BT Epoxy Resin PCB Manufacturing
BT Epoxy Resin PCB Manufacturing,BT epoxy resin PCB (Printed Circuit Board) is a type of printed circuit board that uses Bismaleimide Triazine (BT) resin as its base material. It boasts excellent electrical properties, mechanical strength, and heat resistance, making it suitable for various high-performance electronic applications. The manufacturing process for BT epoxy resin PCBs includes material preparation, drilling, through-hole plating, circuit pattern formation, layer stacking, imaging, etching, surface treatment, solder mask application, and silk-screen printing. Widely used in aerospace, automotive, telecommunications, consumer electronics, and other fields, it provides reliable circuit support for modern electronic devices.
What is a BT Epoxy Resin PCB?
A BT epoxy resin PCB (Printed Circuit Board) refers to a type of PCB made using a base material called “Bismaleimide Triazine” or simply “BT resin.” BT epoxy resin is a high-performance thermosetting resin known for its excellent electrical properties, mechanical strength, and heat resistance. It is often used in the manufacturing of advanced PCBs, especially those designed for high-frequency and high-speed applications.
BT epoxy resin PCBs offer several advantages:
- High Temperature Resistance: BT epoxy resin can withstand high operating temperatures, making it suitable for applications where heat dissipation is a concern.
- Low Dielectric Constant and Dissipation Factor: These properties make BT epoxy resin PCBs ideal for high-frequency applications, such as telecommunications and RF (Radio Frequency) devices, as they minimize signal loss and distortion.
- Mechanical Strength: BT epoxy resin PCBs exhibit good mechanical properties, providing excellent stability and reliability, even under harsh environmental conditions.
- Chemical Resistance: They are resistant to many chemicals, making them suitable for applications where exposure to corrosive substances is possible.
- Dimensional Stability: BT epoxy resin PCBs maintain their shape and dimensions over a wide range of operating conditions, ensuring consistent performance.
Overall, BT epoxy resin PCBs are favored for their reliability, performance, and versatility, making them a popular choice in various industries, including aerospace, automotive, telecommunications, and consumer electronics.
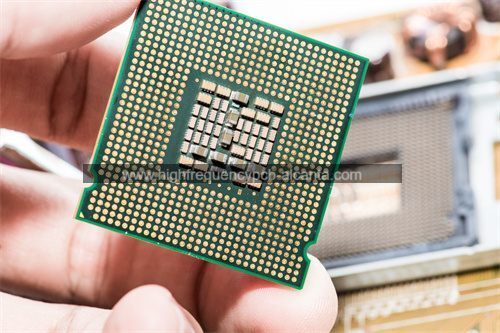
BT Epoxy Resin PCB Manufacturing
What are the BT Epoxy Resin PCB Design Guidelines?
Designing BT epoxy resin PCBs requires adherence to specific guidelines to ensure optimal performance and reliability. Here are some common BT epoxy resin PCB design guidelines:
- Material Selection: Choose high-quality BT epoxy resin materials with suitable dielectric properties and thermal characteristics to meet the requirements of the application.
- Layer Stackup: Design an appropriate layer stackup considering signal integrity, impedance control, and thermal management. Proper layer arrangement helps minimize signal distortion and ensures efficient heat dissipation.
- Trace Routing: Follow best practices for trace routing, including maintaining proper trace widths, spacing, and impedance control. Use differential pair routing for high-speed signals to minimize signal skew and crosstalk.
- Via Design: Optimize via placement and design to minimize signal reflections and impedance variations. Use blind vias and buried vias carefully to reduce signal distortion and improve signal integrity.
- Component Placement: Place components strategically to minimize signal path lengths, reduce electromagnetic interference (EMI), and facilitate efficient routing.
- Power Distribution: Design a robust power distribution network with adequate decoupling capacitors and power planes to ensure stable power delivery and minimize voltage fluctuations.
- Thermal Management: Incorporate thermal vias, heatsinks, and proper copper pours to efficiently dissipate heat generated by active components and prevent overheating.
- Design for Manufacturability (DFM): Follow DFM guidelines to ensure the design is manufacturable with high yield and minimal defects. Consider factors such as minimum trace widths/gaps, solder mask clearances, and component footprint accuracy.
- Signal Integrity Analysis: Perform signal integrity analysis, such as simulations for impedance matching, signal reflections, and timing analysis, to verify design performance and identify potential issues early in the design process.
- Reliability Considerations: Consider environmental factors, such as temperature, humidity, and vibration, during the design phase to ensure the PCB meets reliability requirements over its operational lifespan.
