Cavity Step PCB Manufacturer
Cavity Step PCB Manufacturer,Cavity Step PCB (Printed Circuit Board) is an advanced design used in high-density and high-performance electronic applications. It features cavities or recessed areas within the board, allowing for the embedding of components, thus achieving a lower profile and improved thermal management. This design supports complex circuit layouts and miniaturization, making it ideal for applications like RF modules, aerospace, and medical devices. Cavity Step PCBs enhance signal integrity and performance by reducing parasitic inductance and capacitance. Their precise manufacturing process ensures reliable and robust connections, contributing to the overall efficiency and durability of advanced electronic systems.
What is a Cavity Step PCB?
A Cavity Step PCB refers to a type of printed circuit board (PCB) that incorporates cavities or recessed areas within the board itself. These cavities are created by milling or routing out specific areas of the PCB material, leaving step-like transitions between different levels or layers of the board.
The primary purpose of using a Cavity Step PCB is to allow components to be mounted at different heights within the board structure. This design enables more efficient use of space and can facilitate complex PCB layouts where components need to be positioned at different levels for reasons such as thermal management, signal integrity, or mechanical constraints.
Applications of Cavity Step PCBs are diverse and can be found in various industries including telecommunications, aerospace, automotive, and consumer electronics. They are particularly useful in high-density PCB designs where minimizing the overall size of the board and optimizing component placement are critical.
Manufacturing Cavity Step PCBs requires precise planning and machining capabilities to ensure that the cavities are accurately aligned with the design specifications. This precision is essential to maintain the integrity of the board’s electrical connections and mechanical stability.
In summary, Cavity Step PCBs represent a specialized type of printed circuit board that leverages recessed areas or cavities to accommodate components at different heights within the board structure, offering advantages in space utilization and design flexibility for demanding electronic applications.
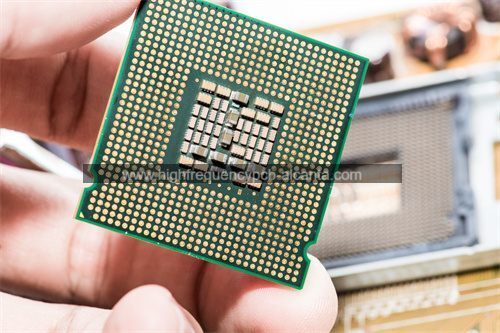
Cavity Step PCB Manufacturer
What are the Cavity Step PCB Design Guidelines?
Designing Cavity Step PCBs requires careful consideration of several key guidelines to ensure optimal performance and manufacturability:
- Component Placement: Plan the placement of components carefully, taking into account the different levels or steps created by the cavities. Ensure that components requiring different heights are placed accordingly to maximize space utilization and maintain signal integrity.
- Cavity Size and Depth: Determine the dimensions of the cavities based on the components that will be housed within them. The depth of the cavities should be sufficient to accommodate the tallest component without compromising the overall structural integrity of the PCB.
- Mechanical Support:Provide adequate mechanical support around the cavities to maintain the rigidity of the PCB. Consider using additional structural elements or reinforcement techniques if necessary, especially if the cavities are large or deep.
- Clearance and Spacing: Maintain proper clearance and spacing between the edges of the cavities and other components, traces, or copper pours. This prevents electrical shorts or mechanical interference during assembly and operation.
- Thermal Management: Consider the thermal implications of cavity design. Cavities can affect heat dissipation and airflow within the PCB assembly. Ensure that any thermal vias or heat dissipation paths are appropriately integrated into the design to manage temperature rise effectively.
- Signal Integrity: Minimize the impact of cavities on signal integrity by carefully routing high-speed signal traces away from cavity edges. Avoid sharp corners or abrupt changes in trace routing near cavities to reduce signal reflections and impedance mismatches.
- Manufacturability:Collaborate closely with your PCB manufacturer to ensure that the cavity dimensions and design specifications are feasible for their manufacturing capabilities. Provide detailed drawings and specifications to clearly communicate your design intent.
- Material Selection: Choose PCB materials that can withstand the milling or routing processes used to create cavities. Consider the impact of cavity design on material properties such as mechanical strength, dielectric properties, and thermal conductivity.
- Testing and Validation: Conduct thorough testing and validation of prototypes to verify the functionality and reliability of the cavity step design. Test for mechanical strength, thermal performance, and electrical characteristics to ensure that the design meets performance requirements.
By following these guidelines, designers can effectively implement cavity step PCB designs that optimize space utilization, maintain signal integrity, and ensure reliable performance across various electronic applications.
