Bt Laminate PCB Manufacturing
Bt Laminate PCB Manufacturing,BT Laminate PCB (Bismaleimide Triazine) is a high-performance substrate material known for its excellent thermal stability and electrical properties. Composed of woven fiberglass impregnated with BT resin, it offers superior mechanical strength and reliability, making it ideal for demanding applications in aerospace, automotive, and telecommunications industries. BT Laminate PCB enables high-frequency signal transmission and supports miniaturization due to its low dielectric constant and low loss tangent. With its exceptional thermal performance, this substrate material ensures efficient heat dissipation, enhancing the longevity and reliability of electronic devices in harsh operating environments.
Bt laminate PCBs are printed circuit boards with high flame-retardant properties, using a laminate material composed of brominated epoxy resin and woven glass cloth. Their unique material composition endows them with excellent fire safety performance, making them widely used in electronic devices and industries with stringent safety requirements. Bt laminate PCBs not only possess good mechanical strength, thermal stability, and electrical insulation properties but also effectively prevent fire hazards to equipment and personnel, making them an integral component in electronic product manufacturing.
What is a Bt laminate PCB?
A Bt laminate PCB refers to a printed circuit board (PCB) that uses a laminate material made from a blend of brominated epoxy resin and woven glass cloth. The term “Bt” typically stands for “Brominated Epoxy Resin,” which is a type of flame-retardant material used in PCB manufacturing.
Bt laminate PCBs are commonly used in electronic devices where fire safety is a concern, as the brominated epoxy resin provides a high level of flame resistance. These PCBs are often used in applications such as consumer electronics, automotive electronics, aerospace, and other industries where safety standards are stringent.
Bt laminate PCBs offer good mechanical strength, thermal stability, and electrical insulation properties, making them suitable for various demanding applications. They are manufactured using standard PCB fabrication processes, including etching, drilling, and soldering, but with the use of Bt laminate materials to ensure fire safety compliance.
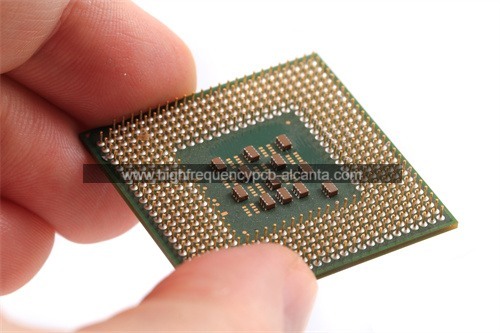
Bt laminate PCB manufacturing
What are the Bt laminate PCB Design Guidelines?
Designing a PCB with Bt laminate material involves considering several guidelines to ensure optimal performance and reliability. Here are some common Bt laminate PCB design guidelines:
- **Material Selection**: Choose a Bt laminate material with appropriate specifications for your application, considering factors such as dielectric constant, thermal conductivity, and flame retardancy.
- **Layer Stackup**: Design the layer stackup carefully to meet signal integrity, power distribution, and thermal management requirements. Consider factors like signal routing, power plane distribution, and heat dissipation.
- **Trace Width and Spacing**: Follow standard trace width and spacing guidelines to maintain signal integrity and prevent signal crosstalk and impedance mismatch.
- **Grounding and Power Planes**: Implement a solid ground plane and power distribution planes to minimize noise, provide stable power delivery, and enhance EMC performance.
- **Component Placement**: Optimize component placement to minimize signal path lengths, reduce noise coupling, and ensure efficient heat dissipation. Pay attention to high-speed signal paths and sensitive components.
- **Thermal Management**: Incorporate thermal vias, heatsinks, or other thermal management techniques to dissipate heat effectively, especially in areas with high power components.
- **Signal Integrity**: Use controlled impedance routing for high-speed signals to maintain signal integrity and reduce signal reflections and losses.
- **Drill and Annular Ring Sizes**: Ensure drill and annular ring sizes are compatible with the capabilities of your PCB manufacturer and meet design requirements for reliability and manufacturability.
- **Solder Mask and Silkscreen**: Define solder mask and silkscreen layers appropriately to provide insulation, protect copper traces, and provide component identification.
- **Compliance with Standards**: Ensure your design complies with relevant industry standards and regulations, especially regarding flame retardancy and safety requirements.
- **Testing and Verification**: Perform thorough design verification, including signal integrity analysis, thermal analysis, and manufacturability checks, to identify and address potential issues early in the design process.
By adhering to these Bt laminate PCB design guidelines, you can optimize the performance, reliability, and manufacturability of your PCB design while ensuring compliance with safety and regulatory requirements.
What is the Bt laminate PCB Fabrication Process?
