Cross Blind/buried Vias PCB Manufacturing
Cross Blind/buried Vias PCB Manufacturing,Cross Blind/Buried Vias PCBs represent a cutting-edge advancement in printed circuit board technology. These boards incorporate a sophisticated network of vias, including blind and buried vias, strategically positioned within the layers of the PCB. Blind vias connect the outer layers of the board to one or more inner layers, while buried vias establish connections solely within the inner layers without penetrating the outer surfaces. This intricate design allows for high-density interconnections and enables the routing of signals across different layers without compromising board integrity. Cross Blind/Buried Vias PCBs find extensive applications in industries requiring superior signal integrity, such as telecommunications, aerospace, and high-speed digital electronics. Their ability to minimize signal distortion, enhance thermal management, and optimize space utilization makes them indispensable for modern electronic systems where performance and reliability are paramount. With their advanced construction and capabilities, Cross Blind/Buried Vias PCBs represent the forefront of PCB technology, driving innovation and pushing the boundaries of electronic design.
What is a Cross Blind/Buried Vias PCB?
A Cross Blind/Buried Vias PCB refers to a type of printed circuit board (PCB) design that incorporates both blind and buried vias. Here’s a breakdown of these terms:
- Blind Vias: Blind vias are holes that are drilled from the outer surface of one or more layers of a PCB and terminate at an internal layer without penetrating through the entire board. They allow connections between the surface layers and one or more inner layers without going through the entire thickness of the PCB.
- Buried Vias: Buried vias are holes that are drilled completely through inner layers of a multilayer PCB, connecting one or more inner layers but not extending to the outer layers. They are not visible from the outer surface of the PCB.
A Cross Blind/Buried Vias PCB utilizes both types of vias in its design. This can be advantageous in complex PCB designs where there is a need for high-density interconnections while maintaining signal integrity and minimizing signal distortion. By strategically placing blind and buried vias, designers can optimize routing and reduce signal interference.
Cross Blind/Buried Vias PCBs are commonly used in applications such as high-speed digital circuits, RF (radio frequency) circuits, and other advanced electronic systems where space constraints and signal integrity are critical considerations.
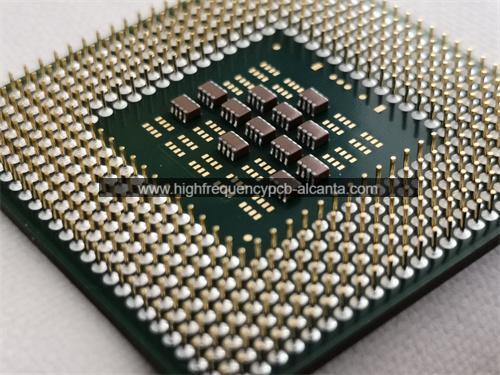
Cross Blind/buried Vias PCB Manufacturing
What are the Cross Blind/Buried Vias PCB Design Guidelines?
Here are some general guidelines for designing a PCB with cross blind/buried vias:
- Layer Stacking: Plan your PCB layer stackup carefully. Determine which layers will contain blind vias, buried vias, and which layers will be used for signal routing and power/ground planes.
- Via Types and Placement: Strategically place blind and buried vias to optimize signal routing and reduce signal distortion. Consider factors such as signal integrity, impedance control, and high-speed signal paths.
- Minimum Annular Ring: Ensure that the annular ring (the copper pad surrounding the via hole) meets minimum requirements for reliability and manufacturability. Consult your PCB manufacturer for specific guidelines.
- Aspect Ratio: Consider the aspect ratio of the vias, which is the ratio of the via’s length to its diameter. High aspect ratios may require special manufacturing techniques and can affect signal integrity.
- Vias in High-Speed Signal Paths: Avoid placing vias in critical high-speed signal paths whenever possible. If vias are necessary, minimize their impact on signal integrity by carefully planning their placement and adhering to best practices for via design.
