Buried Cavity Package Substrate Manufacturer
Buried Cavity Package Substrate Manufacturer,Buried Cavity Package Substrates (BCPS) revolutionize semiconductor packaging with their innovative design. Featuring a substrate with a concealed cavity, BCPS technology optimizes thermal dissipation and electrical performance. This advanced packaging solution enhances the reliability and efficiency of high-frequency and high-power semiconductor devices. By strategically positioning the cavity within the substrate, BCPS minimizes parasitic capacitance and inductance, ensuring superior signal integrity. The multi-layered structure enables compact integration of components, making BCPS ideal for space-constrained applications like mobile devices and IoT devices. Manufactured through precise fabrication processes and stringent quality control measures, BCPS delivers exceptional performance and reliability. With its ability to mitigate heat buildup and signal distortion, BCPS stands as a cornerstone in enabling next-generation semiconductor products that push the boundaries of technology and innovation.
What is a Buried Cavity Package Substrate?
A Buried Cavity Package Substrate (BCPS) is a specialized type of packaging technology used in semiconductor devices, particularly in integrated circuits (ICs). It is designed to provide enhanced performance and reliability for high-frequency and high-power applications.
At its core, a BCPS consists of a multi-layered substrate with a cavity or void buried within its structure. This cavity is typically created using advanced manufacturing processes such as laser drilling or chemical etching. The cavity is strategically positioned within the substrate to optimize its electrical and thermal properties.
One of the primary advantages of a BCPS is its ability to provide improved thermal management. By having a void within the substrate, heat generated by the IC can be more efficiently dissipated through the substrate material. This helps to prevent overheating of the device, which can degrade performance and reliability.
Additionally, the design of a BCPS allows for better signal integrity and electrical performance. The buried cavity helps to minimize parasitic capacitance and inductance, reducing signal distortion and improving overall device efficiency. This makes BCPS particularly well-suited for high-frequency applications where signal integrity is critical.
Furthermore, BCPS technology enables higher levels of integration and miniaturization. By optimizing the layout and design of the substrate, more components can be packed into a smaller footprint, leading to smaller and more compact devices. This is especially beneficial for applications where space is limited, such as in mobile devices and IoT (Internet of Things) devices.
Overall, the use of Buried Cavity Package Substrates offers numerous advantages for semiconductor devices, including improved thermal management, enhanced electrical performance, and greater integration capabilities. As technology continues to advance, BCPS is expected to play an increasingly important role in enabling next-generation semiconductor products.
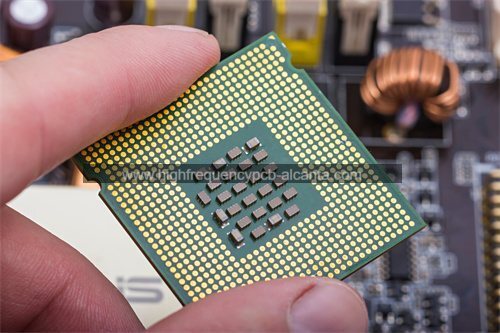
Buried Cavity Package Substrate Manufacturer
What are the BCPS Design Guidelines?
Designing with Buried Cavity Package Substrates (BCPS) requires careful consideration of several key factors to ensure optimal performance and reliability. While specific guidelines may vary depending on the application and manufacturer, some common design principles include:
- Thermal Management: Efficient thermal management is critical for BCPS designs. The buried cavity within the substrate helps dissipate heat, but proper thermal vias and heat spreaders should be incorporated into the design to ensure effective heat transfer away from the IC. Thermal simulations and analysis should be conducted to optimize the placement and design of these elements.
- Signal Integrity: Maintaining signal integrity is essential, especially in high-frequency applications. Minimizing parasitic capacitance and inductance is crucial for achieving low signal distortion and high-speed performance. Careful routing of signal traces, ground planes, and power planes is necessary to minimize signal losses and electromagnetic interference (EMI).
- Power Delivery: Providing stable and clean power to the IC is essential for reliable operation. Proper power distribution network (PDN) design, including decoupling capacitors and power planes, helps ensure low noise and adequate power delivery to the device. Power integrity analysis should be performed to validate the PDN design and optimize its performance.
- Mechanical Stability: BCPS designs should be mechanically robust to withstand various environmental stresses, including mechanical shock, vibration, and thermal cycling. Proper mechanical support structures, such as stiffeners and underfill materials, should be employed to enhance the package’s mechanical stability and reliability.
- Manufacturability: Design for manufacturability (DFM) considerations are essential to ensure the BCPS can be reliably manufactured at scale. Design features such as minimum feature sizes, aspect ratios, and tolerances should be carefully chosen to align with the capabilities of the manufacturing process. Collaboration between design and manufacturing teams is crucial to address any potential manufacturability issues early in the design phase.
