Cavity PCB/Substrate Manufacturer
Cavity PCB/Substrate Manufacturer,Cavity PCB/Substrate integrates cavities within the board, allowing components to sit lower for reduced profile designs. These substrates facilitate compact electronic assemblies, optimizing space utilization while maintaining performance. The cavities can house sensitive components or accommodate heat sinks for efficient thermal management. Cavity PCB/Substrate manufacturing involves precise milling or etching processes to create the recessed areas. By enabling tighter integration and improved thermal performance, these substrates cater to the demands of high-performance electronics in sectors like telecommunications, automotive, and aerospace, where space constraints and thermal management are critical considerations.
In the intricate tapestry of electronics, Semiconductor BGA (Ball Grid Array) substrates emerge as protagonists, their narrative revealed through a curated collection of Frequently Asked Questions (FAQs). This mosaic unravels the diverse facets of BGA substrates—from their myriad types and nuanced production processes to their versatile applications and inherent advantages.
These substrates, with their diverse compositions, encompass organic FR-4 materials, robust ceramics like alumina and aluminum nitride, and innovative designs such as metal cores and flexible solutions. The production journey, akin to a meticulously orchestrated symphony, weaves together layers of complexity, from the artistry of lamination to the precision of etching, drilling finesse, and the delicate choreography of solder ball placement. Throughout this symphony, the vigilant scrutiny of quality control ensures each substrate attains the zenith of reliability and electrical performance.
Solder balls, the unsung heroes in this electronic odyssey, emerge as indispensable connectors, intricately knitting the fabric of electrical connectivity and mechanical attachment. The versatility of BGA substrates finds expression across a vast spectrum of electronic devices—integrated seamlessly into consumer electronics, fortifying industrial machinery, empowering automotive systems, and making strides in the realm of wearable devices.
Ceramic BGA substrates, with their thermal prowess, carve a niche in applications demanding efficient heat dissipation. The integration of High-Density Interconnect (HDI) technology adds a crescendo to the design, elevating circuit density and signal integrity—an exquisite overture in the pursuit of miniaturization and heightened performance.
As the production curtain gracefully descends, these substrates take center stage in the grand electronic narrative, not merely answering questions but painting a vivid mural of technological progression. The FAQs stand as a testament to the pivotal role played by Semiconductor BGA substrates, casting them as the luminary protagonists in the ever-evolving saga of electronic technology.
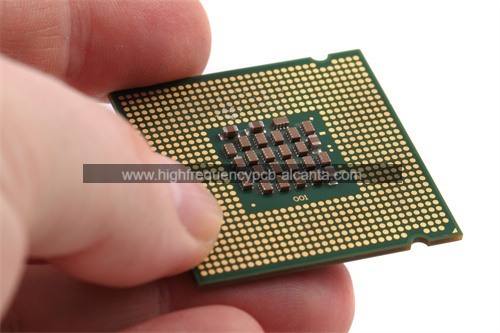
Cavity PCB/Substrate Manufacturer
What functionalities do Cavity PCBs/Substrates possess?
Cavity PCBs, with their distinct architectural feature of intentional cutouts or cavities, unfold a spectrum of functionalities that elevate them into a realm of specialized versatility within electronic applications. Let’s embark on a journey to reimagine and articulate these functionalities with a fresh perspective:
Innovative Component Sanctuary:
Cavity PCBs serve as avant-garde shelters, intricately enveloping components within their structure. This innovative approach provides a haven, safeguarding sensitive components from the external elements—be it the ingress of dust, the intrusion of moisture, or the imposition of mechanical stress.
Strategic Thermal Symphony:
The orchestration of cavities in Cavity PCBs is a symphony of thermal management. Ingeniously designed to enhance heat dissipation, these boards feature cavities that choreograph improved airflow or graciously host heat sinks. This symphony becomes especially crucial in applications pulsating with high-power components.