- Thermal Considerations: Pay attention to thermal management, especially if vias are used for heat dissipation. Ensure that vias are properly connected to thermal pads or planes to efficiently transfer heat away from components.
- Manufacturability: Consult with your PCB manufacturer early in the design process to ensure that the chosen via types and placements are compatible with their manufacturing capabilities. Consideration should be given to drilling capabilities, registration accuracy, and alignment tolerances.
- Documentation: Clearly document the location, type, and purpose of blind and buried vias in your PCB design files. This information will be crucial for fabrication and assembly processes.
- Design Rule Check (DRC): Run a design rule check (DRC) to ensure that your PCB design complies with the manufacturing capabilities and constraints related to blind and buried vias.
- Test and Validation: Perform thorough testing and validation of your PCB design to verify signal integrity, impedance matching, and overall performance, especially in areas where blind and buried vias are used extensively.
By following these guidelines, you can optimize your cross blind/buried vias PCB design for reliable operation, manufacturability, and performance.
What is the Cross Blind/Buried Vias PCB Fabrication Process?
The fabrication process for a PCB with cross blind/buried vias involves several steps, which may vary slightly depending on the specific requirements of the design and the capabilities of the PCB manufacturer. Here’s an overview of the typical process:
- Design Preparation: Create or obtain the PCB design files, including the layout, schematic, and any design constraints. Ensure that the design incorporates cross blind/buried vias according to the project requirements.
- Material Selection: Choose the appropriate substrate material for the PCB based on factors such as dielectric constant, thermal conductivity, and mechanical properties. Discuss material options with the PCB manufacturer to ensure compatibility with the fabrication process.
- Layer Stackup Design: Determine the layer stackup configuration, specifying the arrangement of signal, power, and ground planes, as well as the location of blind and buried vias within the stack. Consider factors such as signal integrity, impedance control, and thermal management.
- Drilling: Drill the via holes in the PCB substrate using precision drilling equipment. For blind vias, the holes are drilled from the outer layers of the PCB and terminate at specified inner layers. For buried vias, the holes are drilled completely through inner layers without penetrating the outer layers.
- Via Plating: After drilling, the via holes are plated with conductive material (typically copper) to establish electrical connections between the different layers of the PCB. This process involves electroplating or chemical deposition to deposit a thin layer of copper inside the via holes.
- Circuit Patterning: Apply a layer of photoresist to the PCB surface and expose it to UV light through a photomask to transfer the circuit pattern onto the substrate. Then, etch away the unwanted copper using chemical etchants, leaving behind the desired copper traces and vias.
- Dielectric Lamination: Assemble the individual layers of the PCB stackup together, interleaving them with prepreg layers and bonding them under heat and pressure to form a single, multilayered substrate. This process ensures proper alignment and adhesion of the layers.
- Plating and Surface Finish: Plate the exposed copper surfaces with a protective finish (e.g., HASL, ENIG, OSP) to prevent oxidation and ensure solderability. Apply solder mask over the non-conductive areas of the PCB to define the soldering pads and provide additional protection.
- Final Inspection and Testing: Conduct thorough visual inspection and electrical testing of the completed PCB to verify dimensional accuracy, connectivity, and functionality. This may involve automated optical inspection (AOI), electrical continuity testing, and other quality control measures.
- Fabrication Documentation: Generate documentation detailing the fabrication process, materials used, and any specific instructions for assembly and testing. This information is essential for traceability and quality assurance.
By following these steps, manufacturers can fabricate PCBs with cross blind/buried vias to meet the requirements of diverse electronic applications, ranging from consumer electronics to aerospace systems.
How do you manufacture a Cross Blind/Buried Vias PCB?
Manufacturing a cross blind/buried vias PCB involves several key steps:
- Design Preparation: The process begins with the PCB design. Designers specify the locations of blind and buried vias in the PCB layout software, along with their respective diameters, pad sizes, and other relevant parameters.
