Aviation Substrate Manufacturer
Aviation Substrate Manufacturer,Mixed Dielectric Rogers PCBs combine multiple types of dielectric materials to optimize performance for high-frequency applications. These printed circuit boards (PCBs) use Rogers laminates, renowned for their superior electrical properties, including low dielectric loss and minimal signal attenuation. By integrating different dielectric materials, such as FR-4 with Rogers laminates, these PCBs can achieve a balanced cost-to-performance ratio. The hybrid design allows engineers to strategically use high-performance materials where needed, such as in RF and microwave circuits, while utilizing more cost-effective substrates for less critical areas. This approach enhances signal integrity, reduces transmission losses, and improves overall circuit performance, making Mixed Dielectric Rogers PCBs ideal for advanced telecommunications, aerospace, and military applications. Their versatility and reliability enable the development of cutting-edge electronic devices that demand precise signal control and high-frequency operation.
What is an Aviation Substrate?
Aviation Substrate Manufacturer and package substrate Manufacturer. We use advanced Msap and Sap technology, High multilayer interconnection substrates from 4 to 18 layers,
An Aviation Substrate is a term commonly used in the context of aviation electronics and systems. It refers to the foundational platform or base upon which various aviation systems, such as avionics, flight control systems, navigation systems, and communication systems, are built and integrated.
Think of it as the underlying framework that provides the necessary infrastructure, interfaces, and compatibility for these systems to operate effectively and safely within an aircraft. The aviation substrate typically includes components like processors, memory modules, input/output interfaces, power management circuits, and communication protocols.
One key aspect of aviation substrates is their reliability and robustness, as they must adhere to stringent safety standards and regulations set by aviation authorities. They need to withstand harsh environmental conditions, vibrations, electromagnetic interference, and other challenges commonly encountered during flight.
Moreover, aviation substrates often incorporate redundancy and fault-tolerant features to ensure continued operation even in the event of component failures or system malfunctions, thus contributing to the overall safety and reliability of the aircraft.
In essence, the aviation substrate forms the backbone of modern aircraft electronics, enabling the seamless integration and operation of various critical systems essential for safe and efficient flight.
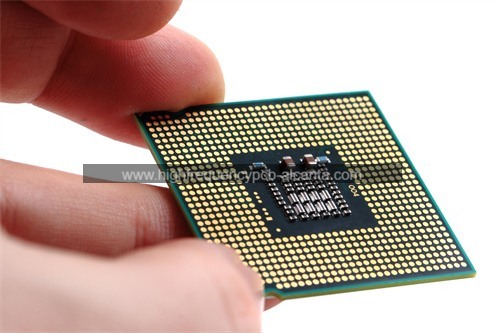
Aviation Substrate Manufacturer
What are Aviation Substrate Design Guidelines?
Aviation Substrate Design Guidelines are a set of principles, standards, and best practices that guide the development and implementation of aviation substrates in aircraft electronics and systems. These guidelines aim to ensure the reliability, safety, and performance of aviation substrates in compliance with industry regulations and standards.
Here are some key aspects typically covered by Aviation Substrate Design Guidelines:
- Reliability and Safety: Emphasis is placed on designing substrates that are highly reliable and robust, capable of operating under extreme environmental conditions encountered in aviation, such as temperature variations, vibrations, and electromagnetic interference. Safety features are integrated to minimize the risk of system failures or malfunctions that could compromise flight safety.
- Compatibility and Interoperability: Guidelines address the need for aviation substrates to be compatible with a wide range of avionics systems, sensors, and communication protocols commonly used in aircraft. Interoperability ensures seamless integration and communication between different subsystems, promoting efficiency and reliability in flight operations.
- Redundancy and Fault Tolerance: Design guidelines often recommend incorporating redundancy and fault-tolerant features into aviation substrates to mitigate the impact of component failures or system errors. Redundant components and fail-safe mechanisms are implemented to maintain system functionality and prevent single points of failure.
- Standardization and Certification: Adherence to industry standards and certification requirements, such as those set by organizations like RTCA (Radio Technical Commission for Aeronautics) and EUROCAE (European Organization for Civil Aviation Equipment), is essential. Design guidelines ensure that aviation substrates comply with relevant standards and undergo rigorous testing and certification processes to meet regulatory requirements.
- Power and Thermal Management: Efficient power management and thermal dissipation are critical considerations in aviation substrate design. Guidelines provide recommendations for optimizing power consumption, managing heat generation, and ensuring adequate cooling to prevent overheating and maintain system performance.
