What is BGA Substrate?
BGA Substrate,BGA Substrate (Ball Grid Array Substrate) is a crucial component for integrated circuit packaging, designed with an array of balls. This packaging technology utilizes solder balls to connect the chip to the Printed Circuit Board (PCB), enabling high-density connections and reliable electrical links. Typically composed of multiple layers of thin films including insulation, metal, and conductor layers, BGA Substrate ensures excellent electrical connections and effective thermal management. Its compact design supports miniaturization, facilitating higher component density and smaller sizes in modern electronic devices, while maintaining performance and reliability.
BGA, short for Ball Grid Array, denotes the substrate that plays a foundational role in facilitating the attachment of a Ball Grid Array package to a circuit board. Within the landscape of integrated circuit packaging, the Ball Grid Array distinguishes itself by employing an array of solder balls to establish connections between the integrated circuit and the printed circuit board.
The BGA substrate assumes a pivotal function, serving as both the structural underpinning and the conduit for connectivity between the BGA package and the circuit board. Typically a sleek, flat material, the substrate is often composed of fiberglass-reinforced epoxy or other materials characterized by commendable electrical and thermal attributes.
The solder balls on the BGA are intricately arranged in a grid configuration on the underside of the package. These solder balls establish contact with corresponding pads on the BGA substrate, adeptly forming the requisite electrical connections between the integrated circuit and the circuit board. BGA packaging finds widespread utility in electronic devices necessitating a high pin count and an efficiently designed space, spanning applications such as microprocessors, memory chips, and various other integrated circuits.
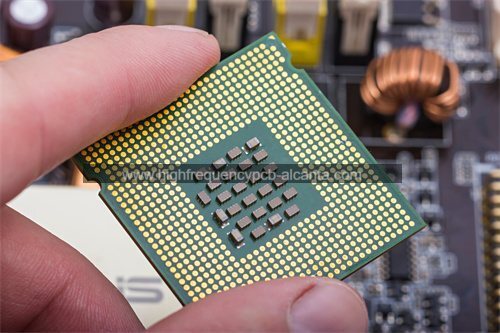
BGA Substrate
What Functionality Does BGA Substrate Serve?
Within the vast landscape of electronic systems and integrated circuits, the BGA (Ball Grid Array) substrate takes center stage as a dynamic linchpin, encapsulating a myriad of essential functions:
Pillar of Stability: At its essence, the substrate establishes itself as a stalwart foundation, imparting resilience and stability to the Ball Grid Array package. This foundational strength acts as a shield against potential damage during the intricate phases of handling, assembly, and operational deployment.
Electrical Nexus: Operating as an adept electrical conduit, the substrate facilitates a seamless interplay between the integrated circuit (IC) nestled within the BGA package and the printed circuit board (PCB). The intentional alignment of solder balls with corresponding pads on the substrate orchestrates a symphony of reliable electrical pathways.
Mastery in Thermal Dynamics: Engineered with a keen focus on thermal conductivity, the BGA substrate excels in the art of dissipating the heat generated by the integrated circuit during its operational odyssey. This prowess in thermal dynamics is pivotal, acting as a vanguard against overheating and ensuring a sustained symphony of optimal performance and reliability.
Guardian of Insulation: Donning the mantle of a formidable insulator, the substrate acts as a protective guardian, thwarting inadvertent electrical encounters between the BGA package and the PCB. This insulation mastery is instrumental in upholding the sanctity of electrical connections and quelling the specter of short circuits.
Precision Choreography: The substrate assumes the role of a precision choreographer, orchestrating the meticulous alignment and positioning of the BGA package on the PCB. This dance of precision is paramount, laying the groundwork for flawless connections between solder balls and their corresponding pads on the board.
Architect of Sleek Designs: Contributing to the ethos of sleek design inherent in BGA packaging, the substrate becomes an architect, facilitating the creation of electronic devices with a minimized footprint and an intensified congregation of components. This architectural finesse aligns harmoniously with the ever-evolving canvas of electronic engineering.