The fabrication process for a Bt laminate PCB is similar to that of a standard PCB, with the main difference being the use of Bt laminate material, which contains brominated epoxy resin for flame retardancy. Here’s an overview of the typical fabrication process for a Bt laminate PCB:
- **Design**: The PCB design is created using PCB design software, including schematic capture and layout design. During this stage, designers consider factors such as component placement, signal routing, power distribution, and thermal management.
- **Material Selection**: Choose Bt laminate material suitable for the specific application requirements, considering factors such as dielectric constant, thermal conductivity, flame retardancy, and compliance with safety standards.
- **Layer Stackup**: Determine the layer stackup configuration based on the design requirements, including the number of layers, signal, power, and ground plane arrangement.
- **Preparation**: Prepare the laminate material by cutting it to the required size and cleaning the surfaces to remove any contaminants that could affect adhesion.
- **Lamination**: Layer the prepreg material and copper foil sheets according to the desired layer stackup configuration. Apply heat and pressure to bond the layers together into a single panel.
- **Drilling**: Drill holes (vias) at specified locations for component mounting, interconnection between layers, and electrical testing. Use precision drilling equipment to ensure accuracy.
- **Plating**: Plate the drilled holes with copper to establish electrical connections between layers. This process involves depositing a thin layer of copper inside the vias using electroplating or other metallization techniques.
- **Etching**: Apply a layer of photoresist material to the copper surface and expose it to UV light through a photomask with the desired circuit pattern. Develop and etch away the exposed copper to create the circuit traces.
- **Surface Finish**: Apply a surface finish to protect exposed copper traces, improve solderability, and enhance the PCB’s durability. Common surface finishes include hot air solder leveling (HASL), electroless nickel immersion gold (ENIG), and immersion tin or silver.
- **Solder Mask**: Apply solder mask ink over the entire board surface, leaving openings for component pads and vias. Cure the solder mask to create an insulating layer and define the solderable areas.
- **Silkscreen**: Print component designators, logos, and other identifying information onto the board surface using silkscreen printing. This helps with component placement and assembly.
- **Testing and Inspection**: Perform electrical testing, including continuity testing, insulation resistance testing, and impedance testing, to ensure the PCB meets design specifications. Inspect the PCB for any defects or manufacturing errors.
- **Routing and Profiling**: Cut the individual PCBs from the panel using routing or scoring techniques. Profile the edges of the PCBs to remove excess material and ensure smooth edges.
- **Final Inspection**: Conduct a final inspection to verify the quality of the finished PCBs, including dimensional accuracy, surface finish quality, solder mask alignment, and overall appearance.
- **Packaging and Shipping**: Package the finished PCBs according to customer requirements and ship them to the assembly facility or end-user.
Throughout the fabrication process, strict quality control measures are implemented to ensure the reliability, performance, and safety of the Bt laminate PCBs. Compliance with industry standards and regulations, such as IPC standards and RoHS directives, is also essential.
How do you manufacture a Bt laminate PCB?
Manufacturing a Bt laminate PCB involves several steps, similar to the fabrication process for other types of printed circuit boards. Here’s a general overview of the manufacturing process:
- **Design**: The process begins with the PCB design, where the circuit schematic is translated into a physical layout using PCB design software. Design considerations include component placement, routing, layer stackup, and signal integrity.
- **Material Selection**: Choose Bt laminate material suitable for the specific application requirements, considering factors such as dielectric constant, thermal conductivity, flame retardancy, and compatibility with manufacturing processes.
- **Preparation of Substrate**: Cut the Bt laminate material into panels or sheets of the required size for the PCBs. Clean the substrate surface to remove any contaminants that could affect adhesion during subsequent processes.
- **Drilling**: Drill holes for through-hole components, vias, and mounting holes using precision drilling equipment. Ensure accurate hole placement and size according to the PCB design specifications.
- **Layer Imaging**: Apply a layer of photoresist material onto the substrate surface. Expose the photoresist to UV light through a photomask containing the PCB circuit pattern. Develop the photoresist to remove the unexposed areas, leaving behind the circuit pattern.
- **Copper Plating**: Plate the exposed copper areas with a thin layer of copper through an electroplating process. This step forms the conductive traces and pads of the PCB circuit.
- **Etching**: Remove the excess copper from the substrate surface using a chemical etchant, leaving behind only the copper traces and pads defined by the circuit pattern. Rinse and neutralize the substrate after etching to stop the etching process.
- **Surface Finish**: Apply a surface finish to protect the exposed copper traces from oxidation and facilitate soldering during assembly. Common surface finish options include HASL (Hot Air Solder Leveling), ENIG (Electroless Nickel Immersion Gold), and OSP (Organic Solderability Preservatives).
- **Solder Mask Application**: Apply a solder mask layer over the entire surface of the PCB, leaving openings for component pads and vias. The solder mask provides insulation and protection for the copper traces while defining solderable areas for component attachment.
- **Silkscreen Printing**: Print component designators, logos, and other markings onto the PCB surface using a silkscreen printing process. These markings aid in component placement, identification, and assembly.
