Ceramic Packages For MEMS Sensors Manufacturing
Ceramic Packages For MEMS Sensors Manufacturing,Ceramic Package MEMS Sensors (CPMS) represent a pinnacle in sensor technology, encapsulating Microelectromechanical Systems (MEMS) within robust ceramic housings. CPMS are engineered to withstand demanding environments, offering exceptional performance, reliability, and longevity. These sensors leverage advanced ceramic materials such as alumina (Al2O3) or aluminum nitride (AlN), renowned for their superior thermal stability, mechanical strength, and electrical insulation properties. With hermetic sealing capabilities, CPMS provide protection against moisture, dust, and other contaminants, making them ideal for diverse applications across industries including automotive, aerospace, and medical devices. The manufacturing process for CPMS involves precise shaping, firing, metallization, and assembly techniques to ensure the creation of highly durable and resilient sensor packages. Customizable and adaptable, CPMS can be tailored to meet specific application requirements, offering versatility and flexibility. Overall, CPMS exemplify cutting-edge sensor technology, offering unparalleled performance and reliability in demanding operational environments.
What is a Ceramic Package for MEMS Sensors?
A ceramic package for MEMS (Microelectromechanical Systems) sensors is a type of housing or enclosure designed to protect and encapsulate the MEMS sensor component. MEMS sensors are tiny devices that combine mechanical and electrical components on a microscopic scale, typically used for sensing various physical phenomena such as acceleration, pressure, temperature, and more.
Ceramic packages offer several advantages for MEMS sensors:
- Hermetic sealing: Ceramic materials can provide excellent hermeticity, meaning they can seal the MEMS sensor from the external environment, protecting it from moisture, dust, and other contaminants. This is crucial for maintaining the sensor’s accuracy and longevity, especially in demanding or harsh environments.
- Thermal properties: Ceramics have good thermal conductivity and stability, which helps in dissipating heat generated by the sensor or from the environment. This can prevent overheating and ensure consistent sensor performance across a wide range of temperatures.
- Mechanical robustness: Ceramic packages offer high mechanical strength and durability, protecting the delicate MEMS components from mechanical shocks, vibrations, and other physical stresses. This is essential for ensuring the sensor’s reliability, especially in applications where it may be subjected to rough handling or mechanical impact.
- Electrical insulation: Ceramic materials are excellent electrical insulators, which helps in isolating the MEMS sensor from external electrical interference and provides protection against electrostatic discharge (ESD) events.
Overall, ceramic packages play a crucial role in enhancing the performance, reliability, and longevity of MEMS sensors in various applications, including automotive, aerospace, consumer electronics, medical devices, and industrial systems.
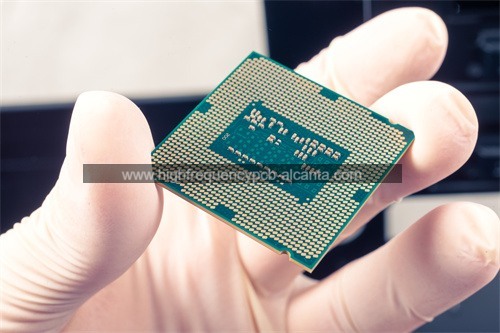
Ceramic Packages For MEMS Sensors Manufacturing
What are the CPMS Design Guidelines?
CPMS, which stands for Ceramic Package MEMS Sensors, is a term used to refer to MEMS sensors housed in ceramic packages. Design guidelines for CPMS typically include considerations and recommendations for various aspects of the sensor package design to ensure optimal performance, reliability, and manufacturability. Some common CPMS design guidelines may include:
- Hermetic Sealing: Ensuring the ceramic package provides adequate hermetic sealing to protect the MEMS sensor from moisture, dust, and other contaminants. This may involve selecting appropriate sealing materials and techniques.
- Material Selection: Choosing ceramic materials with suitable thermal, mechanical, and electrical properties to meet the requirements of the MEMS sensor and its intended application.
- Package Size and Shape: Designing the package dimensions and shape to accommodate the MEMS sensor and any required additional components while considering space constraints and integration with other system elements.
- Thermal Management: Incorporating features such as thermal vias, heat sinks, or other cooling mechanisms to dissipate heat effectively and maintain the sensor’s performance over a range of operating temperatures.
- Mechanical Stability: Ensuring the ceramic package provides sufficient mechanical stability and protection to withstand mechanical shocks, vibrations, and other environmental stresses encountered during handling and operation.
- Electrical Isolation: Designing the package to provide electrical isolation to prevent interference from external electrical sources and protect against electrostatic discharge (ESD) events.
