Ceramic PCB Substrates Manufacturing
Ceramic PCB Substrates Manufacturing,Ceramic PCB substrates, also known as ceramic printed circuit boards, are advanced electronic substrates composed of ceramic materials such as alumina (Al2O3) or aluminum nitride (AlN). These substrates offer exceptional thermal conductivity, excellent electrical insulation, and mechanical robustness, making them ideal for demanding electronic applications. Ceramic PCB substrates are commonly used in industries such as power electronics, LED lighting, RF/microwave circuits, automotive electronics, and aerospace systems.
One of the key advantages of ceramic PCB substrates is their ability to efficiently dissipate heat generated by electronic components, thus enabling reliable performance in high-power applications. Additionally, their superior electrical insulation properties prevent short circuits and signal interference, ensuring optimal signal integrity. Moreover, ceramic substrates exhibit excellent dimensional stability, chemical resistance, and compatibility with various assembly processes, making them highly versatile for diverse electronic designs.
Overall, ceramic PCB substrates represent a critical component in modern electronic systems, providing engineers with a reliable foundation for developing high-performance, durable, and efficient electronic devices.
What is a Ceramic PCB Substrate?
A Ceramic PCB (Printed Circuit Board) substrate is a type of substrate material used in electronic circuits. It’s made from ceramics, which are non-metallic, inorganic compounds typically formed through the process of firing, heating, and cooling. Ceramic PCB substrates offer several advantages over traditional organic substrates like FR4 (a type of fiberglass-reinforced epoxy laminate). These advantages include:
- High Thermal Conductivity: Ceramics generally have higher thermal conductivity compared to organic substrates. This property allows for efficient dissipation of heat generated by electronic components, making ceramic PCBs suitable for high-power applications and those requiring thermal management.
- Excellent Electrical Insulation: Ceramics are good electrical insulators, which is crucial for preventing short circuits and maintaining signal integrity in electronic circuits.
- Mechanical Strength: Ceramic substrates tend to have higher mechanical strength and rigidity compared to organic substrates, making them more resistant to mechanical stresses such as bending and flexing.
- Chemical Resistance: Ceramics are typically resistant to chemicals and environmental factors such as moisture and humidity, enhancing the durability and reliability of ceramic PCBs.
- Dimensional Stability: Ceramics exhibit low coefficient of thermal expansion (CTE), meaning they are less prone to expansion and contraction with temperature variations. This property helps maintain the dimensional stability of the PCB over a wide range of operating conditions.
Ceramic PCB substrates are commonly used in applications where high performance, reliability, and thermal management are critical, such as power electronics, RF/microwave circuits, LED lighting, automotive electronics, and aerospace systems. While ceramic PCB substrates offer numerous advantages, they also tend to be more expensive and challenging to manufacture compared to organic substrates, which can limit their use in cost-sensitive applications.
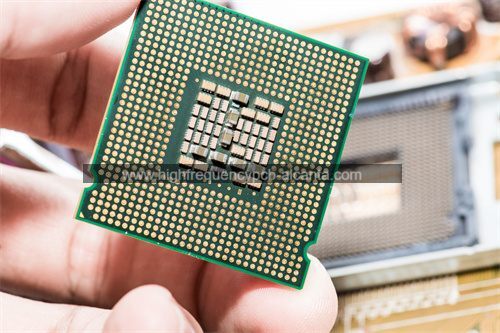
Ceramic PCB Substrates Manufacturing
What are the Ceramic PCB Substrate Design Guidelines?
Ceramic PCB substrates have specific design guidelines to ensure optimal performance and reliability of electronic circuits. Some common design guidelines for ceramic PCB substrates include:
- Thermal Management: Design the layout to facilitate efficient heat dissipation from high-power components. Ensure adequate spacing between components to prevent thermal hotspots and consider the use of thermal vias or heat sinks to improve thermal conductivity.
- Electrical Isolation: Maintain proper electrical isolation between circuit elements to prevent short circuits. Use appropriate clearance and isolation techniques, such as spacing between conductive traces and vias, to minimize the risk of electrical interference.
- Signal Integrity: Pay attention to signal routing and impedance matching to maintain signal integrity. Use controlled impedance traces for high-speed signals and minimize signal reflections and crosstalk by following best practices in routing and layout.
- Mechanical Stability: Design the PCB layout to withstand mechanical stresses and vibrations encountered during operation. Ensure proper support for heavy components and consider the mechanical strength of the ceramic substrate material in the design.
- Component Placement: Optimize the placement of components to minimize signal path lengths, reduce parasitic effects, and improve overall circuit performance. Consider the location of critical components, such as oscillators and RF modules, to minimize interference and noise.
