Cavity Substrate| Package Substrate Manufacturing
Cavity Substrate| Package Substrate Manufacturing,Cavity substrates are integral components in the realm of microwave and radio frequency (RF) engineering, serving as the foundation for a wide array of devices such as filters, resonators, and antennas. These substrates are engineered materials typically composed of dielectrics like ceramics or specialty polymers, meticulously designed to facilitate the formation of resonant cavities within their structure. Through precise manufacturing processes involving etching, metallization, and dielectric deposition, cavity substrates enable the manipulation of electromagnetic signals within specific frequency ranges. Their high electrical performance, thermal stability, and mechanical resilience make them indispensable in demanding applications where reliability and precision are paramount. Cavity substrates can be customized to meet diverse design requirements, offering flexibility and versatility to engineers and designers aiming to optimize the performance of their RF systems. In essence, cavity substrates are the building blocks upon which the intricate network of modern microwave and RF technologies thrives, powering communication systems, wireless devices, and beyond.
What is a Cavity Substrate?
A cavity substrate typically refers to a material or structure used in the construction of microwave or radio frequency (RF) components such as filters, resonators, and antennas.
In the context of microwave engineering, a cavity substrate often refers to a dielectric material that is used to form resonant cavities within the structure of a device. These cavities are designed to resonate at specific frequencies, allowing the device to selectively filter or amplify signals within that frequency range.
Cavity substrates are often chosen for their electrical properties, such as dielectric constant, loss tangent, and temperature stability, which can significantly impact the performance of the microwave or RF device. Examples of materials commonly used as cavity substrates include ceramic materials like alumina (Al2O3), aluminum nitride (AlN), or specialty polymer materials.
In summary, a cavity substrate is a material used in microwave or RF devices to create resonant cavities that enable the manipulation of electromagnetic signals within a specific frequency range.
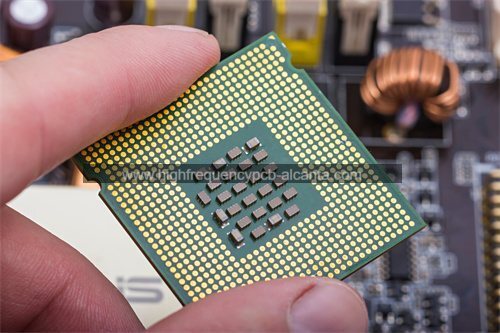
Cavity Substrate| Package Substrate Manufacturing
What are the Cavity Substrate Design Guidelines?
Designing with cavity substrates involves various considerations to ensure optimal performance of microwave or RF components. Here are some general guidelines:
- Material Selection: Choose a substrate material with appropriate dielectric properties for the desired frequency range and application. Consider factors such as dielectric constant, loss tangent, thermal stability, and manufacturability.
- Cavity Geometry: Design the cavity dimensions according to the desired resonant frequency and bandwidth. The geometry of the cavity, including its length, width, and depth, will affect its resonant properties.
- Grounding and Shielding: Ensure proper grounding and shielding to minimize electromagnetic interference and crosstalk. Proper grounding techniques, such as using via fences or solid ground planes, are essential for maintaining signal integrity.
- Feed Structure: Design an appropriate feed structure to couple the signal into and out of the cavity. This may involve the use of transmission lines, waveguides, or other coupling mechanisms tailored to the specific application.
- Tuning and Matching: Fine-tune the cavity dimensions and coupling structures to achieve the desired frequency response and impedance matching. This may involve iterative simulations or measurements to optimize performance.
- Thermal Management: Consider thermal management strategies to ensure stable performance over temperature variations. Proper substrate material selection and heat dissipation mechanisms may be necessary for high-power applications or environments with temperature fluctuations.
- Manufacturability: Design the cavity substrate with manufacturability in mind, considering factors such as fabrication techniques, tolerances, and scalability for mass production.
- Testing and Characterization: Perform thorough testing and characterization of the fabricated cavity substrate to verify its performance against design specifications. This may involve various measurement techniques, such as S-parameter measurements or resonant frequency analysis.
By following these guidelines and iterating through design, simulation, fabrication, and testing stages, engineers can develop cavity substrates that meet the performance requirements of their microwave or RF components.
What is the Cavity Substrate Fabrication Process?