- Security and Cybersecurity: With the increasing connectivity of aircraft systems, cybersecurity considerations are becoming more important. Design guidelines may include recommendations for implementing security measures to protect aviation substrates from cyber threats and unauthorized access, ensuring the integrity and confidentiality of critical flight data.
Overall, Aviation Substrate Design Guidelines serve as a roadmap for engineers and developers to design, evaluate, and deploy aviation substrates that meet the demanding requirements of the aviation industry in terms of reliability, safety, and performance.
What is the Aviation Substrate Fabrication Process?
The Aviation Substrate Fabrication Process involves several stages of manufacturing and assembly to create the foundational platform upon which various aviation systems and electronics are built. While specific details may vary depending on the complexity and requirements of the substrate, here’s a generalized overview of the fabrication process:
- Design and Specification: The process begins with the design phase, where engineers develop the specifications and layout for the aviation substrate based on the requirements of the intended applications. This phase involves determining the size, shape, component placement, signal routing, and other critical parameters.
- Material Selection: Once the design is finalized, appropriate materials are selected for the substrate construction. These materials must possess properties such as high strength, thermal conductivity, electrical insulation, and resistance to environmental factors like moisture, vibration, and electromagnetic interference.
- Substrate Manufacturing: The fabrication of the substrate typically involves precision machining or etching techniques to create the desired structure and features according to the design specifications. This may include processes such as milling, drilling, laser cutting, or chemical etching to shape the substrate and create holes, channels, and mounting points for components.
- Component Mounting and Assembly: Once the substrate is manufactured, electronic components such as processors, memory modules, connectors, and sensors are mounted onto the substrate using soldering, adhesive bonding, or other assembly techniques. Careful attention is paid to component placement and orientation to ensure proper functionality and compatibility with surrounding systems.
- Wiring and Interconnects: Wiring harnesses, cables, and interconnects are then installed to establish electrical connections between components and subsystems on the substrate. This involves routing signal traces, power lines, and communication channels according to the design requirements while minimizing signal interference and maintaining signal integrity.
- Testing and Quality Assurance: After assembly, the aviation substrate undergoes rigorous testing and quality assurance procedures to verify its functionality, reliability, and adherence to performance specifications. This may include electrical testing, functional testing, thermal testing, vibration testing, and environmental testing to simulate real-world operating conditions and identify any defects or issues that need to be addressed.
- Documentation and Certification: Finally, comprehensive documentation is prepared detailing the fabrication process, specifications, test results, and compliance with relevant standards and regulations. Depending on the intended use of the aviation substrate, certification from regulatory authorities such as the Federal Aviation Administration (FAA) may be required to ensure compliance with aviation safety standards.
By following a systematic and controlled fabrication process, aviation substrates can be manufactured to meet the demanding requirements of the aviation industry in terms of reliability, safety, and performance.
How do you manufacture an Aviation Substrate?
Manufacturing an aviation substrate involves several steps to create a robust and reliable platform for integrating various avionics systems and electronics. Here’s a step-by-step overview of the manufacturing process:
- Design Phase: The process begins with the design phase, where engineers define the specifications and layout of the aviation substrate based on the requirements of the intended applications. This phase involves determining the size, shape, material selection, component placement, signal routing, and other critical parameters.
- Material Selection: Once the design is finalized, appropriate materials are selected for the substrate construction. Common materials include high-strength metals (e.g., aluminum, stainless steel) or composite materials (e.g., fiberglass, carbon fiber) that offer excellent mechanical properties, thermal conductivity, and electrical insulation.
- Substrate Fabrication: The substrate is manufactured using precision machining or fabrication techniques to create the desired structure according to the design specifications. This may involve processes such as milling, drilling, laser cutting, chemical etching, or additive manufacturing (e.g., 3D printing) to shape the substrate and create features such as holes, channels, mounting points, and surface coatings.
- Component Mounting: Electronic components such as processors, memory modules, connectors, sensors, and other devices are mounted onto the substrate using soldering, adhesive bonding, or mechanical fastening methods. Careful attention is paid to component placement and orientation to ensure proper functionality and compatibility with surrounding systems.
- Interconnects and Wiring: Wiring harnesses, cables, and interconnects are installed to establish electrical connections between components and subsystems on the substrate. This involves routing signal traces, power lines, and communication channels according to the design requirements while minimizing signal interference and maintaining signal integrity.
- Testing and Quality Assurance: The completed aviation substrate undergoes rigorous testing and quality assurance procedures to verify its functionality, reliability, and compliance with performance specifications. This may include electrical testing, functional testing, thermal testing, vibration testing, and environmental testing to simulate real-world operating conditions and identify any defects or issues that need to be addressed.