- Cost Considerations: While optimizing performance and reliability is important, cost considerations also play a significant role in BCPS design. Balancing performance requirements with cost-effective design choices, such as substrate materials, layer count, and manufacturing processes, is essential to ensure the final product remains competitive in the market.
By following these design guidelines and principles, engineers can develop BCPS designs that meet the performance, reliability, and cost requirements of their specific applications. Collaboration between design, thermal, mechanical, and manufacturing teams is key to successfully implementing BCPS technology in semiconductor devices.
What is the BCPS Fabrication Process?
The fabrication process of Buried Cavity Package Substrates (BCPS) involves several complex steps to create the specialized substrate structure with a buried cavity. While specific details may vary depending on the manufacturer and technology used, a typical BCPS fabrication process involves the following key steps:
- Substrate Preparation: The process begins with the preparation of a substrate material, which is typically a high-performance material such as silicon, silicon carbide (SiC), or gallium arsenide (GaAs). The substrate is cleaned and polished to ensure a smooth and uniform surface.
- Cavity Formation: The next step involves creating a cavity or void within the substrate material. This can be achieved using advanced manufacturing techniques such as laser drilling, chemical etching, or micro-machining. The cavity is strategically positioned within the substrate to optimize thermal and electrical performance.
- Dielectric Layer Deposition: After the cavity is formed, a dielectric layer is deposited onto the substrate surface. This dielectric layer serves as an insulating barrier between the IC components and the substrate material, helping to prevent electrical shorts and signal interference.
- Conductor Deposition: Thin film conductive layers, typically made of metals such as copper or aluminum, are deposited onto the substrate surface. These conductive layers are patterned to create the necessary interconnects, signal traces, and power distribution lines for the IC components.
- Via Formation: Vias, which are vertical interconnects that penetrate through the substrate layers, are created to facilitate electrical connections between different layers of the substrate. Vias are typically formed using processes such as laser drilling or reactive ion etching (RIE).
- Lamination and Bonding: Multiple substrate layers, each containing conductive traces and dielectric materials, are laminated together to form a multi-layered structure. The layers are bonded using processes such as adhesive bonding or thermocompression bonding to create a monolithic substrate with integrated interconnects.
- Surface Finishing: The surface of the BCPS is finished to ensure flatness and smoothness, which is crucial for subsequent assembly processes. Surface finishing techniques may include chemical mechanical polishing (CMP) or mechanical grinding and polishing.
- Quality Control and Testing: Throughout the fabrication process, quality control measures are implemented to ensure the integrity and reliability of the BCPS. Various inspection and testing techniques, including optical microscopy, electrical testing, and thermal analysis, are performed to validate the substrate’s performance and adherence to specifications.
By following these fabrication steps, manufacturers can produce BCPS substrates with the desired electrical, thermal, and mechanical properties for use in high-performance semiconductor devices. Continuous advancements in fabrication technology and process refinement contribute to further improving the performance and reliability of BCPS substrates.
How do you manufacture a BCPS?
Manufacturing a Buried Cavity Package Substrate (BCPS) involves a series of intricate processes that require precision and expertise. Below is a detailed overview of the typical steps involved in manufacturing a BCPS:
- Substrate Selection: The manufacturing process begins with selecting a suitable substrate material, which is often a high-performance semiconductor material like silicon, silicon carbide (SiC), or gallium arsenide (GaAs). The substrate material should possess the desired electrical, thermal, and mechanical properties to meet the requirements of the intended application.
- Substrate Preparation: The selected substrate material undergoes thorough cleaning and polishing to ensure a clean and smooth surface. Any impurities or contaminants are removed to prevent defects in the final BCPS.
- Cavity Formation: A cavity or void is created within the substrate material using advanced fabrication techniques. Common methods for forming the cavity include laser drilling, chemical etching, or micro-machining. The size, shape, and position of the cavity are precisely controlled to optimize thermal management and electrical performance.
- Dielectric Layer Deposition: After the cavity is formed, a dielectric layer is deposited onto the substrate surface. This dielectric layer serves as an insulating barrier between the conductive traces and the substrate material, preventing electrical shorts and signal interference.
- Conductor Deposition: Thin film conductive layers, typically made of metals like copper or aluminum, are deposited onto the substrate surface. These conductive layers are patterned using photolithography and etching techniques to create the necessary interconnects, signal traces, and power distribution lines for the IC components.
- Via Formation: Vias, which are vertical interconnects that penetrate through the substrate layers, are formed to facilitate electrical connections between different layers of the substrate. Vias are typically created using processes such as laser drilling or reactive ion etching (RIE).