Spatial Alchemy for Miniaturization:
Cavity PCBs, akin to alchemists of space, master the art of miniaturization by embedding components within their structural tapestry. This spatial wizardry proves invaluable in applications where the conventional surface-mounted components are akin to spatial extravagance.
RF and Microwave Artistry:
In the realm of RF and microwave applications, Cavity PCBs metamorphose into canvases for precision artistry. The cavities, sculpted with finesse, create resonators or RF shields, imparting a touch of art to control electromagnetic and radiofrequency interference—an art form preserving the sanctity of signal integrity.
Seamless Sensor Ballet:
Cavity PCBs engage in a ballet of integration, seamlessly accommodating sensors within their structured dance. This choreography caters to applications demanding a balletic proximity and protection for sensors—an elegant performance in the world of electronic aesthetics.
Antenna Choreography:
The design of Cavity PCBs is a choreographed spectacle, providing dedicated stages for antennas. This performance optimizes the wireless dance by creating a designated arena for antennas, ensuring a harmonious interplay in the realm of wireless communication.
Acoustic Symphony in Audio Devices:
For audio devices, especially those resonating with microphones or speakers, Cavity PCBs compose an acoustic symphony. The cavities, akin to concert halls, create chambers that contribute to an orchestration of superior audio performance—each note resonating with precision.
Mechanical Fortitude Ballet:
Cavities play a role in the ballet of mechanical fortitude within Cavity PCBs. Ingeniously placed reinforcements within these structural stages enhance the overall rigidity and durability—a dance ensuring resilience in the face of mechanical challenges.
Crosstalk Minuet in High-Frequency Allegro:
High-frequency applications witness a minuet of minimized crosstalk within the allegro of Cavity PCBs. The cavities, conducting a delicate dance, minimize interference between adjacent traces or components—a testament to the finesse in achieving signal integrity.
Tailored Elegance for Specific Applications:
Cavity PCBs unveil a tapestry of tailored elegance, bespoke to the unique needs of specific applications. Whether accommodating unconventional components or orchestrating a specific performance, the adaptability provided by cavities transforms each PCB into a bespoke masterpiece.
In essence, the functionalities of Cavity PCBs are a canvas of innovation, where intentional cutouts transcend mere structural design. These boards emerge as artists, crafting an intricate dance of protection, precision, and customization—an electronic ballet where each cavity contributes to the symphony of specialized versatility.
What are the various types of Cavity PCBs/Substrates?
Cavity PCBs, with their diverse designs catering to specific applications, manifest in various types, each tailored to address distinct functionalities. Let’s explore these types with a fresh perspective:
Harmonic Antenna Chambers:
Crafted for wireless communication, these PCBs feature cavities that act as harmonic chambers for antennas. The design optimizes antenna performance, ensuring efficient signal transmission and reception.
Resonant RF/Microwave Platforms:
Precision meets purpose in these PCBs designed for RF and microwave applications. Cavities sculpt resonators and RF shields, orchestrating an environment that minimizes interference and elevates signal integrity.
Sensor Haven PCBs:
Tailored for precision, these PCBs embrace cavities as secure havens for sensors. The design ensures not only proximity but also protection for sensors demanding a meticulous placement.
Thermal Maestros:
Addressing the heat-intensive landscape, these PCBs with cavities conduct a thermal symphony. Enhanced dissipation is achieved as cavities facilitate improved airflow and the integration of heat sinks.
Spatial Marvels for Miniaturization:
In the pursuit of compactness, these PCBs weave a spatial marvel. Cavities become architects of miniaturization, embedding components within the structure for a streamlined design.
Acoustic Resonance Chambers:
A symphony in itself, these PCBs tailor cavities into acoustic chambers. In the world of audio devices, this design enhances sound waves, ensuring a resonant and superior audio performance.
Component Sanctuaries:
For sensitive components, these PCBs provide sanctuaries within cavities. This encapsulation shields components from external elements, safeguarding against moisture, dust, and mechanical stress.