The fabrication process for cavity substrates involves several steps, depending on the specific material and design requirements. Here is a general overview of the fabrication process:
- Material Preparation: The first step is to prepare the substrate material according to the desired specifications. This may involve cutting the material into the appropriate size and shape using techniques such as sawing, laser cutting, or machining.
- Surface Preparation: Next, the surfaces of the substrate material are prepared for further processing. This typically involves cleaning the surfaces to remove any contaminants or residues that could affect subsequent steps.
- Pattern Transfer: If the cavity substrate requires the formation of specific patterns or features, such as resonant cavities or feed structures, a pattern transfer step is performed. This can be accomplished through techniques such as photolithography, where a photoresist layer is deposited onto the substrate, exposed to a patterned mask, and developed to transfer the desired pattern onto the substrate surface.
- Etching: After pattern transfer, the substrate material may undergo etching to remove material selectively and define the desired features. Wet chemical etching or dry etching techniques such as reactive ion etching (RIE) may be employed depending on the material and design requirements.
- Metallization: In many cases, cavity substrates require metallization to form conductive traces, pads, or ground planes. This is typically achieved through processes such as sputtering, evaporation, or electroplating, where a thin layer of metal is deposited onto the substrate surface.
- Dielectric Deposition: For certain applications, additional dielectric layers may be deposited onto the substrate to provide insulation or impedance control. Techniques such as chemical vapor deposition (CVD) or physical vapor deposition (PVD) can be used to deposit dielectric materials onto the substrate surface.
- Surface Finishing: Once the desired features and metallization layers are in place, the substrate may undergo surface finishing processes to improve its properties or appearance. This may include techniques such as polishing, lapping, or coating with protective layers.
- Quality Control and Testing: Throughout the fabrication process, quality control measures are implemented to ensure that the substrate meets the desired specifications. This may involve visual inspection, dimensional measurements, and electrical testing to verify the integrity and performance of the fabricated substrate.
By following these fabrication steps, engineers can produce cavity substrates with the necessary features and properties to meet the requirements of various microwave or RF components.
How do you manufacture a Cavity Substrate?
Manufacturing a cavity substrate involves several steps, each crucial for producing a substrate that meets the desired specifications. Below is a general outline of the manufacturing process:
- Material Selection: Choose the appropriate substrate material based on the required electrical, mechanical, and thermal properties. Common materials include ceramics like alumina (Al2O3), aluminum nitride (AlN), or specialty polymer materials.
- Material Preparation: Prepare the substrate material in the form required for further processing. This may involve cutting, shaping, or molding the material into the desired size and shape using techniques such as sawing, laser cutting, or machining.
- Surface Preparation: Clean and prepare the surfaces of the substrate material to ensure proper adhesion and uniformity in subsequent processing steps. Surface cleaning may involve solvent cleaning, plasma treatment, or other surface modification techniques.
- Pattern Transfer: Transfer the desired pattern onto the substrate surface. This can be achieved through techniques such as photolithography, where a photoresist layer is deposited, exposed to a patterned mask, and developed to transfer the pattern onto the substrate.
- Etching: Etch away material selectively to define the desired features on the substrate surface. This may involve wet chemical etching or dry etching techniques such as reactive ion etching (RIE) to remove material and create cavities, channels, or other structures.
- Metallization: Deposit metal layers onto the substrate surface to form conductive traces, pads, or ground planes. This can be accomplished using techniques such as sputtering, evaporation, or electroplating to deposit thin layers of metal onto the substrate.
- Dielectric Deposition: Deposit dielectric layers onto the substrate surface to provide insulation or impedance control. This can be done using techniques such as chemical vapor deposition (CVD) or physical vapor deposition (PVD) to deposit dielectric materials onto the substrate.
- Surface Finishing: Finish the substrate surface to improve its properties or appearance. This may include polishing, lapping, or coating the surface with protective layers to enhance durability and performance.
- Quality Control and Testing: Throughout the manufacturing process, implement quality control measures to ensure that the substrate meets the desired specifications. This may involve visual inspection, dimensional measurements, and electrical testing to verify the integrity and performance of the manufactured substrate.
- Packaging and Shipping: Once manufactured and tested, package the cavity substrates appropriately for shipment to customers or assembly into larger electronic systems.
By following these manufacturing steps, engineers can produce cavity substrates with the necessary features and properties to meet the requirements of various microwave or RF components.
