Blind Vias&Buried Vias PCB Manufacturing
Blind Vias&Buried Vias PCB Manufacturing,Blind vias and buried vias PCBs represent advanced technologies in printed circuit board (PCB) design and fabrication. Blind vias are holes that connect the outer layer of the PCB to one or more inner layers, without penetrating the entire board, while buried vias are completely encapsulated within the inner layers. These types of vias enable higher routing density, allowing for more compact and complex PCB designs. By reducing the length of signal paths and minimizing signal interference, blind vias and buried vias contribute to enhanced signal integrity in high-speed electronic devices such as smartphones, computers, and networking equipment. However, their fabrication involves specialized processes like laser drilling and sequential lamination, which can increase manufacturing costs. Despite the challenges, blind vias and buried vias PCBs offer tremendous advantages in terms of space savings, improved performance, and greater design flexibility, making them essential components in modern electronics.
What are Blind Vias&Buried Vias PCB?
Blind vias and buried vias are both types of vias used in printed circuit boards (PCBs) for connecting different layers of the board.
- Blind vias: These are holes that are drilled from the surface of the outer layer of the PCB down to one or more inner layers, but they do not go all the way through the entire board. Blind vias allow connections between the surface layers and some of the inner layers but do not penetrate through the entire thickness of the PCB. They are called “blind” because they are visible only from one side of the board.
- Buried vias: These vias are drilled from within the inner layers of the PCB and do not go through the outer layers. Buried vias are completely encapsulated within the board and are not visible from the surface. They connect one or more inner layers but do not extend to the outer layers.
Both blind and buried vias are used to increase the routing density of PCBs, enabling more compact designs by allowing connections between layers without using up surface area for through-hole vias that go all the way through the board. They are commonly used in high-density, multilayer PCBs found in complex electronic devices such as smartphones, computers, and other advanced electronic equipment.
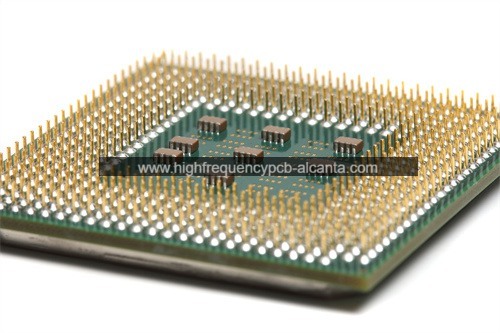
Blind Vias&Buried Vias PCB Manufacturing
What are the Blind Vias&Buried Vias PCB Design Guidelines?
Blind vias and buried vias introduce additional complexity to PCB designs due to their unique nature of connecting different layers without traversing the entire board. Here are some general guidelines for designing PCBs with blind vias and buried vias:
- Aspect Ratio: Keep the aspect ratio of blind vias and buried vias within manageable limits. Aspect ratio refers to the ratio of the depth of the via to its diameter. Higher aspect ratios can increase the difficulty of manufacturing and may lead to reliability issues. Typically, aim for aspect ratios below 10:1.
- Minimum Annular Ring: Maintain an adequate annular ring around vias, especially blind vias, to ensure proper connectivity and reliability. The annular ring is the copper pad around the via. A minimum annular ring ensures sufficient solder connection during assembly.
- Via Pad Size: Adjust the size of the via pads according to the manufacturing capabilities and reliability requirements. Larger via pads provide better mechanical support and thermal dissipation but may increase costs and space consumption.
- Placement: Strategically place blind vias and buried vias to optimize routing density and signal integrity while minimizing signal interference and manufacturing complexity. Consider the signal paths, high-speed signals, and critical components when placing vias.
- Layer Stacking: Plan the layer stackup carefully to accommodate blind vias and buried vias without compromising the structural integrity of the PCB. Ensure that the layer stackup meets the electrical, thermal, and mechanical requirements of the design.
- Manufacturability: Collaborate closely with PCB manufacturers to ensure that the design meets their manufacturing capabilities and constraints. Verify that the design complies with the manufacturer’s guidelines for blind vias and buried vias regarding minimum sizes, tolerances, and process limitations.
- Signal Integrity: Analyze the impact of blind vias and buried vias on signal integrity, impedance control, and electromagnetic compatibility (EMC). Perform signal integrity simulations and impedance calculations to verify that the design meets the required performance criteria.
- Documentation: Clearly document the use of blind vias and buried vias in the PCB design files, including fabrication drawings, assembly drawings, and bill of materials (BOM). Provide detailed instructions and specifications to ensure accurate fabrication and assembly.
By following these guidelines, designers can effectively integrate blind vias and buried vias into PCB designs while ensuring manufacturability, reliability, and performance.
What is the Blind Vias&Buried Vias PCB Fabrication Process?
