What is Cavity PCB?
Cavity PCB Manufacturer,Cavity PCBs feature recessed areas or cavities within the board, providing space for components or special features. These substrates enable compact designs, reduce overall PCB thickness, and enhance thermal management. Cavity PCBs offer precise component placement and can accommodate sensitive components such as RF filters or sensors. They are commonly used in aerospace, automotive, and telecommunications industries, where space-saving and performance are crucial. Cavity PCBs undergo meticulous manufacturing processes to ensure precise cavity dimensions and reliable electrical connections. Their versatility makes them ideal for applications requiring miniaturization and optimized functionality in electronic systems.
Cavity packaging substrate and Cavity PCB manufacturer, Open cavity on the PCBs. or open cavity on the package substrates. Such as: high frequency BGA substrate, using the most advanced Sap process, Msap process technology, fast delivery, stable quality.
A Cavity PCB, also known as a Printed Circuit Board with embedded hollow structures, is a forward-thinking circuit board design that incorporates three-dimensional cutouts or recesses within its structure. These hollow spaces serve diverse functions, ranging from accommodating components to integrating materials for heat dissipation and housing various functional elements. The integration of these cavities introduces innovative possibilities for creating electronic devices with enhanced integration.
Breaking it down further:
Incorporated Hollow Structures: This type of PCB features one or more three-dimensional cutouts or recesses seamlessly integrated into its design.
Efficient Component Integration: By strategically embedding hollow spaces, designated components can be seamlessly integrated directly onto the PCB. This not only results in a more streamlined design but also optimizes space efficiency.
Protective Enclosures:The hollow spaces function as protective barriers, ensuring the safety of sensitive components by shielding them from external factors like electromagnetic interference (EMI) and other environmental elements.
Effective Heat Dissipation:Carefully crafted voids are intentionally fashioned to accommodate materials or structures that play a pivotal role in effectively dispersing heat. This deliberate design enhances the PCB’s capability for robust thermal management.
Compact Form and Weight Reduction: Through the direct integration of components onto the board, there is a notable decrease in both size and weight when juxtaposed with traditional PCB designs.
Enhanced Electrical Performance: The close arrangement of components within the cavities enhances electrical performance by minimizing signal trace lengths and mitigating electromagnetic interference.
Versatile Applications: Cavity PCBs find application in scenarios where considerations such as space limitations, weight constraints, or specific performance criteria are paramount, such as in aerospace, medical devices, or high-performance electronic devices.
It’s important to stay abreast of the dynamic landscape of electronics and PCB design by consulting recent literature, industry standards, or engaging with professionals in the field for the latest developments in Cavity PCBs or related technologies.
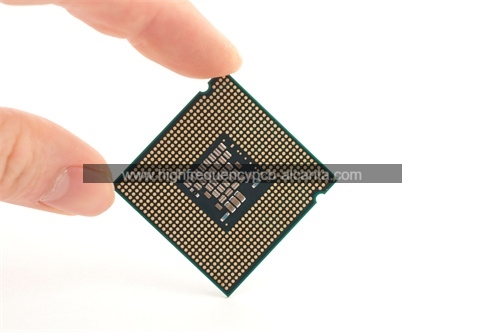
Cavity PCB Manufacturer
What Functions Does Cavity PCB Serve?
Cavity PCBs serve a range of functions that surpass the capabilities of traditional printed circuit boards. Thanks to their embedded cavity structures, these boards fulfill essential roles:
Improved Heat Dissipation: The embedded hollow spaces in Cavity PCBs are crafted to host materials that optimize the dissipation of heat. This results in a notable enhancement of the thermal performance in electronic devices, actively reducing operational temperatures and bolstering overall reliability.
Component Isolation: Cavity PCBs enable the segregation of different components into distinct cavities. This separation minimizes mutual interference among components, elevating the overall performance and dependability of the electronic system. It ensures the efficient functioning of individual components without compromising overall system integrity.
Creative Design Space: The incorporation of cavities offers designers a heightened level of freedom in arranging components. This flexibility allows for innovative design solutions, resulting in a more compact and seamlessly integrated final product. Designers can optimize component placement to maximize space utilization and enhance overall system efficiency.
In essence, Cavity PCBs provide advantages in thermal management, component isolation, and design adaptability, making them well-suited for applications where these features are paramount. This includes high-performance electronic devices, aerospace systems, and various specialized applications.