How much should a Cavity Substrate cost?
The cost of a cavity substrate can vary widely depending on several factors, including:
- Material: The type of material used for the substrate can greatly impact its cost. High-performance materials like alumina (Al2O3) or aluminum nitride (AlN) tend to be more expensive than standard PCB materials due to their superior electrical properties and manufacturing complexity.
- Size and Complexity: The size and complexity of the substrate, including the number of cavities, features, and layers, will affect the manufacturing time and material usage, thereby influencing the overall cost.
- Manufacturing Process: The chosen manufacturing process and techniques, such as photolithography, etching, metallization, and surface finishing, can impact the cost. More complex processes or specialized equipment may increase manufacturing costs.
- Volume: The volume of substrates being produced can also influence the cost. Higher volumes typically result in economies of scale and lower per-unit costs due to efficiencies in manufacturing and material procurement.
- Customization: Customized features or specific requirements may incur additional costs for design, tooling, and setup.
- Quality Standards: Meeting certain quality standards or certifications may add to the cost, as additional testing and quality control measures may be required.
- Supplier and Location: The choice of supplier and their location can affect costs due to differences in labor costs, overhead expenses, and shipping fees.
Given these variables, it’s challenging to provide a specific cost without knowing the details of the substrate’s specifications, materials, volume, and manufacturing process. However, for a rough estimate, cavity substrates can range from a few dollars for simple, small-scale designs to hundreds or even thousands of dollars for complex, high-performance substrates used in specialized applications. It’s recommended to obtain quotes from multiple suppliers based on your specific requirements to determine the cost of cavity substrates for your project.
What is Cavity Substrate base material?
The base material of a cavity substrate can vary depending on the specific application and performance requirements. Common materials used as base materials for cavity substrates include:
- Ceramics: Ceramics such as alumina (Al2O3) and aluminum nitride (AlN) are popular choices for cavity substrates due to their excellent electrical properties, high thermal conductivity, and mechanical strength. These materials are often used in high-frequency and high-power applications where stability and reliability are crucial.
- Polymers: Certain polymers, such as liquid crystal polymers (LCPs) and polytetrafluoroethylene (PTFE or Teflon), can be used as base materials for cavity substrates. These materials offer advantages such as low cost, flexibility, and ease of processing. However, they may have lower electrical performance compared to ceramics.
- Metal Alloys: Metal alloys such as Kovar or stainless steel can also be used as base materials for cavity substrates, particularly in applications where high mechanical strength and hermetic sealing are required. Metal substrates are often used in packages for integrated circuits (ICs) and microwave modules.
- Composite Materials: Composite materials, which combine different materials such as ceramics, polymers, and metals, can be tailored to achieve specific performance requirements. For example, a composite substrate may combine the electrical properties of ceramics with the mechanical flexibility of polymers.
- Glass: Certain types of glass can be used as base materials for cavity substrates, particularly in applications requiring optical transparency or specialized thermal properties.
The choice of base material depends on factors such as frequency range, power handling capability, thermal management requirements, mechanical stability, and cost considerations. Engineers select the most suitable base material based on the specific needs of the application and desired performance characteristics of the cavity substrate.
Which company makes Cavity Substrates?
There are many companies that manufacture cavity substrates, including internationally renowned manufacturers of microwave and RF components as well as specialized companies dedicated to cavity substrate production. Some well-known companies include Murata Manufacturing Co., Ltd., Kyocera Corporation, TDK Corporation, and others. These companies typically have advanced technology and facilities to produce high-performance cavity substrates for various microwave and RF applications, such as filters, amplifiers, antennas, etc.
Our company is also a professional manufacturer of microwave and RF components, with extensive experience and advanced production capabilities to produce high-quality cavity substrates. We have a professional engineering team capable of customizing various types of cavity substrates according to customer requirements, including designs with different materials, sizes, frequency ranges, and complexities. Our manufacturing process strictly follows international standards and is equipped with advanced equipment and quality control systems to ensure that each cavity substrate meets customer requirements.
Our company’s cavity substrates have the following advantages:
- High-performance materials:We use high-quality materials such as high-purity ceramics or specialty polymers to ensure that the substrates have excellent electrical, mechanical, and thermal properties.
- Customization capability:We can customize various types of cavity substrates according to customer-specific requirements, including designs with different frequency ranges, sizes, and shapes.
