CPU Package Substrates Manufacturer
CPU Package Substrates Manufacturer,CPU Package Substrates are pivotal components in modern central processing units (CPUs), serving as the physical bridge between the CPU die and the rest of the computer system. Comprised of materials like organic laminate, ceramic, or metal core, these substrates facilitate electrical connections, thermal management, and mechanical support within the CPU package. They enable efficient data transmission, maintain signal integrity, and dissipate heat generated by the CPU. Designed with considerations for factors such as electrical performance, thermal conductivity, and compatibility, CPU package substrates play a crucial role in optimizing CPU performance and ensuring system reliability. Through advanced manufacturing processes and stringent quality control measures, these substrates are engineered to meet the demanding requirements of modern computing environments, contributing to the seamless operation and longevity of CPUs in various applications.
What is a CPU Package Substrate?
A CPU package substrate, often referred to simply as a substrate, is a crucial component in modern central processing units (CPUs). It serves as the physical interface between the CPU die (the actual silicon chip) and the rest of the computer system, including the motherboard and other components.
The substrate typically consists of a layered structure, usually made of a durable material like fiberglass or ceramic, with multiple layers of conductive traces and insulating layers. These traces act as pathways for electrical signals to travel between the CPU die and other parts of the system, such as memory modules, peripheral devices, and the power supply.
One of the primary functions of the substrate is to provide electrical connections between the CPU die and the package pins, which are used to interface with the motherboard. The substrate also helps to distribute power and manage heat within the CPU package, ensuring stable and efficient operation.
In addition to its electrical and thermal functions, the substrate also plays a role in providing mechanical support and protection for the delicate CPU die. It helps to absorb mechanical stress and prevent damage to the chip during handling, installation, and operation.
The design and construction of the substrate are critical factors in the overall performance and reliability of the CPU. Advanced manufacturing techniques, such as multilayer interconnects and flip-chip bonding, are used to create substrates that can support the high-speed, high-density, and low-power requirements of modern CPUs.
Overall, the CPU package substrate is a fundamental component that enables the seamless integration of the CPU into the broader computer system, facilitating communication, power delivery, and thermal management to ensure optimal performance and reliability.
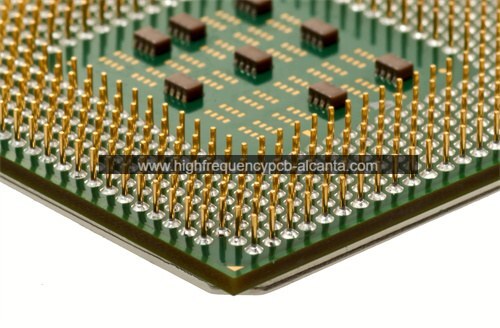
CPU Package Substrates Manufacturer
What are the CPU Package Substrate Design Guidelines?
CPU package substrate design guidelines are a set of principles and specifications that engineers follow when designing the substrate for a central processing unit (CPU). These guidelines ensure that the substrate meets the performance, reliability, and compatibility requirements of the CPU and the overall computer system. While specific guidelines may vary depending on the CPU architecture and manufacturing process, some common design considerations include:
- Electrical Performance:The substrate must provide low impedance paths for electrical signals between the CPU die and other components. Designers consider factors such as signal integrity, impedance matching, and cross-talk to minimize signal degradation and ensure reliable communication.
- Signal Integrity: Maintaining signal integrity is crucial for high-speed data transmission within the CPU and between the CPU and other system components. Design guidelines include minimizing signal reflections, managing transmission line effects, and reducing noise interference.
- Power Delivery: The substrate must efficiently distribute power to the CPU die and other components while minimizing voltage drops and power losses. Designers consider factors such as power plane design, decoupling capacitor placement, and thermal management to ensure stable power delivery.
- Thermal Management:Efficient heat dissipation is essential to prevent overheating and maintain CPU performance and reliability. Substrate design guidelines may include provisions for thermal vias, heat spreaders, and thermal interface materials to facilitate heat transfer away from the CPU die.
- Mechanical Integrity: The substrate must provide mechanical support and protection for the CPU die during handling, installation, and operation. Designers consider factors such as substrate material selection, die attach methods, and mechanical reinforcement to ensure structural integrity and prevent damage to the CPU.
