Ceramic Package Substrate Manufacturer
Ceramic Package Substrate Manufacturer,Ceramic Package Substrate is a key component in semiconductor packaging, renowned for its exceptional thermal and mechanical properties. Composed of ceramic materials like alumina or aluminum nitride, these substrates offer superior heat dissipation and electrical insulation. Ceramic Package Substrates ensure reliable connections between integrated circuits and printed circuit boards, supporting high-performance electronic devices. Their robust construction withstands harsh operating environments, making them ideal for aerospace, automotive, and power electronics applications. With precise manufacturing processes, Ceramic Package Substrates provide a stable platform for semiconductor chips, enhancing reliability and longevity in electronic systems.
What is ceramic package substrate?
A ceramic package substrate is a type of substrate used in semiconductor packaging. It serves as a foundation for mounting and interconnecting semiconductor devices such as integrated circuits (ICs) or chips.
Ceramic package substrates offer several advantages, including excellent thermal conductivity, electrical insulation, and mechanical strength. These properties make them suitable for applications requiring high reliability and performance, such as in aerospace, automotive, telecommunications, and high-power electronics.
Ceramic package substrates can be made from various materials such as alumina (Al2O3), aluminum nitride (AlN), or silicon nitride (Si3N4). They come in different shapes and sizes, depending on the specific requirements of the semiconductor device and the application. The substrate typically contains metal traces or wiring patterns to facilitate electrical connections between the semiconductor devices and other components on the circuit board.
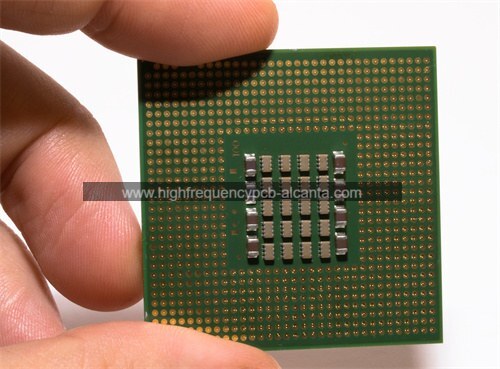
Ceramic Package Substrate Manufacturer
What are the functions of ceramic package substrate?
Ceramic package substrates serve several key functions in semiconductor packaging:
Mechanical Support: The substrate provides a sturdy mechanical foundation for mounting and securing semiconductor devices. It helps protect the delicate semiconductor components from physical damage due to handling, environmental factors, and mechanical stresses.
Electrical Interconnection: Ceramic substrates feature metal traces or wiring patterns that facilitate electrical connections between the semiconductor devices and other components on the circuit board. These connections enable the flow of electrical signals between different parts of the electronic system.
Thermal Management: Ceramic materials exhibit excellent thermal conductivity, allowing them to efficiently dissipate heat generated by the semiconductor devices during operation. This helps prevent overheating and ensures the reliable performance of the electronic system, particularly in applications with high power densities or demanding thermal environments.
Electrical Insulation: Ceramic substrates provide electrical insulation between the semiconductor devices and the surrounding environment or adjacent components. This insulation prevents electrical shorts and interference, enhancing the reliability and safety of the electronic system.
Environmental Protection: Ceramic package substrates offer resistance to moisture, chemicals, and other environmental factors that could potentially damage the semiconductor devices. This protection helps extend the lifespan of the electronic system and ensures its performance in harsh operating conditions.
Overall, ceramic package substrates play a critical role in ensuring the reliability, performance, and longevity of semiconductor devices and electronic systems in various applications.
What are the different types of ceramic package substrate?
There are several types of ceramic package substrates, each with its own unique properties and advantages. Some of the most common types include:
Alumina (Al2O3): Alumina ceramic substrates are widely used due to their excellent thermal conductivity, electrical insulation properties, and mechanical strength. They are suitable for various applications, including high-frequency circuits, power electronics, and LED packaging.
Aluminum Nitride (AlN): Aluminum nitride ceramic substrates offer superior thermal conductivity compared to alumina, making them particularly well-suited for high-power and high-frequency applications. They also exhibit good electrical insulation properties and excellent thermal stability.
Silicon Nitride (Si3N4): Silicon nitride ceramic substrates feature high thermal shock resistance and thermal conductivity, along with good mechanical strength. They are often used in demanding applications such as automotive electronics, power modules, and aerospace systems.
Beryllium Oxide (BeO): Beryllium oxide ceramic substrates possess extremely high thermal conductivity, making them ideal for applications requiring efficient heat dissipation, such as high-power RF amplifiers and laser diode packaging. However, beryllium oxide poses health risks due to its toxicity, so appropriate precautions must be taken during manufacturing and handling.