- Manufacturability: Considering manufacturing processes and constraints to ensure the package design is compatible with mass production techniques and can be reliably manufactured at scale.
- Testing and Quality Assurance: Incorporating features such as test pads or access points to facilitate testing and calibration of the MEMS sensor during production, as well as implementing quality control measures to ensure consistent performance and reliability of the packaged sensors.
These guidelines may vary depending on the specific requirements of the MEMS sensor, its application, and the manufacturing capabilities of the production facility. Following CPMS design guidelines helps ensure that the ceramic package effectively protects the MEMS sensor while meeting performance and reliability requirements.
What is the CPMS Fabrication Process?
The fabrication process for Ceramic Package MEMS Sensors (CPMS) involves several steps to create the ceramic housing or enclosure for the MEMS sensor. Below is a general overview of the typical CPMS fabrication process:
- Design Phase: The process starts with the design of the ceramic package, considering factors such as the size and shape of the MEMS sensor, material properties, thermal management requirements, and manufacturing feasibility.
- Material Selection: Suitable ceramic materials are selected based on their thermal, mechanical, and electrical properties, as well as their compatibility with MEMS sensor requirements and manufacturing processes. Common ceramics used for CPMS include alumina (Al2O3) and aluminum nitride (AlN).
- Substrate Preparation: The ceramic substrate material is prepared by cutting, grinding, and polishing to achieve the desired dimensions and surface finish. This may involve CNC machining or other precision machining techniques.
- Green Body Formation: The ceramic substrate is formed into the desired shape using techniques such as dry pressing, injection molding, or tape casting. In this step, ceramic powder is mixed with binders and additives to form a green body with the required geometry.
- Drying: The green ceramic substrate is dried to remove excess moisture and solvents from the material. This helps prevent cracking and distortion during subsequent processing steps.
- Firing: The dried green ceramic substrate is fired in a kiln at high temperatures to sinter the ceramic particles and form a dense, solid structure. This step may involve multiple heating and cooling cycles to achieve the desired material properties and dimensional accuracy.
- Machining and Finishing: After firing, the ceramic substrate may undergo additional machining and finishing processes to refine its dimensions, surface finish, and features such as mounting holes, channels, or cavities for the MEMS sensor.
- Metallization: Metal layers are deposited onto the ceramic substrate surface using techniques such as sputtering, evaporation, or plating. These metallized layers serve various purposes, such as providing electrical contacts, heat dissipation paths, or hermetic sealing barriers.
- Assembly:The MEMS sensor component is assembled into the ceramic package, typically using adhesive bonding or soldering techniques. Any additional components, such as sealing lids or covers, may also be integrated at this stage.
- Testing and Quality Assurance: The completed CPMS undergoes testing to verify its performance, reliability, and conformance to specifications. This may include electrical testing, thermal cycling, vibration testing, and leak testing to ensure hermeticity.
- Packaging and Shipping: Once validated, the CPMS is packaged and prepared for shipping to customers or integration into larger systems.
Throughout the fabrication process, strict quality control measures are implemented to ensure consistency, reliability, and repeatability of the CPMS production. Advanced manufacturing technologies and techniques may be employed to optimize process efficiency and yield while meeting stringent performance requirements.
How do you manufacture CPMS?
Manufacturing Ceramic Package MEMS Sensors (CPMS) involves several key steps, including material preparation, shaping, firing, assembly, and testing. Below is a detailed outline of the typical manufacturing process for CPMS:
- Material Selection: The process begins with selecting suitable ceramic materials with properties that meet the requirements of the MEMS sensor and its intended application. Common ceramics used for CPMS include alumina (Al2O3) and aluminum nitride (AlN), chosen for their thermal, mechanical, and electrical properties.
- Material Preparation: The selected ceramic material is prepared for shaping by grinding, milling, and mixing it with binders and additives to form a homogeneous mixture.
- Shaping: The ceramic material is formed into the desired shape of the CPMS substrate using techniques such as dry pressing, injection molding, or tape casting. This step produces a “green body” with the approximate dimensions of the final CPMS substrate.
- Drying: The green ceramic substrate is dried to remove excess moisture and binders. This helps prevent cracking and distortion during firing.
- Firing (Sintering): The dried green ceramic substrate is fired in a kiln at high temperatures (typically above 1000°C) to sinter the ceramic particles and create a dense, solid structure. This step involves carefully controlled heating and cooling cycles to achieve the desired material properties and dimensional accuracy.
- Machining and Finishing: After firing, the sintered ceramic substrate may undergo additional machining and finishing processes to refine its dimensions, surface finish, and features such as mounting holes, channels, or cavities for the MEMS sensor.
