BT Resin Substrate Manufacturing
BT Resin Substrate Manufacturing,BT resin substrate is a high-performance material used in electronic packaging and printed circuit boards (PCBs). It is composed of reinforcing materials, such as glass fiber or aramid fiber, with excellent mechanical strength and stability, combined with bismaleimide triazine (BT) resin known for its high-temperature stability. BT resin substrate features low dielectric constant, excellent electrical properties, and outstanding high-frequency performance, making it widely utilized in high-frequency applications. It efficiently transmits high-speed digital signals and high-frequency signals while providing good dimensional stability and reliability. BT resin substrate finds applications in various fields including telecommunications equipment, microwave devices, and high-speed digital systems. Its superior performance and reliability make it an ideal choice for designing and manufacturing advanced electronic systems.
What is a BT Resin Substrate?
BT resin substrate typically refers to a type of resin-based material used in electronic packaging and printed circuit boards (PCBs). The term “BT” stands for “bismaleimide triazine,” which is a type of thermoset resin known for its high-temperature stability, low dielectric constant, and excellent electrical properties.
BT resin substrates are commonly used in high-frequency applications, such as telecommunications equipment, microwave devices, and high-speed digital systems. They offer good dimensional stability, mechanical strength, and reliability, making them suitable for demanding electronic applications where performance and durability are critical.
These substrates are often used in multilayer PCBs where high-frequency signals and high-speed data transmission are required. The use of BT resin substrates helps ensure signal integrity and minimizes signal loss due to its low dielectric constant and low loss tangent properties. Additionally, BT resin substrates can withstand the high temperatures encountered during soldering processes, making them suitable for lead-free assembly techniques.
Overall, BT resin substrates play a vital role in the design and manufacturing of advanced electronic systems, particularly those requiring high performance, reliability, and stability under harsh operating conditions.
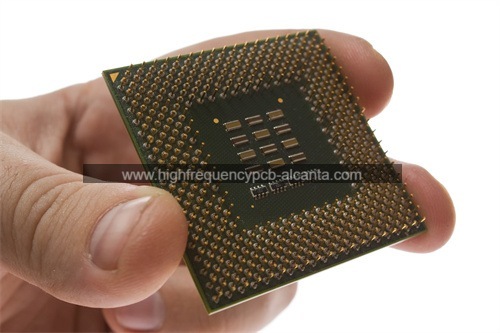
BT Resin Substrate Manufacturing
What are the BT Resin Substrate Design Guidelines?
Design guidelines for BT resin substrates typically include recommendations and considerations for designing printed circuit boards (PCBs) using BT resin-based materials. These guidelines aim to ensure optimal performance, reliability, and manufacturability of electronic systems. Some common design guidelines for BT resin substrates include:
- Thermal Management: BT resin substrates have good thermal stability, but it’s still important to consider thermal management in PCB design. Properly designed thermal vias, heatsinks, and thermal pads can help dissipate heat effectively, preventing overheating of components.
- Signal Integrity: Designing for signal integrity is crucial, especially in high-frequency applications. Considerations such as controlled impedance routing, minimizing signal reflections, and reducing crosstalk are essential for maintaining signal integrity on BT resin substrates.
- High-Speed Design: For high-speed digital systems, careful attention should be given to signal integrity, transmission line effects, and impedance matching. Techniques such as differential signaling, length matching, and proper termination are important for minimizing signal distortion and ensuring reliable data transmission.
- Power Delivery: Ensure adequate power delivery and distribution throughout the PCB. Proper placement of power planes, decoupling capacitors, and power distribution networks helps to minimize voltage drops and ensure stable power supply to components.
- Component Placement: Optimize component placement to minimize signal interference, thermal issues, and routing complexities. Group related components together and place critical components strategically to minimize signal paths and reduce EMI/RFI effects.
- Manufacturability: Consider manufacturability aspects such as panelization, solder mask design, and pad sizes to facilitate PCB fabrication and assembly processes. Ensure that design features comply with manufacturer’s capabilities and industry standards to avoid manufacturing issues.
- Environmental Considerations: Factor in environmental conditions such as temperature, humidity, and vibration when designing PCBs with BT resin substrates. Choose materials and design features that can withstand the intended operating environment to ensure long-term reliability.
- Compliance and Certification: Ensure that the PCB design meets relevant industry standards and regulatory requirements. Considerations such as RoHS compliance, UL certification, and EMC/EMI compliance may be necessary depending on the intended application and market.
