BT Laminate Substrate Manufacturer
BT Laminate Substrate Manufacturer,BT Laminate Substrate Manufacturer,BT laminate substrate is a high-performance material used in electronic packaging and printed circuit board (PCB) manufacturing. It utilizes Bismaleimide Triazine (BT) resin as its matrix, reinforced with composite fiberglass cloth to provide excellent thermal performance, mechanical strength, and electrical properties. BT laminate substrate exhibits outstanding thermal stability, capable of withstanding high temperatures while maintaining stable electrical performance. Its low dielectric constant and loss tangent make it suitable for high-frequency circuits and microwave applications. Additionally, BT laminate substrate demonstrates excellent chemical stability and low moisture absorption, making it ideal for use in various demanding environments. Due to its reliability and performance, BT laminate substrate is widely utilized in high-end electronic devices in industries such as aerospace, defense, telecommunications, and industrial control.
What is a BT Laminate substrate?
A BT laminate substrate, also known as a Bismaleimide Triazine laminate substrate, is a type of material used in electronic packaging and printed circuit board (PCB) manufacturing. It’s a high-performance substrate known for its excellent thermal, mechanical, and electrical properties, making it suitable for demanding applications in industries like aerospace, defense, and telecommunications.
Here’s a breakdown of its key characteristics:
- Thermal Stability: BT laminate substrates exhibit exceptional thermal stability, capable of withstanding high temperatures without significant degradation. This property is crucial in electronic devices where components may generate heat during operation.
- Mechanical Strength: These substrates offer impressive mechanical strength and dimensional stability, ensuring the integrity of the circuitry even under harsh environmental conditions or mechanical stress.
- Electrical Performance: BT laminates possess excellent electrical properties, including low dielectric constant and loss tangent, which contribute to maintaining signal integrity in high-frequency applications.
- Chemical Resistance: They are resistant to various chemicals and solvents, which is advantageous in environments where exposure to such substances is a concern.
- Low Water Absorption: BT laminate substrates have low water absorption rates, minimizing the risk of delamination or electrical malfunction due to moisture ingress.
- Compatibility with High-Frequency Signals: These substrates are well-suited for high-frequency applications due to their low loss tangent and stable dielectric properties, making them ideal for use in microwave and RF circuits.
- Manufacturability: BT laminate materials can be easily processed using standard PCB manufacturing techniques, including drilling, etching, and plating, allowing for efficient production of complex circuitry.
Overall, BT laminate substrates are valued for their combination of thermal performance, mechanical strength, and electrical properties, making them a preferred choice for advanced electronic applications where reliability and performance are critical.
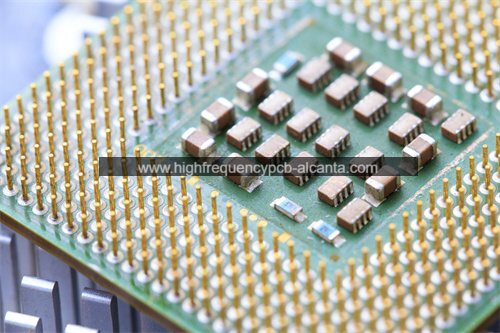
BT Laminate Substrate Manufacturer
What are the BT Laminate substrate Design Guidelines?
Design guidelines for BT laminate substrates are essential to ensure the optimal performance and reliability of electronic circuits. Here are some key considerations:
- Material Selection: Choose the appropriate grade and thickness of BT laminate substrate based on the specific requirements of your application, considering factors such as operating frequency, thermal management needs, and mechanical stability.
- Layer Stackup: Determine the layer stackup configuration based on the complexity of the circuit, signal integrity requirements, and manufacturing constraints. Considerations include signal routing, power and ground plane distribution, and impedance matching.
- Trace Width and Spacing: Follow recommended trace width and spacing guidelines to maintain signal integrity and prevent signal interference or crosstalk. These guidelines may vary depending on the operating frequency and impedance requirements of the circuit.
- Via Design: Optimize via placement and design to minimize signal distortion and impedance discontinuities. Use proper via types (such as microvias or buried vias) and consider via stub length reduction techniques to enhance high-frequency performance.
- Thermal Management: Incorporate thermal vias or heat sinks into the PCB design to dissipate heat effectively, especially in applications with high-power components or operating in elevated temperature environments. Ensure adequate clearance and airflow for heat dissipation.