What Types of Cavity PCB Exist?
Cavity PCBs exhibit diverse types, categorized according to their design nuances and application domains. These categories encompass:
Heat-dissipating Cavity PCBs: Crafted with a central focus on enhancing heat dissipation, these PCBs are ideal for applications that demand high-power electronic devices. The strategically designed embedded cavities serve as purposeful enclosures for materials adept at efficiently dissipating heat. This meticulous design ensures superior thermal management, mitigating the risk of overheating in demanding electronic systems.
Functional Cavity PCBs: Tailored to meet specific functional requirements, this particular PCB variant excels in adapting to a wide range of functionalities. To illustrate, it can be finely adjusted for optimal performance in RF (radio frequency) applications, guaranteeing precise transmission and reception of signals. On the other hand, it can also be configured to seamlessly integrate sensors, thereby augmenting the board’s capabilities for sensing and data acquisition.
Hybrid Cavity PCBs: This category represents a versatile class of Cavity PCBs that amalgamate diverse characteristics to address a spectrum of engineering needs. By combining features from heat-dissipating and functional cavity designs, hybrid Cavity PCBs offer a comprehensive solution that can adapt to a variety of applications. This flexibility makes them suitable for complex electronic systems where multiple requirements need to be met simultaneously.
In essence, the classification of Cavity PCBs into these types underscores their adaptability to specific design goals and application scenarios, catering to the diverse and evolving needs of the electronics industry.
How Does Cavity PCB Integrate with IC Packaging Technology?
Cavity PCB seamlessly integrates with IC (Integrated Circuit) packaging technology, forming a symbiotic relationship. Their deep integration and innovative design collectively contribute to enhancing the performance of electronic devices. Cavity PCB, with its embedded hollow structures, and chip packaging technology complement each other in the following ways:
Optimized Design Space: Cavity PCBs offer additional design space within their embedded hollow structures. This extra space allows for more efficient layout and integration of components, providing designers with flexibility and opportunities for innovative configurations. This optimization is crucial in achieving high performance in electronic devices.
Improved Heat Dissipation:Incorporating cavity structures into PCBs facilitates the inclusion of materials that significantly improve heat dissipation. This proves particularly advantageous for electronic devices characterized by densely packed components or high-power demands. Effective heat dissipation becomes paramount in preserving optimal operating temperatures and guaranteeing the reliability of integrated circuits.
Enhanced Potential in Confined Spaces: The collaboration between Cavity PCB and chip packaging technology enables integrated circuits to unleash greater potential even within smaller spaces. This is essential for compact electronic devices where size constraints are significant, such as in mobile devices, wearables, or other portable electronics.
In summary, the integration of Cavity PCB with IC packaging technology enhances the overall performance of electronic devices by providing optimized design space and improved heat dissipation. This collaboration is particularly valuable in the development of smaller and more powerful electronic devices, meeting the demands of modern technology.
How Does Cavity PCB Differ from Traditional PCBs?
Cavity PCB stands apart from conventional Printed Circuit Boards (PCBs) with its distinctive structural and application variances:
Incorporation of Cavity Structures: Cavity PCB sets itself apart by integrating cavity structures into its design. These hollow spaces broaden its applications in electronic engineering, presenting unique possibilities for specialized designs that go beyond the capabilities of traditional PCBs.
Revolutionizing Motherboard Design: Cavity PCB introduces a new dimension to motherboard design, breaking away from the limitations of traditional PCBs. This forward-thinking approach enhances the overall performance of electronic devices by providing a platform for imaginative and efficient component layouts.
Contrast with Substrate-like PCB (SLP): While Cavity PCB shares structural similarities with Substrate-like PCB (SLP), the incorporation of cavities serves as a distinctive feature. These hollow spaces in Cavity PCBs empower a more functional and flexible design, allowing for the integration of additional components, heat-dissipating materials, or other elements that contribute to heightened performance.
In essence, Cavity PCBs redefine electronic engineering by embracing cavity structures, introducing novel opportunities for specialized designs, especially in the realm of motherboard innovation.
What is the Structure and Production Technology of Cavity PCB?