These guidelines serve as a foundation for designing PCBs using BT resin substrates, helping designers achieve optimal performance, reliability, and manufacturability of electronic systems. It’s important to consult with material suppliers, PCB manufacturers, and design experts to ensure that design practices align with best practices and industry standards.
What is the BT Resin Substrate Fabrication Process?
The fabrication process for BT resin substrates involves several steps to manufacture printed circuit boards (PCBs) using BT resin-based materials. While specific processes may vary depending on the manufacturer and the desired specifications of the PCB, the general steps involved in BT resin substrate fabrication are as follows:
- Substrate Preparation: The fabrication process typically starts with the preparation of the substrate material, which is often a laminate consisting of layers of woven glass fiber impregnated with BT resin. The substrate material may come in sheets or panels of various thicknesses and dimensions.
- Layer Alignment:If the PCB design involves multiple layers, the individual layers of substrate material are aligned and stacked together according to the design specifications. Alignment is critical to ensure proper registration of circuitry and vias across the different layers.
- Circuit Patterning: The circuit patterns, including traces, pads, vias, and other features, are transferred onto the substrate material using a process such as photolithography or direct imaging. This step typically involves applying a layer of photoresist material onto the substrate, exposing it to UV light through a photomask, and developing the exposed areas to reveal the desired circuit patterns.
- Etching: After patterning, the substrate undergoes an etching process to remove unwanted copper from the substrate surface, leaving behind the desired circuit traces and features. Chemical etchants are commonly used to selectively dissolve the exposed copper, leaving the circuit patterns intact.
- Through-Hole Plating: If the PCB design includes vias that penetrate through multiple layers of the substrate, a through-hole plating process is performed to metallize the vias and establish electrical connections between the different layers. This process typically involves electroplating copper onto the walls of the vias, followed by a chemical deposition of a thin layer of metal to enhance conductivity.
- Surface Finishing: Surface finishing is applied to protect the exposed copper surfaces from oxidation and to facilitate soldering during assembly. Common surface finishes for BT resin substrates include HASL (hot air solder leveling), ENIG (electroless nickel immersion gold), and immersion silver.
- Drilling: Holes for component mounting and through-hole vias are drilled into the substrate using precision drilling equipment. Advanced drilling techniques may be employed to achieve tight tolerances and high aspect ratios for vias in high-density PCB designs.
- Final Inspection: The fabricated PCB undergoes thorough inspection to ensure that it meets the required quality standards and design specifications. This may include visual inspection, electrical testing, and dimensional measurements to verify the integrity and functionality of the circuitry.
- Routing and Profiling: After inspection, the individual PCBs are separated from the panel or sheet and routed to remove excess material around the board edges. This process, known as profiling, gives the PCB its final shape and dimensions.
- Quality Assurance and Packaging: The finished PCBs are subjected to final quality assurance checks to ensure compliance with customer requirements and industry standards. Once approved, the PCBs are packaged and prepared for shipment to the customer or assembly facility.
Overall, the fabrication process for BT resin substrates involves a combination of precision manufacturing techniques and quality control measures to produce high-quality PCBs with excellent performance and reliability. Collaboration between PCB designers, fabricators, and assembly partners is essential to optimize the fabrication process and meet the specific requirements of each application.
How do you manufacture a BT Resin Substrate?
Manufacturing a BT resin substrate involves several steps to produce the laminate material used in printed circuit boards (PCBs). Here is an overview of the manufacturing process for BT resin substrates:
- Material Preparation: The manufacturing process begins with the preparation of the raw materials. The primary components include bismaleimide triazine (BT) resin, reinforcing materials such as woven glass fiber or non-woven aramid fiber, and additives such as curing agents and fillers. These materials are carefully measured and mixed according to specific formulations.
- Resin Impregnation: The reinforcing materials, typically in the form of woven or non-woven fabric sheets, are impregnated with the BT resin mixture. This impregnation process ensures that the resin thoroughly saturates the fibers, forming a uniform and homogenous mixture.
- Lamination: The impregnated fiber sheets are stacked together to form a multi-layered laminate structure. Each layer may have a different fiber orientation to provide desired mechanical properties such as strength and dimensional stability. The laminate stack is then placed in a hydraulic press and subjected to heat and pressure to bond the layers together and cure the resin. This lamination process may involve multiple cycles of heating and pressing to achieve the desired thickness and properties.