- Compatibility and Interoperability: The substrate design must be compatible with the CPU package form factor and interface specifications, as well as industry standards for motherboard connections and mounting. Designers may also consider interoperability with other system components, such as memory modules, expansion cards, and cooling solutions.
- Manufacturability and Cost: Design guidelines aim to balance performance and reliability requirements with practical considerations such as manufacturability, yield, and cost-effectiveness. Designers optimize substrate layouts, materials, and fabrication processes to achieve the desired performance while minimizing production costs.
By adhering to these CPU package substrate design guidelines, engineers can ensure that the substrate effectively supports the operation of the CPU within the computer system, meeting performance, reliability, and compatibility requirements.
What is the CPU Package Substrate Fabrication Process?
The fabrication process for a CPU package substrate involves several steps to manufacture the layered structure that serves as the interface between the CPU die and the rest of the computer system. While specific techniques and technologies may vary depending on factors such as substrate material, design complexity, and manufacturing scale, a typical substrate fabrication process involves the following key steps:
- Substrate Material Selection: The fabrication process begins with the selection of a suitable substrate material, such as fiberglass, ceramic, or organic laminate. The material choice depends on factors such as electrical properties, thermal conductivity, mechanical strength, and cost.
- Substrate Preparation: The substrate material is prepared for processing by cleaning and surface treatment to remove contaminants and promote adhesion of subsequent layers.
- Layer Formation: Multiple layers of conductive traces, insulating materials, and other functional elements are formed on the substrate material using techniques such as photolithography, etching, deposition, and plating. These layers create the intricate patterns of electrical pathways and features required for the substrate’s functionality.
- Via Formation:Vias are small holes drilled or etched through the substrate layers to establish electrical connections between different layers and provide pathways for heat dissipation. Vias may be formed using techniques such as laser drilling, mechanical drilling, or chemical etching.
- Surface Finishing:The substrate surface is finished to enhance electrical conductivity, solderability, and corrosion resistance. Common surface finishing techniques include electroplating, immersion plating, and solder mask application.
- Die Attachment: The CPU die is attached to the substrate using methods such as flip-chip bonding or wire bonding. This step involves placing the CPU die onto the substrate, aligning it with the electrical pads, and bonding it securely in place.
- Encapsulation: The CPU die and substrate assembly may be encapsulated with a protective material, such as epoxy resin or molding compound, to provide mechanical support, moisture protection, and environmental durability.
- Testing and Quality Control: The fabricated substrate undergoes rigorous testing to ensure functionality, reliability, and compliance with specifications. Testing may include electrical continuity checks, signal integrity analysis, thermal performance evaluation, and visual inspection.
- Packaging and Assembly: The completed substrate is packaged and assembled with other components, such as heat spreaders, thermal interface materials, and connectors, to form the final CPU package ready for integration into the computer system.
Overall, the CPU package substrate fabrication process involves a combination of materials science, microfabrication techniques, and assembly technologies to create a highly integrated and reliable interface for modern CPUs. Each step in the process is carefully controlled to achieve the desired performance, quality, and cost-effectiveness.
How do you manufacture a CPU Package Substrate?
Manufacturing a CPU package substrate involves a complex series of steps, each meticulously designed to ensure the substrate meets the stringent requirements for performance, reliability, and compatibility with the CPU and the overall computer system. Here’s an expanded explanation of the process:
- Material Selection: The process begins with selecting a suitable substrate material, typically fiberglass, ceramic, or organic laminate. Material choice depends on factors like electrical properties, thermal conductivity, mechanical strength, and cost.
- Substrate Preparation: The chosen substrate material undergoes preparation, including cleaning and surface treatment, to remove contaminants and enhance adhesion for subsequent layers.
- Layer Formation: Multiple layers of conductive traces, insulating materials, and other functional elements are formed on the substrate material. Techniques such as photolithography, etching, deposition, and plating create intricate patterns of electrical pathways and features.
- Via Formation: Vias, small holes drilled or etched through the substrate layers, establish electrical connections between different layers and provide pathways for heat dissipation. Vias are formed using techniques like laser drilling, mechanical drilling, or chemical etching.
- Surface Finishing: The substrate surface is finished to enhance electrical conductivity, solderability, and corrosion resistance. Surface finishing techniques include electroplating, immersion plating, and application of solder mask.
- Die Attachment: The CPU die is attached to the substrate using methods like flip-chip bonding or wire bonding. The die is placed onto the substrate, aligned with electrical pads, and bonded securely in place.