Structure:
Cavity PCB is characterized by a core structure that melds the traditional printed circuit board with strategically embedded cavities. Designers need a nuanced comprehension of how cavities impact circuit performance in Cavity PCBs. These hollow spaces aren’t just structural elements; they function as integral components, introducing a three-dimensional dimension to the traditional flat PCB architecture. This sophisticated design facilitates the integration of diverse elements, including components, materials for heat dissipation, or other essential functionalities.
Manufacturing Technology:
The manufacturing technology behind Cavity PCB involves sophisticated processes, with a primary focus on advancing High-Density Interconnect (HDI) manufacturing and adopting semi-additive methods. HDI technology brings forth increased component density and finer trace routing, optimizing the utilization of space within the embedded cavities. Semi-additive methods ensure a meticulous and controlled deposition of materials, guaranteeing the creation of intricate structures. Through these advanced manufacturing techniques, Cavity PCBs are produced with precision and reliability, aligning with the stringent requirements of contemporary electronics.
In essence, the structure of Cavity PCB seamlessly integrates embedded cavities, demanding a profound understanding of their impact on circuit performance. The manufacturing processes, driven by HDI and semi-additive methods, reflect a commitment to precision and quality, making Cavity PCBs well-suited for applications where intricate design and optimal performance are paramount.
FAQs about Cavity PCB
What defines a Cavity PCB?
A Cavity PCB, or Cavity Printed Circuit Board, is characterized by its unique design featuring embedded cavity structures. These hollow spaces serve diverse functions such as accommodating components, improving heat dissipation, and enhancing overall integration.
How does Cavity PCB differ from traditional PCBs?
Cavity PCB sets itself apart from traditional counterparts by integrating hollow structures. This distinctive feature opens avenues for creative layouts, efficient heat dissipation, and improved performance, making it well-suited for applications with specific and unique requirements.
What purposes do Cavity PCBs serve?
Cavity PCBs serve multiple functions, including superior heat dissipation, reduced interference through component isolation, and the provision of innovative design space for more streamlined and integrated solutions. These functionalities make them valuable in applications demanding specific performance attributes.
What types of Cavity PCBs are available?
Cavity PCBs can be classified based on their design and applications. Examples include heat-dissipating Cavity PCBs focused on thermal management, functional Cavity PCBs customized for specific needs like RF applications or sensor integration, and hybrid Cavity PCBs combining various characteristics to meet diverse engineering requirements.
How does Cavity PCB mesh with IC packaging technology?
Cavity PCB seamlessly integrates with IC (Integrated Circuit) packaging technology, enhancing overall device performance. This collaboration optimizes design space, improves heat dissipation, and allows integrated circuits to achieve their full potential, even in confined spaces.
What manufacturing technologies are involved in Cavity PCB production?
Cavity PCB manufacturing utilizes advanced techniques, including High-Density Interconnect (HDI) processes and semi-additive methods. These approaches ensure the precise creation of structures within the PCB, ensuring high-quality production that aligns with the demands of modern electronics.
What Significance Does Cavity PCB Hold for the Future of Electronic Engineering?
Cavity PCB emerges as a pioneering technology in electronic engineering, charting a course toward a future marked by innovative designs and high-performance electronic devices. Its forward-looking significance is underscored by its deep integration capabilities and the transformative impact of its inventive design.
Within the realm of electronic engineering, Cavity PCB serves as a catalyst for a new wave of possibilities. The incorporation of embedded cavity structures provides designers with a dynamic platform, fostering creative and efficient component layouts. Beyond mere spatial optimization, this approach elevates the overall performance benchmarks of electronic devices.
Looking forward, Cavity PCB is poised to be a linchpin in shaping the future of electronic engineering. Its capacity to host diverse functionalities within the embedded cavities, whether for heat dissipation or specialized components, contributes to the evolution of more compact and seamlessly integrated solutions. This aligns with the burgeoning demand for electronics that are not only smaller but also more potent and resource-efficient.
As the electronic engineering landscape undergoes transformation, Cavity PCB is set to play a pivotal role in advancing technologies across various industries. From aerospace applications to medical devices, its adaptability positions it as a driving force behind innovation.
In essence, the significance of Cavity PCB for the future lies in its potential to inspire creativity, streamline efficiency, and elevate performance standards. As we embrace this technology, we collectively embark on a journey to explore and unlock the myriad possibilities it holds for the next era of electronic devices and systems.