Titanate Ceramics: Titanate ceramics, such as barium titanate (BaTiO3) and lead zirconate titanate (PZT), exhibit piezoelectric properties and are used primarily in electronic components such as sensors, actuators, and transducers.
These are just a few examples of ceramic package substrates, and there are other specialized formulations and compositions available to meet specific requirements for different applications. The choice of substrate type depends on factors such as thermal management needs, electrical performance requirements, mechanical properties, and cost considerations.
What is the relationship between ceramic package substrate and IC packaging?
Ceramic package substrates are an integral part of IC (integrated circuit) packaging. IC packaging involves enclosing semiconductor chips or dies within protective casings and providing electrical connections to external circuitry. Ceramic package substrates serve as the foundation upon which the semiconductor devices are mounted and interconnected within the package.
Here’s the relationship between ceramic package substrates and IC packaging:
Mounting Surface: Ceramic package substrates provide a flat, stable surface for mounting semiconductor chips or dies. These chips contain the actual integrated circuits, fabricated with transistors, resistors, and other electronic components.
Electrical Interconnection: Ceramic substrates feature metal traces or wiring patterns that facilitate electrical connections between the semiconductor devices and other components within the package, such as lead frames or bond wires. These connections allow the integrated circuits to communicate with external circuitry and perform their intended functions.
Thermal Management: Ceramic package substrates play a crucial role in managing heat generated by the integrated circuits during operation. The high thermal conductivity of ceramic materials helps dissipate heat efficiently, preventing overheating and ensuring the reliable performance of the semiconductor devices.
Environmental Protection: Ceramic package substrates provide a protective enclosure for the semiconductor devices, shielding them from moisture, contaminants, and mechanical stresses. This protection helps extend the lifespan of the integrated circuits and ensures their performance in various operating conditions.
Overall, ceramic package substrates are essential components of IC packaging, providing mechanical support, electrical connectivity, thermal management, and environmental protection for semiconductor devices. The choice of substrate material and packaging design depends on factors such as the specific requirements of the application, thermal performance needs, and cost considerations.
How does ceramic package substrate differ from PCB?
Ceramic package substrates and printed circuit boards (PCBs) serve different but complementary roles in electronic systems. Here are some key differences between the two:
Material Composition:
Ceramic Package Substrate: Ceramic substrates are typically made from materials such as alumina (Al2O3), aluminum nitride (AlN), silicon nitride (Si3N4), or beryllium oxide (BeO). These materials offer excellent thermal conductivity, electrical insulation, and mechanical strength.
PCB: PCBs are typically made from non-conductive substrate materials such as fiberglass-reinforced epoxy (FR-4) or polyimide. They feature conductive traces made of copper that are etched onto the substrate to provide electrical connections between components.
Application:
Ceramic Package Substrate: Ceramic substrates are primarily used in semiconductor packaging to mount and interconnect semiconductor devices such as integrated circuits (ICs) or chips. They are often used in high-reliability applications where thermal management and electrical performance are critical.
PCB: PCBs are used to provide mechanical support and electrical connections for various electronic components, including ICs, resistors, capacitors, and connectors. They are used in a wide range of electronic devices, from consumer electronics to industrial equipment.
Thermal Management:
Ceramic Package Substrate: Ceramic substrates offer superior thermal conductivity compared to traditional PCB materials, making them well-suited for applications requiring efficient heat dissipation, such as high-power electronics or RF modules.
PCB: PCBs can dissipate some heat, but their thermal conductivity is generally lower than that of ceramic substrates. Additional thermal management techniques, such as heat sinks or thermal vias, may be employed to improve heat dissipation in PCB-based systems.
Complexity and Cost:
Ceramic Package Substrate: Ceramic substrates are often more expensive and difficult to manufacture compared to PCBs, especially for complex designs or custom configurations. However, they offer superior performance in terms of thermal conductivity and reliability.
PCB: PCBs are typically more cost-effective and easier to manufacture in large volumes. They can accommodate complex layouts and are well-suited for high-density interconnects and multilayer designs.
In summary, ceramic package substrates and PCBs serve different functions within electronic systems, with ceramic substrates being specialized components primarily used in semiconductor packaging for high-performance applications, while PCBs provide the foundation for interconnecting various electronic components in a wide range of devices.
What are the structure and production technology of ceramic package substrate?
The structure and production technology of ceramic package substrates can vary depending on the specific material used and the requirements of the application. However, here is a general overview of the structure and production process:
Structure:
Ceramic package substrates typically consist of a ceramic material base, which serves as the foundation for mounting semiconductor devices, along with metal traces or wiring patterns for electrical connections.