By adhering to these BT epoxy resin PCB design guidelines, designers can create PCB layouts optimized for performance, reliability, and manufacturability, meeting the requirements of diverse electronic applications.
What is the BT Epoxy Resin PCB Fabrication Process?
The fabrication process for BT epoxy resin PCBs involves several steps, each crucial for ensuring the final product meets design specifications and quality standards. Below is an overview of the typical fabrication process:
- Material Preparation: The fabrication process begins with the preparation of the base material, which is typically a laminate composed of layers of BT epoxy resin reinforced with glass fibers. The material is inspected for quality and then cut to the required panel sizes.
- Drilling: Holes for component mounting and interconnection are drilled into the laminate panels using computer-controlled drilling machines. Small diameter drill bits are used for precise hole placement according to the PCB design.
- Through-Hole Plating: After drilling, the panels undergo through-hole plating. This process involves depositing a thin layer of copper onto the walls of the drilled holes through a series of chemical and electroplating steps. The copper plating provides electrical conductivity and ensures reliable interconnections between the PCB layers.
- Copper Pattern Formation: A layer of copper foil is laminated onto the surface of the laminate panels. A photoresist film is applied over the copper layer, and the PCB design’s circuit patterns are transferred onto the panel through photolithography. The unwanted copper is then etched away using chemical etchants, leaving behind the desired copper traces.
- Layer Alignment and Lamination: For multilayer PCBs, individual copper-clad panels are aligned and sandwiched together with prepreg layers (fiberglass impregnated with uncured resin) to form a single composite structure. The layered stack is then pressed under heat and pressure in a lamination press to bond the layers together.
- Outer Layer Imaging: The outer layer circuit patterns are defined by applying a photoresist film and exposing it to UV light through a photomask. After exposure, the unexposed photoresist is developed, leaving behind the patterned resist for subsequent etching.
- Final Etching: Chemical etching is used to remove the unwanted copper from the outer layers, leaving behind the desired circuit traces.
- Surface Finishing: Surface finishing processes such as HASL (Hot Air Solder Leveling), ENIG (Electroless Nickel Immersion Gold), or OSP (Organic Solderability Preservatives) are applied to protect exposed copper surfaces and facilitate soldering during assembly.
- Solder Mask Application: A solder mask layer is applied over the entire surface of the PCB, leaving openings only where soldering is required. This layer protects the copper traces from oxidation and facilitates soldering.
- Silkscreen Printing: Component designators, reference labels, and other identifying information are printed onto the PCB surface using silkscreen printing.
- Final Inspection and Testing: The fabricated PCBs undergo thorough visual inspection, electrical testing, and dimensional verification to ensure they meet the specified quality standards and design requirements.
- Routing and Profiling: Individual PCBs are routed out of the panel and separated. The edges are profiled to achieve the final PCB dimensions.
Following these fabrication steps meticulously ensures the production of high-quality BT epoxy resin PCBs that meet the stringent demands of modern electronic applications.
How do you manufacture a BT Epoxy Resin PCB?
To manufacture a BT epoxy resin PCB, you would follow a detailed process involving several stages. Here’s a step-by-step guide to manufacturing a BT epoxy resin PCB:
- Design Preparation: Develop a comprehensive PCB design using electronic design automation (EDA) software. Ensure the design meets the required specifications, including circuit layout, component placement, and signal integrity considerations.
- Material Selection: Choose high-quality BT epoxy resin laminate materials suitable for your specific application requirements. Consider factors such as dielectric constant, thermal conductivity, and mechanical strength.
- Panel Preparation: Cut the BT epoxy resin laminate material into panels of appropriate sizes, considering the dimensions of the final PCBs and manufacturing constraints.
- Drilling: Use computer-controlled drilling machines to drill holes in the laminate panels according to the PCB design. These holes will accommodate component leads and interconnections between PCB layers.
- Through-Hole Plating: Apply a thin layer of copper onto the walls of the drilled holes through a process called through-hole plating. This copper plating enhances conductivity and ensures reliable electrical connections between PCB layers.
- Circuit Pattern Formation: Apply a layer of copper foil onto the surface of the laminate panels. Use photolithography techniques to transfer the PCB design’s circuit patterns onto the copper foil. Etch away the unwanted copper using chemical etchants, leaving behind the desired copper traces.
- Layer Stacking: For multilayer PCBs, align and stack individual copper-clad panels with prepreg layers (resin-impregnated fiberglass) in the desired configuration. Apply heat and pressure to bond the layers together in a process called lamination.