What is the Cavity Step PCB Fabrication Process?
The fabrication process of Cavity Step PCBs involves several key steps to create the recessed areas or cavities within the PCB structure. Here’s an overview of the typical fabrication process:
- Design Preparation: Start with the PCB design process where the layout includes specifications for the cavities. This involves determining the dimensions, positions, depths, and other parameters of the cavities based on the components and design requirements.
- Material Selection: Choose appropriate PCB materials that can withstand the milling or routing processes required to create cavities. The choice of material should consider mechanical strength, thermal properties, and compatibility with the manufacturing process.
- Circuit Layer Preparation: Begin the PCB fabrication process by preparing the base circuit layers. This includes cleaning and preparing the substrate material (usually fiberglass-reinforced epoxy laminate), applying copper layers (through processes like lamination or deposition), and imaging the circuit layers with the desired traces and pads.
- Cavity Definition: Once the base circuit layers are prepared, define the cavities according to the design specifications. Cavities are typically created using mechanical milling or routing techniques. CNC (Computer Numerical Control) machines are commonly used for this purpose, where precise cutting tools remove material to form the recessed areas.
- Cavity Inspection and Cleaning: After milling or routing, inspect the cavities to ensure they meet dimensional and positional accuracy requirements. Clean the PCB thoroughly to remove any debris or residues that could affect subsequent processing steps.
- Additional Layers and Processing: Continue with the fabrication process by adding additional layers (if a multilayer PCB) and conducting necessary processes such as via drilling, copper plating, and solder mask application. Each layer is processed and inspected to ensure alignment and integrity.
- Component Assembly: Once all layers are fabricated and processed, proceed with component assembly. Place surface-mount and through-hole components onto the PCB as per the assembly plan. Special attention is given to component placement around cavities to ensure proper clearance and alignment.
- Soldering and Testing:Solder components onto the PCB using appropriate soldering techniques (e.g., reflow soldering for surface-mount components, wave soldering for through-hole components). Conduct electrical testing, including continuity checks, functional testing, and possibly in-circuit testing (ICT), to verify proper functionality.
- Final Inspection and Quality Assurance: Perform final inspection and quality assurance checks to ensure the assembled PCB meets all design specifications and functional requirements. This includes visual inspection, electrical testing, and possibly environmental testing depending on application requirements.
- Finishing and Packaging: Apply any final surface finishes (such as HASL, ENIG, or OSP) and markings to the PCB. Cut or panelize the PCBs as needed for shipping and assembly into final products.
Throughout the entire fabrication process, collaboration between the PCB designer and manufacturer is crucial to ensure that the cavity step design is implemented accurately and that the finished PCB meets all performance and reliability standards for its intended application.
How do you manufacture a Cavity Step PCB?
Manufacturing a Cavity Step PCB involves a detailed process to create recessed areas within the PCB structure. Here’s a step-by-step outline of the manufacturing process:
- Design and Layout: Begin with the PCB design phase where the layout includes specifications for cavities. Define the dimensions, positions, depths, and other parameters based on component requirements and design considerations.
- Material Selection: Choose PCB materials suitable for creating cavities. Common materials include FR4 (fiberglass-reinforced epoxy laminate) or high-frequency materials depending on the application’s needs for mechanical strength, thermal properties, and performance.
- Circuit Layer Preparation: Prepare the base circuit layers by cleaning and applying copper layers. This involves processes like lamination, imaging the circuit layers with traces and pads using photolithography, and etching away unwanted copper.
- Cavity Creation: Use CNC (Computer Numerical Control) milling or routing machines to create cavities in the PCB. CNC machines are programmed to precisely cut out areas of the PCB substrate to the specified depths and dimensions outlined in the design.
- Inspection and Cleaning: Inspect the cavities post-milling to ensure they meet dimensional and positional accuracy requirements. Clean the PCB thoroughly to remove any debris or residues left from the milling process.
- Layer Addition and Processing: Proceed with adding additional layers if the PCB is multilayered. Each layer undergoes processes such as drilling vias, copper plating, applying solder mask, and legend printing. These steps are critical for maintaining alignment and structural integrity around the cavities.
- Component Assembly: Place surface-mount and through-hole components onto the PCB as per the assembly plan. Carefully position components around cavities to ensure proper fit and alignment. Consider mechanical support requirements for components placed near cavities.
- Soldering and Testing: Solder components onto the PCB using appropriate techniques such as reflow soldering for surface-mount components and wave soldering for through-hole components. Perform electrical testing, including continuity checks and functional testing, to verify proper assembly and functionality.
