BT PCB Manufacturer
BT PCB Manufacturer,A BT PCB (Bluetooth Printed Circuit Board) is a specialized circuit board designed specifically for enabling Bluetooth communication between electronic devices. It integrates components such as Bluetooth modules, antennas, microcontrollers, and other necessary circuitry to facilitate wireless connectivity between devices. BT PCBs find widespread applications in various electronic products such as wireless headphones, speakers, keyboards, mice, smartwatches, fitness trackers, and more, providing users with convenient Bluetooth connectivity. During the design and manufacturing process, BT PCBs require consideration of factors such as antenna layout, signal integrity, power consumption, size constraints, and compliance with Bluetooth standards and regulations. High-quality BT PCBs offer stable signal transmission, low power consumption, high performance, and reliability, serving as a solid foundation for wireless communication in electronic devices.
What is a BT PCB?
A BT PCB, or Bluetooth Printed Circuit Board, is a specialized type of circuit board designed to facilitate Bluetooth communicati
on between electronic devices. It typically consists of various components such as microcontrollers, antennas, Bluetooth modules, and other necessary circuitry arranged on a substrate material like fiberglass or polyimide.
The primary function of a BT PCB is to enable wireless communication between devices over short distances, typically within a range of 10 meters or so. This technology is widely used in various applications such as wireless headphones, speakers, keyboards, mice, smartwatches, and IoT devices.
The design of a BT PCB must take into account factors like signal integrity, power consumption, size constraints, and regulatory compliance. Engineers often optimize the layout and placement of components to ensure reliable and efficient Bluetooth connectivity while minimizing interference and maximizing battery life.
Overall, BT PCBs play a crucial role in enabling the seamless wireless connectivity that has become increasingly essential in modern electronics, allowing devices to communicate and interact with each other without the need for physical cables.
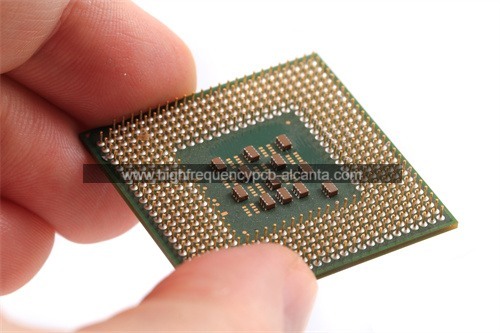
BT PCB Manufacturer
What are BT PCB Design Guidelines?
Bluetooth PCB design guidelines are a set of recommendations and best practices to ensure optimal performance and reliability of Bluetooth-enabled devices. These guidelines are crucial for engineers and designers working on Bluetooth PCBs to follow to achieve the desired functionality and compliance with Bluetooth standards. Here are some common Bluetooth PCB design guidelines:
- Antenna Placement: Proper placement of the Bluetooth antenna is critical for achieving good signal strength and range. Antennas should be positioned away from obstructions such as metal components and should have sufficient ground plane clearance.
- RF Trace Routing: RF traces carrying Bluetooth signals should be kept short, direct, and impedance-controlled to minimize signal loss and interference. Avoid crossing RF traces with high-speed digital signals or power lines to prevent signal degradation.
- Ground Plane Design: A solid ground plane beneath the RF circuitry helps to minimize electromagnetic interference (EMI) and maintain signal integrity. It’s essential to ensure a low-impedance ground plane for optimal RF performance.
- Decoupling Capacitors: Place decoupling capacitors close to the power pins of RF components to suppress noise and provide stable power supply voltage, especially during transmission bursts.
- Component Placement: Carefully place Bluetooth modules, microcontrollers, and other RF components to minimize signal reflections and interference. Keep sensitive components away from noisy components like switching regulators and high-speed digital circuits.
- Board Layout:Follow recommended layout guidelines provided by the Bluetooth module manufacturer or Bluetooth SIG (Special Interest Group). Pay attention to the location of critical components, signal traces, and antenna placement to ensure compliance with Bluetooth standards.
- Keepout Areas: Define keepout areas around the antenna and RF circuitry to prevent interference from nearby components or metal structures. Avoid placing conductive materials or components within these keepout zones.
- Power Supply Filtering: Use low-pass filters and ferrite beads on power supply lines to attenuate high-frequency noise and ripple that could degrade Bluetooth signal quality.
- Testing and Validation: Perform thorough testing and validation of the Bluetooth PCB design using RF test equipment to ensure compliance with Bluetooth standards and optimize performance.
- Regulatory Compliance: Ensure that the Bluetooth PCB design meets regulatory requirements for electromagnetic compatibility (EMC) and radio frequency (RF) emissions to obtain necessary certifications for commercial distribution.