The ceramic base is usually a thin, flat substrate with a smooth surface, providing a stable mounting platform for the semiconductor chips.
Metal traces or wiring patterns are deposited onto the ceramic substrate using various techniques such as screen printing, thin-film deposition, or thick-film deposition. These traces provide the necessary electrical connections between the semiconductor devices and other components on the circuit board.
Production Technology:
Substrate Fabrication: The production process begins with the fabrication of the ceramic substrate. This involves mixing raw ceramic powders with binders and additives to form a slurry, which is then cast or pressed into the desired shape and size. The green ceramic substrate is then sintered at high temperatures to densify the material and form the final ceramic substrate.
Metallization: After the ceramic substrate is formed, metal traces or wiring patterns are applied to the surface using metallization techniques. This can involve screen printing conductive inks, sputtering or evaporation of metal films, or other deposition methods. These metal traces provide the electrical connections for the semiconductor devices.
Die Attach and Wire Bonding: Once the substrate is metallized, semiconductor chips or dies are attached to the substrate using die attach materials such as epoxy or solder. Wire bonding techniques are then used to make electrical connections between the semiconductor chips and the metal traces on the substrate.
Encapsulation: In some cases, the assembled substrate may be encapsulated with a protective material such as epoxy resin to provide additional environmental protection and mechanical stability.
Testing and Inspection: After assembly, the ceramic package substrates undergo testing and inspection to ensure proper functionality and quality. This may include electrical testing, visual inspection, and other quality control measures.
Overall, the production of ceramic package substrates involves several steps, including substrate fabrication, metallization, die attach, wire bonding, encapsulation, and testing, to create high-performance electronic components suitable for a wide range of applications.
Frequently Asked Questions (FAQs)
What is a ceramic package substrate?
A ceramic package substrate is a type of substrate used in semiconductor packaging. It provides a foundation for mounting and interconnecting semiconductor devices such as integrated circuits (ICs) or chips.
What are the advantages of ceramic package substrates?
Ceramic package substrates offer excellent thermal conductivity, electrical insulation, and mechanical strength. They are suitable for high-reliability applications and provide efficient heat dissipation, making them ideal for use in power electronics, RF modules, and other demanding environments.
What materials are used to make ceramic package substrates?
Ceramic package substrates can be made from materials such as alumina (Al2O3), aluminum nitride (AlN), silicon nitride (Si3N4), or beryllium oxide (BeO). Each material offers different properties and advantages depending on the specific requirements of the application.
How are ceramic package substrates manufactured?
The manufacturing process for ceramic package substrates typically involves substrate fabrication, metallization, die attach, wire bonding, encapsulation, and testing. This process includes steps such as forming the ceramic substrate, depositing metal traces or wiring patterns, attaching semiconductor chips, making electrical connections, encapsulating the assembly, and testing for functionality and quality.
What are the differences between ceramic package substrates and PCBs?
Ceramic package substrates are specialized components used primarily in semiconductor packaging for high-performance applications, whereas PCBs provide the foundation for interconnecting various electronic components in a wide range of devices. Ceramic substrates offer superior thermal conductivity and reliability compared to traditional PCB materials but are often more expensive to manufacture.
What are the applications of ceramic package substrates?
Ceramic package substrates are used in a variety of applications, including power electronics, RF modules, LED packaging, automotive electronics, aerospace systems, and high-reliability industrial equipment. They are particularly well-suited for applications requiring efficient heat dissipation, electrical insulation, and mechanical stability.
Conclusion
In conclusion, ceramic package substrates play a crucial role in semiconductor packaging, providing a robust foundation for mounting and interconnecting semiconductor devices such as integrated circuits (ICs) or chips. They offer several advantages, including excellent thermal conductivity, electrical insulation, and mechanical strength, making them ideal for high-reliability applications in industries such as power electronics, RF modules, LED packaging, automotive electronics, aerospace systems, and more.
The production process for ceramic package substrates involves several steps, including substrate fabrication, metallization, die attach, wire bonding, encapsulation, and testing. These substrates are made from materials such as alumina, aluminum nitride, silicon nitride, or beryllium oxide, each offering unique properties suited to different application requirements.
Compared to printed circuit boards (PCBs), ceramic package substrates provide superior thermal conductivity and reliability but may be more expensive to manufacture. However, their performance benefits make them indispensable for applications demanding efficient heat dissipation, electrical insulation, and mechanical stability.
Overall, ceramic package substrates contribute significantly to the reliability, performance, and longevity of electronic systems in a wide range of industries, making them essential components in modern semiconductor packaging technology.