- Curing: The laminate undergoes a curing process to cross-link the resin molecules and create a thermoset material. Curing is typically carried out in a controlled environment, such as a heated press or oven, at elevated temperatures and pressures for a specific duration. This step ensures that the resin reaches its full strength and stability.
- Post-Cure Treatment: After curing, the laminate may undergo post-cure treatment to further enhance its properties. This may involve additional heating or cooling cycles to optimize the material’s performance, such as improving dimensional stability or reducing moisture absorption.
- Surface Treatment: Depending on the application requirements, the surface of the BT resin substrate may undergo treatment to enhance adhesion or solderability. This may include processes such as plasma treatment, chemical etching, or applying surface coatings.
- Quality Control: Throughout the manufacturing process, quality control measures are implemented to ensure that the BT resin substrate meets the required specifications and standards. This may involve testing the mechanical, thermal, and electrical properties of the material, as well as conducting visual inspections to detect any defects or inconsistencies.
- Cutting and Packaging: Once the BT resin substrate is manufactured and inspected, it is typically cut into sheets or panels of the desired dimensions. The finished substrate material is then packaged and prepared for shipment to PCB manufacturers or assembly facilities.
Overall, the manufacturing process for BT resin substrates involves precision handling of materials, controlled processing conditions, and rigorous quality control to produce high-quality laminate materials suitable for various electronic applications. Collaboration between material suppliers, manufacturers, and end-users is essential to ensure that the final product meets the specific requirements and performance criteria of each application.
How much should a BT Resin Substrate cost?
The cost of a BT resin substrate can vary depending on several factors such as the thickness, size, quality, and specific requirements of the substrate, as well as market conditions and supplier pricing. Generally, BT resin substrates tend to be more expensive compared to traditional FR-4 substrates due to the higher performance characteristics and specialized manufacturing processes involved.
On average, the cost of BT resin substrates ranges from several dollars per square foot to tens of dollars per square foot, with thicker and higher-quality substrates typically commanding higher prices. Customized or specialized substrates with unique features or properties may incur additional costs.
It’s important to consider not only the initial cost of the substrate but also factors such as long-term reliability, performance, and compatibility with the intended application. Additionally, bulk purchasing or long-term contracts with suppliers may provide opportunities for cost savings.
Ultimately, the cost of a BT resin substrate should be weighed against its performance, reliability, and suitability for the specific application to determine its overall value. Working closely with material suppliers and considering factors such as total cost of ownership can help ensure that you get the best value for your investment in BT resin substrates.
What is BT Resin Substrate Base Material?
The base material of a BT resin substrate refers to the foundational material used to create the substrate. In the context of electronic applications, including printed circuit boards (PCBs), BT resin substrates are typically composed of a laminate material.
The base material of a BT resin substrate laminate consists of reinforcing fibers, such as woven glass fiber or non-woven aramid fiber, impregnated with BT resin. The BT resin, also known as bismaleimide triazine, is a thermosetting polymer known for its high-temperature stability, low dielectric constant, and excellent electrical properties.
The reinforcing fibers provide mechanical strength and dimensional stability to the substrate, while the BT resin acts as a binder that holds the fibers together and provides the desired electrical properties. The combination of these materials results in a robust substrate material suitable for various electronic applications, including high-speed digital systems, telecommunications equipment, and microwave devices.
BT resin substrates are favored for their superior performance characteristics, including high-frequency signal integrity, thermal stability, and reliability. The base material composition and manufacturing process play a crucial role in determining the overall properties and performance of the BT resin substrate.
Which company makes BT Resin Substrate?
BT resin substrates are produced by several companies, including many electronic materials manufacturers and printed circuit board (PCB) manufacturers. These companies typically produce BT resin substrates in their factories using specialized equipment and processes to meet the needs of their customers.
The production of BT resin substrates typically involves several steps, including raw material preparation, pretreatment, stacking, pressing, curing, and surface treatment. The production process requires strict quality control and management to ensure that the produced substrates meet customer specifications and industry standards.
As a professional electronic materials manufacturer, our company also has the capability to produce BT resin substrates. We have advanced production equipment and a skilled technical team to customize BT resin substrates in various specifications and performance characteristics according to customer requirements.
The production process of BT resin substrates in our company includes raw material procurement, process optimization, quality control, and testing. We are committed to providing high-quality, reliable, and performance-stable BT resin substrate products to meet the needs of customers in the electronics industry.