- Component Placement: Place components strategically to minimize signal distortion, reduce electromagnetic interference (EMI), and facilitate efficient routing. Follow best practices for high-speed digital and RF component placement, considering signal paths and signal return paths.
- Signal Integrity Analysis: Conduct signal integrity simulations and analysis to evaluate the impact of the PCB layout on signal quality, including impedance matching, signal attenuation, and timing characteristics. Adjust the design as needed to optimize signal integrity.
- Manufacturability:Design the PCB layout with manufacturability in mind, considering factors such as panelization, solder mask clearance, copper balance, and alignment features for automated assembly processes.
- Design for Testability: Incorporate test points, fiducial marks, and other features to facilitate testing and inspection during PCB assembly and quality assurance processes.
- Documentation: Provide comprehensive documentation including PCB layout files, assembly drawings, fabrication notes, and design guidelines to ensure accurate and efficient manufacturing and assembly.
By following these design guidelines, you can maximize the performance, reliability, and manufacturability of electronic circuits using BT laminate substrates.
What is the BT Laminate substrate Fabrication Process?
The fabrication process of BT laminate substrates involves several steps to manufacture the printed circuit boards (PCBs) using Bismaleimide Triazine (BT) laminate materials. Here’s an overview of the typical fabrication process:
- Material Preparation: The process begins with the preparation of BT laminate sheets. These sheets are typically composed of woven fiberglass cloth impregnated with BT resin. The sheets are available in various thicknesses and copper foil cladding options.
- Layer Stacking: Multiple layers of BT laminate sheets are stacked together to create the desired layer configuration for the PCB. Each layer may contain copper foil bonded to the laminate, which forms the conductive traces and planes of the circuit.
- Lamination: The stacked layers are laminated together under heat and pressure using a hydraulic press or vacuum lamination equipment. This process bonds the layers into a solid composite structure, with the copper foil embedded within the BT laminate.
- Drilling: After lamination, holes are drilled into the PCB using precision drilling machines. These holes are used for through-hole components, vias, and interconnections between different layers of the PCB.
- Copper Plating: Copper plating is applied to the walls of the drilled holes to create electrical connections between the different layers of the PCB. This process, known as electroplating, involves the deposition of a thin layer of copper onto the exposed surfaces of the drilled holes.
- Circuit Patterning: A layer of photosensitive material called photoresist is applied to the surface of the PCB. The desired circuit pattern is then transferred onto the photoresist using photolithography techniques, which involves exposing the PCB to UV light through a mask.
- Etching: The exposed copper areas not protected by the photoresist are chemically etched away, leaving behind the desired copper traces and pads on the PCB surface. The remaining photoresist is then stripped away, revealing the completed circuit pattern.
- Surface Finishing: Surface finishing processes may be applied to the PCB to improve solderability, corrosion resistance, and electrical performance. Common surface finishes include HASL (Hot Air Solder Leveling), ENIG (Electroless Nickel Immersion Gold), and OSP (Organic Solderability Preservatives).
- Final Inspection and Testing: The finished PCBs undergo visual inspection, electrical testing, and quality assurance checks to ensure they meet the required specifications and standards.
- Routing and Profiling: The individual PCBs are routed out of the larger panel and separated using milling or depanelization equipment. The edges of the PCBs may be trimmed or profiled to achieve the final desired dimensions.
- Packaging and Shipping: The finished PCBs are packaged according to customer requirements and shipped to their destination for use in electronic devices and systems.
Overall, the fabrication process of BT laminate substrates involves a series of precision steps to create high-quality PCBs with reliable electrical and mechanical properties.
How do you manufacture a BT Laminate substrate?
Manufacturing a BT laminate substrate involves several steps to create a composite material suitable for use in printed circuit boards (PCBs). Here’s an overview of the typical manufacturing process:
- Preparation of Raw Materials: The process begins with the preparation of raw materials, including Bismaleimide Triazine (BT) resin, fiberglass cloth, and copper foil. The BT resin is typically supplied as a liquid or powder, while the fiberglass cloth is available in various weave patterns and thicknesses. Copper foil is used as the conductive material for the PCB traces and planes.
- Resin Impregnation: The fiberglass cloth is impregnated with BT resin to create prepreg sheets. This is typically done using a process called “hot-melt” impregnation, where the resin is heated and applied to the fiberglass cloth under pressure to ensure uniform impregnation.
- Layer Stacking: Multiple layers of prepreg sheets are stacked together with copper foil interleaved between them to form the desired layer configuration for the PCB. The number of layers and the arrangement of copper foil may vary depending on the specific requirements of the PCB design.
