Shinko Electric Industries Co., Ltd., underscore the pivotal role of this technology.
Breaking down the components of CSP Package Substrate reveals a meticulous design, incorporating substrate materials, solder balls or pads, die attach regions, routing and traces, and the optional inclusion of passive components. The production journey, ranging from wafer-level processing to stencil printing for solder application, underscores the intricacies involved in creating these substrates. A stringent adherence to quality control measures ensures the dependability and functionality of the final product.
CSP Package Substrate extends its impact across diverse electronic devices, adeptly meeting the dynamic needs of modern technologies such as mobile phones, IoT devices, and consumer electronics. The versatility of CSP, showcased through material choices, production techniques, and integration possibilities, positions it as an adaptable solution for a variety of application demands.
Looking forward, the trajectory of CSP Package Substrate manufacturing is influenced by ongoing trends. These include breakthroughs in materials, an intensified focus on 3D integration strategies, advancements in thermal management, and an unwavering commitment to enhancing power efficiency and reliability. As the semiconductor packaging landscape undergoes continuous evolution, CSP retains its position at the forefront, guiding the course of innovation and efficiency in electronic device design.