Bt Laminate Substrate Manufacturing
Bt Laminate Substrate Manufacturing,Bt laminate substrate is a high-performance substrate material used in electronic circuit manufacturing, composed of bismaleimide triazine (Bt) resin and glass fiber cloth. This substrate exhibits excellent thermal stability, mechanical strength, and chemical resistance, making it suitable for various demanding applications such as aerospace, automotive, and telecommunications industries. Manufactured through a process of multiple layer stacking and pressing, Bt laminate substrate provides good electrical insulation performance and reliability, offering robust support for circuit designs.
What is a Bt Laminate Substrate?
A “Bt laminate substrate” likely refers to a type of substrate material used in the manufacturing of electronic circuits, particularly in the field of printed circuit boards (PCBs).
“Bt” could stand for “bismaleimide triazine,” which is a type of resin material commonly used in high-performance PCBs. Bismaleimide triazine resin is known for its excellent thermal stability, mechanical strength, and resistance to chemicals, making it suitable for demanding applications in industries such as aerospace, automotive, and telecommunications.
Laminates made with bismaleimide triazine resin are often used in multilayer PCBs where high reliability and performance are required, such as in military equipment, medical devices, and high-speed communication systems. These laminates provide good electrical insulation, high-frequency performance, and reliability under extreme conditions, making them suitable for a wide range of electronic applications.
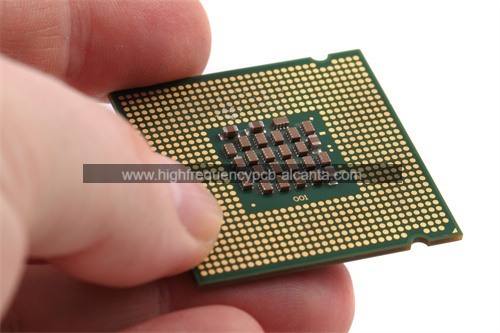
Bt laminate substrate manufacturing
What are the Bt Laminate Substrate Design Guidelines?
Design guidelines for Bt laminate substrates typically include recommendations and best practices for designing printed circuit boards (PCBs) using laminates made with bismaleimide triazine (Bt) resin. These guidelines aim to ensure the optimal performance, reliability, and manufacturability of the PCBs. Here are some common design guidelines:
- Thermal Management: Ensure proper thermal management to handle the heat generated by electronic components. This may involve using thermal vias, copper pours, and heat sinks to dissipate heat efficiently.
- Trace Width and Spacing: Follow recommended trace width and spacing guidelines to maintain signal integrity and prevent signal interference or crosstalk. These guidelines may vary depending on the specific application and signal requirements.
- Layer Stackup: Design the layer stackup carefully, considering factors such as signal integrity, impedance control, and manufacturing constraints. Proper layer stackup design helps achieve desired electrical performance and ease of manufacturing.
- Impedance Control: Maintain controlled impedance for high-speed signals by adhering to specific trace geometries, dielectric thicknesses, and layer stackup configurations. Impedance mismatches can degrade signal quality and lead to signal integrity issues.
- Component Placement: Place components strategically to minimize signal distortion, electromagnetic interference (EMI), and thermal issues. Consider the placement of high-speed components, connectors, and critical signal paths to optimize performance.
- Grounding: Implement a solid grounding strategy to minimize ground loops, reduce noise, and improve signal integrity. Use ground planes or distributed ground networks to provide low-impedance return paths for signals.
- Signal Integrity Analysis: Perform signal integrity analysis, including simulation and modeling, to predict and mitigate signal integrity issues such as reflections, ringing, and signal degradation. This helps ensure reliable operation of the PCB under various operating conditions.
- Manufacturability: Design the PCB with manufacturability in mind, considering factors such as PCB size, panelization, assembly processes, and material availability. Optimize the design to facilitate efficient and cost-effective manufacturing.
- Compliance and Standards: Ensure compliance with relevant industry standards and regulations, such as IPC (Association Connecting Electronics Industries) standards, to meet quality and reliability requirements.
- Testing and Validation: Plan for testing and validation of the PCB design to verify its performance and functionality. Conduct signal integrity testing, impedance measurements, and other tests to validate the design against specifications.
These guidelines serve as a foundation for designing high-performance and reliable PCBs using Bt laminate substrates, but it’s essential to adapt them based on specific project requirements, industry standards, and technological advancements. Collaboration with experienced PCB designers and manufacturers can also provide valuable insights and assistance in optimizing the design for success.
What is the Bt Laminate Substrate Fabrication Process?