- Manufacturability: Design the PCB with manufacturability in mind, considering the capabilities and limitations of ceramic PCB fabrication processes. Ensure that the design is compatible with the chosen manufacturing techniques, such as laser drilling for vias or thick film printing for conductive traces.
- Environmental Considerations: Take into account environmental factors such as temperature, humidity, and exposure to chemicals or contaminants. Select materials and coatings that provide protection against environmental hazards and ensure long-term reliability of the ceramic PCB.
Following these design guidelines helps ensure that ceramic PCB substrates meet performance requirements, reliability standards, and manufacturing constraints for various electronic applications.
What is the Ceramic PCB Substrate Fabrication Process?
The fabrication process for ceramic PCB substrates involves several steps to create the necessary circuitry on the ceramic material. Here’s a general overview of the process:
- Substrate Preparation: The process starts with preparing the ceramic substrate material. Ceramic materials such as alumina (Al2O3) or aluminum nitride (AlN) are commonly used due to their excellent thermal conductivity and electrical insulation properties. The ceramic substrate is typically in the form of a sheet or panel.
- Circuit Design and Layout: The circuit design is created using specialized PCB design software. This involves designing the layout of conductive traces, vias, and component placement according to the desired functionality and performance requirements of the electronic circuit.
- Film Deposition or Thick Film Printing: In ceramic PCB fabrication, conductive traces and components are typically applied using either thin film deposition techniques or thick film printing methods. Thin film deposition involves depositing thin layers of conductive materials such as gold or silver onto the ceramic substrate through techniques like sputtering or evaporation. Thick film printing involves using a paste made of conductive materials mixed with glass binders, which is screen-printed onto the substrate and then fired to form the conductive traces.
- Via Formation: Vias are small holes drilled or laser-ablated through the ceramic substrate to create electrical connections between different layers of the circuit. Laser drilling is commonly used due to its precision and ability to create small-diameter vias without damaging the substrate.
- Metallization and Plating: After via formation, the vias are typically metallized to provide electrical conductivity between different layers of the circuit. This may involve depositing a thin layer of metal onto the walls of the vias using techniques such as sputtering or electroplating.
- Component Attachment: Electronic components such as integrated circuits (ICs), resistors, capacitors, and other active and passive devices are then attached to the ceramic substrate using techniques such as soldering, wire bonding, or flip-chip bonding.
- Curing and Firing: The assembled ceramic PCB undergoes a curing and firing process to bond the conductive traces, vias, and components to the substrate and to achieve the desired electrical and mechanical properties. The firing process typically involves subjecting the PCB to high temperatures in a controlled atmosphere furnace.
- Surface Finish and Coating: Once the firing process is complete, the ceramic PCB may undergo surface finishing processes such as solder mask application, surface coating, or protective encapsulation to improve solderability, protect against environmental factors, and enhance overall reliability.
- Quality Control and Testing: Finally, the fabricated ceramic PCBs undergo rigorous quality control and testing procedures to ensure that they meet the specified performance criteria and reliability standards before being released for use in electronic devices.
Overall, the fabrication process for ceramic PCB substrates requires specialized equipment and expertise to achieve high precision, reliability, and performance in electronic circuits.
How do you manufacture Ceramic PCB Substrates?
Manufacturing ceramic PCB substrates involves a series of specialized processes to create the necessary circuitry on the ceramic material. Here’s an overview of the typical manufacturing steps:
- Substrate Preparation: Ceramic materials such as alumina (Al2O3) or aluminum nitride (AlN) are used as the substrate material. The ceramic substrate is usually in the form of sheets or panels. These substrates are manufactured separately and supplied to PCB manufacturers.
- Circuit Design: The circuit design is created using PCB design software, specifying the layout of conductive traces, vias, and component placement. Design considerations include electrical performance, thermal management, and mechanical stability.
- Film Deposition or Thick Film Printing: Conductive traces and components are applied to the ceramic substrate using either thin film deposition techniques or thick film printing methods. Thin film deposition involves depositing thin layers of conductive materials such as gold or silver onto the substrate through techniques like sputtering or evaporation. Thick film printing involves screen-printing a paste made of conductive materials mixed with glass binders onto the substrate, which is then fired to form the conductive traces.
- Via Formation: Vias are created to establish electrical connections between different layers of the circuit. This may involve laser drilling or mechanical drilling to create small holes through the ceramic substrate. Laser drilling is preferred for its precision and ability to create small-diameter vias.
- Metallization and Plating: After via formation, the vias are typically metallized to provide electrical conductivity between different layers of the circuit. This may involve depositing a thin layer of metal onto the walls of the vias using techniques such as sputtering or electroplating.
