What is a Ceramic PCB?
Ceramic PCB Manufacturer,Ceramic PCBs are advanced circuit boards constructed from ceramic materials, offering superior electrical and thermal properties. These substrates provide excellent heat dissipation, ensuring stable performance in high-power applications. With low dielectric constants and minimal signal loss, ceramic PCBs enable efficient signal transmission in high-frequency circuits. They are resistant to corrosion, moisture, and extreme temperatures, making them ideal for harsh environments such as automotive, aerospace, and medical industries. Ceramic PCBs are widely used in electronic devices requiring reliability, durability, and high performance, where conventional materials may not meet stringent requirements.
Ever pondered the backstage maestros orchestrating the electronic symphony? Enter the realm of Ceramic Printed Circuit Boards (PCBs), the avant-garde artisans reshaping the narrative. These boards dare to defy convention, bidding adieu to the mundane materials like fiberglass and epoxy, and instead, don the sophisticated garb of ceramics—typically, the likes of alumina or aluminum nitride. Let’s unravel the mystique of Ceramic PCBs and decode why they’re the trailblazers of contemporary electronics.
Inner Alchemy:
Ceramic Nexus: Envision the core of a Ceramic PCB as an alchemical blend of ceramics, exuding thermal brilliance, mechanical mettle, and an unwavering composure across the temperature spectrum.
Trace Tapestry: Much like clandestine paths in a labyrinth, Ceramic PCBs host an intricate tapestry of traces, woven from metallic strands, creating a symphony of connections between electronic comrades.
Marvels of Enchantment:
Thermal Sorcery: The true enchantment of Ceramic PCBs lies in their thermal wizardry. Picture them as adept sorcerers, gracefully dissipating heat, making them the chosen custodians for high-powered electronic devices, where cool composure is the epitome.
Frequency Incantations: Unfazed by the realms of high-frequency sorcery, Ceramic PCBs wield a low dielectric loss, making them the maestros in preserving signal integrity amidst frequency tumult.
Mechanical Alchemy: Far from mundane, these boards possess a mechanical alchemy, scoffing at stress and dancing through the vibrations with an air of invincibility.
Stellar Performers in the Electronic Constellation:
Power Conjurations: Ceramic PCBs take the spotlight in power electronic devices, the conjurers behind power amplifiers, voltage regulators, and power converters—where the mastery of heat dissipation is the sacred grail.
RF and Microwave Ovations: Ever witnessed a PCB stealing the thunder in the radiofrequency and microwave theatrics? That’s the Ceramic PCBs, commanding the stage, empowering antennas and communication systems with their low signal loss and thermal brilliance.
LED Luminescence: Illuminating the electronic cosmos, Ceramic PCBs play a pivotal role in LED technology. They are the custodians of the LED magic in high-power lighting fixtures, mastering the art of heat governance.
In essence, Ceramic PCBs are the virtuosos of the electronic overture, wielding thermal batons, casting high-frequency spells, and standing resilient against the forces of stress. They transcend being mere components; they’re the unsung heroes crafting the melody of electronic marvels, especially in arenas thirsting for heat dissipation and unwavering performance.
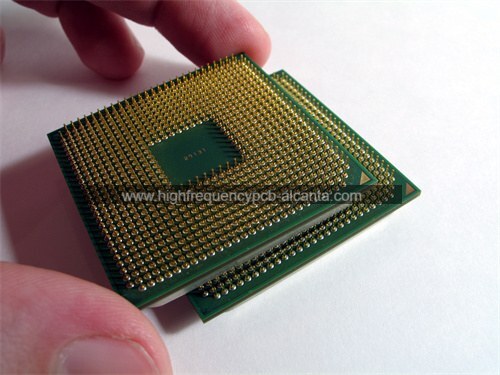
Ceramic PCB Manufacturer
How do Ceramic PCBs Function?
Picture Ceramic Printed Circuit Boards (PCBs) as the unsung heroes of electronic harmony, weaving a tale of enhanced performance and unwavering reliability. These specialized circuit boards, donning ceramic substrates crafted from alumina or aluminum nitride, orchestrate a symphony of functions tailored for applications craving high power, high frequency, and beyond.
Thermal Choreography:
Function: The ceramic substrates, donned in alumina or aluminum nitride attire, boast exceptional thermal conductivity.
