Cavity PCB | High Frequency PCB Manufacturing
Cavity PCB | High Frequency PCB Manufacturing,Cavity PCBs, also known as embedded cavity printed circuit boards, are a specialized type of PCB that integrates one or more cavities within the board’s structure. These cavities are meticulously milled or routed out of the PCB substrate, creating empty spaces where components can be partially or fully embedded. This unique design feature offers several advantages, including space optimization, improved thermal management, enhanced electromagnetic shielding, and the ability to mount components flush with the board surface. Cavity PCBs are commonly utilized in applications requiring high-frequency circuits, RF/microwave systems, MEMS devices, and compact electronic assemblies. By embedding components within the PCB, these boards enable more efficient use of space, reduce overall system footprint, and enhance performance. With their ability to accommodate complex designs and stringent requirements, cavity PCBs represent a versatile solution for demanding applications across various industries, including aerospace, telecommunications, automotive, and medical devices.
What is a Cavity PCB?
A “cavity PCB” refers to a type of printed circuit board (PCB) that includes one or more cavities or cutouts within the board itself. These cavities are typically milled or routed out of the PCB substrate material, leaving empty spaces within the board’s structure.
Cavity PCBs are often used in applications where components need to be mounted flush with the surface of the PCB or where space-saving is critical. By embedding components partially or fully within the cavities, the overall profile of the PCB assembly can be reduced, making it more compact and potentially improving the thermal performance or electromagnetic shielding of the device.
Common applications of cavity PCBs include RF/microwave circuits, high-frequency applications, MEMS (Micro-Electro-Mechanical Systems), and electronic devices where miniaturization and performance are paramount.
Designing and manufacturing cavity PCBs require specialized techniques and equipment to ensure the integrity of the board structure and proper functioning of embedded components. These techniques may include precise milling or routing processes, careful consideration of material properties, and attention to thermal management and signal integrity concerns.
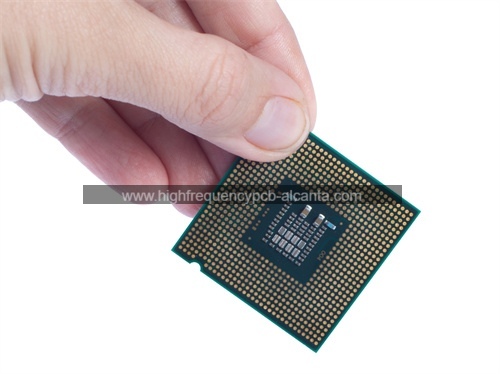
Cavity PCB | High Frequency PCB Manufacturing
What are the Cavity PCB Design Guidelines?
Designing cavity PCBs requires careful consideration of various factors to ensure the integrity of the board structure, proper functioning of embedded components, and optimal performance of the overall system. Here are some guidelines to follow when designing cavity PCBs:
- Component Placement: Strategically place components to maximize space utilization within the cavities while ensuring proper clearance for assembly and maintenance.
- Cavity Dimensions: Determine the dimensions of the cavities based on the size and shape of the components to be embedded. Ensure sufficient space for component placement and routing of traces while maintaining the structural integrity of the PCB.
- Material Selection: Choose PCB substrate materials with suitable properties for cavity PCB applications, such as low dielectric constant (εr) for RF/microwave applications or high thermal conductivity for improved heat dissipation.
- Signal Integrity: Minimize signal degradation by carefully routing traces away from cavity edges and avoiding sharp corners. Use controlled impedance routing techniques to maintain signal integrity, especially for high-frequency applications.
- Thermal Management: Implement thermal vias and conductive pads to dissipate heat generated by embedded components effectively. Ensure adequate ventilation within cavities to prevent heat buildup.
- Mechanical Stability: Reinforce cavity edges and surrounding areas to prevent structural weaknesses or flexing of the PCB during handling or operation.
- EMI Shielding: Utilize cavity PCBs for electromagnetic interference (EMI) shielding by embedding components within conductive enclosures or incorporating shielding layers within the PCB stackup.
- Manufacturability: Consider manufacturability constraints such as minimum feature size, tooling limitations, and assembly processes when designing cavity PCBs. Optimize designs for ease of fabrication and assembly.
- Testing and Debugging: Design access points or test points for probing and debugging embedded components within cavities. Ensure accessibility for testing and maintenance purposes.
- Documentation: Clearly document cavity dimensions, component placement guidelines, and other design considerations to facilitate communication with manufacturers and ensure accurate fabrication.
