Chip Substrates Manufacturer
Chip Substrates Manufacturer,Chip substrates are the foundational building blocks of integrated circuits (ICs), serving as the essential platform upon which electronic components are fabricated and interconnected. These substrates, typically made of materials like silicon, ceramics, or specialized compounds, provide mechanical support and electrical connectivity for the intricate circuitry of modern electronic devices.
Manufactured through precise processes like thin film deposition, photolithography, and etching, chip substrates enable the creation of complex electronic systems with high levels of functionality and performance. They play a crucial role in various industries, including consumer electronics, telecommunications, automotive, and healthcare, powering a wide range of devices from smartphones and computers to medical implants and automotive sensors.
The design and quality of chip substrates directly impact the reliability, efficiency, and performance of integrated circuits. As technology advances, chip substrates continue to evolve to meet the demands of increasingly sophisticated electronic applications, driving innovation and shaping the future of electronics.
What is a Chip Substrate?
A chip substrate is a foundational component of integrated circuits (ICs) or microchips. It serves as the physical base or platform upon which various electronic components, such as transistors, diodes, and resistors, are fabricated and interconnected to form a functional electronic device.
The substrate typically consists of a thin, flat piece of material, often made of silicon, ceramic, or a specialized compound such as gallium arsenide (GaAs). This material provides mechanical support for the integrated circuit and also serves as a medium for the electrical connections between different components.
In addition to providing mechanical and electrical support, the chip substrate may also play a role in thermal management, helping to dissipate heat generated by the integrated circuit during operation.
The design and material of the chip substrate can significantly impact the performance, power consumption, and reliability of the integrated circuit, making it an important consideration in the development of electronic devices.
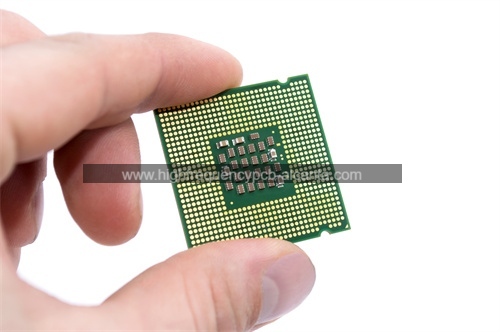
Chip Substrates Manufacturer
What are the Chip Substrate Design Guidelines?
Chip substrate design guidelines encompass a set of principles and practices aimed at optimizing the performance, reliability, and manufacturability of integrated circuits by focusing on the design and layout of the substrate. Here are some key aspects typically considered in chip substrate design:
- Material Selection: Choosing the appropriate substrate material is crucial, depending on factors such as the intended application, operating conditions, and manufacturing process. Common substrate materials include silicon, ceramics, and specialized compounds like gallium arsenide (GaAs).
- Dimensional Stability: The substrate material should have good dimensional stability to minimize the effects of thermal expansion and contraction, ensuring the integrity of the electrical connections and overall structural integrity of the chip.
- Electrical Properties: The substrate material should exhibit desirable electrical properties, such as low electrical resistance, high dielectric strength, and minimal signal loss, to ensure efficient electrical performance of the integrated circuit.
- Thermal Management: Effective heat dissipation is critical for maintaining the reliability and longevity of integrated circuits. Chip substrate design should incorporate features like thermal vias, heat sinks, and thermal pads to facilitate the efficient removal of heat generated during operation.
- Signal Integrity: Proper signal routing and impedance matching are essential for maintaining signal integrity and minimizing signal distortion and noise. Chip substrate design should optimize signal paths, minimize crosstalk, and ensure consistent impedance throughout the circuit.
- Power Distribution: Efficient power distribution is necessary to ensure stable voltage levels across the integrated circuit. Chip substrate design should include well-designed power planes, decoupling capacitors, and low-resistance power distribution networks to minimize voltage drops and power supply noise.
- Manufacturability and Yield: The chip substrate design should be compatible with the chosen manufacturing process and assembly techniques. Design features such as standardized dimensions, alignment marks, and test structures can facilitate the manufacturing process and improve yield rates.
- Reliability and Durability: The chip substrate should be designed to withstand mechanical stress, thermal cycling, and environmental factors encountered during operation and handling. Design considerations such as proper pad and trace placement, robust solder joints, and adequate clearance and spacing help enhance reliability and durability.
- Cost Optimization: Balancing performance requirements with cost considerations is essential in chip substrate design. Designers should strive to minimize material usage, simplify manufacturing processes, and optimize layout efficiency without compromising performance or reliability.
Overall, adhering to these chip substrate design guidelines helps ensure that integrated circuits meet performance specifications, reliability requirements, and cost targets while facilitating efficient manufacturing and assembly processes.