The fabrication process for PCBs with blind vias and buried vias involves additional steps compared to standard multilayer PCB fabrication. Here’s an overview of the process:
- Layer Preparation:
– Begin with the design of the PCB layers, including the placement of blind vias and buried vias in the PCB layout.
– Each layer of the PCB is typically manufactured individually on a substrate material like FR-4, with copper clad on both sides.
- Drilling:
– Drill vias according to the design specifications. For blind vias, the holes are drilled only partially through the PCB, stopping at the desired inner layer(s). For buried vias, holes are drilled completely through the inner layers.
– Precision drilling equipment is used to ensure accurate placement of the vias.
- Lamination:
– After drilling, the layers are laminated together using heat and pressure to form a single multilayer PCB stack.
– The stack typically consists of alternating layers of copper-clad substrates and prepreg (epoxy resin-impregnated fiberglass) to bond the layers together.
- Through-Hole Plating:
– Through-hole plating is performed to metallize the vias and provide electrical continuity between layers.
– This involves electroplating the vias with a conductive material, usually copper, to fill the drilled holes and create a continuous conductive path.
- Circuit Patterning:
– The outer layers of the PCB are coated with a photoresist material.
– Circuit patterns are then transferred onto the photoresist using a photolithography process, exposing the areas where copper will remain after etching.
- Etching:
– Chemical etching is used to remove unwanted copper from the outer layers, leaving behind the desired circuit traces and pads.
– The etching process is repeated for each layer of the PCB.
- Surface Finishing:
– Surface finishing processes such as HASL (Hot Air Solder Leveling), ENIG (Electroless Nickel Immersion Gold), or immersion tin are applied to protect exposed copper surfaces and improve solderability.
- Final Fabrication Steps:
– Additional fabrication steps may include solder mask application, silkscreen printing, and routing of the PCB edges.
– Quality control inspections are carried out to ensure the PCB meets specifications before it is shipped to assembly.
The fabrication process for PCBs with blind vias and buried vias requires precision and careful coordination to ensure proper alignment and integrity of the vias between layers. Advanced equipment and expertise are necessary to achieve reliable results.
How do you manufacture Blind Vias&Buried Vias PCBs?
Manufacturing PCBs with blind vias and buried vias involves specialized processes to drill, plate, and laminate the layers of the PCB stack. Here’s a detailed overview of how blind vias and buried vias PCBs are manufactured:
- Preparation of Individual Layers:
– Begin with designing the individual layers of the PCB, including the placement of blind vias and buried vias.
– Each layer is typically manufactured separately on a substrate material such as FR-4 with copper foil bonded to both sides.
- Drilling:
– Precision drilling equipment is used to create blind vias and buried vias according to the design specifications.
– For blind vias, holes are drilled partially through the PCB stack, stopping at the desired inner layer(s).
– For buried vias, holes are drilled completely through the inner layers.
– Laser drilling is often employed for blind and buried vias due to its accuracy and ability to drill very small holes.
- Copper Plating:
– After drilling, the vias are plated with a thin layer of copper to provide electrical conductivity and structural support.
– The plating process involves cleaning the vias and then electroplating them with copper to fill the holes.
- Layer Lamination:
– The individual layers of the PCB stack are then laminated together using heat and pressure.
– Layers of copper-clad substrate and prepreg (epoxy resin-impregnated fiberglass) are stacked alternately to bond the layers together.
- Through-Hole Plating:
– Through-hole plating is performed to metallize the vias and provide electrical continuity between layers.
– This involves electroplating the vias with additional copper to ensure a continuous conductive path.
- Circuit Patterning and Etching:
– The outer layers of the PCB stack are coated with a photoresist material.
– Circuit patterns are transferred onto the photoresist using photolithography, exposing areas where copper will remain after etching.
– Chemical etching is then used to remove unwanted copper from the outer layers, leaving behind the desired circuit traces and pads.
- Surface Finishing:
– Surface finishing processes such as HASL (Hot Air Solder Leveling), ENIG (Electroless Nickel Immersion Gold), or immersion tin are applied to protect exposed copper surfaces and improve solderability.
- Final Fabrication Steps:
– Additional fabrication steps may include solder mask application, silkscreen printing, and routing of the PCB edges.
– Quality control inspections are carried out to ensure the PCB meets specifications before it is shipped for assembly.
Manufacturing PCBs with blind vias and buried vias requires advanced equipment and expertise to ensure precise drilling, plating, and lamination processes. Collaboration between PCB designers and manufacturers is essential to achieve the desired results.
How much should Blind Vias&Buried Vias PCBs cost?
The cost of PCBs with blind vias and buried vias can vary significantly depending on several factors, including the complexity of the design, the number of layers, the size of the board, the quantity ordered, the choice of materials, and the manufacturing processes involved. However, generally speaking, PCBs with blind vias and buried vias tend to be more expensive than standard PCBs due to the additional complexity and specialized manufacturing processes required.
