Cavity Substrate/PCB Manufacturer
Cavity Substrate/PCB Manufacturer,Cavity Substrate/PCB incorporates recessed areas within the board to accommodate components, offering a compact and efficient design solution. This allows for lower profile assemblies and optimal space utilization, essential for modern electronic devices. The cavities provide protection for sensitive components and enhance thermal management by enabling direct placement of heat sinks. Typically used in high-performance applications like telecommunications, automotive, and aerospace, Cavity Substrate/PCB manufacturing involves precise milling or etching processes. This technology supports advanced miniaturization and integration, meeting the stringent requirements for performance, reliability, and space efficiency in cutting-edge electronics.
A Printed Circuit Board (PCB) stands as a pivotal electronic device component. Constructed from insulating material, typically fiberglass-reinforced epoxy, it establishes support and connectivity for electronic components via etched conductive pathways on copper sheets. This board forms a robust base for integrating diverse electronic elements like resistors, capacitors, and integrated circuits.
On the other hand, “Cavity Substrate” denotes a specialized PCB variant featuring deliberate recesses or cavities. These recessed areas serve varied functions, ranging from accommodating specific components to facilitating heat dissipation or incorporating other design elements of the device.
In essence, a Cavity Substrate or PCB with cavities represents a circuit board designed with intentional recessed regions to cater to specific needs in electronic device manufacturing. These recesses contribute to elevating the functionality, performance, or form factor of the electronic system.
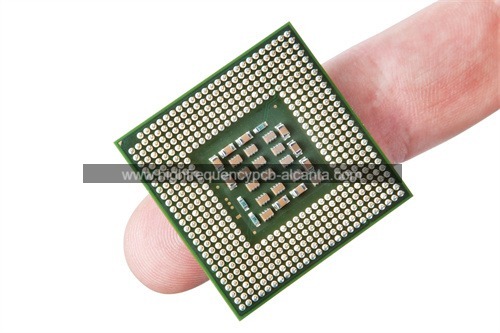
Cavity Substrate/PCB Manufacturer
What are the Functions of Cavity Substrate?
Cavity Substrates exhibit a myriad of functionalities within electronic devices, introducing features that significantly impact their performance, efficiency, and aesthetics. Let’s delve into the diverse roles they play:
Tailored Component Shelter: Cavity Substrates are designed with precision, incorporating recessed areas to securely host specific electronic components. This meticulous arrangement ensures the safeguarding and optimal functionality of sensitive elements.
Heat Harmony: Strategically engineered cavities facilitate efficient heat dissipation. This is particularly crucial for electronic components prone to generating heat during operation, preventing overheating and maintaining an ideal thermal environment.
Interference Mitigation Mastery: By isolating certain components in dedicated cavities, these substrates act as shields, minimizing electromagnetic interference (EMI) and radio frequency interference (RFI). This meticulous approach enhances the overall electromagnetic compatibility of the device.
Elevated Signal Integrity: Cavity Substrates contribute to heightened signal integrity by providing controlled environments for specific components. This plays a vital role in reducing crosstalk and minimizing signal noise for enhanced overall performance.
Space Efficiency Symphony: The integration of recessed areas unleashes space optimization on the PCB, allowing for a more compact and streamlined design. This proves invaluable, especially in applications where spatial constraints are a critical consideration.
Design Artistry Unleashed: The existence of cavities provides designers with a canvas for creativity and innovation. It allows for the thoughtful and purposeful integration of components, contributing to the uniqueness and functionality of the electronic device.
Aesthetic Panache: Beyond functionality, Cavity Substrates add an aesthetic dimension to electronic devices. Carefully crafted recessed areas can enhance the visual appeal, contributing to the overall attractiveness of the product.
Structural Symphony: Cavities can be engineered not just for electronic considerations but also to provide mechanical support and structural reinforcement. This enhances the robustness and durability of the electronic device.
In essence, Cavity Substrates transcend mere circuit connectivity, assuming a pivotal role in component protection, thermal equilibrium, interference reduction, and the overall optimization of electronic device design with an artistic touch.
What are the Different Types of Cavity Substrate?
The world of electronic device manufacturing is enriched with a diverse array of Cavity Substrates, each meticulously crafted to address specific demands. Let’s navigate through this array:
Metal Core Cavity Substrate (MCPCB): Sporting a sturdy metal core, typically aluminum, MCPCBs shine in dissipating heat efficiently. They find their calling in applications where precise thermal management is crucial, such as in LED lighting and power electronics.