- Encapsulation: The CPU die and substrate assembly may be encapsulated with a protective material, such as epoxy resin or molding compound, to provide mechanical support, moisture protection, and environmental durability.
- Testing and Quality Control: Rigorous testing ensures the substrate’s functionality, reliability, and compliance with specifications. Tests include electrical continuity checks, signal integrity analysis, thermal performance evaluation, and visual inspection.
- Packaging and Assembly: The completed substrate is packaged and assembled with other components like heat spreaders, thermal interface materials, and connectors to form the final CPU package, ready for integration into the computer system.
Throughout the manufacturing process, strict quality control measures are implemented to monitor and maintain consistency in substrate fabrication. Any deviations or defects are identified and rectified to ensure that the final product meets the highest standards of performance and reliability.
How much should a CPU Package Substrate cost?
The cost of a CPU package substrate can vary widely depending on factors such as substrate material, design complexity, manufacturing technology, and volume production. Typically, the substrate cost is a fraction of the overall cost of manufacturing a CPU, but it still plays a significant role in the overall cost structure.
On average, the cost of a CPU package substrate for mainstream consumer-grade CPUs can range from a few dollars to tens of dollars per unit. However, this cost can increase for high-performance CPUs used in servers, workstations, or specialized computing applications where more advanced substrate materials, manufacturing techniques, or larger form factors are required.
The substrate cost is influenced by several factors:
- Substrate Material: Different substrate materials have varying costs. For example, ceramic substrates are generally more expensive than organic laminate substrates due to their superior thermal and electrical properties.
- Design Complexity:Complex substrate designs with multiple layers, fine-pitch traces, and advanced features may require more sophisticated manufacturing processes and incur higher production costs.
- Manufacturing Technology: The choice of manufacturing technology and equipment can impact substrate fabrication costs. Advanced techniques such as laser drilling, high-resolution photolithography, and precision deposition may increase production expenses.
- Volume Production: Economies of scale apply in substrate manufacturing. Higher volumes typically lead to lower per-unit costs due to optimized production processes, bulk material purchasing, and reduced overhead expenses.
- Customization and Specialization: Customized substrates designed for specific CPU architectures, form factors, or performance requirements may involve additional development and tooling costs, potentially increasing the overall substrate cost.
Overall, while the substrate cost is a significant consideration in CPU manufacturing, it represents only one aspect of the overall cost structure. CPU manufacturers carefully balance performance, reliability, and cost considerations when selecting substrate materials and fabrication processes to ensure competitiveness in the market.
What is CPU Package Substrate Base Material?
The CPU package substrate base material refers to the foundational material used to construct the substrate on which the CPU die is mounted. Several materials are commonly used as substrate base materials, each with its own properties and advantages:
- Organic Laminate: Organic laminate substrates are made from layers of fiberglass reinforced with epoxy resin. They are cost-effective, lightweight, and offer good electrical insulation properties. Organic laminate substrates are widely used in mainstream consumer-grade CPUs due to their affordability and ease of fabrication.
- Ceramic:Ceramic substrates are composed of alumina (Al2O3) or other ceramic materials. They offer excellent thermal conductivity, mechanical strength, and dimensional stability, making them ideal for high-performance CPUs that require efficient heat dissipation and reliability. Ceramic substrates are often used in server-grade CPUs and other specialized applications.
- Metal Core: Metal core substrates consist of a metal base layer, typically aluminum or copper, sandwiched between layers of insulating material. They provide superior thermal conductivity compared to organic laminate substrates, making them suitable for CPUs that require enhanced heat dissipation. Metal core substrates are commonly used in high-power CPUs and LED applications.
- Flexible Substrates: Flexible substrates are made from thin, flexible materials such as polyimide or polyester. They are used in applications where space constraints or bending requirements necessitate a flexible substrate. Flexible substrates are less common in CPU packaging but may be used in specialized applications or in conjunction with rigid substrates in multi-chip module designs.
The choice of substrate base material depends on factors such as performance requirements, thermal management needs, cost considerations, and manufacturing processes. CPU manufacturers carefully select the substrate material that best balances these factors to ensure optimal performance, reliability, and cost-effectiveness for the target application.
Which company manufactures CPU Package Substrates?
CPU package substrates are manufactured by several companies, including Nippon Steel & Sumikin, Axcelis, Samsung SDI, Bosch, Macronix, TSMC, UMC, BOE Technology Group, and ChangXin Technology in Japan, the United States, South Korea, Germany, Taiwan, and China, respectively.