- Lamination: The stacked layers are laminated together under heat and pressure using a hydraulic press or vacuum lamination equipment. This process bonds the layers into a solid composite structure, with the copper foil embedded within the BT laminate. The lamination process also helps to remove air and voids from the laminate, ensuring good electrical and mechanical properties.
- Curing: The laminated substrate is then cured in an oven at elevated temperatures to complete the polymerization of the BT resin. Curing times and temperatures may vary depending on the specific formulation of the BT resin and the desired properties of the laminate.
- Surface Treatment: After curing, the surface of the laminate may be treated to improve adhesion and solderability. This may involve applying a thin layer of copper or other metal to the surface of the laminate, followed by chemical treatment to clean and activate the surface.
- Quality Control: Throughout the manufacturing process, quality control measures are implemented to ensure that the laminate meets the required specifications and standards. This may include visual inspection, dimensional measurement, and testing of mechanical and electrical properties.
- Final Inspection and Packaging: Once the laminate has been manufactured and inspected, it is packaged according to customer requirements and shipped to PCB manufacturers for use in the fabrication of printed circuit boards.
By following these steps, manufacturers can produce high-quality BT laminate substrates with the thermal, mechanical, and electrical properties required for demanding electronic applications.
How much should a BT Laminate substrate cost?
The cost of a BT laminate substrate can vary depending on several factors, including the manufacturer, the grade and thickness of the laminate, the quantity ordered, and any additional features or customization options. Here are some factors that can influence the cost:
- Material Grade: BT laminate substrates are available in different grades, each offering specific performance characteristics. Higher-grade materials with enhanced thermal, mechanical, or electrical properties may command a higher price.
- Thickness: The thickness of the BT laminate substrate can affect its cost. Thicker substrates typically require more raw material and may involve additional manufacturing steps, leading to higher costs compared to thinner substrates.
- Copper Cladding: The presence and thickness of copper foil cladding on the laminate can also impact the cost. Thicker copper foils or multiple layers of copper can increase material costs.
- Quantity Ordered: Bulk purchasing typically results in lower unit costs. Manufacturers may offer volume discounts for larger orders of BT laminate substrates.
- Customization: Custom features or special requirements, such as specific dielectric properties, surface finishes, or unique layer configurations, may incur additional costs.
- Supplier and Geographic Location: Different suppliers may offer varying prices for BT laminate substrates based on factors such as manufacturing capabilities, overhead costs, and geographic location.
- Market Conditions: Market demand, supply chain disruptions, and fluctuations in raw material prices can influence the overall cost of BT laminate substrates.
As a rough estimate, the cost of BT laminate substrates can range from a few dollars per square foot for standard-grade materials to tens of dollars per square foot for high-performance or specialty laminates. For precise pricing information, it’s recommended to contact suppliers or manufacturers directly and provide details about your specific requirements and quantities.
What is BT Laminate substrate base material?
The base material of a BT laminate substrate is composed of a reinforced resin matrix, typically made from Bismaleimide Triazine (BT) resin. This resin matrix is reinforced with a woven fiberglass cloth to enhance mechanical strength and dimensional stability.
Bismaleimide Triazine (BT) resin is a high-performance thermosetting polymer known for its excellent thermal, mechanical, and electrical properties. It offers superior thermal stability, allowing it to withstand high temperatures without significant degradation. This property is particularly important in electronic applications where components may generate heat during operation.
The fiberglass cloth reinforcement provides additional strength and rigidity to the laminate substrate. The fiberglass cloth is typically made from woven glass fibers, which are impregnated with the BT resin during the manufacturing process. The fiberglass reinforcement helps to improve the laminate’s mechanical properties, such as tensile strength, flexural strength, and impact resistance.
In summary, the base material of a BT laminate substrate consists of a resin matrix composed of Bismaleimide Triazine (BT) resin, reinforced with woven fiberglass cloth. This combination of materials results in a composite substrate with excellent thermal, mechanical, and electrical properties, making it suitable for use in demanding electronic applications such as printed circuit boards (PCBs).
Which company makes BT Laminate substrate?
Several companies manufacture BT laminate substrates, including well-known manufacturers such as Rohm and Ericsson. These companies have good reputations in the electronics industry, and their BT laminate substrates are widely used in high-end applications in aerospace, defense, telecommunications, and other fields.
As part of our company, we can also produce BT laminate substrates. We have advanced production equipment and technology, as well as an experienced technical team, capable of meeting various customer requirements.