- Lamination and Bonding: Multiple substrate layers, each containing conductive traces and dielectric materials, are laminated together to form a multi-layered structure. The layers are bonded using techniques such as adhesive bonding or thermocompression bonding to create a monolithic substrate with integrated interconnects.
- Surface Finishing: The surface of the BCPS is finished to ensure flatness and smoothness, which is crucial for subsequent assembly processes. Surface finishing techniques such as chemical mechanical polishing (CMP) or mechanical grinding and polishing are employed to achieve the desired surface quality.
- Quality Control and Testing: Throughout the manufacturing process, rigorous quality control measures are implemented to ensure the integrity and reliability of the BCPS. Various inspection and testing techniques, including optical microscopy, electrical testing, and thermal analysis, are performed to validate the substrate’s performance and adherence to specifications.
By following these manufacturing steps with precision and attention to detail, manufacturers can produce high-quality BCPS substrates suitable for use in advanced semiconductor devices. Continuous refinement of manufacturing processes and technologies contributes to further improving the performance and reliability of BCPS substrates.
How much should a BCPS cost?
The cost of a Buried Cavity Package Substrate (BCPS) can vary significantly depending on several factors, including the substrate material, manufacturing complexity, size, quantity, and additional features required for a specific application.
- Substrate Material: The choice of substrate material can have a significant impact on the cost of a BCPS. High-performance materials such as silicon, silicon carbide (SiC), or gallium arsenide (GaAs) typically command higher prices compared to more conventional materials.
- Manufacturing Complexity: The complexity of the BCPS fabrication process, including the number of layers, features, and the precision required, will influence the manufacturing cost. More complex designs with finer features and tighter tolerances may incur higher manufacturing costs.
- Size and Quantity: The size of the BCPS and the quantity ordered also affect the overall cost. Larger substrates or higher quantities typically result in economies of scale, leading to lower unit costs.
- Additional Features: Additional features such as integrated heat spreaders, advanced packaging technologies, or customized designs may increase the cost of a BCPS.
- Market Factors: Market demand, competition among suppliers, and fluctuations in raw material prices can all impact the overall cost of BCPS substrates.
Due to these variables, it’s challenging to provide a specific cost estimate for a BCPS without knowing the exact specifications and requirements of the application. Typically, BCPS solutions are priced on a per-unit basis, and costs can range from a few dollars to several hundred dollars per substrate, depending on the factors mentioned above.
For accurate pricing information, it’s recommended to consult with BCPS manufacturers or suppliers directly, providing detailed specifications and volume requirements for a customized quotation. Additionally, conducting a cost-benefit analysis considering performance, reliability, and other factors is essential to determine the value proposition of a BCPS solution for a specific application.
What is a BCPS base material?
The base material used for Buried Cavity Package Substrates (BCPS) varies depending on the specific requirements of the application and the desired properties of the substrate. Some common materials used as the base substrate for BCPS include:
- Semiconductor Grade Silicon: Silicon is a widely used substrate material in semiconductor manufacturing due to its excellent electrical properties, thermal conductivity, and availability. Semiconductor-grade silicon substrates are often used for BCPS applications where high performance and reliability are essential.
- Silicon Carbide (SiC): SiC is a semiconductor material known for its high thermal conductivity, wide bandgap, and excellent mechanical properties. SiC substrates are used in BCPS applications that require enhanced thermal management, high-power handling capabilities, and resistance to harsh environments.
- Gallium Arsenide (GaAs):GaAs is another semiconductor material commonly used in BCPS applications, particularly in high-frequency and optoelectronic devices. GaAs substrates offer high electron mobility and low noise characteristics, making them suitable for RF and microwave applications.
- Ceramic Substrates: Ceramic materials such as aluminum oxide (Al2O3) or aluminum nitride (AlN) are used as base substrates for BCPS in some applications. Ceramic substrates offer excellent thermal conductivity, mechanical strength, and reliability, making them suitable for high-power and high-temperature environments.
- Glass Substrates: Glass substrates, including borosilicate glass or fused silica, are used in specialized BCPS applications where optical transparency, low thermal expansion, and high chemical resistance are required.
The selection of the base material for a BCPS depends on various factors such as electrical performance, thermal management requirements, mechanical stability, and cost considerations. Additionally, the fabrication process and compatibility with other materials used in the BCPS structure also influence the choice of substrate material. Ultimately, the base material is chosen to optimize the performance, reliability, and manufacturability of the BCPS for its intended application.
Which company makes BCPS?
Many semiconductor manufacturers and electronic component suppliers offer Buried Cavity Package Substrate (BCPS) technology and solutions. These companies include well-known semiconductor manufacturers, packaging service providers, and companies specializing in advanced packaging technologies. Some famous BCPS manufacturers include Intel, TSMC, Samsung Electronics, NXP Semiconductors, and others.