What is the Chip Substrate Fabrication Process?
The chip substrate fabrication process involves several steps to create the foundational platform upon which electronic components are built to form integrated circuits (ICs) or microchips. Here’s a generalized overview of the chip substrate fabrication process:
- Substrate Material Preparation: The process begins with the preparation of the substrate material. Common substrate materials include silicon, ceramics, and specialized compounds like gallium arsenide (GaAs). The substrate material is typically supplied in the form of wafers or sheets.
- Cleaning and Surface Preparation: The substrate material undergoes cleaning and surface preparation steps to remove contaminants and create a clean, uniform surface suitable for subsequent processing. This may involve techniques such as chemical cleaning, etching, and surface passivation.
- Thin Film Deposition: Thin films of various materials are deposited onto the substrate surface using techniques such as chemical vapor deposition (CVD), physical vapor deposition (PVD), or sputtering. These thin films may include metal layers for wiring, dielectric layers for insulation, and semiconductor layers for active components.
- Photolithography: Photolithography is a key process used to define the pattern of features on the substrate surface. A photosensitive material called photoresist is applied to the substrate, exposed to ultraviolet (UV) light through a mask or reticle containing the desired pattern, and then developed to remove the exposed or unexposed regions, depending on the type of resist used.
- Etching: Etching is used to selectively remove material from the substrate surface according to the pattern defined by the photoresist. Wet etching and dry etching are common etching techniques employed to transfer the pattern into the substrate material. Wet etching involves chemical dissolution of the material, while dry etching uses plasma to remove material through physical or chemical reactions.
- Doping and Ion Implantation: Dopants or impurities may be introduced into the substrate material to modify its electrical properties and create regions with specific conductivity characteristics. Ion implantation is a common technique used to precisely control the doping profile within the substrate.
- Metallization and Interconnection: Metal layers are deposited onto the substrate surface to create electrical interconnections between different components and features. Techniques such as sputtering or electroplating are used to deposit metal films, which are then patterned and etched to define the wiring and interconnect structures.
- Insulation and Passivation: Dielectric materials are deposited onto the substrate surface to insulate and protect the underlying components and interconnections. These insulating layers also serve to passivate the surface, reducing leakage currents and enhancing device reliability.
- Packaging and Testing: Once the chip substrate fabrication is complete, individual chips are typically separated from the substrate and packaged into protective enclosures. The packaged chips undergo testing to ensure they meet performance specifications and reliability requirements before being shipped for use in electronic devices.
Overall, the chip substrate fabrication process involves a series of precise and controlled steps to create the foundational platform for building integrated circuits, incorporating various materials, deposition techniques, patterning methods, and surface treatments to achieve the desired device functionality and performance.
How do you manufacture a Chip Substrate?
Manufacturing a chip substrate involves a series of complex processes that transform raw materials into a functional platform for building integrated circuits. Here’s an overview of the typical steps involved in manufacturing a chip substrate:
- Substrate Material Selection: The process begins with selecting the appropriate substrate material based on factors such as the desired electrical properties, thermal characteristics, and intended application. Common substrate materials include silicon, ceramics, and specialized compounds like gallium arsenide (GaAs).
- Wafer Preparation: If silicon is chosen as the substrate material, the manufacturing process starts with the preparation of silicon wafers. This involves slicing a single crystal ingot of silicon into thin, flat discs known as wafers. The wafers are then polished to achieve a smooth and uniform surface.
- Cleaning and Surface Treatment: The silicon wafers undergo rigorous cleaning and surface treatment steps to remove contaminants and create a pristine surface suitable for subsequent processing. This may involve techniques such as chemical cleaning, etching, and surface passivation.
- Thin Film Deposition: Thin films of various materials, such as metals for wiring and dielectrics for insulation, are deposited onto the substrate surface using techniques like chemical vapor deposition (CVD), physical vapor deposition (PVD), or sputtering. These thin films form the foundation for building the integrated circuits.
- Photolithography: Photolithography is used to define the pattern of features on the substrate surface. A layer of photosensitive material called photoresist is applied to the substrate, exposed to ultraviolet (UV) light through a mask or reticle containing the desired pattern, and then developed to transfer the pattern onto the substrate surface.
- Etching: Etching is employed to selectively remove material from the substrate surface according to the pattern defined by the photoresist. Wet etching and dry etching are common etching techniques used to transfer the pattern into the substrate material, creating the desired circuitry and features.
- Doping and Ion Implantation: Dopants or impurities may be introduced into the substrate material to modify its electrical properties and create regions with specific conductivity characteristics. Ion implantation is a precise technique used to control the doping profile within the substrate.