By following these guidelines, designers can create cavity PCBs that meet the requirements of specific applications while maximizing performance, reliability, and manufacturability.
What is the Cavity PCB Fabrication Process?
The fabrication process for cavity PCBs involves several steps, including design, material selection, substrate preparation, cavity creation, component assembly, and testing. Here’s a general overview of the cavity PCB fabrication process:
- Design: Create the PCB layout using electronic design automation (EDA) software, considering the placement of components and the location of cavities within the board. Ensure that the design meets the electrical and mechanical requirements of the application.
- Material Selection: Choose appropriate PCB substrate materials based on the application requirements, such as FR-4 for standard applications or specialized materials for high-frequency or high-temperature environments.
- Substrate Preparation: Prepare the PCB substrate by cleaning and surface treatment to improve adhesion and promote uniformity during subsequent processing steps.
- Cavity Creation: Use precision milling or routing techniques to create cavities within the PCB substrate according to the design specifications. This step requires careful control of depth, dimensions, and tolerances to ensure accuracy and consistency.
- Surface Treatment: Apply surface finishes, such as HASL (Hot Air Solder Leveling), ENIG (Electroless Nickel Immersion Gold), or OSP (Organic Solderability Preservatives), to protect exposed copper surfaces and facilitate soldering during component assembly.
- Component Assembly: Mount components onto the PCB using automated pick-and-place machines or manual assembly methods. Ensure proper alignment and soldering of components, including those embedded within cavities.
- Cavity Sealing (Optional): If required, seal the cavities with compatible materials to protect embedded components from environmental factors such as moisture, dust, or vibration.
- Testing and Inspection: Perform electrical testing, such as continuity checks, functional testing, and inspection of solder joints and component placements, to verify the integrity and functionality of the assembled PCB.
- Finishing Processes: Complete final finishing processes, such as depanelization, where individual PCBs are separated from larger panels, and surface cleaning to remove residues and contaminants.
- Quality Assurance: Conduct quality control checks throughout the fabrication process to ensure compliance with specifications, standards, and customer requirements.
- Documentation and Packaging: Generate documentation, including assembly drawings, bill of materials (BOM), and test reports, to accompany the finished PCBs. Package the PCBs securely for shipping or further integration into electronic assemblies.
By following these steps and employing specialized equipment and techniques, manufacturers can produce cavity PCBs that meet the stringent requirements of various applications while ensuring high quality and reliability.
How do you manufacture a Cavity PCB?
Manufacturing a cavity PCB involves several specialized steps and techniques to create the desired cavity structures within the printed circuit board. Here’s an overview of the manufacturing process:
- Design Phase:
– Develop the PCB layout using CAD (Computer-Aided Design) software, incorporating the design specifications, component placements, and cavity locations.
– Ensure that the design meets the electrical, mechanical, and thermal requirements of the intended application.
- Material Selection:
– Choose appropriate substrate materials based on factors such as dielectric constant, thermal conductivity, and mechanical strength.
– Select materials suitable for cavity creation and integration of embedded components.
- Substrate Preparation:
– Prepare the PCB substrate by cleaning and surface treatment to remove contaminants and promote adhesion.
– Apply a copper layer onto the substrate through processes like lamination or electrodeposition.
- Cavity Creation:
– Utilize precision milling or routing techniques to remove substrate material and create cavities according to the design specifications.
– Ensure precise control of cavity dimensions, depth, and tolerances to meet the requirements of embedded components.
- Surface Treatment:
– Apply surface finishes such as HASL, ENIG, or OSP to protect exposed copper surfaces and facilitate soldering.
– Ensure uniform coverage and compatibility with subsequent assembly processes.
- Component Assembly:
– Mount components onto the PCB using automated pick-and-place machines or manual assembly methods.
– Place components within the cavities and ensure proper alignment and soldering.
- Cavity Sealing (Optional):
– If required, seal the cavities with compatible materials to protect embedded components from environmental factors.
– Use adhesives, coatings, or encapsulation techniques to provide moisture resistance and mechanical stability.
- Testing and Inspection:
– Perform electrical testing, functional testing, and visual inspection to verify the integrity and functionality of the assembled PCB.
– Check for continuity, shorts, opens, and other defects.
- Finishing Processes:
– Complete final finishing processes such as depanelization, where individual PCBs are separated from larger panels.
– Clean the PCB surface to remove residues and contaminants.
- Quality Assurance:
– Implement quality control checks throughout the manufacturing process to ensure compliance with specifications and standards.