- Final Inspection and Quality Assurance: Conduct final inspection and quality assurance checks to ensure the assembled PCB meets all design specifications and functional requirements. This includes visual inspection, electrical testing, and possibly environmental testing depending on application requirements.
- Finishing and Packaging: Apply final surface finishes (e.g., HASL, ENIG, OSP) and markings to the PCB. Cut or panelize the PCBs for shipping and assembly into final products.
Throughout the entire manufacturing process of a Cavity Step PCB, collaboration between the PCB designer and manufacturer is crucial. Clear communication ensures that the cavities are accurately machined, and the final PCB meets performance, reliability, and manufacturability standards for its intended application.
How much should a Cavity Step PCB cost?
The cost of a Cavity Step PCB can vary significantly depending on several factors:
- Complexity of Design: The more intricate and detailed the cavity design, the higher the cost. Complex shapes, multiple levels, and tight tolerances all contribute to increased manufacturing complexity and cost.
- Number of Layers: Cavity Step PCBs can be single-sided, double-sided, or multilayered. Multilayer boards are generally more expensive due to the additional processes required for layer alignment, via drilling, and lamination.
- Material Type:The choice of PCB substrate material impacts cost. High-frequency materials or specialty substrates designed for specific applications may be more expensive than standard FR4.
- Cavity Depth and Size: Larger and deeper cavities require more machining time and precision, which can increase manufacturing costs.
- Volume and Quantity: Economies of scale apply to PCB manufacturing. Higher volumes typically lead to lower per-unit costs due to optimized production processes and bulk material purchasing.
- Additional Processes:Surface finish options (e.g., HASL, ENIG, OSP), special requirements for impedance control, and testing procedures (e.g., electrical testing, environmental testing) can add to the overall cost.
- Supplier and Location:PCB manufacturing costs can vary based on the supplier’s capabilities, location, and overhead costs.
To provide a rough estimate, Cavity Step PCBs can range from tens to hundreds of dollars per board, depending on the factors listed above. For a precise cost estimate, it’s best to consult with PCB manufacturers or suppliers directly. Providing detailed design specifications including cavity dimensions, material requirements, and expected volume will help in obtaining accurate price quotes.
What is Cavity Step PCB base material?
The base material used for Cavity Step PCBs typically refers to the substrate material on which the circuit layers and cavities are formed. The choice of base material depends on several factors including electrical properties, mechanical strength, thermal conductivity, and cost considerations. Here are some common types of base materials used for Cavity Step PCBs:
- FR4 (Fire Retardant 4): FR4 is the most widely used substrate material for PCBs. It is a glass-reinforced epoxy laminate known for its good electrical insulation properties, mechanical strength, and relatively low cost. FR4 is suitable for many applications unless high-frequency performance or specialized thermal management is required.
- High-Frequency Laminates: For applications requiring excellent electrical performance at high frequencies (GHz range), high-frequency laminates such as Rogers, Taconic, or Arlon materials are used. These materials have low dielectric constant (εr) and low loss tangent (tan δ), which are critical for minimizing signal loss in high-frequency circuits.
- Metal Core PCBs:Metal core PCBs (MCPCBs) use a metal substrate (typically aluminum or copper) as the base material instead of fiberglass. MCPCBs offer superior thermal conductivity, making them suitable for applications requiring efficient heat dissipation, such as power electronics or LED lighting.
- Ceramic-Based PCBs: Ceramic materials like alumina (Al2O3) or aluminum nitride (AlN) are used for applications requiring high thermal conductivity and excellent thermal management capabilities. These materials are expensive but offer superior performance in heat-sensitive applications.
- Flexible and Flex-Rigid PCBs: In some cases, flexible substrates (polyimide-based) or flex-rigid constructions are used for Cavity Step PCBs to aThe choice of base material for Cavity Step PCBs depends on the specific application requirements such as electrical performance, thermal management needs, mechanical durability, and cost constraints. Designers typically select the material that best balances these factors to achieve optimal performance and reliability in the final product.
Which company makes Cavity Step PCB?
When it comes to who manufactures Cavity Step PCBs, there are many professional PCB manufacturing companies that can provide this technology. Cavity Step PCBs are a relatively complex PCB design that typically requires high-precision machining and manufacturing processes. Some well-known PCB manufacturing companies have rich experience and technology in this area, catering to various industry needs.
For example, our company has the following advantages and capabilities in producing Cavity Step PCBs:
- Advanced Machining Equipment and Technology: We are equipped with advanced CNC milling and routing machines capable of precisely cutting various complex shapes and sizes of cavities. These machines ensure high-quality machining to meet strict customer requirements for cavity precision and dimensions.