- Advanced manufacturing processes: We have advanced manufacturing equipment and technology to achieve high-precision processing and precise manufacturing processes.
- Quality assurance:We strictly adhere to quality control standards to ensure that each cavity substrate meets customer requirements and international standards.
In summary, our company is a reliable manufacturer of cavity substrates, capable of providing high-quality, customized products to meet various microwave and RF application needs.
What are the 7 qualities of good customer service?
Good customer service is essential for building positive relationships with customers and ensuring their satisfaction. Here are seven qualities that characterize good customer service:
- Empathy: Good customer service representatives demonstrate empathy by understanding and acknowledging the customer’s feelings, concerns, and needs. They listen actively, show compassion, and strive to put themselves in the customer’s shoes to provide personalized assistance.
- Responsiveness: Good customer service is prompt and responsive. Representatives should be readily available to assist customers, whether through phone, email, chat, or in-person interactions. Responding to inquiries, resolving issues, and addressing customer needs in a timely manner shows commitment and dedication to customer satisfaction.
- Professionalism: Professionalism is crucial in delivering good customer service. Representatives should maintain a courteous and respectful demeanor at all times, regardless of the situation. They should communicate clearly, provide accurate information, and follow through on commitments to build trust and credibility with customers.
- Knowledgeability: Good customer service representatives possess in-depth knowledge about the products or services they support. They are well-trained and informed, able to answer questions, provide recommendations, and offer solutions effectively. Having a thorough understanding of the company’s offerings instills confidence in customers and enhances their overall experience.
- Flexibility: Good customer service involves being flexible and adaptable to meet the diverse needs of customers. Representatives should be able to accommodate special requests, handle unexpected situations, and tailor solutions to individual circumstances. Being flexible demonstrates a commitment to customer satisfaction and fosters positive relationships.
- Problem-solving skills: Good customer service representatives are skilled problem solvers. They approach challenges with a positive attitude, analyze issues thoroughly, and work proactively to find solutions. They take ownership of problems, escalate when necessary, and follow up to ensure resolution, turning negative experiences into positive ones for the customer.
- Consistency: Consistency is key to delivering good customer service. Representatives should strive to maintain consistent service standards across all interactions and channels. This includes consistent communication, follow-up, and service delivery to build trust and reliability with customers over time.
By embodying these qualities, businesses can provide exceptional customer service that exceeds expectations, fosters customer loyalty, and contributes to long-term success.
FAQs (Frequently Asked Questions)
What is a cavity substrate?
A cavity substrate is a material or structure used in the construction of microwave or radio frequency (RF) components such as filters, resonators, and antennas. It typically refers to a dielectric material used to form resonant cavities within the structure of a device.
What are cavity substrates used for?
Cavity substrates are used in various microwave and RF applications to manipulate electromagnetic signals within a specific frequency range. They are commonly used in devices such as filters, oscillators, amplifiers, and antennas to achieve desired performance characteristics.
What materials are used for cavity substrates?
Common materials used for cavity substrates include ceramics such as alumina (Al2O3) and aluminum nitride (AlN), as well as specialty polymer materials. The choice of material depends on factors such as frequency range, thermal stability, and mechanical strength.
How are cavity substrates manufactured?
The manufacturing process for cavity substrates involves steps such as material preparation, surface preparation, pattern transfer, etching, metallization, dielectric deposition, surface finishing, quality control, and testing. Specific techniques and processes vary depending on the material and design requirements.
What are the advantages of cavity substrates?
Cavity substrates offer advantages such as high electrical performance, thermal stability, mechanical strength, and customization capabilities. They enable the design and fabrication of high-performance microwave and RF components for various applications.
What factors should be considered when selecting a cavity substrate?
Factors to consider when selecting a cavity substrate include dielectric properties, thermal conductivity, mechanical stability, cost, manufacturability, and compatibility with the intended application and environment.
Can cavity substrates be customized?
Yes, cavity substrates can be customized to meet specific design requirements, including dimensions, frequency range, material composition, and features such as cavities, feed structures, and metallization patterns. Customization allows for tailored solutions to address unique application needs.
Where can I purchase cavity substrates?
Cavity substrates can be purchased from various manufacturers and suppliers specializing in microwave and RF components. It’s essential to choose a reputable supplier with expertise in cavity substrate fabrication and a track record of delivering high-quality products.