Cavity Substrate Manufacturing
Cavity Substrate Manufacturing,Cavity Substrate integrates recessed areas within the substrate, optimizing space and enhancing functionality in electronic devices. These cavities accommodate components or modules, allowing for compact designs and efficient heat dissipation. Cavity Substrates are crucial in high-density applications such as telecommunications, automotive, and aerospace, where space constraints are paramount. Manufacturing involves precise milling or etching processes to create the recessed areas, ensuring reliable electrical connections and effective thermal management. This substrate technology supports advanced miniaturization and integration, driving innovation in electronic device manufacturing and enabling sleek designs with improved performance and reliability.
Cavity substrates are essential components used in the construction of high-frequency microwave circuits. Composed of materials like alumina or aluminum nitride, these substrates provide a stable platform for components such as filters, resonators, and amplifiers. Their precise machining and metallization ensure optimal performance, offering low insertion loss, high thermal conductivity, and mechanical stability. Cavity substrates play a critical role in telecommunications, radar systems, and satellite communications, enabling the reliable transmission and reception of microwave signals in various applications.
What is a Cavity Substrate?
A cavity substrate typically refers to a material used in the construction of microwave and millimeter-wave circuits, particularly in radio frequency (RF) and microwave engineering. It’s an integral part of a cavity filter, resonator, or other microwave components.
In microwave engineering, cavity substrates are chosen for their dielectric properties, which affect the performance of the microwave device. These properties include dielectric constant, loss tangent, thermal conductivity, and coefficient of thermal expansion. Common materials used for cavity substrates include ceramics such as alumina (Al2O3), aluminum nitride (AlN), and various types of dielectric materials.
The design and choice of cavity substrate are crucial for achieving desired electrical characteristics such as frequency response, bandwidth, insertion loss, and power handling capabilities in microwave circuits. Additionally, the mechanical properties of the substrate, such as its dimensional stability and compatibility with manufacturing processes, also play a significant role in the overall performance and reliability of the microwave device.
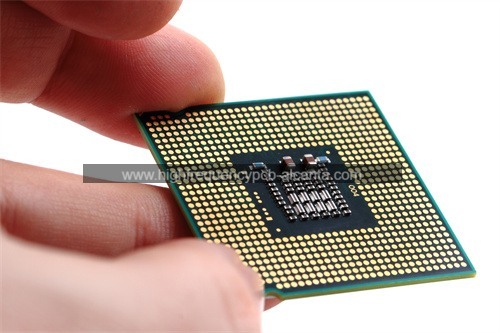
Cavity substrate manufacturing
What are Cavity Substrate Design Guidelines?
Cavity substrate design guidelines provide recommendations and principles for designing microwave and millimeter-wave circuits using cavity substrates. These guidelines are aimed at optimizing the performance, reliability, and manufacturability of the circuits. Here are some common cavity substrate design guidelines:
- Material Selection: Choose a substrate material with suitable dielectric properties for the desired frequency range and performance specifications. Consider factors such as dielectric constant, loss tangent, thermal conductivity, and coefficient of thermal expansion.
- Dimensional Stability: Select a substrate material with good dimensional stability to ensure consistent performance over temperature variations and environmental conditions.
- Compatibility with Manufacturing Processes: Ensure that the chosen substrate material is compatible with the manufacturing processes involved in circuit fabrication, such as machining, bonding, and metallization.
- Mechanical Integrity: Design the substrate to have sufficient mechanical strength and rigidity to withstand handling, assembly, and environmental stresses.
- Surface Finish and Flatness: Specify surface finish requirements to ensure proper bonding and adhesion of components. Maintain substrate flatness to minimize variations in electrical performance.
- Thermal Management: Incorporate thermal management features such as heat sinks, vias, or thermal pads to dissipate heat efficiently and prevent thermal degradation of circuit components.
- RF Performance Optimization: Design the cavity geometry, dimensions, and resonator structures to achieve the desired RF performance metrics such as frequency response, bandwidth, insertion loss, and return loss.
- Minimize Parasitic Effects: Minimize parasitic effects such as substrate loss, conductor loss, and electromagnetic coupling between components to maximize circuit efficiency and signal integrity.