– Monitor process parameters and perform corrective actions as needed.
- Documentation and Packaging:
– Generate documentation including assembly drawings, BOM, and test reports.
– Package the finished PCBs securely for shipping or further integration into electronic assemblies.
By following these steps and employing advanced manufacturing techniques, manufacturers can produce cavity PCBs that meet the demanding requirements of various applications while ensuring high quality and reliability.
How much should a Cavity PCB cost?
The cost of a cavity PCB can vary significantly depending on various factors including the complexity of the design, the size of the board, the number of layers, the type of materials used, the quantity ordered, and the manufacturing processes involved. Here are some factors that can influence the cost of a cavity PCB:
- Design Complexity: Intricate designs with complex routing, multiple layers, and tight tolerances may require more time and resources to manufacture, thus increasing the overall cost.
- Materials: The choice of substrate materials, surface finishes, and additional features such as impedance control or thermal management can impact the cost of the PCB.
- Cavity Creation: Creating cavities within the PCB substrate involves additional manufacturing steps such as milling or routing, which can contribute to the overall cost.
- Component Assembly: The cost of component assembly, including the placement of components within the cavities, soldering, and testing, can affect the total cost of the PCB.
- Quantity: Larger order quantities typically result in lower per-unit costs due to economies of scale. However, smaller quantities may incur higher setup and tooling costs.
- Manufacturing Technology: Advanced manufacturing technologies and processes such as laser drilling or HDI (High-Density Interconnect) can increase the cost but may be necessary for certain applications.
- Lead Time: Expedited manufacturing or delivery options may come with additional costs compared to standard lead times.
- Supplier Selection: Different PCB manufacturers may offer varying pricing structures, so it’s essential to obtain quotes from multiple suppliers to compare costs.
As a rough estimate, the cost of a cavity PCB can range from a few dollars to several hundred dollars per board, depending on the factors mentioned above. For a more accurate cost assessment, it’s advisable to consult with PCB manufacturers and provide them with detailed specifications and requirements for a customized quote.
What is Cavity PCB base material?
The choice of base material for cavity PCBs depends on the specific requirements of the application, including factors such as electrical performance, thermal management, mechanical strength, and cost considerations. Here are some common base materials used for cavity PCBs:
- FR-4 (Flame Retardant 4): FR-4 is a widely used standard epoxy-based laminate material known for its good electrical insulation properties, mechanical strength, and cost-effectiveness. It is suitable for many general-purpose applications but may not be ideal for high-frequency or high-temperature environments.
- Rogers High-Frequency Laminates: Rogers Corporation offers a range of high-frequency laminates specially designed for RF/microwave applications. These laminates typically have low dielectric constants, low loss tangents, and excellent electrical performance at high frequencies.
- Polyimide (PI): Polyimide-based laminates, such as Kapton, are known for their high-temperature resistance, flexibility, and excellent dimensional stability. They are suitable for applications requiring operation at elevated temperatures or with stringent thermal management requirements.
- PTFE (Polytetrafluoroethylene): PTFE-based laminates, such as Teflon, offer exceptional electrical properties, including low dielectric constant, low loss tangent, and high thermal stability. They are commonly used in high-frequency and microwave applications where signal integrity is critical.
- Metal Core PCBs: Metal core PCBs feature a metal substrate layer, such as aluminum or copper, which provides excellent thermal conductivity for heat dissipation. They are suitable for applications requiring efficient thermal management, such as LED lighting and power electronics.
- Ceramic Substrates: Ceramic substrates, such as alumina (Al2O3) or aluminum nitride (AlN), offer excellent thermal conductivity, high mechanical strength, and stability over a wide temperature range. They are used in high-power applications, RF/microwave circuits, and harsh environments.
The choice of base material for a cavity PCB depends on the specific requirements of the application, including electrical performance, thermal management, mechanical strength, and cost considerations. It’s essential to select a material that can meet the performance and reliability requirements of the intended application while also considering factors such as manufacturability and cost-effectiveness.
Which company makes Cavity PCB?
There are many companies that specialize in manufacturing cavity PCBs, some of which include: Advanced Circuits, Epec Engineered Technologies, MCL Industries, PCB Universe, San Francisco Circuits, and more. These companies have advanced technology and professional manufacturing capabilities to meet the diverse needs of various applications.
Our company can also produce Embedded Cavity PCBs, which are a highly customized type of PCB requiring special design and manufacturing techniques. Embedded Cavity PCBs involve partially or fully embedding components within cavities inside the PCB during the design phase, allowing for more compact board designs and higher performance. With experienced engineering teams and advanced production equipment, our company can design and manufacture Embedded Cavity PCBs according to customer requirements and specifications.