Our production process includes the following key steps:
- Raw Material Procurement and Preparation: We procure high-quality BT resin, fiberglass cloth, copper foil, and other raw materials to ensure the quality and performance of our products.
- Preprocessing and Layer Stacking: We preprocess the raw materials and then stack multiple layers of fiberglass cloth and copper foil together to form the desired laminate structure.
- Pressing and Curing: We use advanced pressing equipment to laminate the stacked materials into sheets under high temperature and pressure, followed by curing to ensure the stability and performance of the sheets.
- Processing and Testing: We process and trim the sheets to meet dimensional and surface quality requirements. Subsequently, we conduct rigorous testing and quality control to ensure compliance with customer technical specifications and standards.
- Packaging and Delivery: Finally, we package the finished products according to customer requirements and deliver them on time to ensure timely use.
We are committed to providing high-quality, reliable, and customized BT laminate substrates to meet the diverse needs of our customers. Our production process is carefully designed and optimized to ensure that our products meet industry-leading levels of quality and performance.
What are the 7 qualities of good customer service?
Good customer service is essential for building strong relationships with customers and fostering loyalty. Here are seven qualities that characterize good customer service:
- Responsiveness: Good customer service involves being attentive and responsive to customers’ needs and inquiries in a timely manner. This includes promptly addressing questions, concerns, and requests for assistance.
- Empathy: Empathy is the ability to understand and relate to customers’ feelings and perspectives. Good customer service representatives demonstrate empathy by actively listening to customers, acknowledging their concerns, and showing genuine concern for their satisfaction.
- Clear Communication: Effective communication is key to providing good customer service. Clear and concise communication helps ensure that customers understand information, instructions, and solutions provided by the service representative.
- Problem-Solving Skills: Good customer service representatives possess strong problem-solving skills to address customer issues and resolve conflicts effectively. They are resourceful, creative, and proactive in finding solutions that meet customers’ needs and expectations.
- Professionalism: Professionalism encompasses behaviors such as courtesy, respect, and integrity in interactions with customers. Good customer service representatives maintain a positive attitude, remain calm under pressure, and uphold ethical standards in their dealings with customers.
- Product Knowledge: Having a thorough understanding of the products or services offered allows customer service representatives to provide accurate information, answer questions, and offer helpful recommendations. Good customer service involves ongoing training and development to stay updated on product features, benefits, and use cases.
- Follow-Up and Feedback: Following up with customers after resolving their inquiries or issues demonstrates a commitment to their satisfaction and allows for feedback on the service provided. Good customer service includes soliciting feedback, addressing any remaining concerns, and proactively seeking opportunities for improvement.
By embodying these qualities, organizations can deliver exceptional customer service experiences that leave a positive impression and build long-term relationships with customers.
FAQs
What is BT Laminate substrate?
BT laminate substrate, also known as Bismaleimide Triazine laminate substrate, is a type of material used in electronic packaging and printed circuit board (PCB) manufacturing. It is known for its excellent thermal, mechanical, and electrical properties.
What are the key properties of BT laminate substrate?
BT laminate substrates exhibit excellent thermal stability, mechanical strength, and electrical performance. They have low dielectric constant and loss tangent, making them suitable for high-frequency applications. They are also resistant to chemicals and have low water absorption rates.
What are the applications of BT laminate substrates?
BT laminate substrates are commonly used in aerospace, defense, telecommunications, and other industries where high-performance electronic packaging is required. They are used in applications such as RF/microwave circuits, high-speed digital circuits, and power electronics.
How are BT laminate substrates manufactured?
BT laminate substrates are typically manufactured through a process that involves impregnating fiberglass cloth with Bismaleimide Triazine resin, stacking multiple layers together, laminating them under heat and pressure, and then curing the laminate to form a solid composite structure.
What are the design guidelines for using BT laminate substrates?
Design guidelines for BT laminate substrates include considerations such as material selection, layer stackup configuration, trace width and spacing, via design, thermal management, component placement, signal integrity analysis, manufacturability, and documentation.
What factors can affect the cost of BT laminate substrates?
The cost of BT laminate substrates can vary depending on factors such as material grade, thickness, copper cladding, quantity ordered, customization options, supplier, geographic location, and market conditions.
Where can I purchase BT laminate substrates?
BT laminate substrates are available from various manufacturers and suppliers specializing in electronic materials and PCB fabrication. They can be purchased directly from manufacturers or through authorized distributors.