- EMI Shielding: Consider incorporating shielding features or ground planes in the substrate design to mitigate electromagnetic interference (EMI) and improve circuit stability.
- Reliability and Longevity: Design the substrate with considerations for long-term reliability, including material aging, thermal cycling, and mechanical stress.
By following these cavity substrate design guidelines, engineers can develop microwave circuits that meet performance requirements while ensuring reliability and manufacturability.
What is the Cavity Substrate Fabrication Process?
Cavity substrate fabrication process refers to the series of steps involved in manufacturing cavity substrates for microwave and millimeter-wave circuits. These processes typically include:
- Material Selection: Choose a suitable substrate material based on dielectric properties, thermal conductivity, mechanical strength, and compatibility with manufacturing processes.
- Substrate Preparation: Start with raw substrate material in the form of sheets, blocks, or wafers. Clean the substrate surface to remove any contaminants and ensure proper adhesion of subsequent layers.
- Machining: Use precision machining techniques such as cutting, drilling, milling, or grinding to shape the substrate into the desired dimensions and cavity structures. This step may involve the use of computer numerical control (CNC) machines for high precision.
- Surface Treatment: Apply surface treatments such as chemical etching or polishing to achieve the required surface finish, flatness, and roughness for optimal circuit performance.
- Metallization: Deposit metal layers onto the substrate surface using techniques like sputtering, evaporation, or electroplating. These metal layers form conductive traces, pads, and grounding structures necessary for circuit connectivity.
- Pattern Definition: Use photolithography or other patterning techniques to define the circuit layout on the substrate surface. This step involves applying a photoresist material, exposing it to UV light through a mask, and developing to transfer the desired pattern onto the substrate.
- Etching: Remove unwanted metal or substrate material using wet or dry etching processes based on the defined pattern. This step creates the final cavity structure, conductive pathways, and component features on the substrate.
- Dielectric Layer Deposition: Optionally, deposit dielectric layers on the substrate surface to provide insulation between conductive traces and components, improve signal integrity, and prevent crosstalk.
- Surface Finish and Inspection: Finish the substrate surface to the required specifications, including cleaning, polishing, and inspection for defects, dimensional accuracy, and electrical continuity.
- Quality Assurance: Perform rigorous testing and quality control checks on fabricated cavity substrates to ensure they meet the specified electrical, mechanical, and dimensional requirements.
By following these steps, manufacturers can produce high-quality cavity substrates tailored to the needs of various microwave and millimeter-wave circuit applications.
How do you manufacture a Cavity Substrate?
Manufacturing a cavity substrate involves several steps to produce a high-quality substrate suitable for microwave and millimeter-wave circuits. Here’s an overview of the typical manufacturing process:
- Material Selection: Choose a substrate material based on dielectric properties, thermal conductivity, mechanical strength, and compatibility with manufacturing processes. Common materials include ceramics like alumina (Al2O3) or aluminum nitride (AlN), as well as various types of dielectric materials.
- Substrate Preparation: Start with raw substrate material in the form of sheets, blocks, or wafers. Clean the substrate surface thoroughly to remove any contaminants that could affect subsequent processing steps.
- Machining: Use precision machining techniques such as cutting, drilling, milling, or grinding to shape the substrate into the desired dimensions and cavity structures. Computer numerical control (CNC) machines are often used for high precision and repeatability.
- Surface Treatment: Apply surface treatments such as chemical etching or polishing to achieve the required surface finish, flatness, and roughness for optimal circuit performance. This step may involve multiple iterations to achieve the desired surface quality.
- Metallization: Deposit metal layers onto the substrate surface using techniques like sputtering, evaporation, or electroplating. These metal layers form conductive traces, pads, and grounding structures necessary for circuit connectivity. Photolithography and etching processes define the metal patterns.
- Dielectric Layer Deposition: Optionally, deposit dielectric layers on the substrate surface to provide insulation between conductive traces and components, improve signal integrity, and prevent crosstalk. Techniques such as chemical vapor deposition (CVD) or physical vapor deposition (PVD) are commonly used for dielectric layer deposition.
