Cavity PCB Technology Manufacturing
Cavity PCB Technology Manufacturing,Cavity PCB Technology revolutionizes traditional printed circuit board design by incorporating hollowed-out spaces within the board’s layers. These cavities, meticulously engineered and strategically placed, serve multifaceted purposes, from enhancing miniaturization to optimizing thermal management and improving signal integrity. By integrating these voids into the PCB structure, electronic devices can achieve remarkable advancements in size reduction, allowing for sleeker and more compact designs without compromising performance. Additionally, the controlled isolation provided by cavity structures minimizes electromagnetic interference, ensuring pristine signal transmission in high-frequency applications. Cavity PCB Technology represents a sophisticated approach to PCB design, offering a blend of innovation, efficiency, and functionality that empowers the next generation of electronic devices with unparalleled performance and reliability.
What is Cavity PCB Technology?
Cavity PCB (Printed Circuit Board) technology involves creating a cavity or depression within the layers of a PCB. This cavity is typically created by removing a portion of the substrate material, leaving an empty space within the board’s structure.
Cavity PCB technology is used for various reasons, including:
- Miniaturization: By creating cavities within the PCB, components can be placed closer together, allowing for more compact and smaller electronic devices.
- Signal Integrity: Cavity PCBs can help in reducing electromagnetic interference (EMI) and crosstalk between adjacent signal traces by providing shielding or isolation for sensitive components or traces.
- Thermal Management: Cavities can be used to integrate thermal management solutions such as heat sinks or thermal vias, improving the dissipation of heat generated by electronic components.
- RF and Microwave Applications: Cavity PCBs are commonly used in radio frequency (RF) and microwave applications due to their ability to provide better isolation and controlled impedance for high-frequency signals.
- Antenna Integration: Cavity PCB technology allows for the integration of antennas within the PCB structure, providing a compact solution for wireless communication devices.
Overall, cavity PCB technology offers advantages in terms of size reduction, improved signal integrity, better thermal management, and suitability for high-frequency applications, making it a preferred choice for many advanced electronic systems.
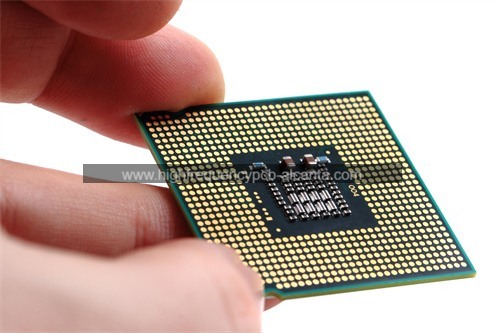
Cavity PCB Technology Manufacturing
What are the Cavity PCB Technology Design Guidelines?
The design guidelines for Cavity PCB technology include the following aspects:
- Cavity Design: Determine the location, size, and shape of the cavity within the PCB structure. This requires consideration of signal isolation, thermal management, component layout, and assembly requirements.
- Signal Integrity: Pay special attention to signal integrity when routing around the cavity, ensuring that signal line lengths, impedances, and paths are designed appropriately to minimize signal interference and loss.
- Thermal Management: Design appropriate thermal solutions such as heat spreaders, thermal vias, or heat sinks to ensure effective heat dissipation for electronic components within the cavity, preventing performance issues or damage due to overheating.
- Mechanical Stability: Consider mechanical stability in cavity design to ensure that structural issues or damage do not occur during PCB manufacturing, assembly, and usage.
- RF and Microwave Applications: If used for RF or microwave applications, focus on cavity design to provide optimal signal isolation, impedance matching, and high-frequency characteristics.
- Material Selection: Choose materials suitable for cavity PCBs, considering their dielectric constant, loss factor, thermal conductivity, and other properties to meet design requirements.
- Packaging and Component Layout: Select appropriate packaging and component layouts to ensure they fit within the cavity’s dimensions and shape, facilitating manufacturing and assembly.
- Testing and Validation: Consider testing and validation needs during the design phase to ensure that the performance and reliability of the cavity PCB meet expectations.