- **Final Inspection and Testing**: Conduct a series of quality control inspections and tests to ensure the manufactured PCBs meet the specified design requirements and industry standards. This may include visual inspection, electrical testing, and functionality testing.
- **Panelization and Separation**: If manufacturing multiple PCBs on a panel, perform panelization to group multiple PCBs together for efficient production. After testing and inspection, separate the individual PCBs from the panel using methods such as routing, V-scoring, or depanelization.
- **Packaging and Shipping**: Package the finished PCBs securely to protect them during transit and storage. Ship the PCBs to customers or assembly facilities for further integration into electronic products.
Throughout the manufacturing process, strict quality control measures are essential to ensure the reliability, performance, and consistency of the Bt laminate PCBs. This includes monitoring process parameters, conducting inspections at each stage, and addressing any deviations or defects promptly.
How much should a Bt laminate PCB cost?
The cost of a Bt laminate PCB can vary widely depending on several factors such as:
- **Size and Complexity**: Larger and more complex PCBs typically cost more to manufacture due to increased material and production time.
- **Number of Layers**: The number of layers in the PCB affects the fabrication process complexity and material cost. More layers usually result in higher costs.
- **Material Specifications**: The type and quality of Bt laminate material used can impact the cost. High-performance materials with specific characteristics may incur higher expenses.
- **Surface Finish and Additional Features**: Surface finish options and additional features like impedance control, blind vias, and buried vias can add to the cost.
- **Quantity**: Economies of scale apply, meaning larger production quantities generally result in lower per-unit costs due to bulk material purchases and optimized production processes.
- **Lead Time**: Expedited or rush orders may incur additional fees compared to standard lead times.
- **Supplier and Location**: PCB manufacturers in different regions may have varying labor costs, overhead expenses, and pricing structures.
To get an accurate cost estimate for your specific Bt laminate PCB project, it’s best to contact multiple PCB manufacturers, provide them with your design specifications, and request quotes. Additionally, online PCB cost calculators offered by some manufacturers can provide rough estimates based on basic parameters such as board size, layer count, and quantity.
Which company makes Bt laminate PCBs?
Currently, there are many companies offering Bt laminate PCB manufacturing services in the market. Some well-known PCB manufacturers include Foxconn Technology Group, JLCPCB in Taiwan, and LCSC. These companies possess advanced production equipment, extensive experience, and professional teams to meet various customer needs, including the manufacturing of Bt laminate PCBs.
Our company is also a professional PCB manufacturer with the capability to produce Bt laminate PCBs. We have advanced production equipment and a skilled technical team capable of providing high-quality and reliable Bt laminate PCB products according to customer requirements. We prioritize quality control and adhere to strict quality management systems to ensure that each batch of products meets customer requirements and standards.
In addition to manufacturing Bt laminate PCBs, our company also offers one-stop solutions from design to assembly to meet customers’ overall needs. Whether it’s prototyping or mass production, we can provide efficient and high-quality services to support the success of our customers’ projects.
If you have a need for Bt laminate PCBs, we are willing to collaborate with you to provide customized solutions to ensure the smooth progress and expected results of your project. We look forward to working with you!
FAQs
What is a Bt laminate PCB?
A Bt laminate PCB refers to a printed circuit board that uses a laminate material made from a blend of brominated epoxy resin and woven glass cloth. The term “Bt” typically stands for “Brominated Epoxy Resin,” which provides flame-retardant properties to the PCB.
What are the advantages of Bt laminate PCBs?
Bt laminate PCBs offer high flame resistance, making them suitable for applications where fire safety is a concern. They also provide good mechanical strength, thermal stability, and electrical insulation properties.
Where are Bt laminate PCBs commonly used?
Bt laminate PCBs are commonly used in electronic devices and industries where fire safety standards are stringent. They find applications in consumer electronics, automotive electronics, aerospace, and other safety-critical systems.
How are Bt laminate PCBs manufactured?
The manufacturing process of Bt laminate PCBs involves several steps, including substrate preparation, layer imaging, copper plating, etching, surface finish application, solder mask application, silkscreen printing, final inspection, and testing. The process ensures the formation of conductive traces and components on the PCB while incorporating flame-retardant properties.
What considerations should be made when designing Bt laminate PCBs?
Design considerations for Bt laminate PCBs include material selection, layer stackup design, trace width and spacing, grounding and power planes, component placement, thermal management, signal integrity, drill and annular ring sizes, solder mask, silkscreen, compliance with standards, and testing and verification.
How much do Bt laminate PCBs cost?
The cost of Bt laminate PCBs varies depending on factors such as size, complexity, number of layers, material specifications, surface finish, quantity, lead time, and supplier. It’s best to request quotes from multiple PCB manufacturers to get an accurate cost estimate for your specific project.