HDI Virtuosos:
Mastering the intricacies of high-density interconnects, these PCBs blend cavities with HDI technology. The result is a virtuoso performance—increased circuit density and meticulous routing for compact designs.
Wearable Harmony:
Tailored for wearables, these PCBs dance with flexibility. Cavities, along with flexible substrates, conform to non-planar surfaces, offering harmony between form and function.
Hybrid Material Synthesis:
Blurring material boundaries, these PCBs amalgamate cavities with hybrid materials. The synthesis creates a versatile canvas, optimizing the performance of diverse components.
Automotive Prowess:
Engineered for the road, these PCBs feature cavities catering to automotive needs. The design accommodates specific components and sensors, addressing the unique challenges of the automotive environment.
Flexible Choreography:
Exhibiting a dance of flexibility, these PCBs incorporate cavities into flexible substrates. The choreography allows them to flex and adapt, ideal for applications demanding flexibility.
In essence, the multitude of Cavity PCB types unfolds a narrative of innovation. Each type is a distinct chapter, addressing the unique demands of diverse applications with a nuanced approach to design and functionality.
How are Cavity PCBs/Substrates related to IC packaging?
The dynamic interplay between Cavity PCBs (Printed Circuit Boards) and IC (Integrated Circuit) packaging unfolds as a nuanced collaboration, where the intricacies of design converge to shape the integration and protection of ICs. Let’s explore this relationship with a fresh perspective:
Versatility in Integration:
Cavity PCBs emerge as versatile canvases for the integration of ICs. Through carefully designed cavities, ICs find a purposeful space, ensuring not just connection but a harmonious integration into the broader circuit.
Guardians of Components:
Within the intricate tapestry of Cavity PCBs, the cavities stand as guardians, enveloping ICs and their companions in a protective embrace. This encapsulation shields against the elements, fortifying the components against the uncertainties of the environment.
Thermal Choreography:
Acknowledging the thermal ballet of high-power ICs, Cavity PCBs take center stage with cavities orchestrating a choreography of enhanced heat dissipation. This dance involves the strategic use of cavities for hosting heat sinks and facilitating optimal airflow to maintain the ICs’ temperature equilibrium.
Symphony of Signal Integrity:
In the symphony of high-frequency applications, Cavity PCBs conduct a meticulously composed piece. The strategic placement of cavities becomes the conductor’s wand, minimizing signal interference and ensuring the fluidity of signal integrity for the ICs.
Bespoke Elegance for IC Packages:
Cavity PCBs offer a canvas for bespoke elegance tailored to the unique packaging requirements of ICs. Each cavity is a bespoke frame, adapting seamlessly to accommodate different IC packages—be it the grace of surface-mount devices or the intricacies of ball grid arrays.
Integration of Passive Elements:
Within the cavities, Cavity PCBs integrate passive elements, creating a symphony of integration. This integration adds layers to the composition, harmonizing the presence of resistors, capacitors, and other passive components essential for the ICs.
HDI Flourish:
High-Density Interconnect (HDI) technology in Cavity PCBs adds a flourish to the design, turning the PCB into a canvas of precision. Cavities, coupled with the finesse of HDI, result in an intricate pattern—increased circuit density that speaks to the demands of modern IC interconnections.
Resonance in RF and Microwave Realms:
In the specialized realms of RF and microwave applications, Cavity PCBs resonate with purpose. Cavities sculpt structures that minimize interference, creating a harmonic environment where ICs can perform seamlessly in high-frequency settings.
Hybrid Material Ballet:
Cavity PCBs perform a ballet of integration with hybrid materials. The dance involves the marriage of materials within the cavities, creating a symphony of adaptability that addresses the unique thermal, mechanical, and electrical demands of IC packaging.