- Metallization and Interconnection: Metal layers are deposited onto the substrate surface to create electrical interconnections between different components and features. Techniques such as sputtering or electroplating are used to deposit metal films, which are then patterned and etched to define the wiring and interconnect structures.
- Insulation and Passivation: Dielectric materials are deposited onto the substrate surface to insulate and protect the underlying components and interconnections. These insulating layers also serve to passivate the surface, reducing leakage currents and enhancing device reliability.
- Packaging and Testing:Once the chip substrate manufacturing is complete, individual chips are separated from the substrate and packaged into protective enclosures. The packaged chips undergo rigorous testing to ensure they meet performance specifications and reliability requirements before being shipped for use in electronic devices.
Overall, the manufacturing process for chip substrates involves a combination of materials deposition, patterning, doping, and surface treatment techniques to create the foundational platform for building integrated circuits with the desired functionality and performance.
How much should a Chip Substrate cost?
The cost of a chip substrate can vary significantly depending on various factors such as the substrate material, size, complexity, manufacturing technology, and volume of production. However, to provide a rough estimate, let’s consider some typical costs associated with chip substrate manufacturing:
- Substrate Material: The cost of the substrate material itself can vary widely depending on factors such as the material type (e.g., silicon, ceramic, GaAs), purity, and size. Silicon wafers, for example, are a significant cost factor in semiconductor manufacturing and can range from a few dollars to hundreds of dollars per wafer, depending on the size and quality.
- Manufacturing Process: The manufacturing process for chip substrates involves multiple steps, including thin film deposition, photolithography, etching, doping, metallization, and packaging. Each of these steps incurs costs related to equipment, materials, labor, and overhead expenses.
- Volume of Production: Economies of scale play a significant role in chip substrate manufacturing costs. Higher volumes of production generally result in lower per-unit costs due to spreading fixed costs over a larger number of units. Conversely, low-volume or custom manufacturing may incur higher costs per unit.
- Complexity and Features:The complexity of the chip substrate, including the number of layers, feature density, and precision requirements, can impact manufacturing costs. More complex designs may require advanced fabrication techniques and specialized equipment, leading to higher costs.
- Technology Node: The manufacturing technology node refers to the size of the smallest features that can be reliably fabricated on the substrate. Advanced technology nodes with smaller feature sizes typically require more sophisticated manufacturing processes and equipment, which can increase production costs.
- Quality and Yield: Achieving high yields (the percentage of functional chips produced per batch) is essential for controlling manufacturing costs. Lower yields can result in higher per-unit costs due to wasted materials and production time.
Given these factors, the cost of a chip substrate can range from a few dollars for simpler designs produced in high volumes using mature manufacturing processes to hundreds or even thousands of dollars for more complex, custom substrates fabricated using advanced technologies in low volumes. For precise cost estimates, it’s advisable to consult with semiconductor manufacturers or suppliers who can provide quotes based on specific requirements and volume projections.
What is Chip Substrate Base Material?
The chip substrate base material is the foundational material upon which integrated circuits (ICs) or microchips are built. The choice of substrate base material depends on various factors such as electrical properties, thermal conductivity, cost, and compatibility with the manufacturing process. Some common materials used for chip substrate base include:
- Silicon: Silicon is the most widely used substrate base material in semiconductor manufacturing due to its excellent electrical properties, abundance, and well-established fabrication techniques. Silicon substrates are used for both discrete components and integrated circuits.
- Ceramics: Ceramics such as alumina (Al2O3) and aluminum nitride (AlN) are used in applications requiring high thermal conductivity and mechanical strength. Ceramics are often chosen for power electronics, radio frequency (RF) components, and high-temperature applications.
- Gallium Arsenide (GaAs):GaAs substrates are used in specialized applications such as high-frequency RF devices and optoelectronic components. GaAs offers superior electron mobility compared to silicon, making it suitable for high-speed and high-frequency applications.
- Glass: Glass substrates are used in certain applications where transparency or optical properties are required, such as display technologies (e.g., liquid crystal displays, OLEDs) and sensors.
- Specialized Compounds: Other specialized compounds such as silicon carbide (SiC) and gallium nitride (GaN) are used in specific applications requiring superior thermal conductivity, high breakdown voltage, or resistance to harsh environmental conditions.
The choice of substrate base material depends on the requirements of the specific application, including electrical performance, thermal management, reliability, and cost considerations. Each material has its own advantages and limitations, and selecting the most appropriate substrate base material is crucial for achieving the desired performance and functionality of the integrated circuits.