By adhering to these Bluetooth PCB design guidelines, engineers can develop Bluetooth-enabled devices that offer robust wireless connectivity, reliable performance, and compliance with industry standards.
What is the BT PCB Fabrication Process?
The fabrication process for a BT (Bluetooth) PCB involves several steps to create the printed circuit board that will facilitate Bluetooth communication between electronic devices. Here’s an overview of the typical BT PCB fabrication process:
- Design: The process begins with the design of the PCB layout using computer-aided design (CAD) software. Engineers design the circuitry, including the Bluetooth module, antennas, microcontrollers, and other components, considering factors like signal integrity, power consumption, and size constraints.
- Gerber Files Generation: Once the PCB design is complete, Gerber files are generated. These files contain the necessary information about the PCB layout, including copper traces, drill holes, solder mask, and silkscreen layers.
- Material Selection: The appropriate substrate material for the PCB is selected based on factors such as dielectric constant, thermal properties, and cost. Common substrate materials for BT PCBs include fiberglass (FR4) and polyimide (PI).
- Preparation of Substrate: The chosen substrate material is prepared by cutting it to the required size and cleaning it to remove any contaminants that could affect the fabrication process.
- Copper Cladding: A thin layer of copper is laminated onto both sides of the substrate material using a process called electroless copper deposition or by bonding copper foil sheets to the substrate.
- Etching: A chemical etching process is used to remove excess copper from the substrate, leaving behind the desired copper traces that form the circuitry of the PCB.
- Drilling: Precision drilling machines are used to create holes in the PCB for through-hole components, vias, and mounting holes. These holes are plated with copper to provide electrical conductivity between layers if the PCB is multilayered.
- Solder Mask Application: A solder mask layer is applied over the surface of the PCB to protect the copper traces from oxidation and to define areas for soldering components. The solder mask is typically green, but other colors are also used for identification and aesthetic purposes.
- Silkscreen Printing: Information such as component labels, reference designators, and manufacturer logos are printed onto the PCB surface using a silkscreen printing process.
- Surface Finish: A surface finish is applied to the exposed copper surfaces of the PCB to protect them from oxidation and facilitate soldering during assembly. Common surface finishes include HASL (Hot Air Solder Leveling), ENIG (Electroless Nickel Immersion Gold), and OSP (Organic Solderability Preservatives).
- Testing: The fabricated PCBs undergo various tests, including electrical continuity testing, impedance testing, and functionality testing, to ensure they meet quality standards and function as intended.
- Assembly: Once the PCBs pass testing, they are ready for component assembly. Surface-mount and through-hole components are soldered onto the PCB using automated assembly equipment or by hand soldering, depending on the complexity of the design and production volume.
- Final Inspection: The assembled PCBs undergo a final inspection to verify the quality of solder joints, component placement, and overall functionality before being packaged and shipped to customers.
By following these steps, manufacturers can produce high-quality BT PCBs that meet performance requirements and enable reliable Bluetooth communication between electronic devices.
How do you manufacture a BT PCB?
Manufacturing a BT (Bluetooth) PCB involves a series of steps from design to assembly. Here’s a comprehensive overview of the manufacturing process:
- Design: Engineers design the circuit layout of the PCB using computer-aided design (CAD) software, considering factors such as signal integrity, component placement, and size constraints.
- Gerber Files Generation: Once the design is finalized, Gerber files containing the PCB layout information, including copper traces, drill locations, solder mask, and silkscreen details, are generated.
- Material Selection: The appropriate substrate material for the PCB is chosen based on factors like dielectric constant, thermal properties, and cost. Common materials include fiberglass (FR4) and polyimide (PI).
- Substrate Preparation: The substrate material is prepared by cutting it to the required size and cleaning it to remove any contaminants that could affect the manufacturing process.
- Copper Cladding: A thin layer of copper foil is bonded or laminated onto the substrate material on both sides. This copper layer forms the conductive traces of the PCB.
- Etching: A chemical etching process is used to remove excess copper from the substrate, leaving behind the desired copper traces that form the circuitry of the PCB.
- Drilling: Precision drilling machines are used to create holes in the PCB for through-hole components, vias, and mounting holes. These holes are plated with copper to provide electrical connectivity between layers in case of multilayered PCBs.
- Solder Mask Application: A solder mask layer is applied over the surface of the PCB to protect the copper traces from oxidation and to define areas for soldering components. The solder mask is typically green, but other colors are also used for identification and aesthetic purposes.
- Silkscreen Printing: Information such as component labels, reference designators, and manufacturer logos are printed onto the PCB surface using a silkscreen printing process for identification and assembly guidance.