- Layer Stackup: Determine the layer stackup configuration, which specifies the arrangement and order of the PCB layers. Layers containing blind and buried vias are typically defined at this stage.
- Drilling: Drilling is a critical step in manufacturing blind and buried vias. For blind vias, holes are drilled from the outer surface of the PCB to a certain depth, terminating within the inner layers. Buried vias are drilled completely through specific inner layers of the PCB. Advanced drilling equipment with high precision is used for this purpose.
- Electroless Copper Deposition: After drilling, the via walls are chemically treated to promote adhesion, followed by an electroless copper deposition process. This step ensures that the interior walls of the vias are plated with a thin layer of copper, providing electrical conductivity and facilitating subsequent plating processes.
- Plating and Surface Finishing: The PCB undergoes a series of plating processes to add additional copper layers and to create circuit traces on the surface layers. Surface finishing techniques such as immersion gold, HASL (Hot Air Solder Leveling), or ENIG (Electroless Nickel Immersion Gold) may be applied to protect the exposed copper surfaces and enhance solderability.
- Lamination: The individual layers of the PCB are laminated together under high pressure and temperature to form a single, cohesive structure. This process bonds the layers together and encapsulates the vias within the PCB.
- Etching and Imaging: Photolithography techniques are used to define the circuit traces and patterns on the PCB layers. A photoresist layer is applied and selectively exposed to UV light through a photomask, followed by etching to remove unwanted copper and reveal the desired circuitry.
- Solder Mask Application: A solder mask layer is applied to the PCB surface to protect the circuit traces from environmental factors and facilitate soldering. Openings are created in the solder mask to expose the solder pads and vias for component attachment.
- Silkscreen Printing: If necessary, component designators, logos, and other markings are printed on the PCB surface using silkscreen printing techniques.
- Testing and Inspection: The manufactured PCB undergoes rigorous testing and inspection processes to ensure compliance with design specifications, functionality, and quality standards. Various tests, including electrical continuity testing, impedance testing, and visual inspection, may be performed.
- Assembly: Once the PCBs pass inspection, they are ready for component assembly. Components are soldered onto the PCB using surface mount technology (SMT) or through-hole technology (THT), depending on the design requirements.
- Final Testing: The assembled PCBs undergo final testing to verify proper functionality and performance before they are packaged and shipped to customers.
Throughout the manufacturing process, strict quality control measures are implemented to ensure that the cross blind/buried vias PCB meets the required specifications and standards for reliability and performance. Collaboration between PCB designers, manufacturers, and assembly partners is essential to achieve successful production of these advanced PCBs.
How much should a Cross Blind/Buried Vias PCB cost?
The cost of a cross blind/buried vias PCB can vary significantly depending on various factors including but not limited to:
- Board Size: Larger PCBs typically cost more due to the increased material and manufacturing complexity.
- Layer Count: The number of layers in the PCB affects its complexity and manufacturing cost. Cross blind/buried vias PCBs often have multiple layers, which can increase the cost.
- Via Density: Higher via density, including blind and buried vias, adds complexity to the manufacturing process and may increase the cost.
- Material Selection: Different PCB materials have varying costs. High-performance materials with specific characteristics such as high-frequency laminates can be more expensive.
- Surface Finish: The choice of surface finish (e.g., HASL, ENIG, immersion gold) can impact the cost of the PCB.
- Copper Weight: Thicker copper layers can increase the cost of the PCB due to the additional material and manufacturing requirements.
- Trace Width/Spacing: PCB designs with finer trace widths and spacing may require more precise manufacturing processes, potentially increasing the cost.
- Tolerances and Specifications: Tighter tolerances and specific design requirements may require specialized manufacturing techniques and can contribute to higher costs.
- Volume: Larger production volumes typically result in lower per-unit costs due to economies of scale. However, prototype or low-volume orders may incur higher costs per unit.
- Manufacturing Capabilities: The capabilities of the chosen PCB manufacturer, including their equipment, expertise, and quality standards, can influence the cost.