Tailored Solutions for IC Diversity:
Recognizing the diversity in IC types, Cavity PCBs offer tailored solutions. The adaptability of cavities ensures a bespoke approach, accommodating the specific packaging requirements of different IC types with finesse.
In essence, the relationship between Cavity PCBs and IC packaging is an orchestrated masterpiece. The cavities become not just design elements but integral players in the ensemble, shaping an environment where ICs find integration, protection, and optimal performance in the grand narrative of electronics.
What are the differences between Cavity PCBs/Substrate and traditional PCBs?
In the realm of circuit board architecture, Cavity PCBs and their traditional counterparts embark on divergent journeys, each weaving a unique narrative through intentional design choices. Let’s explore the distinctive tales these boards tell:
Architectural Innovations:
Cavity PCBs: Pioneers of innovation, Cavity PCBs showcase an avant-garde approach with deliberate cavities shaping their landscape. These intentional cutouts transcend traditional norms, paving the way for specialized functionalities.
Traditional PCBs: Anchored in conventionality, traditional PCBs adhere to a more standardized form, devoid of intentional cavities that redefine structural norms.
Deliberate Component Sanctuaries:
Cavity PCBs: Cavities within these boards are not just voids; they are purposeful sanctuaries for components. This intentional encapsulation shields components from external elements, adding layers of protection.
Traditional PCBs: Components find their place on the surface or through drilled holes, lacking the encapsulating embrace that cavities offer.
Thermal Symphony with Cavities:
Cavity PCBs: The thermal symphony unfolds in Cavity PCBs, where cavities play a pivotal role in dissipating heat. The integration of heat sinks within these intentional voids adds a dynamic rhythm to thermal management.
Traditional PCBs: In the traditional orchestra, external solutions take the lead for thermal control, as the absence of cavities limits the intrinsic dance of heat dissipation.
Elegance in Space Efficiency:
Cavity PCBs: The dance of space efficiency becomes an elegant waltz in Cavity PCBs. Cavities contribute to a more compact design, orchestrating a ballet of miniaturization where each component finds its place within the intentional voids.
Traditional PCBs: Stepping with a more conventional gait, traditional PCBs may occupy larger footprints, following the standard path of component placement.
Precision in RF and Microwave Artistry:
Cavity PCBs: Tailored for precision in RF and microwave applications, Cavity PCBs become canvases for artful design. Cavities sculpted with intent create resonators and shields, an artistic touch that minimizes electromagnetic interference.
Traditional PCBs: While adept in RF applications, traditional PCBs lack the intentional artistry of cavities in controlling electromagnetic fields.
Choreography of Flexibility:
Cavity PCBs: Some Cavity PCBs lead the choreography of flexibility, embracing designs with flexible substrates. This dance allows adaptation to non-planar surfaces, an essential feature in certain applications.
Traditional PCBs: Rooted in rigidity, traditional PCBs adhere to a more fixed structure, not swaying to the rhythm of flexibility.
Cost Dynamics and Conventional Stance:
Cavity PCBs: The incorporation of cavities and bespoke design considerations may add a layer to manufacturing costs, reflecting the innovation and functionality offered.
Traditional PCBs: The stalwarts of cost-effectiveness, traditional PCBs maintain their stronghold with a more conventional and cost-friendly approach.
In essence, the divergence between Cavity PCBs and traditional PCBs goes beyond surface-level differences. It’s a narrative of intentional design choices, where cavities become storytellers, shaping functionalities, protecting components, and adding layers of innovation to the electronic narrative.
What are the main structures and production technologies of Cavity PCBs/Substrates?
Within the realm of circuit board innovation, Cavity PCBs stand as technological marvels, boasting distinctive structures and production methodologies that set them apart. Let’s embark on a journey through the main architectural elements and the intricate production technologies that breathe life into Cavity PCBs:
Architectural Symphony:
Cavity Choreography:
Cavity PCBs take center stage with intentional cavities seamlessly integrated into their design. These voids, meticulously shaped, become the canvas for innovative functionalities.