- Outer Layer Imaging: Define the outer layer circuit patterns by applying a photoresist layer and exposing it to UV light through a photomask. Develop the resist to reveal the patterned areas for subsequent etching.
- Final Etching: Etch away the unwanted copper from the outer layers using chemical etchants, leaving behind the desired circuit traces.
- Surface Finishing: Apply surface finishes such as HASL (Hot Air Solder Leveling), ENIG (Electroless Nickel Immersion Gold), or OSP (Organic Solderability Preservatives) to protect exposed copper surfaces and facilitate soldering during assembly.
- Solder Mask Application: Apply a solder mask layer over the entire PCB surface, leaving openings only where soldering is required. The solder mask protects the copper traces from oxidation and facilitates soldering.
- Silkscreen Printing: Print component designators, reference labels, and other identifying information onto the PCB surface using silkscreen printing techniques.
- Final Inspection and Testing: Thoroughly inspect the fabricated PCBs for visual defects, dimensional accuracy, and electrical continuity. Perform electrical testing to ensure the PCBs meet the specified performance criteria.
- Routing and Profiling: Rout individual PCBs out of the panel and profile their edges to achieve the final dimensions.
Following these steps meticulously ensures the successful manufacture of BT epoxy resin PCBs that meet the required quality standards and performance specifications for various electronic applications.
How much should a BT Epoxy Resin PCB cost?
The cost of a BT epoxy resin PCB can vary significantly depending on various factors such as size, complexity, layer count, material specifications, surface finish, quantity ordered, and supplier pricing. Here are some factors that can influence the cost:
- Size and Complexity: Larger PCBs with complex layouts or densely packed components may require more manufacturing resources and thus cost more to produce.
- Layer Count: Multilayer PCBs typically cost more than single or double-layer boards due to the additional manufacturing processes and materials involved.
- Material Specifications: The choice of BT epoxy resin material, its thickness, and any additional features such as high-frequency laminates or special substrates can affect the cost.
- Surface Finish: Different surface finishes like HASL, ENIG, or OSP have varying costs, with gold-based finishes generally being more expensive than others.
- Quantity Ordered: Bulk orders typically result in lower per-unit costs due to economies of scale. Ordering larger quantities can lead to significant cost savings.
- Turnaround Time: Expedited manufacturing services often come at a premium cost compared to standard lead times.
- Supplier Pricing: The pricing policies of PCB manufacturers and suppliers can vary, so it’s essential to shop around and compare quotes from multiple sources.
As a rough estimate, the cost of a basic BT epoxy resin PCB can range from a few dollars for simple single-layer boards to several hundred dollars or more for complex multilayer PCBs with advanced features. For a more accurate cost estimate, it’s advisable to contact PCB manufacturers or suppliers directly and provide them with detailed specifications for your project. They can then provide you with a customized quote based on your requirements.
What is BT Epoxy Resin PCB base material?
The base material used for BT epoxy resin PCBs is typically composed of a laminate made from Bismaleimide Triazine (BT) resin combined with woven glass fabric reinforcement. This laminate is often referred to as BT epoxy resin or BT resin laminate.
Bismaleimide Triazine (BT) resin is a type of high-performance thermosetting resin known for its excellent electrical properties, mechanical strength, and heat resistance. It provides the PCB with stability, insulation, and durability necessary for various electronic applications.
The woven glass fabric reinforcement provides additional strength and dimensional stability to the laminate, making it suitable for use in multilayer PCBs and applications requiring high reliability and performance.
Overall, the combination of BT resin and glass fabric reinforcement forms the base material for BT epoxy resin PCBs, offering excellent properties for a wide range of electronic circuitry requirements.
Which company makes BT Epoxy Resin PCB?
BT epoxy resin PCBs are typically produced by several electronic manufacturing companies. Some of the well-known companies include AT&S, Ibiden, and Shengyi Technology. These companies have advanced manufacturing equipment and technologies to produce high-quality BT epoxy resin PCBs that meet the requirements of various electronic applications.
Our company is also a professional electronic manufacturing enterprise with rich experience and technical strength, capable of producing high-quality BT epoxy resin PCBs. Our manufacturing process and quality control procedures are strict, ensuring that our products meet the requirements and standards of our customers.
Our BT epoxy resin PCB manufacturing service has the following advantages:
- Customized Production: We can customize BT epoxy resin PCBs of various specifications, layer counts, and complexities according to the requirements of our customers, meeting the needs of different applications.
- Advanced Manufacturing Equipment: We have advanced production equipment and process technologies to achieve high-precision processing and production, ensuring product quality and performance.