As a company focused on electronic packaging and semiconductor solutions, we also have the capability to produce BCPS. We have advanced process technologies and a professional team capable of designing, developing, and manufacturing high-performance BCPS products to meet customers’ requirements for high frequency, high power, low loss, and high reliability.
Our BCPS manufacturing process employs advanced manufacturing processes and strict quality control standards to ensure products have excellent electrical performance, thermal management capabilities, and mechanical stability. We can also customize BCPS products according to customers’ specific requirements, providing personalized solutions to help customers achieve performance and cost advantages for their products.
Additionally, we work closely with supply chain partners to ensure high-quality raw materials and components are obtained, and optimize production processes to improve production efficiency and delivery speed. Through continuous technological innovation and quality improvement, we aim to be one of the leading suppliers in the BCPS field, providing customers with reliable products and excellent services.
What are the 7 qualities of good customer service?
The 7 qualities of good customer service include:
Certainly! Here are the seven qualities of good customer service:
- Responsiveness: A good customer service team responds promptly to customer inquiries, concerns, and requests. They acknowledge customer communication in a timely manner and strive to provide solutions or assistance promptly.
- Empathy: Empathy involves understanding and sharing the feelings of customers. Good customer service representatives demonstrate empathy by listening attentively to customer concerns, showing understanding of their perspectives, and expressing genuine concern for their needs.
- Clear Communication:Effective communication is essential for good customer service. Customer service representatives should communicate clearly and concisely, using language that is easy for customers to understand. They should also provide accurate and relevant information to address customer inquiries or resolve issues.
- Product Knowledge: Good customer service requires a thorough understanding of the products or services offered by the company. Customer service representatives should be knowledgeable about the features, benefits, and specifications of the products/services they support, allowing them to answer customer questions and provide valuable guidance.
- Problem-solving Skills: Customers often reach out to customer service when they encounter problems or issues. Good customer service representatives possess strong problem-solving skills, enabling them to analyze situations, identify root causes of problems, and implement effective solutions to resolve customer issues satisfactorily.
- Professionalism: Professionalism encompasses a range of behaviors and attributes, including politeness, respectfulness, and integrity. Good customer service representatives conduct themselves professionally at all times, maintaining a positive attitude, treating customers with courtesy and respect, and adhering to company policies and standards.
- Follow-up and Follow-through: Providing good customer service doesn’t end with resolving an immediate issue. It also involves following up with customers to ensure their needs have been met and their concerns addressed satisfactorily. Good customer service representatives demonstrate commitment by following through on promises, providing updates as needed, and proactively reaching out to customers to ensure their satisfaction.
By embodying these qualities, companies can deliver exceptional customer service experiences that foster customer loyalty, satisfaction, and positive brand perception.
FAQs
What is a Buried Cavity Package Substrate (BCPS)?
A BCPS is a specialized type of packaging technology used in semiconductor devices, featuring a substrate with a buried cavity or void within its structure. It is designed to enhance thermal management, signal integrity, and integration capabilities in high-performance semiconductor applications.
What are the advantages of BCPS?
BCPS offers several advantages, including improved thermal management, enhanced signal integrity, higher levels of integration, and greater reliability. The buried cavity within the substrate helps dissipate heat more efficiently and reduces parasitic capacitance and inductance, leading to better electrical performance.
What applications are suitable for BCPS?
BCPS is well-suited for a wide range of high-frequency, high-power, and high-reliability semiconductor applications. These include RF and microwave devices, power amplifiers, power modules, RF transceivers, radar systems, and automotive electronics, among others.
How is BCPS manufactured?
The manufacturing process of BCPS involves several steps, including substrate preparation, cavity formation, dielectric layer deposition, conductor deposition, via formation, lamination and bonding, surface finishing, and quality control and testing. Advanced fabrication techniques and strict quality control measures are employed to ensure the performance and reliability of BCPS.
What materials are used in BCPS?
BCPS can be fabricated using various substrate materials, including semiconductor-grade silicon, silicon carbide (SiC), gallium arsenide (GaAs), ceramic materials (e.g., aluminum oxide, aluminum nitride), and glass substrates (e.g., borosilicate glass, fused silica), depending on the specific requirements of the application.
What factors affect the cost of BCPS?
The cost of BCPS can vary depending on factors such as substrate material, manufacturing complexity, size, quantity, and additional features required for the application. High-performance materials and complex designs may incur higher costs, while economies of scale and standardization can help lower costs.
Where can I find BCPS products or services?
BCPS solutions are offered by semiconductor manufacturers, packaging service providers, and companies specializing in advanced packaging technologies. Researching and contacting reputable suppliers or consulting with industry experts can help identify suitable BCPS products or services for specific application requirements.