We are committed to providing customers with high-quality, reliable, and high-performance Embedded Cavity PCB solutions. Our manufacturing processes adhere strictly to international standards, and we have a comprehensive quality control system in place to ensure that each product meets customer requirements and expectations. Our professional team tracks the production process closely to ensure timely delivery of Embedded Cavity PCB products that meet quality standards.
What are the 7 qualities of good customer service?
Good customer service is essential for building strong relationships with customers and fostering loyalty. Here are seven qualities that contribute to excellent customer service:
- Attentiveness: Attentiveness means actively listening to customers, understanding their needs, and responding promptly and appropriately. This involves paying close attention to customer inquiries, feedback, and concerns, and demonstrating genuine interest in helping them resolve issues or achieve their goals.
- Empathy: Empathy involves putting yourself in the customer’s shoes and understanding their emotions, perspectives, and challenges. Showing empathy helps create a positive rapport with customers, making them feel valued and understood. It involves being understanding, compassionate, and supportive, even in challenging situations.
- Communication Skills: Effective communication is crucial for delivering exceptional customer service. This includes clear and concise verbal communication, active listening, and the ability to convey information in a friendly and professional manner. Good communication skills help build trust, clarify expectations, and resolve misunderstandings.
- Problem-Solving Skills: Strong problem-solving skills enable customer service representatives to address customer issues and resolve conflicts efficiently and effectively. This involves identifying root causes, evaluating possible solutions, and taking proactive steps to meet customer needs and exceed their expectations.
- Patience: Patience is a valuable quality in customer service, especially when dealing with challenging or frustrated customers. It involves remaining calm, composed, and respectful, even in stressful situations, and taking the time to address customer concerns thoroughly and thoughtfully.
- Product Knowledge: Having a deep understanding of the company’s products or services allows customer service representatives to provide accurate information, answer questions, and offer helpful recommendations. Product knowledge instills confidence in customers and enhances their overall experience.
- Positive Attitude: Maintaining a positive attitude is essential for creating a welcoming and supportive environment for customers. This involves being friendly, enthusiastic, and approachable, and maintaining professionalism and optimism, even when faced with difficult situations. A positive attitude helps build trust, foster goodwill, and leave a lasting impression on customers.
By embodying these qualities, businesses can deliver exceptional customer service that exceeds expectations, builds loyalty, and contributes to long-term success.
FAQs
What is a cavity PCB?
A cavity PCB is a type of printed circuit board that includes one or more cavities or cutouts within the board itself. These cavities are typically milled or routed out of the PCB substrate material, leaving empty spaces within the board’s structure.
What are the advantages of cavity PCBs?
Cavity PCBs offer several advantages, including space-saving design, improved thermal performance, enhanced electromagnetic shielding, and the ability to mount components flush with the board surface, which can be beneficial for miniaturization and performance optimization.
What applications are cavity PCBs used for?
Cavity PCBs find applications in various industries such as telecommunications, aerospace, automotive, medical devices, and consumer electronics. They are commonly used in RF/microwave circuits, high-frequency applications, MEMS (Micro-Electro-Mechanical Systems), and electronic devices requiring miniaturization and performance.
How are cavity PCBs manufactured?
The manufacturing process for cavity PCBs involves several steps, including design, material selection, substrate preparation, cavity creation, component assembly, testing, and finishing processes. Precision milling or routing techniques are used to create cavities within the PCB substrate, followed by component assembly and testing to ensure functionality and reliability.
What considerations are important in cavity PCB design?
Important considerations in cavity PCB design include component placement, cavity dimensions, material selection, signal integrity, thermal management, mechanical stability, EMI shielding, manufacturability, testing, and documentation.
Can any PCB manufacturer produce cavity PCBs?
While many PCB manufacturers have the capability to produce cavity PCBs, specialized expertise and equipment may be required for precision cavity milling or routing. It’s essential to choose a manufacturer with experience in cavity PCB production and a track record of quality and reliability.
What are the cost implications of cavity PCBs?
The cost of cavity PCBs can vary depending on factors such as design complexity, materials used, manufacturing processes involved, quantity ordered, and supplier selection. Generally, cavity PCBs may incur higher manufacturing costs compared to standard PCBs due to additional machining and assembly steps. However, the benefits they offer in terms of performance and space-saving design may outweigh the costs for certain applications.