- Lead Time: Expedited manufacturing services often come with additional costs compared to standard lead times.
It’s essential to work closely with your chosen PCB manufacturer to obtain an accurate quote based on your specific design requirements and production volume. Generally, cross blind/buried vias PCBs tend to be more expensive compared to standard PCBs due to their increased complexity and manufacturing requirements. Prices can range from a few dollars for simple prototypes to hundreds or even thousands of dollars for complex, high-performance PCBs in production quantities.
What is the Cross Blind/Buried Vias PCB base material?
The choice of base material for a cross blind/buried vias PCB depends on various factors including the application requirements, desired electrical performance, thermal considerations, and budget constraints. However, some common base materials used for manufacturing cross blind/buried vias PCBs include:
- FR-4 (Flame Retardant-4): FR-4 is the most widely used base material for PCBs due to its excellent balance of electrical properties, mechanical strength, and cost-effectiveness. It is a type of epoxy-based laminate reinforced with woven glass fiber.
- High-Frequency Laminates: For applications requiring high-frequency operation, such as RF (radio frequency) circuits and microwave systems, specialized high-frequency laminates are used. These laminates offer low dielectric loss, consistent electrical properties over a wide frequency range, and excellent signal integrity.
- Polyimide (PI): Polyimide-based materials are known for their high-temperature resistance, making them suitable for applications requiring elevated operating temperatures. They are commonly used in aerospace, automotive, and other harsh environment applications.
- Rogers Materials: Rogers Corporation offers a range of high-performance laminates specifically designed for demanding applications such as high-frequency RF/microwave circuits. These materials offer superior electrical properties, thermal stability, and reliability.
- Metal Core PCBs: For applications requiring enhanced thermal management, such as LED lighting and power electronics, metal core PCBs (MCPCBs) are used. These PCBs feature a metal core (typically aluminum or copper) for efficient heat dissipation.
- Flex PCB Materials: Flexible PCBs, also known as flex circuits, are manufactured using flexible base materials such as polyimide or polyester. They are ideal for applications requiring bendability or space constraints.
- Composite Materials: Some advanced applications may require composite materials tailored to specific performance requirements. These materials may incorporate a combination of epoxy resins, ceramics, or other additives to achieve desired electrical, mechanical, or thermal properties.
When selecting the base material for a cross blind/buried vias PCB, it’s crucial to consider factors such as dielectric constant, dissipation factor, thermal conductivity, dimensional stability, and environmental factors to ensure optimal performance and reliability. Additionally, consulting with your PCB manufacturer or materials supplier can help you choose the most suitable material for your application.
Which company manufactures Cross Blind/Buried Vias PCB?
There are many companies that manufacture Cross Blind/Buried Vias PCBs, some well-known PCB manufacturers include Foxconn, OKI, Eaton, and JLCPCB. These companies have advanced production equipment, rich experience, and professional teams to meet the diverse needs of customers and provide high-quality products and services.
As a professional PCB manufacturer, our company can also produce Cross Blind/Buried Vias PCBs. We have advanced manufacturing processes and equipment to achieve complex blind and buried via technologies to meet customers’ requirements for high-density interconnects and signal integrity. Our team has extensive experience and can provide customized solutions for customers, precisely manufacturing according to their requirements and specifications.
We are committed to providing customers with high-quality products and professional services. From design to production to delivery, we strictly control the quality to ensure that every PCB meets customer requirements and standards. We value communication and cooperation with customers, understand their needs, and provide customized solutions to meet their specific requirements.
Our manufacturing process follows industry standards rigorously. From raw material procurement to production processing to final inspection, every step is carefully managed and strictly controlled to ensure product quality and performance meet customer expectations.
In summary, as a PCB manufacturer with extensive experience and professional technology, we have the capability to produce Cross Blind/Buried Vias PCBs and provide customers with high-quality products and excellent services. We are willing to work with customers to achieve mutual development and win-win situations.