In essence, the BGA substrate unfurls as a multifaceted protagonist, weaving a narrative of robust foundational support, seamless electrical connectivity, thermal dynamics finesse, insulation mastery, precision choreography, and an overarching efficiency in the grand tapestry of electronic component integration.
What Types of BGA Substrate Exist?
BGA (Ball Grid Array) substrates unfold a panorama of diversity, each meticulously designed to harmonize with specific requisites and applications. Embark on a journey through varied BGA substrate nuances:
Organic Substrates:
FR-4 Substrates: Universally embraced, these organic substrates, born from flame-retardant fiberglass-reinforced epoxy, offer economical electrical insulation.
BT Epoxy Substrates: Sculpted from bismaleimide triazine (BT) epoxy, these substrates ascend in thermal prowess, finding resonance in applications demanding fortitude against elevated temperatures.
Ceramic Substrates:
Alumina Substrates: Forged from the crucible of aluminum oxide, alumina substrates emerge as champions, boasting commendable thermal conductivity and robust mechanical resilience. They stand as paragons of excellence in scenarios that beckon for masterful heat dissipation.
Aluminum Nitride (AlN) Substrates: Excelling beyond the thermal conductivity of alumina, AlN substrates take the spotlight as the preferred choice for applications with demanding thermal management requirements.
Flexible Substrates:
Polyimide-based Substrates: Woven from polyimide materials, these flexible substrates offer adaptability, finding their niche in scenarios where rigidity is an encumbrance, often in flexible and bendable electronics.
Metal Core Substrates:
Metal Core PCB (MCPCB): Anchored by a layer of metal, frequently aluminum, as the core material, these substrates glitter in thermal conductivity, making them the darlings of applications necessitating proficient heat dissipation.
High-Frequency Substrates:
Rogers Substrates:Engineered by Rogers Corporation, these high-frequency laminates proudly showcase negligible dielectric loss, earning them a prime spot in the spotlight of RF (Radio Frequency) and microwave circuit applications.
Ceramic-Polymer Hybrids:
Ceramic-Polymer Composite Substrates:Blending the durability inherent in ceramics with the pliability of polymers, these substrates achieve a seamless equilibrium between thermal efficiency and adaptability.
Low-Temperature Co-fired Ceramic (LTCC) Substrates:
LTCC Substrates: Harnessing LTCC (Low-Temperature Co-fired Ceramic) technology entails the controlled firing of ceramic layers at lower temperatures, ushering in opportunities for seamlessly incorporating passive components and weaving conductive traces into a multi-layered architectural symphony.
The meticulous curation of a BGA substrate pivots on considerations such as thermal prerequisites, electrical characteristics, flexibility, and fiscal prudence. Tailoring the substrate choice to specific applications ensures not just functionality but an orchestrated symphony of optimized and efficient performance in the intricate dance of electronic components.
How Does BGA Substrate Differ from PCB?
BGA (Ball Grid Array) substrates and PCBs (Printed Circuit Boards) are distinctive entities in the electronic realm, each contributing unique attributes. Let’s embark on a comparative exploration:
Function:
BGA Substrate: Precision-crafted for BGA configurations, the substrate serves as a dedicated hub for packaging integrated circuits (ICs). Its role spans providing essential support, establishing precise electrical connections, and managing thermal considerations tailored specifically to BGA packages.
PCB: Functioning as the central orchestrator of electronic components, PCBs provide a comprehensive platform for hosting an array of elements, from ICs to resistors, capacitors, and more, ensuring seamless integration and connectivity.
Design and Structure:
BGA Substrate: Characterized by meticulous design, BGA substrates feature solder balls for exact connections, thermal vias for efficient heat dissipation, and an intricately tailored layout designed explicitly for the nuances of BGA packages.
PCB: Embracing a more expansive design landscape, PCBs incorporate traces, pads, and multiple layers, facilitating seamless connectivity across diverse electronic components. Their versatile design caters to the varied specifications and complexities of electronic devices.