- Rich Experience and Expertise: Our engineering team has many years of experience in PCB design and manufacturing, especially in handling complex PCB structures and special requirements. We can provide customized solutions and recommendations based on customer design specifications and requirements.
- Quality Control and Testing Capability: We strictly adhere to international standards and quality management systems, ensuring that every Cavity Step PCB undergoes detailed quality control and testing. From material selection to final product shipment, we conduct rigorous inspections and testing to ensure product reliability and stability.
- Wide Range of Application Areas: Cavity Step PCBs are widely used in telecommunications, aerospace, automotive, industrial control, and other fields. Our products meet high industry demands for PCB technology and performance, providing customers with stable and reliable electronic solutions.
- Customer Service and Support: We value communication and cooperation with customers, offering comprehensive customer service and support throughout the entire process. Whether it’s technical consultation, sample production, or mass production support, we are committed to establishing long-term partnerships with customers and achieving successful project implementation.
In summary, our company has mature technology and extensive experience in providing high-quality Cavity Step PCB solutions. Whether your project requires complex cavity designs, we can meet your needs and exceed your expectations through professional manufacturing processes and stringent quality control.
What are the 7 qualities of good customer service?
Good customer service is characterized by several key qualities that contribute to a positive experience for customers. Here are seven essential qualities of good customer service:
- Empathy: Empathy involves understanding and sharing the feelings of customers. Good customer service representatives listen actively to customers’ concerns, acknowledge their emotions, and demonstrate compassion in resolving issues.
- Patience: Patience is crucial in customer service, especially when dealing with frustrated or confused customers. Patient representatives take the time to listen attentively, explain solutions clearly, and remain calm under pressure.
- Clear Communication: Effective communication is essential for good customer service. Representatives should communicate clearly and concisely, using language that is easy for customers to understand. They should also be attentive to non-verbal cues and ensure messages are accurately conveyed.
- Knowledgeability: Good customer service requires a thorough understanding of products or services offered. Representatives should possess adequate knowledge to answer questions, provide solutions, and offer recommendations confidently.
- Problem-Solving Skills: Strong problem-solving skills enable customer service representatives to address issues efficiently and effectively. They identify root causes of problems, explore viable solutions, and follow through to ensure resolutions meet customers’ expectations.
- Positive Attitude: A positive attitude can significantly impact customer interactions. Representatives who approach interactions with enthusiasm, optimism, and a willingness to help create a welcoming and pleasant experience for customers.
- Responsiveness: Responsiveness refers to timely and prompt assistance to customer inquiries or issues. Good customer service involves acknowledging customer contacts promptly, providing updates on progress, and following up to ensure satisfaction.
These qualities collectively contribute to building trust, fostering customer loyalty, and enhancing overall satisfaction with the service provided. Companies that prioritize these qualities in their customer service efforts often differentiate themselves positively in the competitive marketplace.
FAQs
What is a Cavity Step PCB?
A Cavity Step PCB is a type of printed circuit board that features recessed areas or cavities within the board itself. These cavities allow components to be mounted at different heights, optimizing space and enhancing design flexibility.
What are the advantages of using Cavity Step PCBs?
Cavity Step PCBs allow for more compact and efficient PCB designs by accommodating components at varying heights. They can improve thermal management, reduce electromagnetic interference, and optimize signal integrity in high-density electronic assemblies.
Which industries benefit from Cavity Step PCBs?
Cavity Step PCBs find applications across various industries including telecommunications, aerospace, automotive, medical devices, and consumer electronics. They are particularly useful in applications where space optimization and precise component placement are critical.
How are Cavity Step PCBs manufactured?
Manufacturing Cavity Step PCBs involves precision machining processes such as CNC milling or routing to create the recessed cavities within the PCB substrate. The design and manufacturing process ensures that the cavities meet specific dimensional and positional requirements.
What considerations are important in designing Cavity Step PCBs?
Design considerations include the size and depth of cavities, placement of components around cavities to maintain structural integrity, thermal management strategies, and ensuring minimal impact on signal integrity through careful routing and shielding.
Can any PCB manufacturer produce Cavity Step PCBs?
Cavity Step PCBs require specialized equipment and expertise in precision machining and PCB fabrication. Not all PCB manufacturers may offer this capability, so it’s important to choose a manufacturer with experience in producing complex PCB designs.
What are the cost implications of Cavity Step PCBs?
The cost of Cavity Step PCBs depends on factors such as complexity of design, number of layers, material selection, and volume of production. Typically, these PCBs may be more expensive than standard designs due to the precision machining involved.