As a company dedicated to the semiconductor industry, we also produce high-quality CPU package substrates. We have advanced manufacturing equipment and technology, collaborating with customers to customize and manufacture various types of CPU package substrates according to their requirements.
Our manufacturing process strictly adheres to international standards and quality management systems to ensure that our products meet customer needs and expectations. Our professional team has extensive experience and technical knowledge, providing comprehensive technical support and solutions to ensure the smooth progress of our customers’ projects.
Moreover, we focus on continuous innovation and technological development, continuously improving and optimizing our manufacturing processes and product performance to meet the evolving market demands and customer requirements.
In conclusion, we are committed to providing customers with high-quality, reliable, and cost-effective CPU package substrates. Through continuous technological innovation and high-quality service, we contribute to the success of our customers’ businesses.
What are the 7 qualities of good customer service?
Good customer service is essential for maintaining positive relationships with customers and fostering loyalty. Seven qualities of good customer service include:
- Responsiveness: Being prompt and attentive to customer inquiries, requests, and concerns demonstrates respect for their time and needs. Quick responses, whether in person, over the phone, or via digital channels, show customers that their issues are being addressed promptly.
- Empathy:Understanding and empathizing with customers’ perspectives and emotions is crucial for building rapport and trust. Empathetic responses demonstrate genuine concern for customers’ experiences and can help de-escalate tense situations.
- Clarity: Providing clear and concise communication ensures that customers understand information, instructions, and solutions effectively. Avoiding technical jargon and using plain language helps prevent confusion and enhances the overall customer experience.
- Professionalism: Maintaining professionalism in all interactions conveys competence, credibility, and reliability. Professionalism includes being courteous, respectful, and maintaining a positive attitude, even in challenging situations.
- Problem-solving skills: Effective problem-solving skills are essential for resolving customer issues and addressing their needs effectively. Customer service representatives should be proactive in finding solutions and be empowered to make decisions to resolve problems efficiently.
- Consistency:Consistency in service delivery across all touchpoints and interactions ensures a cohesive and reliable customer experience. Customers should receive the same level of service quality regardless of the channel or representative they interact with.
- Follow-up and feedback: Following up with customers after resolving their issues and seeking feedback demonstrates a commitment to continuous improvement and customer satisfaction. Actively soliciting feedback and acting on it helps identify areas for improvement and strengthens customer relationships.
By embodying these qualities, organizations can provide exceptional customer service that exceeds expectations and fosters long-term customer loyalty and advocacy.
FAQs
What is a CPU package substrate?
A CPU package substrate is a critical component in modern central processing units (CPUs). It serves as the physical interface between the CPU die and the rest of the computer system, facilitating electrical connections, thermal management, and mechanical support.
What materials are used to make CPU package substrates?
Common materials used for CPU package substrates include organic laminate, ceramic, metal core, and flexible substrates. Each material offers different properties such as electrical conductivity, thermal management, and mechanical strength.
How does a CPU package substrate contribute to CPU performance?
The substrate facilitates efficient electrical connections between the CPU die and other system components, ensuring fast data transmission and signal integrity. Additionally, the substrate aids in thermal management by dissipating heat generated by the CPU.
What factors should be considered when designing a CPU package substrate?
Important factors in substrate design include electrical performance, signal integrity, power delivery, thermal management, mechanical integrity, compatibility, and manufacturability. Designers strive to optimize these factors to meet the requirements of the CPU and the overall system.
What are the differences between CPU package substrates for consumer-grade and high-performance CPUs?
Substrates for high-performance CPUs, such as those used in servers or workstations, may require materials with superior thermal conductivity and mechanical strength to handle higher power densities and temperatures. They may also feature more advanced designs to support faster data transmission and signal integrity.
How are CPU package substrates manufactured?
The manufacturing process for CPU package substrates involves steps such as substrate material selection, layer formation, via formation, surface finishing, die attachment, encapsulation, testing, and packaging. Advanced fabrication techniques and quality control measures are employed to ensure high-quality substrates.
What role does a CPU package substrate play in system reliability and longevity?
A well-designed and properly manufactured substrate contributes to the overall reliability and longevity of the CPU and the computer system. It helps prevent electrical failures, overheating, and mechanical damage, ensuring stable and durable performance over time.