- Surface Finish: A surface finish is applied to the exposed copper surfaces of the PCB to protect them from oxidation and facilitate soldering during component assembly. Common surface finishes include HASL (Hot Air Solder Leveling), ENIG (Electroless Nickel Immersion Gold), and OSP (Organic Solderability Preservatives).
- Testing: The fabricated PCBs undergo various tests, including electrical continuity testing, impedance testing, and functionality testing, to ensure they meet quality standards and function as intended.
- Component Assembly: Surface-mount and through-hole components are soldered onto the PCB using automated assembly equipment or by hand soldering, depending on the complexity of the design and production volume.
- Final Inspection: The assembled PCBs undergo a final inspection to verify the quality of solder joints, component placement, and overall functionality before being packaged and shipped to customers.
By following these steps, manufacturers can produce high-quality BT PCBs that enable reliable Bluetooth communication between electronic devices. Each step is crucial in ensuring the performance, reliability, and quality of the finished product.
How much should a BT PCB cost?
The cost of a BT (Bluetooth) PCB can vary significantly depending on various factors such as complexity, size, number of layers, materials used, manufacturing processes, and quantity ordered. Here are some factors to consider when estimating the cost of a BT PCB:
- Complexity: The complexity of the PCB design, including the number of components, density of traces, and sophistication of features, can impact the cost. More complex designs typically require advanced manufacturing processes and may incur higher costs.
- Size and Number of Layers: Larger PCBs with more layers tend to cost more due to the increased material and manufacturing complexity required. Multilayered PCBs, which have more than two layers, can be more expensive than single or double-layer PCBs.
- Materials: The choice of substrate material, copper thickness, and surface finish can affect the cost of the PCB. High-quality materials and finishes may command a higher price.
- Manufacturing Processes: Specialized manufacturing processes such as impedance control, blind/buried vias, and controlled depth drilling can add to the cost of the PCB.
- Quantity: Typically, the larger the quantity ordered, the lower the cost per unit. PCB manufacturers often offer volume discounts for bulk orders.
- Turnaround Time: Expedited or quick-turn manufacturing services may incur additional charges compared to standard lead times.
- Supplier: The choice of PCB manufacturer or supplier can also impact the cost. Different suppliers may offer different pricing structures, capabilities, and levels of service.
As a rough estimate, the cost of a basic single-layer BT PCB with a standard FR4 substrate, simple design, and standard lead time might range from a few dollars to tens of dollars per unit in low quantities. However, more complex or specialized BT PCBs can cost significantly more, potentially reaching hundreds of dollars per unit.
For accurate pricing, it’s best to consult with PCB manufacturers or suppliers directly, providing them with detailed specifications and requirements for your specific project. They can provide you with quotes based on your needs and volume requirements.
What is BT PCB base material?
The base material for a BT (Bluetooth) PCB, like most other printed circuit boards (PCBs), is typically a substrate made of a non-conductive material that provides mechanical support and insulation between the conductive layers of the PCB. The choice of base material depends on factors such as electrical performance, thermal properties, cost, and manufacturability.
Common base materials used for BT PCBs include:
- FR4 (Flame Retardant 4): FR4 is the most widely used substrate material for PCBs. It’s composed of woven fiberglass cloth impregnated with epoxy resin. FR4 offers good electrical insulation, mechanical strength, and thermal stability, making it suitable for a wide range of applications, including BT PCBs.
- Polyimide (PI): Polyimide is a flexible substrate material known for its excellent thermal stability and resistance to high temperatures. It’s commonly used in applications where flexibility or high-temperature resistance is required, such as flexible BT PCBs for wearables or devices with complex form factors.
- Rogers Materials: Rogers Corporation produces a range of high-performance substrate materials specifically designed for RF/microwave applications, including Bluetooth PCBs. These materials offer low dielectric constant (Dk) and low loss tangent (Df), making them ideal for high-frequency RF circuits.
- Metal Core (MCPCB): Metal core PCBs feature a metal core, usually aluminum or copper, sandwiched between layers of dielectric material. They offer excellent thermal conductivity and heat dissipation, making them suitable for applications requiring high power or heat management, such as LED lighting systems with Bluetooth control.
The choice of base material for a BT PCB depends on the specific requirements of the application, such as frequency of operation, thermal considerations, flexibility, and cost constraints. Designers must carefully select the appropriate base material to ensure the desired electrical performance, reliability, and manufacturability of the Bluetooth PCB.
Which company makes BT PCB?
Many companies can manufacture BT PCBs, including Foxconn, Orikon, Unimicron, and other electronics manufacturing companies. These companies have advanced manufacturing equipment and technologies to meet the needs of different customers, from small-scale to large-scale production.