By following these guidelines, designers can effectively utilize Cavity PCB technology and ensure that the designed circuit board meets performance, reliability, and manufacturing requirements.
What is the Cavity PCB Technology Fabrication Process?
The fabrication process for Cavity PCB technology typically involves several key steps:
- Substrate Preparation: The process begins with preparing the substrate material, usually a laminate material such as FR-4 (Flame Retardant 4). The substrate is typically a rigid material with copper foil bonded to one or both sides.
- Cavity Formation: The next step involves creating the cavity or depression within the substrate material. This can be done using various techniques such as mechanical milling, routing, or laser ablation. The cavity is typically created on one or more layers of the PCB, depending on the design requirements.
- Copper Cladding: After the cavity is formed, the exposed surfaces of the substrate and the cavity walls are typically coated with a thin layer of copper through processes such as electroless copper deposition or sputtering. This copper cladding helps improve the electrical conductivity and facilitates subsequent plating processes.
- Circuit Patterning: The circuit patterns are then defined on the outer layers of the PCB using processes such as photolithography, where a photoresist material is applied, exposed to UV light through a photomask, developed, and then etched to remove unwanted copper, leaving behind the desired circuit traces.
- Plating: Plating processes are used to thicken the copper traces and vias on the PCB. This involves electroplating copper onto the exposed surfaces of the substrate and the cavity walls, as well as filling vias and through-holes to establish electrical connections between different layers of the PCB.
- Surface Finish: After the copper plating process, the PCB’s surface is typically coated with a surface finish to protect the copper traces from oxidation and provide solderability for component attachment. Common surface finishes include hot air solder leveling (HASL), immersion gold (ENIG), or immersion silver.
- Assembly: Once the fabrication of the PCB is complete, electronic components are assembled onto the board using techniques such as surface mount technology (SMT) or through-hole mounting. Components are soldered onto the PCB using reflow soldering or wave soldering processes.
- Testing and Inspection: The finished PCB undergoes testing and inspection to ensure that it meets the required electrical and mechanical specifications. This may include electrical continuity testing, functionality testing, and visual inspection for defects.
Overall, the fabrication process for Cavity PCB technology involves several intricate steps to create the cavity, define circuit patterns, establish electrical connections, and assemble electronic components, resulting in a finished PCB that meets the desired design requirements.
How do you manufacture a Cavity PCB Technology?
Manufacturing a Cavity PCB involves several specialized steps to create the cavity within the PCB structure. Here’s an overview of the manufacturing process for Cavity PCB technology:
- Design Preparation: The process starts with the design of the PCB layout using computer-aided design (CAD) software. During this stage, the designer specifies the location, size, and shape of the cavity within the PCB structure.
- Substrate Preparation: Once the design is finalized, the manufacturing process begins with the preparation of the substrate material. This typically involves selecting a suitable laminate material such as FR-4 (Flame Retardant 4) and cutting it to the required size.
- Cavity Formation: The next step is to create the cavity or depression within the substrate material. This can be achieved using various techniques such as mechanical milling, routing, or laser ablation. The cavity is typically created on one or more layers of the PCB, depending on the design requirements.
- Copper Cladding: After the cavity is formed, the exposed surfaces of the substrate and the cavity walls are typically coated with a thin layer of copper. This copper cladding helps improve the electrical conductivity and facilitates subsequent plating processes.
- Circuit Patterning: Circuit patterns are then defined on the outer layers of the PCB using processes such as photolithography. A photoresist material is applied to the copper-clad substrate, exposed to UV light through a photomask, developed, and then etched to remove unwanted copper, leaving behind the desired circuit traces.
- Plating: Plating processes are used to thicken the copper traces and establish electrical connections between different layers of the PCB. This involves electroplating copper onto the exposed surfaces of the substrate and the cavity walls, as well as filling vias and through-holes.
- Surface Finish: Once the plating process is complete, the PCB’s surface is typically coated with a surface finish to protect the copper traces and provide solderability for component attachment. Common surface finishes include hot air solder leveling (HASL), immersion gold (ENIG), or immersion silver.