- Component Attachment: Electronic components such as integrated circuits (ICs), resistors, capacitors, and other devices are attached to the ceramic substrate using techniques such as soldering, wire bonding, or flip-chip bonding.
- Curing and Firing: The assembled ceramic PCB undergoes a curing and firing process to bond the conductive traces, vias, and components to the substrate. This process involves subjecting the PCB to high temperatures in a controlled atmosphere furnace to achieve the desired electrical and mechanical properties.
- Surface Finish and Coating: Once the firing process is complete, the ceramic PCB may undergo surface finishing processes such as solder mask application, surface coating, or protective encapsulation to improve solderability, protect against environmental factors, and enhance overall reliability.
- Quality Control and Testing: The fabricated ceramic PCBs undergo rigorous quality control and testing procedures to ensure they meet specified performance criteria and reliability standards before being released for use in electronic devices.
Overall, manufacturing ceramic PCB substrates requires specialized equipment, expertise, and controlled processes to achieve high precision, reliability, and performance in electronic circuits.
How much should a Ceramic PCB Substrate cost?
The cost of a ceramic PCB substrate can vary widely depending on several factors such as:
- Material Type: Different ceramic materials have different costs associated with them. For example, alumina (Al2O3) and aluminum nitride (AlN) are commonly used ceramic substrates, but they may have different prices due to variations in material properties and manufacturing processes.
- Substrate Size and Thickness: Larger substrates or substrates with greater thickness may cost more due to increased material usage and manufacturing complexity.
- Manufacturing Processes: The cost of manufacturing processes such as thin film deposition, thick film printing, laser drilling, metallization, and firing can significantly impact the overall cost of the ceramic PCB substrate.
- Complexity of Circuit Design: PCBs with complex circuit designs, dense trace patterns, and multiple layers may require more intricate manufacturing processes, leading to higher costs.
- Volume and Order Size: Economies of scale can play a significant role in determining the cost of ceramic PCB substrates. Larger order sizes typically result in lower per-unit costs due to efficiencies in manufacturing and material procurement.
- Supplier and Location: The choice of supplier and their location can also influence the cost of ceramic PCB substrates. Suppliers with advanced manufacturing capabilities or located in regions with lower labor and production costs may offer more competitive pricing.
- Additional Features and Requirements: Additional features such as surface finishes, coatings, testing, and certifications may add to the overall cost of the ceramic PCB substrate.
Given these factors, it’s challenging to provide a specific cost without knowing the details of the substrate’s specifications, quantity, and supplier. However, ceramic PCB substrates tend to be more expensive than traditional organic substrates like FR4 due to their superior thermal and electrical properties, as well as the complexity of manufacturing processes involved. As a rough estimate, the cost of a ceramic PCB substrate can range from a few dollars to several hundred dollars per unit, depending on the aforementioned factors.
What is Ceramic PCB Substrate base material?
Ceramic PCB substrates are typically made from various types of ceramic materials chosen for their excellent thermal conductivity, electrical insulation properties, and mechanical stability. Some common ceramic materials used as base substrates for ceramic PCBs include:
- Alumina (Al2O3): Alumina is one of the most widely used ceramic materials for PCB substrates due to its high thermal conductivity, good electrical insulation properties, and relatively low cost. It is suitable for a wide range of applications, including power electronics, LED lighting, and RF/microwave circuits.
- Aluminum Nitride (AlN): Aluminum nitride offers even higher thermal conductivity than alumina, making it ideal for applications requiring efficient heat dissipation, such as high-power electronics and high-frequency circuits. AlN substrates also exhibit good electrical insulation and excellent dimensional stability.
- Silicon Carbide (SiC): Silicon carbide is known for its exceptional thermal conductivity, high temperature resistance, and chemical inertness. It is often used in demanding applications where extreme temperatures and harsh environments are present, such as automotive electronics, aerospace systems, and power semiconductor devices.
- Beryllium Oxide (BeO): Beryllium oxide offers very high thermal conductivity, second only to diamond among ceramic materials. However, it is less commonly used due to concerns over beryllium toxicity. BeO substrates are primarily utilized in specialized applications where ultra-high thermal performance is required, such as high-power RF amplifiers and laser diode modules.
These ceramic materials serve as the base substrate onto which conductive traces, vias, and electronic components are integrated to create ceramic PCBs. The choice of substrate material depends on the specific requirements of the application, including thermal management needs, electrical performance, and environmental considerations.
Which company makes Ceramic PCB Substrates?
