Ceramic Substrate LED Manufacturer
Ceramic Substrate LED Manufacturer,Ceramic Substrate LEDs employ advanced ceramic materials like alumina or aluminum nitride as a foundation for LED chips. Renowned for superior thermal conductivity, they efficiently dissipate heat, enhancing performance and lifespan. Versatile and durable, Ceramic Substrate LEDs find applications in diverse fields, from general lighting to automotive and industrial sectors. Their ability to withstand harsh environments and deliver consistent illumination makes them indispensable in demanding settings. With customizable designs and exceptional reliability, Ceramic Substrate LEDs represent a cutting-edge solution for efficient, long-lasting lighting solutions.
What is a Ceramic Substrate LED?
A Ceramic Substrate LED (Light Emitting Diode) is a type of LED that utilizes a ceramic substrate as the base material instead of traditional materials like metal or silicon. The substrate serves as a foundation for the LED chip and helps in dissipating heat efficiently, enhancing the LED’s performance and longevity.
Ceramic substrates offer several advantages over conventional materials. They have excellent thermal conductivity, which means they can quickly transfer heat away from the LED chip, preventing overheating and ensuring stable operation even at high power levels. This feature is particularly crucial in high-intensity applications where heat dissipation is a concern.
Additionally, ceramic substrates are highly durable and resistant to environmental factors such as moisture, chemicals, and temperature fluctuations. This robustness makes ceramic substrate LEDs suitable for a wide range of demanding environments, including outdoor lighting, automotive lighting, and industrial applications.
Furthermore, ceramic substrate LEDs can be manufactured with different shapes and sizes, allowing for flexibility in design and integration into various lighting fixtures and systems. They also tend to have better light output efficiency and color rendering compared to LEDs mounted on other types of substrates.
In summary, Ceramic Substrate LEDs offer superior thermal performance, durability, and versatility, making them a preferred choice for demanding lighting applications where reliability and efficiency are paramount.
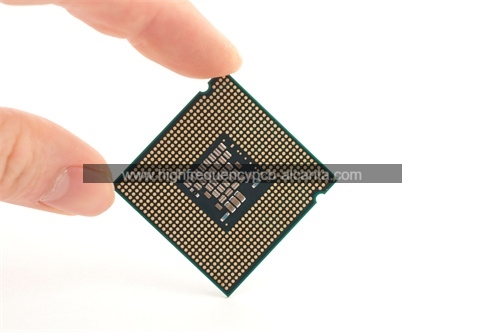
Ceramic Substrate LED Manufacturer
What are the Ceramic Substrate LED Design Guidelines?
Designing with Ceramic Substrate LEDs involves considering several key guidelines to ensure optimal performance and reliability:
- Thermal Management: Proper thermal management is crucial for Ceramic Substrate LEDs. Ensure that the heat generated by the LED is effectively dissipated to prevent overheating, which can degrade performance and reduce lifespan. This may involve incorporating heat sinks, thermal pads, or other thermal management solutions into the design.
- Electrical Design: Pay attention to electrical characteristics such as forward voltage, forward current, and reverse voltage. Ensure that the LED is operated within its specified electrical parameters to avoid damage and ensure longevity.
- Mechanical Considerations: Ceramic Substrate LEDs may have specific mechanical requirements regarding mounting, assembly, and handling. Follow manufacturer guidelines for proper handling and mounting procedures to avoid mechanical stress on the LED, which can lead to premature failure.
- Optical Design:Consider the optical characteristics of the LED, including luminous intensity, viewing angle, and color temperature. Design optical systems, such as lenses or reflectors, to achieve the desired light distribution and intensity for the application.
- Environmental Factors:Consider environmental factors such as moisture, temperature, and chemical exposure. Ceramic substrates offer excellent resistance to environmental stressors, but it’s still essential to design the system to minimize exposure to potentially harmful conditions.
- Reliability Testing:Perform thorough reliability testing on Ceramic Substrate LEDs to ensure they meet performance and longevity requirements. This may include temperature cycling, humidity testing, and electrical stress testing to simulate real-world operating conditions and identify potential failure modes.
- Compliance and Safety: Ensure that the LED design complies with relevant safety standards and regulations. This includes considerations such as electrical safety, electromagnetic compatibility (EMC), and environmental regulations.