Precision Component Placement:
Within the cavities, specific zones are designated for component placement. This deliberate structuring allows for a symphony of precision, ensuring each component finds its harmonious place.
Trace and Routing Ballet:
The dance of signal traces and routing unfolds with grace, meandering around and within the cavities. This choreography is a meticulous arrangement aimed at preserving signal integrity and optimizing performance.
Thermal Harmony Structures:
Cavity PCBs designed for thermal management introduce structures like integrated heat sinks within the cavities. This thermal harmony regulates the temperature, conducting a symphony of efficient heat dissipation.
RF and Microwave Crescendos:
In applications demanding RF and microwave precision, Cavity PCBs craft resonators or RF shields within the cavities. This crescendo of design minimizes electromagnetic interference, creating a harmonious environment.
Optional Flexibility Ballet:
Some Cavity PCBs showcase flexibility as a key feature. With flexible substrates, they perform a ballet of adaptability, conforming to non-planar surfaces with elegance.
Production Artistry:
Cavity Milling Mastery:
The genesis of cavities involves masterful milling or routing processes. CNC machines step onto the stage, sculpting the cavities with precision and artistry.
Component Encapsulation Elegance:
Techniques like selective encapsulation add an element of elegance, encapsulating components within the cavities. This encapsulation is akin to the protective strokes of an artist’s brush.
HDI Technology Symphony:
Cavity PCBs may harmonize with HDI technology, orchestrating a symphony of high-density interconnects. Microvia and fine line technologies play key roles, achieving intricate connectivity.
Thermal Material Composition:
Material selection becomes a compositional choice, with thermally conductive materials and high thermal conductivity substrates taking the spotlight. These materials conduct the thermal symphony with finesse.
RF and Microwave Design Mastery:
Specialized design tools and electromagnetic simulation software step into the limelight for RF and microwave applications. The design mastery ensures optimal cavity placement and controlled signal integrity.
Flexible PCB Ballet (if applicable):
If flexibility is part of the performance, manufacturing processes for flexible PCBs take center stage. Flexible substrates and materials execute a ballet of bending without sacrificing performance.
Lamination Artistry:
Advanced lamination techniques become an art form, ensuring the layers align with precision. The result is a robust and reliable PCB structure, akin to a masterful piece of art.
Soldering Finale:
Components find their place within the cavities through automated pick-and-place machines. The soldering finale secures each component, completing the masterpiece.
In essence, the creation of Cavity PCBs is a symphony of architectural brilliance and production artistry. Each intentional cavity and structural element contributes to a narrative of innovation, precision, and adaptability in the world of electronic compositions.
Frequently Asked Questions (FAQs)
What sets Cavity PCBs or Substrates apart in the world of electronics?
Cavity PCBs or Substrates stand out with their intentional cavities, offering a canvas for innovation. These voids serve diverse purposes, creating a dynamic presence in the electronics landscape.
Where do Cavity PCBs find their niche in applications?
Cavity PCBs carve their niche across industries, from telecommunications to aerospace and medical devices. Their versatility shines in scenarios demanding precise component placement, thermal finesse, and superior RF/microwave performance.
How are the distinctive cavities crafted within Cavity PCBs?
The artistry begins with precision milling or routing processes. Utilizing CNC machines, manufacturers sculpt intentional cavities according to intricate design specifications, adding a touch of craftsmanship to each board.
Why is component encapsulation significant in Cavity PCBs?
Component encapsulation becomes a shield, protecting electronic components from the elements and mechanical strains. It elevates reliability, ensuring the components endure and perform with longevity.
Can Cavity PCBs be enlisted for effective thermal management?
Absolutely. Cavity PCBs are engineered with thermal management in mind. Integrated cavities provide a stage for the incorporation of heat sinks and structures, orchestrating an efficient ballet of heat dissipation.