- Metallization: Metal layers are deposited onto the ceramic substrate surface using techniques such as sputtering, evaporation, or plating. These metallized layers serve various purposes, such as providing electrical contacts, heat dissipation paths, or hermetic sealing barriers.
- MEMS Sensor Integration: The MEMS sensor component is assembled into the ceramic package, typically using adhesive bonding or soldering techniques. Any additional components, such as sealing lids or covers, may also be integrated at this stage.
- Testing and Quality Assurance: The completed CPMS undergoes rigorous testing to verify its performance, reliability, and conformance to specifications. This may include electrical testing, thermal cycling, vibration testing, and leak testing to ensure hermeticity.
- Packaging and Shipping: Once validated, the CPMS is packaged and prepared for shipping to customers or integration into larger systems.
Throughout the manufacturing process, strict quality control measures are implemented to ensure consistency, reliability, and repeatability of the CPMS production. Advanced manufacturing technologies and techniques may be employed to optimize process efficiency and yield while meeting stringent performance requirements.
How much should a CPMS cost?
The cost of a Ceramic Package MEMS Sensor (CPMS) can vary widely depending on several factors, including the complexity of the sensor, the materials used, manufacturing processes, volume of production, and additional features required for specific applications. Here are some factors that can influence the cost of CPMS:
- Sensor Complexity: The complexity of the MEMS sensor itself plays a significant role in determining the cost. Sensors with more advanced functionalities or requiring intricate manufacturing processes may be more expensive.
- Material Cost: The cost of ceramic materials, metallization layers, and any additional components used in the CPMS can impact its overall cost.
- Manufacturing Processes: The manufacturing processes involved in producing CPMS, such as shaping, firing, machining, and assembly, contribute to the cost. Advanced manufacturing techniques may increase production costs but can also improve quality and performance.
- Volume of Production: Economies of scale often apply in manufacturing, meaning that higher production volumes typically result in lower unit costs. Large-scale production runs can reduce per-unit costs through efficiencies in material usage, labor, and overhead expenses.
- Quality and Reliability Requirements: Meeting stringent quality and reliability standards may require additional testing, quality control measures, and higher-grade materials, which can increase costs.
- Customization and Additional Features: CPMS tailored to specific applications or requiring custom features may have higher costs due to development and setup expenses.
- Supplier and Geographic Location: The cost of CPMS can also vary based on the supplier and their geographic location. Labor costs, regulatory requirements, and local market conditions can all influence pricing.
Due to these factors, it’s challenging to provide a specific cost without detailed information about the CPMS’s specifications and production requirements. Typically, CPMS prices can range from a few dollars to several hundred dollars or more per unit, depending on the factors mentioned above. Companies interested in procuring CPMS should work closely with suppliers to obtain accurate cost estimates based on their specific needs and volume requirements.
What is CPMS base material?
The base material used for Ceramic Package MEMS Sensors (CPMS) is typically a high-performance ceramic material. Two common ceramics used for CPMS are:
- Alumina (Al2O3): Alumina is one of the most widely used ceramics for CPMS due to its excellent thermal, mechanical, and electrical properties. It offers good thermal conductivity, high mechanical strength, chemical inertness, and electrical insulation, making it suitable for a wide range of MEMS sensor applications.
- Aluminum Nitride (AlN): Aluminum nitride is another ceramic material commonly used for CPMS, especially in applications requiring enhanced thermal conductivity. AlN offers higher thermal conductivity than alumina, making it ideal for applications where heat dissipation is critical, such as high-power electronics or sensors operating in extreme temperature environments.
Both alumina and aluminum nitride are well-suited for CPMS applications due to their reliability, durability, and compatibility with MEMS sensor requirements. The choice between these materials depends on factors such as thermal management needs, cost considerations, and specific application requirements.
Which company manufactures CPMS?
CPMS (Ceramic Package MEMS Sensors) manufacturing involves highly specialized processes and technologies, so many companies have rich experience and capabilities in this field. Many well-known companies worldwide produce CPMS, including Bosch in Germany, Navitas in the United States, Epson in Japan, and Analog Devices Inc. (ADI) in the United States. These companies possess advanced technologies and facilities to design, manufacture, and supply various types of CPMS to meet the needs of different application areas.
As for our company, we also have the capability to produce CPMS. As a leading technology company, we have extensive experience and expertise in MEMS sensors and ceramic packaging. Our engineering team has deep technical backgrounds and unique capabilities in designing and manufacturing high-performance CPMS. Our manufacturing facilities are equipped with advanced equipment and processes to control the entire process from raw material processing to final assembly. We are committed to providing customized solutions to our customers, designing and manufacturing CPMS that meet their specific application requirements and specifications.