- Application-Specific Considerations: Tailor the LED design to meet the specific requirements of the application. Consider factors such as operating environment, power supply limitations, space constraints, and aesthetic preferences when designing with Ceramic Substrate LEDs.
By following these guidelines, designers can create robust and reliable lighting systems using Ceramic Substrate LEDs that meet the performance and longevity requirements of their intended applications.
What is the Ceramic Substrate LED Fabrication Process?
The fabrication process for Ceramic Substrate LEDs involves several steps:
- Substrate Preparation: The process begins with preparing the ceramic substrate material, which is typically alumina (Al2O3) or aluminum nitride (AlN). The substrate is cleaned and treated to ensure surface cleanliness and uniformity.
- Deposition of Semiconductor Layers:Semiconductor layers, including the n-type and p-type layers, are deposited onto the ceramic substrate using techniques such as chemical vapor deposition (CVD) or molecular beam epitaxy (MBE). These layers form the active region of the LED where light emission occurs.
- Patterning: Photolithography or other patterning techniques are used to define the shape and structure of the LED chip. A photoresist is applied to the semiconductor layers, exposed to UV light through a mask, and developed to selectively remove portions of the semiconductor layers, leaving behind the desired LED structure.
- Doping and Annealing: Dopants are introduced into the semiconductor layers through processes such as ion implantation or diffusion to create regions with specific electrical properties. Annealing is then performed to activate the dopants and repair any damage to the crystal structure caused by the doping process.
- Metallization: Metal contacts are deposited onto the semiconductor layers to provide electrical connections to the LED. These contacts serve as the electrodes through which current is injected into the LED chip.
- Die Attach: The LED chip is attached to the ceramic substrate using a die attach adhesive. This step ensures proper electrical and thermal contact between the LED chip and the substrate, facilitating efficient heat dissipation during operation.
- Wire Bonding: Thin metal wires are bonded between the LED chip’s contacts and the substrate’s external connection points to complete the electrical circuit. Wire bonding can be done using techniques such as thermosonic bonding or ultrasonic bonding.
- Encapsulation: The LED chip and wire bonds are encapsulated with a protective material, such as epoxy resin, to provide mechanical support and environmental protection. The encapsulant also helps to improve light extraction efficiency and thermal performance.
- Testing and Sorting: The fabricated Ceramic Substrate LEDs undergo rigorous testing to ensure they meet specified performance criteria, including electrical characteristics, optical properties, and reliability. LEDs that pass the testing are sorted based on their performance parameters and packaged for distribution.
- Packaging: The sorted Ceramic Substrate LEDs are packaged into individual components or arrays, depending on the application requirements. Packaging options may include surface-mount packages, through-hole packages, or custom-designed packages tailored to specific applications.
Overall, the fabrication process for Ceramic Substrate LEDs involves a series of precise steps to create high-performance LED chips on ceramic substrates, suitable for a wide range of lighting and illumination applications.
How do you manufacture Ceramic Substrate LEDs?
Manufacturing Ceramic Substrate LEDs involves a series of intricate steps and specialized equipment. Here’s a simplified overview of the manufacturing process:
- Substrate Preparation: Alumina (Al2O3) or aluminum nitride (AlN) ceramic substrates are prepared by cleaning and polishing to ensure surface cleanliness and uniformity. The substrates are typically in the form of thin wafers.
- Deposition of Semiconductor Layers: Semiconductor layers are deposited onto the ceramic substrates using techniques such as chemical vapor deposition (CVD) or molecular beam epitaxy (MBE). These layers include the n-type and p-type semiconductor materials that form the active region of the LED.
- Patterning: Photolithography is used to define the shape and structure of the LED chip. A photoresist is applied to the semiconductor layers, exposed to UV light through a mask, and developed to selectively remove portions of the semiconductor layers, leaving behind the desired LED structure.
- Doping and Annealing: Dopants are introduced into the semiconductor layers to create regions with specific electrical properties. This is typically done through processes such as ion implantation or diffusion. Annealing is then performed to activate the dopants and repair any damage to the crystal structure caused by the doping process.
- Metallization: Metal contacts are deposited onto the semiconductor layers to provide electrical connections to the LED. These contacts serve as the electrodes through which current is injected into the LED chip.
- Die Attach: The LED chip is attached to the ceramic substrate using a die attach adhesive. This step ensures proper electrical and thermal contact between the LED chip and the substrate, facilitating efficient heat dissipation during operation.