Role: In the realm of high-power electronics, Ceramic PCBs take center stage, gracefully choreographing the dissipation of heat generated by components. This dance of thermal management ensures a performance sans overheating, ensuring devices operate optimally and reliably.
High-Frequency Ballet:
Function: Ceramic materials take the stage with minimal dielectric loss, especially at high frequencies.
Role: The grand performance lies in high-frequency and radiofrequency (RF) applications. Ceramic PCBs, with their prowess in maintaining signal integrity amidst frequency crescendos, become indispensable in the grand orchestra of RF amplifiers, antennas, and communication systems.
Mechanical Resilience:
Function: Ceramic materials flex their muscles, showcasing robust mechanical strength.
Role: In the face of physical stress, vibrations, or the rigors of challenging environments, Ceramic PCBs stand tall. Their resilience becomes the backbone of longevity and reliability for the electronic devices they grace.
Dielectric Harmony:
Function: The dielectric constant of ceramic substrates maintains a stable melody across a spectrum of temperatures.
Role: This harmonious stability in dielectric properties becomes the key to a consistent electrical performance, irrespective of the environmental temperature. It’s the secret sauce for the reliability of Ceramic PCBs across diverse operating conditions.
Insulation Ballet:
Function: Ceramic material takes on the role of an electrical virtuoso, providing top-notch insulation.
Role: In the dance of electrons, Ceramic PCBs ensure a flawless performance by isolating conductive traces and components. This insulation prowess guards against unwanted electrical duets, ensuring a pristine performance devoid of interference.
LED Luminary Act:
Function: Ceramic PCBs step into the limelight in high-power LED applications.
Role: Their ability to manage heat takes center stage in LED technology, where temperature control becomes the director’s cue for the longevity and peak performance of LEDs.
Power Electronics Choreography:
Function: Ceramic PCBs take a leading role in the power electronic ensemble.
Role: From power amplifiers to voltage regulators and power converters, Ceramic PCBs join forces to choreograph the ballet of efficient heat dissipation and unwavering operation in power-hungry applications.
In essence, Ceramic PCBs are the conductors in the electronic symphony, where thermal ballet, high-frequency performances, and mechanical resilience take center stage. Their unique material properties become the notes that compose the melody of reliable performance, especially in applications demanding the perfect harmony of high power and high frequency.
What Types of Ceramic PCBs Exist?
Embark on an exploration of the nuanced world of Ceramic Printed Circuit Boards (PCBs), where the selection of ceramic substrates becomes a pivotal design choice, shaping the unique characteristics of each variant. From the venerable alumina-based renditions to the cutting-edge alternatives like aluminum nitride, the landscape of Ceramic PCBs unfolds as a canvas of specialized advantages, addressing specific needs in thermal management, electrical performance, and overall functionality.
Alumina (Aluminum Oxide) Ceramic PCBs:
Composition: Alumina takes the helm as the foundational material in these PCBs.
Essence:
Thermal Guardians: Alumina-based Ceramic PCBs assert their dominance in the realm of thermal regulation, adeptly managing the dissipation of heat.
Mechanical Fortresses:Blessed with robust mechanical resilience, these PCBs rise as unwavering sentinels, standing tall as guardians of enduring strength and unyielding reliability.
Aluminum Nitride Ceramic PCBs:
Composition: Aluminum nitride emerges as a frontrunner, defining the core substrate material.
Advantages:
Thermal Virtuosos: With exceptional thermal conductivity, aluminum nitride Ceramic PCBs lead the charge in applications requiring superior heat dissipation.
Signal Custodians: These PCBs serve as vigilant custodians of signal integrity, especially in scenarios demanding unblemished electrical pathways at high frequencies.
Hybrid Ceramic PCBs:
Composition: Hybrid Ceramic PCBs tell a story of diversity, intertwining a fusion of different ceramic materials to create a rich tapestry of versatility and tailored excellence.
Versatility:
Tailored Brilliance: By harmonizing the virtues inherent in materials such as alumina and aluminum nitride, hybrid PCBs encapsulate a personalized equilibrium of thermal resilience, mechanical fortitude, and electrical prowess.
Zirconia Ceramic PCBs:
Composition: Zirconia, a ceramic virtuoso, takes center stage as the elemental cornerstone.
Attributes:
Heat Defenders: Zirconia-based Ceramic PCBs showcase resilience in high-temperature domains, carving a niche for applications under challenging thermal conditions.
Stability Sentinels: Their resilience against chemical reactions transforms them into stalwart guardians, steadfastly repelling the erosive effects of time.