There are many companies that produce ceramic PCB substrates, some well-known manufacturers include Rogers Corporation, Kyocera, Materion Corporation from the United States, as well as Chinese companies like Ruifeng Technology and Guangbao Technology. These companies are dedicated to the research and manufacture of high-performance ceramic PCB substrates to meet the needs of various electronic applications.
As for our company, we are also a professional manufacturer of ceramic PCB substrates. We have advanced production equipment and a skilled technical team, committed to providing high-quality and reliable products. Our production process includes:
- Professional design team: We have an experienced team of engineers who can provide customized design solutions according to customer requirements.
- Advanced production equipment: We have introduced advanced production equipment and technologies, including thin film deposition, laser drilling, thick film printing, and others, to ensure product quality and performance stability.
- Strict quality control: We strictly adhere to ISO quality management system standards, conduct rigorous screening and testing of raw materials, and ensure that each process meets standard requirements.
- Comprehensive after-sales service: We provide comprehensive after-sales services, including technical support, problem-solving, and product maintenance, to ensure customer satisfaction and trust.
As a professional manufacturer of ceramic PCB substrates, we are committed to providing high-quality, high-performance products, and services to our customers. Our products are widely used in power electronics, LED lighting, RF/microwave circuits, and other fields, and have received consistent praise from customers. We welcome you to cooperate with us for mutual development and growth!
What are the 7 qualities of good customer service?
Good customer service is characterized by several key qualities that contribute to positive experiences and satisfaction for customers. Here are seven qualities of good customer service:
- Responsiveness: Good customer service involves promptly addressing customer inquiries, concerns, and requests. This means providing timely responses to phone calls, emails, live chat messages, and other forms of communication. Customers appreciate quick assistance and solutions to their issues.
- Empathy: Empathy is crucial in understanding and relating to customers’ emotions, needs, and challenges. Good customer service representatives listen attentively, show genuine concern, and demonstrate empathy towards customers’ situations, fostering trust and rapport.
- Professionalism: Professionalism entails conducting oneself with integrity, respect, and courtesy towards customers at all times. This includes maintaining a positive attitude, using appropriate language and tone, and adhering to company policies and standards. Professional behavior instills confidence and reliability in customers’ interactions with the company.
- Knowledgeability: Good customer service representatives possess comprehensive knowledge about the company’s products, services, policies, and procedures. They can effectively answer customer questions, provide accurate information, and offer relevant recommendations or solutions. Knowledgeable staff build credibility and instill confidence in customers.
- Flexibility: Flexibility involves adapting to customers’ needs and preferences to accommodate diverse situations and requirements. Good customer service entails being open-minded, resourceful, and willing to find creative solutions to meet customers’ demands, even in challenging circumstances.
- Consistency: Consistency is essential for maintaining high-quality customer service across all interactions and touchpoints. Customers expect consistent experiences regardless of the channel or representative they engage with. Good customer service requires standardized processes, clear communication, and alignment with the company’s brand values.
- Follow-up and Resolution: Good customer service doesn’t end with initial interactions but extends to follow-up and resolution of issues. This involves ensuring that customer concerns are fully addressed, problems are resolved satisfactorily, and appropriate actions are taken to prevent recurrence. Follow-up communication demonstrates commitment to customer satisfaction and fosters long-term loyalty.
By embodying these qualities, businesses can deliver exceptional customer service experiences that build trust, loyalty, and positive relationships with customers.
FAQs (Frequently Asked Questions)
What are the advantages of Ceramic PCB Substrates over traditional PCBs?
Ceramic substrates offer superior thermal conductivity, electrical insulation, and mechanical stability compared to traditional materials like fiberglass.
They are well-suited for high-performance applications in industries such as aerospace, automotive, and telecommunications.
Are Ceramic PCB Substrates more expensive than traditional PCBs?
Yes, Ceramic PCB Substrates tend to be more expensive due to the higher cost of ceramic materials and specialized manufacturing processes.
What are some common applications of Ceramic PCB Substrates?
Ceramic PCB Substrates are commonly used in power electronics, LED lighting, RF/microwave devices, and high-frequency circuits where thermal management and reliability are critical.
Can Ceramic PCB Substrates be manufactured in custom shapes and sizes?
Yes, Ceramic PCB Substrates can be customized to meet specific design requirements, including complex shapes and sizes.
What are the main factors to consider when designing with Ceramic PCB Substrates?
Design considerations include thermal management, signal integrity, component placement, and manufacturing tolerances. Ensuring proper thermal expansion matching and optimizing trace routing are particularly important.
How durable are Ceramic PCB Substrates compared to traditional PCBs?
Ceramic PCB Substrates offer excellent mechanical stability and durability, making them highly resistant to temperature extremes, vibration, and mechanical stress compared to traditional PCB materials.