- Quality Control: We strictly implement a quality management system from raw material procurement to production and final inspection, ensuring that each batch of products meets relevant standards and customer requirements.
- Timely Delivery: We have efficient production management and logistics distribution systems, enabling us to deliver customer orders on time to meet their production needs and deadlines.
- Professional Team Support: We have a team of experienced and highly skilled professionals who can provide comprehensive technical support and customer service, ensuring customer satisfaction and trust.
In conclusion, our company has the capability and strength to produce BT epoxy resin PCBs, and we are committed to providing customers with high-quality and reliable electronic manufacturing solutions. We welcome customers to cooperate with us for mutual development and growth.
What are the 7 qualities of good customer service?
Good customer service is characterized by several key qualities that contribute to positive interactions and satisfaction for customers. Here are seven essential qualities of good customer service:
- Responsiveness: Good customer service involves being prompt and timely in addressing customer inquiries, concerns, or requests. Responding quickly to customer needs demonstrates attentiveness and a commitment to providing efficient service.
- Empathy: Empathy is the ability to understand and share the feelings of customers, showing genuine concern for their issues or challenges. Empathetic customer service representatives listen actively, acknowledge customer emotions, and strive to offer appropriate solutions or support.
- Professionalism: Professionalism encompasses maintaining a courteous and respectful demeanor when interacting with customers, regardless of the situation. Customer service representatives should exhibit competence, confidence, and reliability in their communication and actions.
- Clarity and Transparency: Effective communication is crucial in customer service. Providing clear and accurate information, explanations, and instructions helps customers understand the resolution process and builds trust. Transparency involves being honest and upfront about policies, fees, and potential limitations.
- Problem-solving Skills: Good customer service involves the ability to identify and resolve customer issues efficiently and effectively. Customer service representatives should possess strong problem-solving skills, creativity, and resourcefulness to address diverse customer concerns and achieve satisfactory outcomes.
- Consistency: Consistency in service delivery ensures that customers receive a uniform and reliable experience across various interactions and touchpoints. Consistent customer service standards, procedures, and quality contribute to building customer loyalty and satisfaction over time.
- Personalization: Tailoring the service experience to meet the unique needs and preferences of individual customers enhances customer satisfaction and loyalty. Personalization involves understanding customer preferences, history, and context to deliver customized solutions and recommendations.
By embodying these qualities, businesses can cultivate positive relationships with customers, foster loyalty, and differentiate themselves in competitive markets.
FAQs
What is BT epoxy resin PCB?
BT epoxy resin PCB refers to a type of printed circuit board made using a base material called Bismaleimide Triazine (BT) resin. These PCBs offer excellent electrical properties, mechanical strength, and heat resistance, making them suitable for various electronic applications.
What are the advantages of BT epoxy resin PCBs?
BT epoxy resin PCBs offer advantages such as high temperature resistance, low dielectric constant, excellent mechanical strength, chemical resistance, dimensional stability, and suitability for high-frequency applications.
What are the typical applications of BT epoxy resin PCBs?
BT epoxy resin PCBs are commonly used in applications requiring high reliability and performance, such as aerospace, automotive, telecommunications, consumer electronics, and industrial equipment.
How are BT epoxy resin PCBs manufactured?
The manufacturing process for BT epoxy resin PCBs involves steps such as material preparation, drilling, through-hole plating, circuit pattern formation, layer stacking (for multilayer PCBs), outer layer imaging, final etching, surface finishing, solder mask application, silkscreen printing, final inspection, and routing/profiling.
What are the design guidelines for BT epoxy resin PCBs?
Design guidelines for BT epoxy resin PCBs include considerations for material selection, layer stackup, trace routing, via design, component placement, power distribution, thermal management, design for manufacturability (DFM), signal integrity analysis, and reliability considerations.
Where can I purchase BT epoxy resin PCBs?
BT epoxy resin PCBs can be purchased from various electronic manufacturing companies, PCB manufacturers, or suppliers specializing in producing high-quality PCBs. It’s essential to choose a reputable supplier that meets your specific requirements and quality standards.
How much do BT epoxy resin PCBs cost?
The cost of BT epoxy resin PCBs varies depending on factors such as size, complexity, layer count, material specifications, surface finish, quantity ordered, and supplier pricing. It’s advisable to request quotes from multiple suppliers to compare prices and ensure cost-effectiveness.
What are the environmental considerations of BT epoxy resin PCBs?
BT epoxy resin PCBs should be manufactured and disposed of responsibly to minimize environmental impact. This may include using environmentally friendly materials, adhering to regulations for hazardous substances, and recycling or disposing of PCBs properly at the end of their lifecycle.