- Wire Bonding: Thin metal wires are bonded between the LED chip’s contacts and the substrate’s external connection points to complete the electrical circuit. Wire bonding can be done using techniques such as thermosonic bonding or ultrasonic bonding.
- Encapsulation: The LED chip and wire bonds are encapsulated with a protective material, such as epoxy resin, to provide mechanical support and environmental protection. The encapsulant also helps to improve light extraction efficiency and thermal performance.
- Testing and Sorting:The fabricated Ceramic Substrate LEDs undergo rigorous testing to ensure they meet specified performance criteria, including electrical characteristics, optical properties, and reliability. LEDs that pass the testing are sorted based on their performance parameters.
- Packaging: The sorted Ceramic Substrate LEDs are packaged into individual components or arrays, depending on the application requirements. Packaging options may include surface-mount packages, through-hole packages, or custom-designed packages tailored to specific applications.
Throughout the manufacturing process, quality control measures are implemented to ensure the consistency and reliability of the Ceramic Substrate LEDs produced. This involves monitoring various parameters such as layer thickness, dopant concentration, wire bond integrity, and optical performance.
How much should a Ceramic Substrate LED cost?
The cost of Ceramic Substrate LEDs can vary depending on several factors, including:
- Size and Complexity: Larger and more complex Ceramic Substrate LEDs typically cost more to manufacture due to increased material and processing requirements.
- Material Quality: Higher-quality ceramic substrates and semiconductor materials may command a higher price, as they offer better performance and reliability.
- Manufacturing Process: The manufacturing process used to produce Ceramic Substrate LEDs can impact their cost. Advanced fabrication techniques and equipment may result in higher production costs.
- Volume: The economies of scale play a significant role in LED manufacturing costs. Higher production volumes generally lead to lower per-unit costs due to efficiencies in materials purchasing, equipment utilization, and labor.
- Customization: Custom-designed Ceramic Substrate LEDs tailored to specific applications may incur additional development and tooling costs, which can affect the overall cost.
- Supplier and Market Dynamics: Prices can vary between different suppliers and regions due to factors such as competition, supply chain efficiency, and market demand.
- Additional Features: LEDs with additional features such as integrated optics, thermal management solutions, or specialized coatings may have higher costs compared to basic LED chips.
As a rough estimate, the cost of Ceramic Substrate LEDs can range from a few cents to several dollars per unit, depending on the factors mentioned above. High-performance, specialized Ceramic Substrate LEDs used in demanding applications may command higher prices, while standard, mass-produced LEDs intended for general lighting purposes may be more affordable. It’s essential for buyers to consider their specific requirements and budget constraints when evaluating Ceramic Substrate LED options.
What is Ceramic Substrate LED base material?
The base material for Ceramic Substrate LEDs is typically a ceramic material, which provides a sturdy and thermally conductive foundation for the LED chip. The two most common types of ceramic substrates used in LED manufacturing are:
- Alumina (Al2O3):Alumina ceramic substrates are widely used in LED fabrication due to their excellent thermal conductivity, mechanical strength, and chemical stability. They offer good electrical insulation properties and can withstand high temperatures, making them suitable for high-power LED applications.
- Aluminum Nitride (AlN): Aluminum nitride ceramic substrates offer even higher thermal conductivity than alumina, making them particularly well-suited for applications where efficient heat dissipation is critical. AlN substrates also exhibit excellent thermal expansion properties, which can help reduce thermal stress on the LED chip during operation.
Both alumina and aluminum nitride ceramic substrates provide a stable and reliable platform for mounting and electrically connecting the LED chip. They help to dissipate heat generated by the LED during operation, thereby enhancing performance and longevity. The choice of substrate material depends on factors such as the specific application requirements, thermal management needs, and cost considerations.
Which company manufactures Ceramic Substrate LEDs?
There are many companies manufacturing Ceramic Substrate LEDs. Some major manufacturers include well-known LED companies such as Philips, Osram, Nichia, Samsung, and Cree. In addition, there are also specialized companies dedicated to the production of Ceramic Substrate LEDs, such as BOE and San’an Optoelectronics.
As for our company, we also have the capability to produce Ceramic Substrate LEDs. As a professional LED manufacturer, we have advanced production equipment and a skilled technical team capable of controlling the entire process from design to production. Our manufacturing process covers aspects such as substrate selection and treatment, deposition of semiconductor layers, chip processing, and encapsulation, ensuring product quality and stability.