For our company, we are also a professional electronics manufacturing company with the capability to produce BT PCBs. We have advanced production equipment and a skilled technical team to provide high-quality BT PCB solutions. Here are some advantages and capabilities of our company in producing BT PCBs:
- Technical Strength: We have an experienced team of engineers proficient in PCB design, manufacturing, and testing technologies. They can customize designs according to customer requirements to ensure the performance and reliability of the PCBs meet the requirements.
- Advanced Production Equipment: We are equipped with advanced PCB production lines and testing equipment to achieve high-precision manufacturing processes and strict quality control. From material procurement to product delivery, we ensure the controllability and stability of the production process.
- Flexible Production Capacity: We have flexible production capacity to meet orders of different scales and requirements from customers. Whether it’s small-scale rapid delivery or large-scale batch production, we can effectively meet customer needs.
- Quality Assurance: We strictly adhere to international standards and quality management systems to ensure stable and reliable product quality. All produced BT PCBs undergo rigorous testing and quality inspection to ensure they meet customer requirements and industry standards.
- Customer Service: We value communication and cooperation with customers, providing customized solutions based on customer requirements and responding promptly to customer feedback and needs. Our customer service team is always available to support and assist customers, ensuring customer satisfaction.
In summary, our company has the technical strength, production capacity, and quality assurance capabilities required to produce BT PCBs. We are committed to providing customers with high-quality, reliable BT PCB products and services, and to developing cooperation and mutual success with customers.
What are the 7 qualities of good customer service?
Good customer service is essential for building strong relationships with customers and fostering loyalty. Here are seven qualities that contribute to excellent customer service:
- Responsiveness: Good customer service involves being prompt and responsive to customer inquiries, requests, and concerns. Customers appreciate quick and efficient assistance when they have questions or encounter issues.
- Empathy: Empathy is the ability to understand and share the feelings of others. Effective customer service representatives demonstrate empathy by listening attentively to customers, acknowledging their concerns, and showing understanding and compassion.
- Communication Skills: Clear and effective communication is crucial for providing good customer service. Customer service representatives should be able to convey information clearly, answer questions concisely, and provide assistance in a friendly and professional manner.
- Problem-Solving Abilities: Good customer service involves resolving customer problems and issues effectively. Customer service representatives should have strong problem-solving skills to identify root causes of issues, explore solutions, and address customer concerns satisfactorily.
- Product Knowledge: Customer service representatives should have a deep understanding of the products or services they are supporting. Having comprehensive product knowledge enables them to provide accurate information, answer questions confidently, and offer relevant recommendations or solutions.
- Professionalism:Professionalism encompasses qualities such as reliability, integrity, and courtesy. Customer service representatives should conduct themselves professionally at all times, treating customers with respect, maintaining confidentiality, and upholding company values and policies.
- Follow-Up and Feedback: Good customer service doesn’t end with resolving immediate issues. It also involves following up with customers to ensure their needs have been met and soliciting feedback to identify areas for improvement. Following up shows customers that their satisfaction is a priority and demonstrates a commitment to continuous improvement.
By embodying these qualities, businesses can deliver exceptional customer service experiences that leave customers satisfied and eager to return.
FAQs
What are the key features of a BT PCB?
Key features of a BT PCB include Bluetooth module integration, antenna design for wireless communication, RF trace routing for signal integrity, and compatibility with Bluetooth standards and protocols.
What are the applications of BT PCBs?
BT PCBs are used in various applications such as wireless headphones, speakers, keyboards, mice, smartwatches, fitness trackers, IoT devices, and other electronic gadgets that require Bluetooth connectivity.
What are the design considerations for BT PCBs?
Design considerations for BT PCBs include antenna placement and design, RF trace routing, ground plane design, component placement, signal integrity, power consumption, size constraints, and regulatory compliance.
What materials are used in manufacturing BT PCBs?
Common substrate materials for BT PCBs include fiberglass (FR4), polyimide (PI), and specialized materials optimized for RF/microwave applications. Copper is used for conductive traces, and various surface finishes such as HASL, ENIG, and OSP are applied for protection and solderability.
How can I ensure the quality of BT PCBs?
Quality assurance measures for BT PCBs include thorough testing during production, compliance with Bluetooth standards and regulations, adherence to design guidelines, selection of reputable suppliers, and validation through functional testing and performance evaluation.
Can BT PCBs be customized for specific applications?
Yes, BT PCBs can be customized to meet the requirements of specific applications, such as incorporating additional features, optimizing antenna performance, adjusting form factors, or integrating with other wireless technologies.
Where can I find reliable suppliers for BT PCBs?
Reliable suppliers for BT PCBs can be found through industry directories, trade shows, online marketplaces, and referrals from colleagues or industry experts. It’s important to evaluate suppliers based on factors such as reputation, experience, capabilities, quality standards, and pricing.