Are there nuances in designing Cavity PCBs for RF and microwave applications?
Precision takes center stage. Strategic placement of cavities, resonators, and RF shields becomes a delicate dance, minimizing electromagnetic interference and preserving the symphony of signal integrity.
What materials take the spotlight in the manufacturing of Cavity PCBs?
The material ensemble varies based on application needs. From standard FR-4 to high-frequency laminates and thermally conductive materials, each plays a role in harmonizing the board’s performance.
Can the flexibility of Cavity PCBs be explored?
Certainly. Some Cavity PCBs embrace flexibility through designed substrates, enabling them to gracefully adapt to non-planar surfaces. It’s a flexibility that resonates with specific applications.
Unraveling the intrigue of High-Density Interconnect (HDI) technology in Cavity PCBs?
HDI technology unfolds as a tapestry of intricacy. Microvias and fine lines, orchestrated by HDI, contribute to heightened circuit density and precise routing, adding a layer of sophistication.
Are there considerations in the cost realm for manufacturing Cavity PCBs?
Indeed. The incorporation of cavities and specialized features introduces a dimension of cost considerations. The intricacy of design, material choices, and production technologies shape the overall manufacturing landscape.
Conclusion
As we bring the curtain down on the exploration of Cavity PCBs/Substrates, we find ourselves immersed in a narrative woven with threads of innovation, precision, and purpose. These circuit boards, distinguished by intentional voids and intricacies, transcend the mundane to redefine the possibilities within the realm of electronics.
Our journey through the frequently asked questions (FAQs) has been akin to turning the pages of a technological saga. Cavity PCBs are not just circuits etched onto boards; they are canvases adorned with technological marvels. The deliberate crafting of cavities, guided by the finesse of precision milling or routing processes, transforms each board into a masterpiece of design.
Cavity PCBs find their place as protagonists across diverse industries – from the vast expanses of aerospace to the intricate landscapes of medical devices. Their versatility shines in applications demanding not just functionality, but a symphony of precise component placement, thermal finesse, and superior RF/microwave performance.
The intentional encapsulation of components within these cavities becomes a guardian’s embrace, a narrative of protection against the elements and mechanical stress. This emphasis on reliability adds a layer of endurance to the story, ensuring that the components within these boards stand the test of time.
Thermal management takes center stage as integrated cavities become the stage for a ballet of heat dissipation. Heat sinks and structures dance in harmony, orchestrating an elegant performance that ensures each component operates within optimal temperatures—a dynamic narrative within the heart of the boards.
For RF and microwave applications, the design narrative transforms into a delicate dance of precision. Cavities, resonators, and RF shields join in a serenade that minimizes electromagnetic interference, preserving the melodic symphony of signal integrity—an artful composition in the electronic landscape.
Material selection emerges as a cast of characters, each playing a vital role in the harmonic performance of the board. From the foundational FR-4 to high-frequency laminates and thermally conductive materials, they form an ensemble, shaping the narrative of material science.
Flexibility becomes a sonata in the board’s performance, with designed substrates allowing Cavity PCBs to dance gracefully and adapt to non-planar surfaces. This flexibility adds a layer of adaptability, harmonizing with specific applications that demand a dynamic approach.
The symphony of High-Density Interconnect (HDI) technology introduces a layer of intricacy. Microvias and fine lines, guided by this technological symphony, create a heightened circuit density and precise routing—a technological composition that adds sophistication to the narrative.
In the realm of cost considerations, the narrative takes an intriguing turn. The incorporation of cavities and specialized features introduces a dimension of complexity, shaping the overall manufacturing landscape. The cost becomes a subplot, intricately woven into the story of each crafted board.
As we bid farewell to this exploration, the journey through the world of Cavity PCBs/Substrates leaves an indelible mark. These boards are not just components; they are stories unfolding with each circuit, each cavity, and each innovation—a narrative that continues to evolve in the dynamic landscape of electronics.