The fabrication process of a Bt laminate substrate involves several steps:
- Preparation of Base Materials: The process typically starts with preparing the base materials, which include woven glass fiber cloth and bismaleimide triazine (Bt) resin. These materials need to be clean and free from contaminants to ensure proper adhesion and performance.
- Prepreg Preparation: Prepreg is a composite material made by impregnating reinforcement fibers with resin. In the case of Bt laminate substrates, the prepreg is prepared by impregnating the glass fiber cloth with Bt resin. This is often done using a combination of heat and pressure to ensure thorough impregnation and uniform distribution of the resin.
- Layer Stacking: Multiple layers of prepreg are stacked together with conductive copper foil layers in between to form a multilayer structure. The copper foil serves as the conductive pathway for electrical signals on the PCB.
- Lamination: The stacked layers are then pressed together under heat and pressure in a lamination process. This step bonds the layers together, forming a solid composite material with the desired thickness.
- Curing: After lamination, the composite material undergoes a curing process. This involves subjecting the material to elevated temperatures for a specific period to fully cure the resin and achieve the desired mechanical and thermal properties.
- Drilling and Plating: Holes are drilled into the substrate where electrical connections are needed. These holes are then plated with copper to provide conductivity between the different layers of the PCB.
- Etching: Excess copper is removed from the surface of the substrate through an etching process, leaving behind the desired circuit pattern.
- Surface Finishing: The final step involves applying a surface finish to the PCB to protect the copper traces from oxidation and ensure good solderability.
Overall, the fabrication process of a Bt laminate substrate requires precision and careful control of various parameters to ensure the quality and performance of the final product.
How do you manufacture a Bt Laminate Substrate?
Manufacturing a Bt laminate substrate involves several steps:
- Preparation of Materials: The process begins with preparing the base materials, including bismaleimide triazine (Bt) resin and woven glass fiber cloth. These materials should be clean and free from contaminants.
- Prepreg Production: Prepreg, a composite material made by impregnating reinforcement fibers with resin, is produced by saturating the glass fiber cloth with Bt resin. This is typically achieved using a process that involves applying resin evenly to the cloth, followed by heating to cure and partially polymerize the resin.
- Layer Stacking: Multiple layers of prepreg are stacked alternately with conductive copper foil layers. The copper foil serves as the conductive pathways for electrical signals on the PCB. The number of layers depends on the design requirements of the PCB.
- Lamination: The stacked layers are pressed together under heat and pressure in a lamination process. This step bonds the layers together, forming a solid composite material with the desired thickness. The lamination process typically occurs in a hydraulic press or a vacuum-assisted press to ensure uniform pressure distribution.
- Curing: After lamination, the composite material undergoes a curing process. This involves subjecting the material to elevated temperatures for a specific period to fully cure the resin and achieve the desired mechanical and thermal properties. The curing process is crucial for ensuring the stability and reliability of the laminate substrate.
- Drilling and Plating: Holes, known as vias, are drilled into the substrate where electrical connections are required between different layers. These holes are then plated with copper to provide conductivity between the layers. This process is typically carried out using automated drilling and plating equipment.
- Etching: Excess copper is removed from the surface of the substrate through an etching process, leaving behind the desired circuit pattern. Etching involves applying a chemical solution or using a plasma to dissolve or remove the unwanted copper.
- Surface Finishing: The final step involves applying a surface finish to the PCB to protect the copper traces from oxidation and ensure good solderability. Common surface finishes include immersion gold, electroless nickel immersion gold (ENIG), and immersion tin.
Throughout the manufacturing process, quality control measures are implemented to ensure the consistency and reliability of the Bt laminate substrate. These measures may include inspections, testing, and adherence to industry standards and specifications.
How much should a Bt Laminate Substrate cost?
The cost of a Bt laminate substrate can vary depending on several factors, including:
- Material Quality: The quality of the bismaleimide triazine (Bt) resin and the glass fiber cloth used in the laminate substrate can affect its cost. Higher quality materials typically command a higher price.
- Thickness and Layer Count: Thicker substrates and substrates with more layers generally cost more due to the increased material and manufacturing complexity involved.
- Size and Complexity: The size and complexity of the PCB design can also impact the cost. Larger boards or designs with intricate features may require more material and labor, resulting in a higher cost.
- Manufacturing Process: The specific manufacturing processes used, such as lamination, curing, drilling, and surface finishing, can influence the cost. More advanced or specialized processes may incur additional expenses.
- Volume and Order Size: Typically, larger orders or higher volumes can lead to economies of scale, resulting in lower unit costs. However, smaller orders or custom requirements may incur higher costs.