Here are some factors that can influence the cost of PCBs with blind vias and buried vias:
- Design Complexity: PCBs with blind vias and buried vias typically involve more complex designs compared to standard PCBs. Complex designs may require more layers, tighter tolerances, and specialized routing, which can increase manufacturing costs.
- Number of Layers: The number of layers in the PCB stackup affects the overall cost. PCBs with blind and buried vias often require more layers to accommodate the vias, which can increase material and manufacturing costs.
- Materials: The choice of materials can impact the cost of PCB fabrication. High-quality materials with specific properties, such as high-speed materials for signal integrity or high-temperature materials for thermal management, may come at a higher cost.
- Manufacturing Processes: Specialized manufacturing processes, such as laser drilling for blind vias or sequential lamination for buried vias, can add to the cost of fabrication.
- Quantity: Larger production quantities typically result in lower per-unit costs due to economies of scale. Ordering in bulk may help reduce the cost per PCB.
- Lead Time: Expedited production or shorter lead times may incur additional fees from the PCB manufacturer.
- Additional Features: Any additional features such as surface finishing options, impedance control, or special testing requirements can contribute to the overall cost.
To obtain an accurate cost estimate for PCBs with blind vias and buried vias, it’s best to consult with PCB manufacturers and provide detailed specifications of your design. They can provide quotes based on your specific requirements and volume needs.
What are Blind Vias&Buried Vias PCB base materials?
The choice of base materials for PCBs with blind vias and buried vias is crucial for achieving the desired performance, reliability, and manufacturability. Here are some common base materials used for these types of PCBs:
- FR-4 (Flame Retardant 4):
– FR-4 is the most widely used substrate material for PCBs due to its cost-effectiveness, mechanical strength, and electrical properties.
– FR-4 materials with high Tg (glass transition temperature) are preferred for PCBs with blind vias and buried vias to ensure dimensional stability during fabrication and operation.
- High-Speed Materials:
– PCBs with blind vias and buried vias often require high-speed materials with controlled dielectric properties to minimize signal loss and maintain signal integrity.
– Materials such as Rogers RO4000 series, Isola FR408, and Nelco N4000 series are commonly used for high-speed applications.
- High-Temperature Materials:
– PCBs operating in high-temperature environments or subjected to elevated temperatures during assembly processes may require materials with high thermal stability.
– Materials such as Isola IS620 and Panasonic Megtron series offer high thermal conductivity and excellent thermal resistance.
- Metal Core Materials:
– Metal core materials such as aluminum or copper provide superior thermal management capabilities, making them suitable for PCBs with blind vias and buried vias in high-power applications.
– Aluminum-based materials like Bergquist IMS or Laird Tlam offer excellent thermal conductivity, while copper-based materials like Ventec VT-4B and Arlon CuClad provide high electrical conductivity.
- Flexible Materials:
– For flexible PCBs with blind vias and buried vias, polyimide (PI) films are commonly used as the base material due to their flexibility, lightweight, and thermal stability.
– Polyimide materials such as DuPont Kapton and Shengyi PI are well-suited for flexible PCB applications.
- Ceramic Materials:
– Ceramic substrates offer exceptional thermal conductivity, mechanical strength, and reliability, making them suitable for high-power and high-frequency applications.
– Alumina (Al2O3) and aluminum nitride (AlN) are commonly used ceramic materials for PCBs requiring excellent thermal management and RF performance.
The choice of base material depends on the specific requirements of the PCB design, including electrical performance, thermal management, mechanical strength, and cost considerations. It’s essential to select a base material that meets the performance requirements while remaining within the project budget. Collaboration with PCB manufacturers and material suppliers can help in selecting the most suitable base material for PCBs with blind vias and buried vias.
Which company manufactures Blind Vias&Buried Vias PCBs?
Many companies can manufacture printed circuit boards (PCBs) with blind vias and buried vias, including some well-known PCB manufacturers and electronic engineering service providers. These companies have advanced technology and equipment to meet various design requirements and provide high-quality products and services.
Our company is also one of them, specializing in the production of PCBs with blind vias and buried vias. We have advanced manufacturing equipment and an experienced engineering team capable of meeting customers’ demands for complex PCB designs. Here are the services and advantages we can provide:
- Technical Expertise: Our engineering team has extensive experience and professional knowledge in designing and manufacturing PCBs with blind vias and buried vias, demonstrating excellent technical capabilities.
- Advanced Equipment: We have state-of-the-art production equipment and technology, including high-precision drilling equipment, laser drilling technology, and advanced plating and lamination processes, ensuring the production of high-quality PCBs.
- Quality Assurance: We strictly adhere to ISO quality management systems and conduct comprehensive quality control and inspection to ensure that each step meets the highest quality standards.