- Assembly and Integration: Assemble additional components such as filters, resonators, or semiconductor devices onto the substrate using bonding techniques like soldering or adhesive bonding. This step may involve precise alignment and bonding to ensure proper electrical connectivity.
- Surface Finish and Inspection: Finish the substrate surface to the required specifications, including cleaning, polishing, and inspection for defects, dimensional accuracy, and electrical continuity. Surface finish is critical to ensure proper adhesion of components and optimal electrical performance.
- Quality Assurance: Perform rigorous testing and quality control checks on fabricated cavity substrates to ensure they meet the specified electrical, mechanical, and dimensional requirements. Testing may include electrical characterization, mechanical stress testing, and visual inspection.
- Packaging and Shipping: Package the finished cavity substrates securely to prevent damage during transportation and storage. Proper packaging ensures that the substrates retain their quality until they are installed in the final electronic systems.
By following these steps, manufacturers can produce high-quality cavity substrates tailored to the needs of specific microwave and millimeter-wave circuit applications.
How much should a Cavity Substrate cost?
The cost of a cavity substrate can vary significantly depending on several factors, including:
- Material: The type and quality of material used for the substrate can greatly influence its cost. High-performance materials with specific dielectric properties may be more expensive than standard materials.
- Size and Complexity: Larger substrates or those with intricate cavity structures may require more material and labor, leading to higher costs.
- Manufacturing Process: The fabrication method and complexity of manufacturing processes involved, such as machining, metallization, and surface treatment, can impact the overall cost.
- Volume: Economies of scale apply, meaning larger production volumes typically lead to lower costs per unit. However, smaller production runs may incur higher costs due to setup and tooling expenses.
- Quality and Tolerance Requirements: Higher precision and tighter tolerances required for the substrate can increase manufacturing costs due to additional inspection and quality control measures.
- Supplier and Location: The choice of supplier and their location can affect costs due to differences in labor, overhead, and shipping expenses.
Given these factors, the cost of a cavity substrate can range from a few dollars for simple, small-scale applications to hundreds or even thousands of dollars for larger, more complex substrates used in high-frequency, precision applications. It’s essential to consider the trade-offs between cost, performance, and reliability when selecting cavity substrates for specific applications. Additionally, obtaining quotes from multiple suppliers and comparing prices can help ensure competitive pricing.
What is Cavity Substrate Base Material?
The basic material of a cavity substrate is typically the primary component used in manufacturing substrates for microwave and millimeter-wave circuits. These materials are selected based on their dielectric properties, thermal conductivity, mechanical strength, and compatibility with manufacturing processes. Common base materials for cavity substrates include:
- Alumina (Aluminum Oxide): Alumina is a commonly used base material known for its good dielectric properties, thermal conductivity, and mechanical strength. It is often used in manufacturing high-frequency circuits and power amplifiers.
- Aluminum Nitride (AlN): Aluminum nitride exhibits high thermal conductivity and excellent dielectric properties, making it suitable for high-power applications and circuits requiring good heat dissipation.
- Aluminum Boron Nitride (Aluminum Boron Nitride): Aluminum boron nitride offers outstanding thermal conductivity and chemical stability, often used in high-temperature applications and circuits requiring excellent thermal management.
- Multilayer Dielectric Materials: Multilayer dielectric materials typically consist of stacked layers of dielectric materials interleaved with metal layers. They can provide higher integration densities and lower transmission losses, suitable for miniaturization and high-frequency circuit designs.
- Zirconia (Zirconium Oxide): Zirconia exhibits excellent dielectric properties and high-temperature stability, commonly used in circuit applications requiring high stability and durability.
These base materials are utilized in the manufacture of cavity substrates to meet the performance requirements of various microwave and millimeter-wave circuits. Choosing the appropriate base material is crucial for the circuit’s performance, reliability, and manufacturing cost.
Which company makes Cavity Substrates?
Many companies produce cavity substrates, including internationally renowned electronic component manufacturers and companies specialized in microwave and millimeter-wave technology. Some of these companies include Murata Manufacturing Co., Kyocera Corporation, TDK Corporation, Rogers Corporation, and others. These companies have extensive experience and advanced technologies in the field of cavity substrate manufacturing, offering various types and specifications to meet the needs of different applications.