Ceramic Cavity Substrate: Revered for superior thermal conductivity and electrical insulation, ceramic substrates carve a niche in high-power applications, microwave devices, and electronic modules seeking the delicate equilibrium of heat dissipation and electrical isolation.
Flex Cavity Substrate: Unveiling flexibility, these substrates are pliable circuit boards with recessed areas. Ideal for applications demanding adaptability, from wearable devices to surfaces with curves.
RF Cavity Substrate: Engineered for precision in radio frequency (RF) applications, these substrates minimize signal loss and interference. Common in communication devices, radar systems, and various wireless applications.
Embedded Component Cavity Substrate: Seamlessly integrating components into the substrate, this type results in a compact and space-efficient design. A go-to choice for miniaturized electronic devices.
Multilayer Cavity Substrate: Layered intricately with strategically placed recesses, these substrates elevate functionality, making them suitable for intricate electronic systems.
Metal Backed Cavity Substrate: Echoing MCPCBs, metal-backed substrates efficiently dissipate heat. They prove valuable in applications requiring a fusion of structural support and thermal management.
High-Frequency Cavity Substrate: Crafted for the demands of high-frequency applications, these substrates uphold signal integrity and minimize signal loss. Widely used in telecommunications and high-frequency electronic devices.
Hybrid Cavity Substrate: Blending diverse materials and technologies, hybrid cavity substrates offer a versatile solution for applications with varied requirements. They strike a harmonious balance between thermal performance, electrical properties, and structural support.
These examples illustrate the expansive landscape of choices available. The selection of a Cavity Substrate hinges on the nuanced requirements of the device, encompassing considerations of thermal characteristics, flexibility, RF performance, and overall design intricacies.
What is the Relationship Between Cavity Substrate and IC Packaging?
Cavity Substrates and Integrated Circuit (IC) packaging share a symbiotic relationship in the intricate landscape of electronic device creation. Let’s delve into the interconnected roles they play:
Harmonious Component Integration: Both Cavity Substrates and IC packaging contribute to the integration of electronic components. IC packaging encapsulates semiconductor elements within a protective housing, while Cavity Substrates offer a platform on the printed circuit board (PCB) for the amalgamation of diverse components.
Thermal Symphony: Addressing thermal concerns is a common goal. IC packaging incorporates features for effective heat dissipation, and Cavity Substrates, particularly those with metal cores, are designed to efficiently manage heat emanating from electronic components.
Spatial Optimization Ballet: Both entities dance to the rhythm of space optimization. IC packaging strives for a compact enclosure for semiconductor components, and Cavity Substrates, featuring recessed areas, facilitate space efficiency, especially when accommodating specific components.
Signal Integrity Sonata: The duet of Cavity Substrates and IC packaging influences signal integrity. IC packaging shields semiconductor components from external factors affecting signal quality, while Cavity Substrates contribute to mitigating crosstalk and signal noise on the PCB.
Tailored Design Elegance: The synergy between Cavity Substrates and IC packaging provides designers with a canvas for customization and design flexibility. Designers can select specific IC packages and seamlessly integrate them into Cavity Substrates, aligning with the unique requirements of the device.
EMC Pas de Deux: Both contribute to the electromagnetic compatibility (EMC) choreography. IC packaging often includes shielding against electromagnetic interference (EMI), and Cavity Substrates, through component isolation, play a role in diminishing EMI on the PCB.
Mechanical Support Waltz: While IC packaging lends physical protection to semiconductor components, certain Cavity Substrates, especially those with metal backing, offer an additional layer of mechanical support, enriching the structural integrity of the electronic device.
In essence, Cavity Substrates and IC packaging perform a synchronized dance in the expansive world of electronic device design and production. They collaborate seamlessly to integrate components, manage heat, optimize space, ensure signal integrity, uphold EMC standards, and provide the necessary mechanical support for a harmonious electronic symphony. The selection and configuration of these components are intricately woven into the unique requirements and constraints of each device.
What are the Differences Between Cavity Substrate and Traditional PCBs?
Cavity Substrates and traditional Printed Circuit Boards (PCBs) diverge in their design philosophy, functionalities, and applications. Let’s navigate through the distinctive features that set them apart:
Design Elegance:
Cavity Substrates: Embrace intentional recessed areas or cavities strategically embedded within the board design. This thoughtful design allows for the accommodation of specific components and facilitates efficient heat dissipation.
Traditional PCBs: Adhere to a more straightforward design with a flat and uniform surface, lacking intentional recesses or cavities.
Thermal Management Embrace:
Cavity Substrates: Engineered with a focus on sophisticated heat dissipation, particularly evident in designs featuring metal cores and specialized materials crafted for optimal thermal regulation.