Silicon Carbide (SiC) Ceramic PCBs:
Composition: Silicon carbide, a vibrant fusion of silicon and carbon, stands as the elemental tapestry.
Dominance:
Thermal Connoisseurs: SiC Ceramic PCBs emerge as connoisseurs of thermal dynamics, excelling in thermal conductivity and mastering the intricate dance of effective heat dissipation.
Temperature Warriors: With resilience to high temperatures, they become warriors in applications subjected to the crucible of harsh thermal environments.
Titanate Ceramic PCBs:
Composition: Titanate ceramics carve their niche as the foundational material.
Attributes:
Dielectric Virtuosos: Titanate ceramics often showcase dielectric mastery, earning their place in applications where precise electrical insulation is the conductor’s baton.
In this tapestry of material choices, designers wield the palette of Ceramic PCBs, selecting types that resonate harmoniously with the unique demands of their electronic opus.
Ceramic PCBs vs. Traditional PCBs: What Sets Them Apart?
Step into the dynamic world of electronic circuit boards, where Ceramic Printed Circuit Boards (PCBs) and their traditional counterparts diverge in features, offering unique traits that cater to distinct electronic demands.
Material Symphony:
Ceramic PCBs: Crafted from ceramic elegance—alumina or aluminum nitride—with metallic traces creating intricate pathways.
Traditional PCBs: Composed of the familiar duo, fiberglass (often FR-4) and epoxy substrates, with copper traces etching the conventional route.
Thermal Ballet:
Ceramic PCBs: Take the lead in thermal choreography with superior conductivity, gracefully dissipating heat. A virtuoso performance for high-power applications seeking an efficient thermal pas de deux.
Traditional PCBs: Navigate the thermal stage with FR-4, showcasing some thermal prowess but often requiring additional steps for heat relief in demanding scenarios.
High-Frequency Sonata:
Ceramic PCBs: Strike a chord with low dielectric loss, earning the spotlight in high-frequency and radiofrequency ensembles. A harmonious dance, preserving signal integrity in the crescendo of elevated frequencies.
Traditional PCBs: Play their part in the frequency spectrum, but FR-4 materials may introduce some dissonance with higher dielectric losses.
Mechanical Ballet:
Ceramic PCBs: Exhibit strength worthy of a ceramic ballerina, resilient to physical stress and vibrations—a dance partner for longevity.
Traditional PCBs: Showcase reasonable mechanical prowess but may not pirouette as gracefully as ceramics, susceptible to more wear and tear.
Cost Sonata:
Ceramic PCBs: Dressed in elegance but often command a higher ticket price due to the intricacies of ceramic craftsmanship.
Traditional PCBs: Adorned in practicality, cost-effective, a pragmatic choice for scenarios where financial considerations waltz to the forefront.
Application Symphony:
Ceramic PCBs: Feature in grand performances of high-power electronics, intricate high-frequency compositions, RF/microwave sonnets, and illuminate the stage in LED technology, especially where thermal brilliance takes the lead.
Traditional PCBs: Versatile performers, cost-efficient, gracing a broad repertoire of electronic devices, especially those with standard power prerequisites.
In this electronic ballet, the choice between Ceramic PCBs and Traditional PCBs becomes a choreography of considerations. Ceramic PCBs command the stage in specialized performances, while Traditional PCBs remain the reliable ensemble for a multitude of electronic productions. The selection becomes an art, aligning with the nuanced demands and aesthetics of each electronic composition.
How are Ceramic PCBs Structured and Produced?
Exploring the complexities of Ceramic PCBs unveils a detailed production journey meticulously crafted to enhance thermal conductivity, provide robust mechanical support, and elevate electrical performance. Let’s navigate through the layered composition and advanced production methods that characterize these circuit boards.
Ceramic Substrate Foundation:
At the heart of the structure resides the ceramic substrate, commonly crafted from materials such as aluminum oxide (Al2O3) or aluminum nitride (AlN). This fundamental layer serves as the bedrock, imparting formidable thermal conductivity, mechanical resilience, and electrical insulation to the entire assembly.
Conductor Trace Network:
Interwoven with the ceramic substrate are conductor traces, intricately patterned to establish electrical connections. Copper is a common choice for these traces, deposited through techniques like sputtering or thick-film deposition.