Placement of Components:
BGA Substrate: Focused on the singular task of supporting and connecting a specific IC in BGA format, the substrate is engineered with a precision-oriented purpose.
PCB: Providing a dynamic stage, PCBs serve as a holistic platform for hosting and interconnecting a myriad of electronic components, transcending beyond a singular IC package to encompass the entirety of an electronic device’s components.
Integration of Passive Components:
BGA Substrate: In specialized scenarios, BGA substrates may seamlessly integrate passive components directly into the substrate material, resulting in a more compact design suited for specific applications.
PCB: Commonly accommodating passive components like resistors, capacitors, and inductors, PCBs position these elements on the surface or embed them within layers, adapting to the diverse configurations of electronic devices.
Use Cases:
BGA Substrate: Carves its niche in applications where the focal point is the packaging of ICs in the specific BGA format, prevalent in microprocessors, memory chips, and various integrated circuits.
PCB: Ubiquitous across the electronic landscape, PCBs serve as fundamental boards in a spectrum of applications, ranging from simple devices like calculators to sophisticated systems like computers and smartphones.
Complexity and Customization:
BGA Substrate: Tailored with precision for specific IC packages, BGA substrates exhibit a compact and customized layout crafted with a particular IC in mind.
PCB: Renowned for flexibility and adaptability, PCBs accommodate a diverse array of components and configurations, addressing the dynamic and varied needs of electronic devices.
In essence, BGA substrates excel in providing targeted support for specific IC packages, while PCBs stand as versatile and comprehensive circuit boards capable of harmonizing a multitude of electronic elements across varied applications.
What Constitutes the Main Structure and Production Technologies of BGA Substrate?
Crafting a BGA (Ball Grid Array) substrate involves intricacies in composition and fabrication, encompassing crucial elements and manufacturing methodologies. Let’s delve into the essence of the main structure and production technologies:
Main Structure:
Base Material:
Initiated with a foundational base material, the selection hinges on application-specific nuances. Whether opting for the economical FR-4 for general applications or leveraging ceramic materials for heightened thermal performance, this choice lays the groundwork.
Copper Foil Layers:
Layers of copper foil are meticulously laminated onto the base material, weaving a network of conductive pathways that interconnect various components on the substrate.
Dielectric Layers:
Woven amidst copper layers, dielectric layers act as electrical sentinels, preventing unintended short circuits and bolstering the substrate’s overall electrical integrity.
Via Structures:
Enter the plated vias, drilled conduits that traverse substrate layers, fostering electrical connections across different strata and elevating the substrate’s functional prowess.
Solder Mask:
A protective solder mask is deftly applied, shielding conductive traces from environmental elements and mitigating inadvertent solder connections during the intricate assembly dance.
Surface Finish:
The stage is set with surface finishes like HASL, ENIG, or OSP, bestowing upon exposed copper surfaces the finesse required for seamless soldering, thereby enhancing the substrate’s reliability.
Solder Balls:
Enter the BGA configuration with an array of solder balls adorning the substrate’s underbelly, poised to establish connections during the balletic assembly onto the host PCB or other electronic companions.
Production Technologies:
Lamination:
Layers unite in a dance of lamination, orchestrating the fusion of base material, copper foils, and dielectric layers to birth a multilayered core structure.
Drilling:
Precision drilling, whether orchestrated by lasers or mechanical prowess, carves meticulously crafted holes for vias and other vital connections, adhering to the symphony of design specifications.
Copper Plating:
Copper plating enters the stage, adorning drilled holes with conductive grace, ensuring a seamless electrical ballet between different layers of the substrate.
Solder Mask Application:
The choreography continues with the application of the solder mask, a protective dance partner leaving strategic openings for exposed copper regions awaiting their solder embrace.
Surface Finish:
Surface finishes take center stage, each playing its part—be it HASL, ENIG, or OSP—in bestowing upon exposed copper surfaces the allure required for a flawless soldering performance.