- Assembly: After surface finishing, electronic components are assembled onto the board using techniques such as surface mount technology (SMT) or through-hole mounting. Components are soldered onto the PCB using reflow soldering or wave soldering processes.
- Testing and Inspection: The finished Cavity PCB undergoes testing and inspection to ensure that it meets the required electrical and mechanical specifications. This may include electrical continuity testing, functionality testing, and visual inspection for defects.
By following these steps, manufacturers can produce Cavity PCBs that meet the desired design requirements and quality standards.
How much should a Cavity PCB Technology cost?
The cost of manufacturing a Cavity PCB (Printed Circuit Board) depends on various factors, including the complexity of the design, the number of layers, the size of the board, the materials used, and the production volume. Here are some key factors that influence the cost:
- Complexity of Design: More complex designs with intricate circuitry, tight tolerances, and specialized features such as controlled impedance or high-frequency signals will typically incur higher manufacturing costs.
- Number of Layers: Cavity PCBs can be single-sided, double-sided, or multi-layered. Multi-layered PCBs with more layers will generally cost more to manufacture due to the increased material and production complexity.
- Size of the Board: The physical dimensions of the PCB also play a role in determining the manufacturing cost. Larger boards require more material and may involve additional processing steps, resulting in higher costs.
- Materials Used: The choice of substrate material, copper thickness, surface finish, and other materials used in the PCB construction can impact the overall cost. High-performance materials or specialty laminates may incur higher costs compared to standard FR-4 substrates.
- Production Volume: The economies of scale apply to PCB manufacturing, meaning that larger production volumes typically result in lower per-unit costs due to efficiencies in material utilization, setup time, and production processes.
- Additional Processes: Specialized processes such as cavity creation, laser drilling, impedance control, and selective plating required for Cavity PCBs may add to the manufacturing cost.
- Assembly and Testing: The cost of assembling electronic components onto the PCB and testing the finished boards for functionality and quality assurance should also be considered.
It’s essential to work closely with a PCB manufacturer or supplier to obtain a precise cost estimate based on your specific design requirements, production volume, and desired quality standards. Additionally, factors such as lead time, shipping costs, and any additional services required should be factored into the overall cost assessment.
What is Cavity PCB Technology base material?
Cavity PCB technology typically utilizes the same base materials as traditional PCB manufacturing processes. The base material for Cavity PCBs is usually a substrate composed of a laminate material, commonly known as the core material, which provides the structural foundation for the PCB.
The core material used in Cavity PCBs is often a rigid substrate made of fiberglass-reinforced epoxy resin, known as FR-4 (Flame Retardant 4). FR-4 is widely used in PCB manufacturing due to its excellent electrical insulation properties, mechanical strength, and affordability.
In addition to FR-4, other high-performance substrates may also be used for Cavity PCBs depending on specific application requirements. These substrates may include materials such as:
- High-frequency laminates: These substrates are optimized for RF/microwave applications and may feature low dielectric constant (Dk) and low loss tangent (Df) properties to minimize signal loss and distortion.
- Thermally conductive substrates: For applications requiring enhanced thermal management, substrates with high thermal conductivity may be used to efficiently dissipate heat generated by components within the cavity.
- Metal core substrates: In some cases, metal core substrates, such as aluminum or copper-clad laminates, may be used for Cavity PCBs to provide improved thermal performance and mechanical stability.
Overall, the choice of base material for Cavity PCBs depends on factors such as electrical performance, thermal management requirements, mechanical strength, and cost considerations.
Which company makes Cavity PCB Technology?
Currently, there are many companies producing Cavity PCB technology circuit boards. Some of the well-known companies include Foxconn, Lenovo, and Epson. These companies have extensive experience in the field of electronics manufacturing and possess advanced production equipment, enabling them to provide high-quality Cavity PCB technology products.
As for our company, we also have the capability to produce Cavity PCB technology. We have advanced manufacturing equipment and a skilled technical team capable of customizing various types of Cavity PCB boards according to customer requirements and specifications. Our manufacturing process adheres to industry standards, ensuring stable and reliable product quality and performance.