Dielectric Layers Integration:
Intervening dielectric layers strategically placed between conductive traces serve to insulate and shield against electrical interference. These layers significantly contribute to the PCB’s overall electrical performance and reliability.
Via Holes for Vertical Connections:
Via holes, whether through-hole, blind, or buried, facilitate vertical connections between different layers. Techniques like laser drilling or mechanical drilling are employed based on the precision and complexity requirements.
Solder Mask Armor:
A protective layer, known as the solder mask, shields conductive traces from environmental factors and prevents unintended short circuits during assembly. Typically sporting a green hue, it is applied using a screening process.
Surface Finish Fortification:
Surface finishes such as gold plating, tin-lead (HASL), or immersion silver are applied to exposed metal surfaces. These finishes enhance solderability and shield against oxidation.
Harnessing Advanced Techniques:
Embracing High-Density Interconnect (HDI) fabrication allows for finer lines and spaces, enabling intricate designs. Semi-Additive processes selectively deposit metal, optimizing material usage and precision.
Quality Control Vigilance:
Rigorous quality control measures are seamlessly woven into the manufacturing process, ensuring the end product aligns with specifications and industry standards.
This amalgamation of ceramic prowess, meticulous layering, and innovative manufacturing processes positions Ceramic PCBs as stalwarts in electronic applications demanding both high performance and reliability, particularly where effective thermal management is paramount.
FAQs: Common Questions about Ceramic PCBs
What role do conductor traces play in Ceramic PCBs?
Conductor traces establish electrical connections between components. Typically made of metals like copper, these traces contribute to the PCB’s overall electrical performance.
What advanced manufacturing processes are used in Ceramic PCB fabrication?
Enhanced HDI fabrication and semi-additive methods are common in Ceramic PCB manufacturing, allowing for finer details and improved precision in design.
Are there specific surface finishes applied to Ceramic PCBs?
Yes, common surface finishes include gold plating, tin-lead (HASL), or immersion silver, enhancing solderability and protecting exposed metal surfaces.
Are Ceramic PCBs apt for consumer electronics?
Indeed. The combination of substantial mechanical strength and effective electrical insulation positions Ceramic PCBs as a fitting choice for a diverse array of consumer electronic devices, ensuring both reliability and performance.
How does the solder mask contribute to Ceramic PCBs?
The solder mask acts as a protective layer, safeguarding conductive traces from environmental factors and preventing unintended short circuits during assembly, thereby ensuring the PCB’s reliability.
In Conclusion: The Significance of Ceramic PCBs
As we bring our journey through the realm of Ceramic PCBs to a close, it’s essential to recognize their pivotal role as a linchpin in technology. These circuit boards embody a delicate harmony of thermal efficiency, electrical finesse, and mechanical resilience, leaving an indelible mark on the ever-shifting canvas of PCB engineering.
Melody of Thermal Efficiency:
Ceramic PCBs, anchored in materials like aluminum oxide or aluminum nitride, emerge as champions of thermal conductivity. This innate trait ensures the proficient dissipation of heat—a critical factor amid the escalating power demands in today’s electronic landscape.
Symphony of Electrical Excellence:
The meticulously etched conductor traces on the ceramic substrate play a symphonic role in elevating the PCB’s electrical performance. Opting for materials like copper orchestrates seamless connectivity, minimal signal loss, and optimal electrical conductivity—crucial notes in the symphony of high-performance electronics.
Resilience in Mechanical Cadence:
At the core, the robust ceramic substrate not only amplifies thermal efficiency but also lends crucial mechanical strength. This resilience ensures durability, allowing Ceramic PCBs to dance gracefully through environmental challenges and physical demands, fortifying their reliability.
Navigating the Dynamic Dance of PCB Engineering:
In a landscape where PCB engineering pirouettes to the tune of innovation, Ceramic PCBs emerge as nimble partners. Their adaptability and bespoke design capabilities make them apt for a diverse array of applications, ranging from the grace of consumer electronics to the robustness of industrial power systems.
A Glimpse into Harmonious Futures:
Pondering the significance of Ceramic PCBs reveals that these technological virtuosos aren’t just responses to the present but glimpses into harmonious futures. Their role in elevating electronic performance while ensuring stability positions them as indispensable architects in the ever-evolving symphony of electronics.
In essence, Ceramic PCBs encapsulate the delicate interplay of thermal efficiency, electrical virtuosity, and mechanical resilience, leaving an enduring imprint on the evolving landscape of PCB engineering.