Solder Ball Attachment:
The BGA act unfolds with the meticulous attachment of solder balls to the substrate’s underside, a crucial step in the assembly’s grand finale onto the awaiting host PCB.
Testing and Inspection:
The crescendo is reached with rigorous testing and inspection, where the performance, dimensions, and overall quality of the finished BGA substrates take center stage.
Through the harmonious integration of these elements and the finesse of production technologies, BGA substrates emerge, tailored to meet the intricate demands of diverse electronic applications.
Frequently Asked Questions (FAQs) about BGA Substrate
What Defines a BGA Substrate?
A BGA substrate is a specialized board designed for packaging integrated circuits (ICs) in a Ball Grid Array configuration. It offers crucial support, electrical connectivity, and efficient thermal management for the housed IC.
What Elements Constitute the Core Structure of a BGA Substrate?
The core structure comprises a base material, copper foil layers, dielectric layers, via structures, solder mask, surface finish, and, in BGA packages, solder balls affixed to the bottom side.
Which Manufacturing Technologies are Involved in BGA Substrate Production?
The production process encompasses lamination for layer integration, precision drilling for via creation, copper plating for conductive pathways, solder mask application for protection, surface finish application for solderability, solder ball attachment for BGA configurations, and comprehensive testing and inspection.
What Materials Are Commonly Used for BGA Substrates?
BGA substrates can be crafted from diverse materials. While FR-4 is a prevalent choice for general applications, ceramic materials are preferred for enhanced thermal performance.
In Which Applications Are BGA Substrates Widely Deployed?
BGA substrates find their niche in a spectrum of electronic devices, particularly those benefitting from the advantages of IC packaging in a BGA format. This encompasses microprocessors, memory chips, and various integrated circuits.
How Are BGA Substrates Subjected to Quality Assurance?
BGA substrates undergo meticulous testing and inspection, encompassing electrical tests to verify connectivity, dimensional checks for precision, and comprehensive quality assessments aligned with industry standards.
What Role Do Solder Balls Play in BGA Substrates?
Solder balls, integral in BGA configurations, are attached to the substrate’s underside. They act as pivotal connection points during assembly onto the host PCB or other components, ensuring secure electrical connections.
Can BGA Substrates Incorporate Passive Components?
Yes, in specific scenarios, BGA substrates may seamlessly integrate passive components directly into the substrate material, fostering a more compact design tailored for specialized applications.
Conclusion
In conclusion, BGA (Ball Grid Array) substrates stand as pivotal components in the intricate landscape of electronic systems. Tailored for the precise packaging of integrated circuits (ICs) in a BGA format, these substrates exhibit a specialized design and functionality that sets them apart from standard PCBs.
The main structure of a BGA substrate, encompassing elements such as base material, copper foil layers, dielectric layers, via structures, solder mask, surface finish, and solder balls (in BGA configurations), underscores a meticulous engineering process. This process involves advanced production technologies, including lamination, precision drilling, copper plating, solder mask application, surface finish application, solder ball attachment, and rigorous testing and inspection.
The versatility of BGA substrates extends across various materials, with FR-4 and ceramic materials being common choices, each offering distinct advantages. Surface finish options, such as HASL, ENIG, and OSP, cater to specific requirements, emphasizing factors like cost, solderability, and application nuances.
BGA substrates find their application niche in electronic devices, particularly those benefitting from the advantages of IC packaging in a BGA format. Microprocessors, memory chips, and diverse integrated circuits rely on the precision and efficiency that BGA substrates bring to the realm of electronic packaging.
In essence, BGA substrates serve as architectural cornerstones, embodying a fusion of materials, design intricacies, and manufacturing precision. Their role in providing robust support, efficient electrical connections, and tailored thermal management reinforces their significance in shaping the landscape of modern electronics. Whether integrated into complex computing systems or embedded in everyday devices, BGA substrates play a crucial role in advancing the capabilities and miniaturization of electronic components.