Through continuous technological innovation and quality management, our company ensures that the produced BT resin substrates meet the strictest quality standards and industry requirements. Our team is dedicated to providing customized solutions for customers and working towards their success and satisfaction.
If you have any requirements or questions about the production of BT resin substrates, please feel free to contact us. We are committed to providing you with excellent service.
What are the 7 qualities of good customer service?
Good customer service is essential for building and maintaining positive relationships with customers. Here are seven qualities that contribute to effective customer service:
- Responsiveness: Responding promptly to customer inquiries, concerns, and requests demonstrates attentiveness and a commitment to addressing customer needs in a timely manner. Whether it’s answering phone calls, replying to emails, or assisting customers in person, being responsive shows that you value their time and prioritize their satisfaction.
- Empathy: Empathy involves understanding and relating to the emotions and perspectives of customers. It’s important to listen actively to their concerns, acknowledge their feelings, and show genuine empathy and understanding. By demonstrating empathy, customer service representatives can build trust and rapport with customers, leading to more positive interactions.
- Clarity: Providing clear and concise communication is essential for delivering effective customer service. Whether conveying information about products, policies, or procedures, clarity helps prevent misunderstandings and ensures that customers have the information they need to make informed decisions or resolve issues.
- Professionalism: Professionalism encompasses maintaining a courteous, respectful, and professional demeanor in all interactions with customers. This includes being polite, patient, and attentive to their needs, even in challenging or stressful situations. Professional behavior builds credibility and trust, enhancing the overall customer experience.
- Problem-solving skills: Effective customer service involves the ability to identify and resolve customer issues efficiently and effectively. Customer service representatives should be resourceful, proactive, and empowered to find solutions that meet or exceed customer expectations. Being able to navigate and resolve problems demonstrates competence and builds customer confidence.
- Personalization: Personalizing the customer experience involves recognizing and acknowledging individual customer preferences, histories, and needs. Tailoring interactions and recommendations to match the customer’s unique situation fosters a sense of value and appreciation. Personalization can be achieved through techniques such as using the customer’s name, referencing past interactions, and offering personalized recommendations or solutions.
- Follow-up and follow-through: Following up with customers after interactions and ensuring that any promises or commitments made are fulfilled demonstrates reliability and accountability. Whether it’s confirming that an issue has been resolved to the customer’s satisfaction or checking in to see if they need further assistance, follow-up shows that you value their feedback and are committed to their satisfaction.
By embodying these qualities, businesses can deliver exceptional customer service experiences that foster loyalty, satisfaction, and positive word-of-mouth recommendations.
FAQs
What is BT resin?
BT resin, short for bismaleimide triazine, is a type of thermoset resin known for its high-temperature stability, low dielectric constant, and excellent electrical properties. It is commonly used in electronic packaging and printed circuit boards (PCBs) for high-frequency applications.
What are BT resin substrates used for?
BT resin substrates are used in various electronic applications, including telecommunications equipment, microwave devices, high-speed digital systems, and other high-frequency circuits. They provide good dimensional stability, mechanical strength, and reliability, making them suitable for demanding electronic environments.
What are the advantages of BT resin substrates over other materials?
BT resin substrates offer several advantages, including high-temperature stability, low dielectric constant, excellent electrical properties, and good mechanical strength. They also have low moisture absorption and can withstand high-frequency signals without significant loss, making them ideal for high-performance electronic applications.
How are BT resin substrates manufactured?
BT resin substrates are typically manufactured through a process that involves impregnating reinforcing materials, such as woven glass fiber or non-woven aramid fiber, with BT resin. The impregnated materials are then laminated, cured, and processed to produce the final substrate material.
What are the design considerations for using BT resin substrates?
When designing PCBs using BT resin substrates, it’s important to consider factors such as thermal management, signal integrity, high-speed design, power delivery, component placement, manufacturability, and environmental considerations to ensure optimal performance and reliability.
Are BT resin substrates compatible with lead-free assembly processes?
Yes, BT resin substrates are compatible with lead-free assembly processes. They can withstand the high temperatures encountered during soldering and are suitable for various assembly techniques, including surface mount technology (SMT) and through-hole assembly.
Where can I purchase BT resin substrates?
BT resin substrates are available from various electronic materials manufacturers and PCB suppliers. You can contact these companies directly to inquire about product availability, specifications, and pricing.