During the production of Ceramic Substrate LEDs, we strictly adhere to industry standards and quality management systems, conducting comprehensive monitoring and testing to ensure that products meet customer requirements and expectations. Our Ceramic Substrate LED products feature excellent thermal conductivity, stable optoelectronic characteristics, and reliable quality, suitable for various indoor and outdoor lighting, display, and other applications.
Our Ceramic Substrate LED products have not only gained a good reputation and market share in the domestic market but are also exported to international markets, receiving recognition and favor from customers. We are committed to providing customers with high-quality, innovative, and customized LED solutions to meet the needs of different industries and application fields.
Whether it’s standard Ceramic Substrate LED models or custom special models, we can provide flexible production capabilities and services to offer satisfactory solutions to customers. Please feel free to contact us for more information about our Ceramic Substrate LED products and cooperation opportunities.
What are the 7 qualities of good customer service?
Good customer service is characterized by several key qualities that contribute to positive interactions and customer satisfaction:
- Responsiveness: Good customer service involves promptly addressing customer inquiries, concerns, and requests. Responding in a timely manner demonstrates attentiveness and a commitment to meeting customer needs promptly.
- Empathy: Empathy is essential in understanding and acknowledging the customer’s perspective and emotions. Customer service representatives who demonstrate empathy can build rapport, validate concerns, and create a more positive experience for the customer.
- Clear Communication: Effective communication is crucial for conveying information clearly and accurately. Good customer service representatives communicate in a professional, courteous manner, using language that is easy to understand and providing relevant information to assist customers.
- Problem-solving Skills: Good customer service involves effectively resolving customer issues and addressing challenges. Customer service representatives who possess strong problem-solving skills can identify root causes, explore solutions, and take appropriate actions to resolve problems to the customer’s satisfaction.
- Professionalism: Professionalism encompasses attributes such as courtesy, respect, and integrity. Maintaining professionalism in interactions with customers fosters trust, credibility, and a positive perception of the company or organization.
- Flexibility: Good customer service requires adaptability and flexibility to accommodate diverse customer needs and preferences. Being flexible involves being willing to tailor solutions, accommodate special requests, and adjust approaches to meet individual customer requirements.
- Follow-up and Accountability:Following up with customers after resolving their inquiries or issues demonstrates a commitment to customer satisfaction and ensures that their needs have been met. Additionally, taking accountability for any mistakes or shortcomings and working to rectify them builds trust and reinforces the customer’s confidence in the service provider.
By embodying these qualities, organizations can deliver exceptional customer service experiences that foster customer loyalty, positive word-of-mouth, and long-term success.
FAQs
What are the advantages of Ceramic Substrate LEDs?
Ceramic Substrate LEDs offer several advantages, including superior thermal management, excellent durability, resistance to environmental factors, and versatility in design and integration. They are well-suited for high-power applications and demanding environments.
How do Ceramic Substrate LEDs differ from traditional LEDs?
Unlike traditional LEDs, which may use materials like metal or silicon as the substrate, Ceramic Substrate LEDs utilize ceramic materials with higher thermal conductivity. This allows for better heat dissipation and improved performance, especially in high-power applications.
What applications are Ceramic Substrate LEDs suitable for?
Ceramic Substrate LEDs are suitable for a wide range of applications, including general lighting, automotive lighting, outdoor lighting, display backlighting, and industrial applications where reliability and thermal management are critical.
Are Ceramic Substrate LEDs more expensive than traditional LEDs?
While Ceramic Substrate LEDs may have a higher initial cost compared to traditional LEDs, they offer superior performance and longevity, which can result in cost savings over the long term, particularly in high-power applications where thermal management is crucial.
Can Ceramic Substrate LEDs be customized for specific applications?
Yes, Ceramic Substrate LEDs can be customized to meet specific application requirements, including variations in size, shape, electrical characteristics, and optical properties. Customization allows for tailored solutions to address the unique needs of different applications.
Are there any limitations or considerations when using Ceramic Substrate LEDs?
While Ceramic Substrate LEDs offer many advantages, it’s essential to consider factors such as compatibility with existing systems, thermal management requirements, and cost-effectiveness for the intended application. Additionally, proper handling and installation procedures should be followed to maximize performance and reliability.