Our manufacturing process covers every aspect from design to production, including cavity design, material selection, cavity machining, circuit wiring, copper deposition, surface treatment, etc. We strictly control the quality of each process and validate product performance through rigorous testing and inspection procedures.
Furthermore, we prioritize communication and collaboration with customers, providing personalized solutions according to their requirements and ensuring timely delivery and excellent after-sales service. We are committed to delivering high-quality products and satisfactory service experiences to our customers, fostering mutual growth and development.
Therefore, as our company, we have the capability and willingness to provide high-quality Cavity PCB technology products, meet customer demands, and create value for our customers.
What are the 7 qualities of good customer service?
The seven qualities of good customer service are:
- Responsiveness: Good customer service involves promptly addressing customer inquiries, concerns, and requests. This includes responding to emails, calls, and messages in a timely manner, as well as providing assistance when needed.
- Empathy: Empathy involves understanding and acknowledging the customer’s emotions, concerns, and perspectives. Good customer service representatives demonstrate empathy by actively listening to customers, showing understanding of their situations, and expressing genuine concern for their needs.
- Professionalism: Professionalism encompasses maintaining a courteous and respectful demeanor at all times, regardless of the situation. This involves using proper language, tone, and behavior when interacting with customers, as well as adhering to company policies and procedures.
- Knowledgeability: Good customer service requires having a thorough understanding of the products or services offered by the company. Customer service representatives should be knowledgeable about the features, benefits, and usage of the products/services, as well as any relevant policies or procedures.
- Problem-solving skills: Effective problem-solving is essential for resolving customer issues and concerns efficiently and satisfactorily. Good customer service representatives are resourceful, proactive, and solution-oriented, and they work diligently to address customer problems and find suitable resolutions.
- Consistency: Consistency involves delivering a consistent level of service quality across all customer interactions and touchpoints. This includes maintaining consistent communication channels, response times, and service standards to ensure a positive and reliable customer experience.
- Personalization: Personalization involves tailoring the customer service experience to meet the individual needs and preferences of each customer. This may include addressing customers by name, remembering their previous interactions or preferences, and offering personalized recommendations or solutions. By providing personalized service, companies can strengthen customer relationships and foster loyalty.
FAQs
What is Cavity PCB Technology?
Cavity PCB (Printed Circuit Board) technology involves creating a cavity or depression within the layers of a PCB. This cavity can be utilized for various purposes such as miniaturization, thermal management, and improved signal integrity.
What are the advantages of Cavity PCB Technology?
Cavity PCB technology offers advantages such as reduced size and weight of electronic devices, improved thermal management, enhanced signal integrity, and better integration of components, especially for high-frequency applications.
How is a cavity created in a PCB?
Cavity PCBs are created by removing a portion of the substrate material from one or more layers of the PCB. This can be achieved through techniques such as mechanical milling, routing, or laser ablation, leaving an empty space within the board’s structure.
What applications benefit from Cavity PCB Technology?
Cavity PCB technology is commonly used in applications requiring miniaturization, such as smartphones, tablets, wearables, and IoT devices. It is also beneficial for high-frequency applications like RF/microwave systems, antennas, and communication devices.
Does Cavity PCB Technology impact manufacturing costs?
Implementing Cavity PCB technology may lead to slightly higher manufacturing costs compared to traditional PCBs due to additional fabrication steps such as cavity creation and increased complexity. However, the benefits of improved performance and functionality may outweigh the additional costs in many cases.
Are there any limitations to Cavity PCB Technology?
While Cavity PCB technology offers many benefits, it also has limitations such as increased design complexity, potential challenges in thermal management for deeper cavities, and limitations in component placement due to the presence of cavities.
How can I determine if my project requires Cavity PCB Technology?
The decision to use Cavity PCB technology depends on specific project requirements such as size constraints, thermal management needs, signal integrity considerations, and component integration challenges. Consulting with experienced PCB designers and manufacturers can help determine if Cavity PCB technology is suitable for your project.