We prioritize quality and reliability, strictly adhering to quality management systems during the production process to ensure that each production step meets the highest standards. We also have professional testing and validation facilities to conduct comprehensive testing and validation of all CPMS produced to ensure their performance and reliability meet customer requirements and expectations.
In summary, our company has the capability to manufacture CPMS and is committed to providing high-quality, reliable products, and services. Whatever the customer’s needs, we can provide customized solutions to meet the specific requirements of their application areas.
Qualities of Good Customer Service
Good customer service is characterized by several key qualities that contribute to positive interactions between a business and its customers. These qualities include:
- Responsiveness: Good customer service involves promptly addressing customer inquiries, concerns, and requests. This means providing timely responses to emails, phone calls, and other forms of communication, as well as being proactive in addressing customer needs.
- Empathy: Empathy is essential in understanding and relating to customers’ emotions, concerns, and experiences. Good customer service representatives listen actively, show genuine concern for customers’ issues, and strive to find satisfactory solutions.
- Knowledgeability: Customer service representatives should be well-informed about the products or services offered by the business. They should possess comprehensive knowledge to answer customer questions accurately, provide relevant information, and offer assistance effectively.
- Professionalism: Professionalism entails maintaining a courteous and respectful demeanor when interacting with customers. This includes using appropriate language, remaining calm and composed, and demonstrating a willingness to assist customers in a polite manner.
- Flexibility: Good customer service involves being adaptable and flexible to accommodate customers’ needs and preferences. This may involve offering alternative solutions, adjusting policies when necessary, or going above and beyond to meet customers’ expectations.
- Problem-Solving Skills: Customer service representatives should possess strong problem-solving skills to effectively address customer issues and resolve conflicts. This involves analyzing situations, identifying root causes, and implementing solutions that satisfy customers while aligning with business objectives.
- Consistency: Consistency in service delivery is crucial for building trust and loyalty with customers. Good customer service ensures that customers receive a consistent level of quality and care across all interactions and touchpoints with the business.
- Personalization: Tailoring interactions to individual customer preferences and needs can greatly enhance the customer experience. Good customer service involves recognizing and acknowledging customers as individuals, remembering past interactions, and personalizing interactions whenever possible.
- Transparency: Transparency involves providing clear and honest communication with customers regarding products, services, pricing, policies, and any potential issues. Good customer service fosters trust and credibility by being transparent and upfront with customers.
- Follow-Up: Following up with customers after interactions or transactions demonstrates care and concern for their satisfaction and feedback. Good customer service includes seeking feedback, addressing any outstanding issues, and expressing appreciation for customers’ business.
Overall, good customer service is about building positive relationships with customers by meeting their needs, exceeding their expectations, and ensuring a pleasant and satisfying experience throughout their interactions with the business.
FAQs
What are CPMS?
CPMS stands for Ceramic Package MEMS Sensors. They are MEMS (Microelectromechanical Systems) sensors housed within ceramic packages to provide protection and encapsulation.
What are the advantages of CPMS?
CPMS offer several advantages, including excellent hermetic sealing, thermal stability, mechanical robustness, and electrical insulation, making them suitable for a wide range of applications in demanding environments.
What are the applications of CPMS?
CPMS find applications in various industries, including automotive, aerospace, consumer electronics, medical devices, and industrial systems. They are used for sensing physical phenomena such as acceleration, pressure, temperature, and more.
How are CPMS manufactured?
The manufacturing process for CPMS involves several steps, including material preparation, shaping, firing (sintering), metallization, assembly, and testing. This process ensures the creation of robust ceramic packages to protect MEMS sensors.
What types of ceramic materials are used in CPMS?
Common ceramic materials used in CPMS include alumina (Al2O3) and aluminum nitride (AlN). These materials offer excellent thermal, mechanical, and electrical properties suitable for MEMS sensor encapsulation.
What factors affect the cost of CPMS?
The cost of CPMS can vary based on factors such as sensor complexity, material cost, manufacturing processes, volume of production, quality requirements, customization, and geographic location of the supplier.
How do I select the right CPMS for my application?
When selecting CPMS for a specific application, consider factors such as the operating environment, performance requirements, size constraints, electrical interfaces, and budget. Consulting with CPMS manufacturers or experts can help determine the best solution for your needs.
What quality control measures are in place for CPMS?
CPMS manufacturers implement strict quality control measures throughout the manufacturing process to ensure consistency, reliability, and performance. This may include material testing, process validation, and product testing to meet industry standards and customer specifications.
Can CPMS be customized for specific applications?
Yes, CPMS can be customized to meet the specific requirements of different applications. Manufacturers offer flexibility in design, materials, features, and packaging options to tailor CPMS solutions according to customer needs.