Our company is also capable of producing cavity substrates. As a company focused on electronics manufacturing, we have advanced production equipment and a skilled technical team capable of meeting custom requirements. Our cavity substrate manufacturing process strictly adheres to international standards and undergoes rigorous quality control to ensure stable and reliable product quality. We offer a variety of material options, including alumina, aluminum nitride, etc., and have flexible production capabilities to meet the varying specifications and quantities required by customers.
With an experienced engineering team and professional technical support, we collaborate with customers to optimize designs and provide the best solutions. Whether customers require high-frequency, high-power, or other specific requirements for cavity substrates, we can deliver customized solutions tailored to their needs, ensuring timely delivery and competitive pricing.
As a company committed to customer satisfaction and product quality, we continue to strive to provide high-quality cavity substrates, offering reliable support and solutions for our customers’ applications.
What are the 7 qualities of good customer service?
Good customer service is characterized by several key qualities that contribute to a positive experience for customers. Here are seven qualities of good customer service:
- Responsiveness: Good customer service involves being prompt and timely in addressing customer inquiries, concerns, or issues. Responding to customer needs in a timely manner demonstrates respect for their time and shows that their satisfaction is a priority.
- Empathy: Empathy involves understanding and acknowledging the customer’s perspective, feelings, and concerns. Good customer service representatives demonstrate empathy by actively listening to customers, showing compassion, and expressing understanding of their situations.
- Professionalism: Professionalism in customer service involves maintaining a courteous and respectful demeanor at all times, regardless of the situation. This includes using appropriate language, tone of voice, and behavior, as well as adhering to company policies and procedures.
- Knowledgeability: Good customer service representatives possess comprehensive knowledge about the products or services offered by the company. They are able to provide accurate information, answer questions, and offer solutions to customer problems effectively.
- Problem-solving skills: Effective problem-solving skills are essential for resolving customer issues and concerns efficiently. Good customer service representatives are proactive in identifying and addressing customer problems, finding appropriate solutions, and following through to ensure customer satisfaction.
- Flexibility: Flexibility in customer service involves adapting to the unique needs and preferences of each customer. This may include offering personalized solutions, accommodating special requests, or adjusting policies when necessary to meet customer needs while still adhering to company guidelines.
- Consistency: Consistency is key to providing excellent customer service. Customers expect a consistent level of service quality across all interactions with a company, whether it’s in-person, over the phone, via email, or through other channels. Consistently delivering high-quality service builds trust and loyalty with customers over time.
By embodying these qualities, businesses can create positive experiences for their customers, foster customer loyalty, and differentiate themselves from competitors in the marketplace.
FAQs
What is a cavity substrate?
A cavity substrate is a material used in the construction of microwave and millimeter-wave circuits, particularly in RF and microwave engineering. It forms the basis for components such as cavity filters, resonators, and other microwave devices.
What are cavity substrates made of?
Cavity substrates can be made from various materials, including ceramics such as alumina (Al2O3), aluminum nitride (AlN), and specialty dielectric materials. The choice of material depends on factors like dielectric properties, thermal conductivity, and mechanical strength required for the application.
What are the applications of cavity substrates?
Cavity substrates are used in a wide range of applications in RF and microwave engineering, including telecommunications, radar systems, satellite communications, wireless networks, and more. They are essential components in the construction of filters, resonators, amplifiers, oscillators, and other microwave devices.
What are the advantages of cavity substrates?
Cavity substrates offer several advantages, including high-frequency performance, low insertion loss, excellent thermal conductivity, and compatibility with high-power applications. They also provide mechanical stability, reliability, and resistance to environmental factors like temperature variations and humidity.
How are cavity substrates manufactured?
The manufacturing process for cavity substrates typically involves steps such as material selection, substrate preparation, machining, metallization, patterning, and quality control. Advanced techniques like precision machining, chemical etching, and thin-film deposition are often used to achieve the desired substrate properties and dimensions.