- Supplier and Location: The choice of supplier and their location can affect the cost. Suppliers in regions with lower labor or material costs may offer more competitive pricing.
- Market Conditions: Market demand and supply dynamics can influence pricing. Fluctuations in material costs, currency exchange rates, and overall market trends can impact the cost of laminate substrates.
It’s essential to obtain quotes from multiple suppliers and consider factors such as quality, lead times, and customer support when evaluating the cost of Bt laminate substrates. Additionally, working closely with PCB manufacturers or suppliers can help optimize designs for cost efficiency without compromising quality or performance.
What is Bt Laminate Substrate Base Material?
The base material of a Bt laminate substrate primarily consists of two main components: bismaleimide triazine (Bt) resin and glass fiber cloth.
- Bismaleimide Triazine (Bt) Resin: Bt resin is a type of thermosetting polymer known for its exceptional thermal stability, mechanical strength, and resistance to chemicals. It is the primary binding agent used in the laminate substrate. Bt resin provides the substrate with its high-performance properties, making it suitable for applications where reliability and durability are crucial, such as aerospace, automotive, and telecommunications industries.
- Glass Fiber Cloth: The glass fiber cloth serves as the reinforcement material in the laminate substrate. It provides mechanical support and strength to the substrate. The glass fibers are typically woven into a cloth-like structure, which is then impregnated with the Bt resin. This combination of glass fibers and resin creates a composite material with excellent electrical insulation properties, high mechanical strength, and good dimensional stability.
Together, the Bt resin and glass fiber cloth form the base material of the Bt laminate substrate, which undergoes further processing steps such as lamination, curing, drilling, and surface finishing to produce the final printed circuit board (PCB) substrate.
What are the 7 qualities of good customer service?
Good customer service involves meeting and exceeding customer expectations while providing a positive experience. Here are seven qualities of good customer service:
- Responsiveness: Customers appreciate prompt and timely responses to their inquiries, concerns, or issues. Being available and responsive to customer needs demonstrates attentiveness and care.
- Empathy: Showing empathy involves understanding and acknowledging the customer’s feelings, concerns, and perspective. It’s about demonstrating compassion and putting yourself in the customer’s shoes to address their needs effectively.
- Clarity and Communication: Effective communication is essential in providing good customer service. Clear and concise communication helps customers understand information, instructions, or solutions easily, reducing confusion and frustration.
- Problem-solving Skills: Good customer service involves resolving customer issues and problems efficiently and effectively. Having strong problem-solving skills enables customer service representatives to identify root causes, offer appropriate solutions, and ensure customer satisfaction.
- Professionalism: Maintaining professionalism in all interactions with customers fosters trust and confidence. This includes being polite, respectful, and courteous, regardless of the situation or the customer’s demeanor.
- Product Knowledge: Having in-depth knowledge about products or services allows customer service representatives to provide accurate information, answer questions, and offer relevant recommendations. Being knowledgeable instills confidence in customers and enhances their overall experience.
- Proactive Assistance: Anticipating customer needs and offering proactive assistance can enhance the customer experience. This may involve providing relevant information, offering additional support, or suggesting solutions before customers even ask for them.
By embodying these qualities, businesses can create a positive and memorable customer service experience that fosters customer loyalty and satisfaction.
FAQs
What is Bt laminate substrate?
Bt laminate substrate is a type of printed circuit board (PCB) substrate made using bismaleimide triazine (Bt) resin as the base material. It offers high thermal stability, mechanical strength, and chemical resistance, making it suitable for demanding applications.
What are the advantages of Bt laminate substrate?
Bt laminate substrate offers excellent thermal performance, high mechanical strength, and good chemical resistance. It is suitable for high-reliability applications in industries such as aerospace, automotive, and telecommunications.
How is Bt laminate substrate manufactured?
The manufacturing process of Bt laminate substrate involves preparing base materials, such as Bt resin and glass fiber cloth, producing prepreg, stacking layers, laminating under heat and pressure, curing, drilling, plating, etching, and surface finishing.
What are the typical applications of Bt laminate substrate?
Bt laminate substrate is commonly used in high-reliability applications that require excellent thermal performance, mechanical strength, and chemical resistance. It is often found in aerospace components, automotive electronics, high-speed communication systems, and military equipment.
What considerations should be made when designing with Bt laminate substrate?
When designing with Bt laminate substrate, factors such as thermal management, mechanical stability, signal integrity, and compatibility with manufacturing processes should be considered. It’s essential to ensure that the design meets the requirements of the intended application and adheres to industry standards.