Which company makes Chip Substrates?
Many companies specialize in the production of chip substrates, including leading firms like Intel, TSMC, Samsung Electronics, GlobalFoundries, and Micron. These companies possess advanced manufacturing technologies and facilities capable of producing various types and specifications of chip substrates to meet the needs of different industries and applications.
In our company, we also have the capability to manufacture chip substrates. We have advanced manufacturing equipment and a skilled technical team capable of producing high-quality, high-performance chip substrates. Our production process is carefully designed and optimized to ensure the production of products that meet customer requirements. We can provide chip substrates in various materials, including silicon, ceramics, gallium arsenide, and others, to meet the needs of different application scenarios.
We place a strong emphasis on quality control and continuous improvement. Through rigorous quality management systems and comprehensive testing processes, we ensure that every chip substrate meets the highest quality standards. We are also committed to working closely with customers, understanding their needs, and providing customized solutions. We can customize the size, material, process, and other aspects of chip substrates according to customer requirements to meet their specific application needs.
In summary, our company has the technical expertise and capabilities to produce chip substrates and is committed to providing high-quality, customized products and services to meet customer needs and earn their trust and support.
What are the 7 qualities of good customer service?
Good customer service is characterized by several key qualities that contribute to positive customer experiences and satisfaction. Here are seven essential qualities:
- Responsiveness: Good customer service involves being prompt and attentive to customer needs and inquiries. Responding quickly to customer queries, concerns, and requests demonstrates a commitment to excellent service and helps to build trust and loyalty.
- Empathy: Empathy involves understanding and acknowledging the customer’s perspective, emotions, and concerns. Empathetic customer service representatives listen actively, show genuine concern for the customer’s issues, and strive to address their needs with compassion and understanding.
- Clarity: Clear communication is essential for effective customer service. Providing clear and concise information, instructions, and explanations helps customers understand their options, make informed decisions, and resolve issues more effectively. Avoiding jargon and using simple language can enhance clarity in communication.
- Professionalism: Professionalism encompasses a range of behaviors and attributes, including courtesy, respect, integrity, and reliability. Customer service representatives should conduct themselves professionally at all times, treating customers with respect, maintaining confidentiality, and delivering on promises.
- Knowledgeability: Good customer service requires a thorough understanding of the products, services, and policies offered by the company. Knowledgeable customer service representatives are equipped to answer questions, provide accurate information, and offer relevant solutions to customer issues. Continuous training and education are essential to staying updated on product developments and industry trends.
- Problem-Solving Skills: Effective problem-solving skills are crucial for resolving customer issues and concerns. Customer service representatives should be proactive in identifying and addressing customer problems, finding creative solutions, and following through to ensure customer satisfaction. Adopting a positive and solution-oriented mindset can help overcome challenges more effectively.
- Personalization: Personalized customer service involves tailoring interactions and solutions to meet the unique needs and preferences of individual customers. By taking the time to understand each customer’s situation, history, and preferences, customer service representatives can deliver more relevant and meaningful experiences, fostering stronger connections and loyalty.
By embodying these qualities, organizations can cultivate a customer-centric culture and deliver exceptional service that exceeds customer expectations and drives long-term success.
FAQs (Frequently Asked Questions)
What is a chip substrate?
A chip substrate is a foundational component of integrated circuits (ICs) or microchips. It serves as the physical base or platform upon which various electronic components are fabricated and interconnected to form a functional electronic device.
What materials are used for chip substrates?
Common materials used for chip substrates include silicon, ceramics, gallium arsenide (GaAs), glass, and specialized compounds like silicon carbide (SiC) and gallium nitride (GaN). The choice of material depends on factors such as electrical properties, thermal characteristics, and intended application.
What is the role of chip substrates in semiconductor manufacturing?
Chip substrates provide mechanical support for integrated circuits and serve as a medium for electrical connections between different components. They also play a role in thermal management, helping to dissipate heat generated by the integrated circuit during operation.
What are the different types of chip substrates?
Chip substrates can vary in terms of material, size, and design. Common types include silicon wafers for semiconductor devices, ceramic substrates for high-power applications, and specialized substrates for specific technologies like RF devices and optoelectronics.
How are chip substrates manufactured?
Chip substrate manufacturing involves processes such as material preparation, thin film deposition, photolithography, etching, doping, metallization, and packaging. These processes are carried out in specialized facilities using advanced equipment and techniques.
What factors should be considered when selecting a chip substrate?
When selecting a chip substrate, factors such as electrical properties, thermal conductivity, mechanical strength, compatibility with manufacturing processes, and cost should be considered. The substrate material and design should meet the requirements of the specific application.