Traditional PCBs: While competent in heat management, they may lack the specialized features dedicated to thermal regulation found in certain Cavity Substrate designs.
Component Integration Ballet:
Cavity Substrates: Act as a versatile stage for the integration of electronic components. Some variants even allow for the embedding of components directly within the carefully designed cavities.
Traditional PCBs: Present a flat surface optimized for the conventional placement and interconnection of electronic components.
Space Optimization Symphony:
Cavity Substrates: Excel in space optimization by strategically incorporating recessed areas. This deliberate design choice allows for an efficient arrangement of components, contributing to an overall compact and purposeful design.
Traditional PCBs: Components are typically arranged on a flat surface without the intentional use of recesses, which may result in a less space-optimized design.
Applications Focus Spotlight:
Cavity Substrates: Shine in applications where thermal management, specialized component housing, and space optimization take center stage. Commonly found in high-power electronics, LED lighting, and devices with specific design requirements.
Traditional PCBs: Serve as versatile workhorses, catering to a broad spectrum of electronic devices. Their simplicity makes them suitable for applications with standard design needs.
Flexibility Performance:
Cavity Substrates: Certain variants, like Flex Cavity Substrates, take center stage by offering flexibility. This makes them a fitting choice for applications with curved surfaces or where flexibility is a paramount consideration.
Traditional PCBs: Generally embrace rigidity, although flexible PCB options exist for specific applications.
Cost Choreography:
Cavity Substrates: Navigate a landscape involving additional manufacturing intricacies and specialized materials, potentially leading to higher production costs compared to the generally cost-effective traditional PCBs.
Traditional PCBs: Dance in the realm of economic viability, especially for standard electronic applications without the need for specific cavity-related features.
In essence, Cavity Substrates showcase intentional design sophistication and specialized features, making them stars in specific applications. Traditional PCBs, in contrast, maintain versatility and cost-effectiveness, playing a role across a broad spectrum of electronic devices with standard design requisites. The choice between them is a nuanced decision guided by the specific requirements of the electronic system in development.
What is the Main Structure and Production Technology of Cavity Substrate?
Cavity Substrates showcase a captivating blend of intricate structure and advanced production processes, with variations dependent on the specific type of substrate. Let’s embark on a journey through the fundamental elements:
Main Structural Symphony:
Base Material Ballet:
At the core lies the choice of base material, a pivotal decision that includes options such as:
Metal Core: Often crafted from aluminum or copper, champions thermal conductivity.
Ceramic: Revered for its superior thermal properties and electrical insulation.
Flex Material: Embracing flexibility with materials like polyimide for substrates that gracefully bend to the application’s needs.
Dielectric Layer Waltz:
A graceful dielectric layer dances onto the base material, a crucial performer that orchestrates insulation, shielding conductive traces and components from the risk of short circuits.
Conductive Traces Choreography:
Etched or printed with precision, conductive traces perform a choreography, weaving intricate pathways that connect components and conduct the symphony of electric current.
Cavities or Recessed Areas Pas de Deux:
The hallmark feature unfolds with intentional cavities or recessed areas, engaging in a pas de deux, strategically designed to either cradle specific components or offer a stage for the graceful dissipation of heat.
Solder Mask Interlude:
An interlude introduces a protective solder mask layer, shielding conductive traces from potential solder bridges during the grand assembly of components and adding an extra layer of visual elegance.
Surface Finish Finale:
The grand finale arrives with various surface finishes, be it the classic HASL, the regal ENIG, or the subtle OSP, each contributing to the final touch, enhancing solderability, and crowning exposed metal surfaces with a regal finish.
Production Technology Ballet:
Substrate Preparation Prelude:
The symphony unfolds with the preparation of the substrate’s stage, involving meticulous selection and preparation of the chosen base material, setting the tone for the grand performance.
Circuit Design and Etching Overture:
The overture introduces a meticulous dance of circuit design using computer-aided design (CAD) tools, followed by the delicate etching or printing of conductive traces onto the substrate—a performance that crafts the desired circuit pattern.
Cavity Formation Pas de Trois:
Uniquely for Cavity Substrates, a pas de trois emerges with the formation of recessed areas. Techniques such as milling, drilling, or the ethereal touch of laser ablation come into play, aligning with substrate material and design intricacies.
Dielectric Layer and Additional Layers Crescendo:
A crescendo unfolds with the application of a dielectric layer, offering insulation. Additional layers, including the solder mask and surface finish, join the symphony, enhancing protection and functionality.