- Customized Services: We can customize PCB design and manufacturing solutions according to customers’ specific requirements, including the selection of different layers, materials, and sizes to meet various application scenarios.
- Timely Delivery: We are committed to providing timely delivery services, ensuring that customers receive customized PCBs on time and maintaining smooth project progress.
- Competitive Advantages: We have competitive advantages in the PCB manufacturing industry, offering competitive prices and excellent customer service to create maximum value for customers.
In summary, our company can manufacture PCBs with blind vias and buried vias and provide first-class service and support. We are dedicated to establishing long-term cooperative relationships with customers, providing them with the best solutions to meet their needs and achieve mutual development.
What are the qualities of good customer service?
Good customer service is characterized by several key qualities that aim to meet and exceed customer expectations while fostering positive relationships. Here are some qualities of good customer service:
- Empathy: Empathy is the ability to understand and share the feelings of customers. Good customer service representatives listen actively to customers’ concerns, show compassion, and demonstrate understanding of their needs and emotions.
- Patience: Patience is essential in dealing with customers, especially when they are frustrated or have complex issues. Good customer service involves remaining calm, attentive, and respectful even in challenging situations, allowing customers to express themselves fully.
- Communication Skills: Effective communication is crucial for providing good customer service. Clear, concise, and courteous communication helps to convey information accurately, answer questions, and address concerns promptly. Active listening and asking clarifying questions are also important aspects of communication.
- Product Knowledge: Good customer service representatives have a thorough understanding of the products or services they are offering. They should be knowledgeable about features, specifications, pricing, and any other relevant information to assist customers effectively.
- Problem-Solving Skills: Good customer service involves being proactive and resourceful in resolving customer issues and complaints. Customer service representatives should be able to analyze problems, explore solutions, and take appropriate action to achieve a satisfactory resolution.
- Responsiveness: Timely responsiveness is essential for providing good customer service. Whether it’s answering phone calls, responding to emails, or addressing inquiries on social media, customers expect prompt and efficient assistance.
- Professionalism: Professionalism encompasses various aspects of behavior, including courtesy, respect, integrity, and reliability. Good customer service representatives maintain professionalism at all times, ensuring that interactions with customers are positive and constructive.
- Adaptability: Good customer service involves being adaptable and flexible to meet the diverse needs and preferences of customers. Customer service representatives should be willing to adjust their approach, communication style, or solutions based on individual customer requirements.
- Follow-Up: Following up with customers after resolving their issues or completing a transaction demonstrates care and commitment to their satisfaction. Good customer service includes proactive follow-up to ensure that customers are fully satisfied with the service provided.
- Continuous Improvement: Good customer service is a continuous process of improvement and refinement. Companies should regularly gather feedback from customers, evaluate service performance, and implement changes to enhance the overall customer experience.
By embodying these qualities, businesses can cultivate a culture of exceptional customer service that builds trust, loyalty, and positive word-of-mouth recommendations.
FAQs
What are blind vias and buried vias?
Blind vias are holes that are drilled from the surface of the outer layer of a PCB down to one or more inner layers, without penetrating through the entire board. Buried vias are holes that are drilled from within the inner layers of the PCB and do not extend to the outer layers.
What are the benefits of using blind vias and buried vias?
Blind vias and buried vias allow for increased routing density, enabling more compact PCB designs. They also reduce signal interference and improve signal integrity by minimizing the length of signal paths.
What are the challenges associated with blind vias and buried vias PCBs?
Blind vias and buried vias PCBs typically involve more complex manufacturing processes and may require additional steps such as laser drilling and sequential lamination. This can increase manufacturing costs and lead times.
What are the applications of blind vias and buried vias PCBs?
Blind vias and buried vias PCBs are commonly used in high-density, multilayer PCB designs found in advanced electronic devices such as smartphones, computers, networking equipment, and automotive electronics.
What factors should be considered when designing blind vias and buried vias PCBs?
Design considerations include aspect ratio, minimum annular ring, via pad size, layer stacking, signal integrity, manufacturability, and material selection. It’s important to collaborate closely with PCB manufacturers to ensure the design meets their capabilities and constraints.
How do blind vias and buried vias affect PCB fabrication and assembly?
Blind vias and buried vias require specialized fabrication processes such as laser drilling and sequential lamination. Assembly may also require additional steps to ensure proper soldering and assembly of components over the vias.
What are the cost implications of using blind vias and buried vias PCBs?
PCBs with blind vias and buried vias tend to be more expensive than standard PCBs due to the additional complexity and specialized manufacturing processes involved. Costs can vary depending on factors such as design complexity, materials used, and production volume.
How can I ensure the reliability of blind vias and buried vias PCBs?
Reliability can be ensured through thorough design validation, adherence to manufacturing guidelines, quality control inspections, and testing. Collaborating with experienced PCB manufacturers and following industry best practices can help mitigate reliability risks.