What are the 7 qualities of good customer service?
Good customer service is characterized by several key qualities that contribute to positive interactions between a company and its customers. Here are seven qualities of good customer service:
- Responsiveness: Good customer service involves being prompt and responsive to customer inquiries, requests, and issues. This includes promptly answering phone calls, replying to emails, and addressing customer concerns in a timely manner.
- Empathy: Empathy is the ability to understand and share the feelings of others. Good customer service representatives demonstrate empathy by actively listening to customers, acknowledging their concerns, and showing genuine concern for their needs and experiences.
- Professionalism: Professionalism entails maintaining a courteous and respectful demeanor when interacting with customers, regardless of the situation. This includes using polite language, maintaining composure, and treating customers with dignity and respect.
- Knowledgeability: Good customer service representatives possess a deep understanding of their company’s products, services, policies, and procedures. They are able to provide accurate information, answer questions, and offer helpful recommendations to assist customers effectively.
- Problem-solving skills: Effective problem-solving skills are essential for resolving customer issues and concerns in a satisfactory manner. Good customer service representatives are resourceful, proactive, and capable of finding creative solutions to address customer needs and resolve conflicts.
- Consistency: Consistency is important for building trust and credibility with customers. Good customer service involves providing consistent levels of quality and support across all interactions and touchpoints, regardless of the time or channel.
- Follow-up and follow-through: Good customer service doesn’t end with the resolution of a customer’s immediate issue. It also involves following up with customers to ensure their satisfaction, as well as following through on any commitments or promises made during the interaction.
By embodying these qualities, businesses can cultivate positive relationships with their customers, foster loyalty, and differentiate themselves from competitors in the marketplace.
FAQs (Frequently Asked Questions)
What are Cross Blind/Buried Vias PCBs?
Cross Blind/Buried Vias PCBs are types of printed circuit boards that incorporate both blind and buried vias. These vias allow for interconnections between different layers of the PCB without traversing the entire thickness.
What are the advantages of using Cross Blind/Buried Vias PCBs?
Cross Blind/Buried Vias PCBs offer several advantages, including increased routing density, improved signal integrity, reduced signal distortion, and enhanced thermal management. They are particularly beneficial in high-speed digital circuits and RF applications.
What are the differences between blind and buried vias?
Blind vias connect the outer layers of a PCB to one or more inner layers without penetrating through the entire board thickness. Buried vias, on the other hand, connect inner layers of the PCB without extending to the outer layers.
What factors should be considered when designing Cross Blind/Buried Vias PCBs?
Designers should consider factors such as layer stackup, via placement, via size, aspect ratio, signal integrity, thermal management, and manufacturability when designing Cross Blind/Buried Vias PCBs.
What materials are commonly used for Cross Blind/Buried Vias PCBs?
Common materials used for Cross Blind/Buried Vias PCBs include FR-4 (Flame Retardant-4), high-frequency laminates, polyimide (PI), Rogers materials, and metal core materials for enhanced thermal management.
How are Cross Blind/Buried Vias PCBs manufactured?
The manufacturing process for Cross Blind/Buried Vias PCBs involves steps such as drilling, electroless copper deposition, plating, lamination, etching, solder mask application, and final testing. Advanced equipment and precise manufacturing techniques are used to create the blind and buried vias.
What are the applications of Cross Blind/Buried Vias PCBs?
Cross Blind/Buried Vias PCBs are commonly used in high-speed digital circuits, RF/microwave applications, aerospace, automotive electronics, medical devices, telecommunications, and other advanced electronic systems where space constraints and signal integrity are critical.
How much do Cross Blind/Buried Vias PCBs cost?
The cost of Cross Blind/Buried Vias PCBs varies depending on factors such as board size, layer count, via density, material selection, surface finish, volume, and manufacturing capabilities. It’s best to request a quote from a PCB manufacturer based on specific design requirements.