Component Assembly Sonata:
Electronic components take center stage, participating in a sonata as they find their place on the substrate. In some instances, components become integral parts of the composition, embedded directly into the intricately designed cavities.
Quality Control and Testing Crescendo:
A crescendo of quality control and testing ensues—a meticulous inspection involving visual examinations and electrical tests to ensure the structural harmony and functional brilliance of the Cavity Substrate.
Surface Mount Technology (SMT) Crescendo:
The grand crescendo is enhanced with the sophisticated Surface Mount Technology (SMT), a technical marvel that enables the precise placement of miniature components directly onto the substrate’s surface.
Final Inspection and Packaging Coda:
The masterpiece concludes with a coda, a final inspection ensuring that the end product resonates with perfection before gracefully moving into the packaging phase, prepared for its integration into electronic devices.
It’s important to acknowledge that the specific production techniques may vary based on the unique characteristics of the Cavity Substrate and its designated application. The outlined steps offer a nuanced perspective on the intricate processes involved in the manufacturing ballet of Cavity Substrates.
Frequently Asked Questions (FAQs)
What Role Does a Cavity Substrate Manufacturer Play?
Answer: A Cavity Substrate manufacturer specializes in the creation of PCBs featuring intentional cavities. Their responsibilities include designing, fabricating, and assembling these substrates to meet the unique requirements of electronic devices.
Which Industries Commonly Utilize Cavity Substrates?
Answer: Cavity Substrates find applications in industries that prioritize efficient thermal management and specialized component housing. These industries include high-power electronics, LED lighting, automotive electronics, and telecommunications.
What Materials are Employed in Cavity Substrate Manufacturing?
Answer: Cavity Substrates utilize diverse base materials, such as metal cores (aluminum or copper), ceramics, or flexible materials like polyimide for substrates requiring flexibility.
How are Cavities Formed in Cavity Substrates?
Answer: Precision techniques like milling, drilling, or laser ablation are employed to create cavities in Cavity Substrates. The chosen method depends on the substrate material and specific design criteria.
Why is Thermal Management Essential in Cavity Substrates?
Answer: Thermal management is critical in Cavity Substrates, particularly those with metal cores. The designed cavities and specialized materials help dissipate heat effectively, preventing overheating of electronic components.
Can Cavity Substrates be Applied in Flexible Electronics?
Answer: Yes, certain variations known as Flex Cavity Substrates are specifically crafted for flexible electronics. They offer the advantages of both cavity design and flexibility.
How Do Cavity Substrate Manufacturers Ensure Quality Control?
Answer: Quality control involves visual inspections, electrical testing, and adherence to industry standards. Checks for solderability, component placement accuracy, and overall structural integrity are integral to the process.
Are Cavity Substrates More Costly Than Traditional PCBs?
Answer: Cavity Substrates may entail additional manufacturing steps and materials, potentially resulting in higher production costs compared to traditional PCBs. The cost variation depends on the specific substrate requirements.
Conclusion
In conclusion, Cavity Substrates stand out as a specialized and forward-thinking category within the domain of printed circuit boards (PCBs). Their deliberate integration of recessed areas or cavities brings forth a multitude of advantages, ranging from efficient thermal management to the personalized accommodation of components. As we navigate the intricacies of Cavity Substrate manufacturing, it becomes evident that these substrates cater to industries and applications where precision, thermal regulation, and spatial optimization play a pivotal role.
Manufacturers specializing in Cavity Substrates play a central role in orchestrating the intricate dance of materials and processes. From the careful selection of base materials to the precise execution of cavity creation, their expertise ensures the seamless integration of these substrates into electronic devices. The emphasis on quality control, adherence to industry standards, and the ability to meet customization requirements sets reputable manufacturers apart in this specialized field.
As electronic devices evolve and demand more sophisticated designs, Cavity Substrates position themselves as crucial components addressing these evolving needs. The interplay of materials, the choreography of cavities, and the orchestration of thermal management collectively contribute to the success of these substrates across diverse industries, from high-power electronics to automotive applications.
In the dynamic landscape of electronics, the decision between Cavity Substrates and traditional PCBs becomes nuanced. While Cavity Substrates exhibit intentional design sophistication and specialized features, traditional PCBs maintain their versatility and cost-effectiveness, playing complementary roles across various electronic devices.
In essence, Cavity Substrates embody a harmonious fusion of aesthetics and functionality, providing tailored solutions for electronic systems with specific design requisites. As technology advances, the role of Cavity Substrates is poised to expand, facilitating the seamless integration of electronics into our daily lives with finesse.