- Documentation and Certification: Comprehensive documentation is prepared, detailing the manufacturing process, specifications, test results, and compliance with relevant standards and regulations. Depending on the intended use of the aviation substrate, certification from regulatory authorities such as the Federal Aviation Administration (FAA) may be required to ensure compliance with aviation safety standards.
By following these manufacturing steps with precision and attention to detail, aviation substrates can be fabricated to meet the demanding requirements of the aviation industry in terms of reliability, safety, and performance.
How much should an Aviation Substrate cost?
The cost of an aviation substrate can vary significantly depending on various factors such as its complexity, size, materials used, manufacturing processes, and additional features or specifications required for specific applications. Here are some factors that can influence the cost:
- Complexity: The complexity of the aviation substrate, including the number and type of components, the sophistication of the design, and the level of integration required, can impact the cost. More complex substrates typically require higher manufacturing costs due to increased labor, materials, and testing.
- Materials: The choice of materials for the substrate construction can affect the cost. High-quality materials with specific properties such as strength, thermal conductivity, and electrical insulation may be more expensive than standard materials.
- Manufacturing Processes: The manufacturing processes used to fabricate the substrate, such as precision machining, laser cutting, chemical etching, or additive manufacturing, can influence the cost. Advanced manufacturing techniques may require specialized equipment and skilled labor, contributing to higher production costs.
- Testing and Quality Assurance: Rigorous testing and quality assurance procedures are essential to ensure the reliability and safety of aviation substrates. The cost of testing and certification can vary depending on the complexity of the substrate and the regulatory requirements.
- Volume: The volume of substrates being produced can impact the unit cost. Larger production volumes often lead to economies of scale, where the cost per unit decreases as the quantity increases due to efficiencies in production processes and bulk purchasing of materials.
- Additional Features: Additional features or specifications such as redundancy, fault tolerance, enhanced security, or specialized environmental protection may increase the cost of the substrate.
- Regulatory Compliance: Compliance with aviation safety standards and regulatory requirements, such as certification from authorities like the Federal Aviation Administration (FAA) or the European Aviation Safety Agency (EASA), can add to the cost of manufacturing through additional testing and documentation requirements.
Given the wide range of factors influencing the cost, it’s challenging to provide a specific price without detailed information about the substrate’s requirements and specifications. Typically, aviation substrates are custom-designed and manufactured to meet the specific needs of the aircraft and avionics systems they support, and costs can vary accordingly.
What is Aviation Substrate base material?
The choice of base material for aviation substrates depends on various factors such as the specific application, performance requirements, environmental conditions, and regulatory standards. However, some common materials used as base materials for aviation substrates include:
- Aluminum:Aluminum is widely used in aviation substrates due to its lightweight properties, high strength-to-weight ratio, and excellent thermal conductivity. It is often used for substrates where weight reduction is critical, such as in aircraft avionics racks and enclosures.
- Stainless Steel: Stainless steel is valued for its corrosion resistance and durability, making it suitable for aviation substrates exposed to harsh environmental conditions, such as those in aircraft engine compartments or exterior components.
- Composite Materials: Composite materials, such as fiberglass, carbon fiber, or aramid fiber reinforced polymers, are increasingly used in aviation substrates for their high strength, stiffness, and light weight. These materials offer advantages in weight reduction and can be tailored to specific performance requirements.
- Ceramics: Ceramics are used in aviation substrates for their high temperature resistance and electrical insulation properties. They are commonly employed in applications requiring thermal management, such as in power electronics or high-power radio frequency (RF) systems.
- Specialized Alloys: Certain specialized alloys, such as titanium alloys or nickel-based superalloys, may be used in aviation substrates for applications requiring exceptional strength, corrosion resistance, or heat resistance, such as in turbine engine components or structural elements.
The selection of base material depends on factors such as structural requirements, thermal management needs, weight considerations, electrical properties, and cost constraints. Additionally, aviation substrates often incorporate coatings or surface treatments to enhance properties such as corrosion resistance, electrical conductivity, or thermal dissipation, further enhancing their performance and longevity in aircraft applications.
Which company makes Aviation Substrates?
Many companies have rich experience and expertise in manufacturing aviation substrates. Some well-known companies include Honeywell, Rockwell Collins, BAE Systems, Thales, and UTC Aerospace Systems. These companies have strong technical capabilities and advanced manufacturing facilities in the field of aviation electronics, enabling them to design, develop, and produce various types of aviation substrates to support various aircraft systems and electronic devices.
As for our company, we also have the capability to produce aviation substrates. We have a professional team, including engineers and technicians, who have rich experience and expertise in aviation electronics manufacturing. Our manufacturing facilities are equipped with advanced processing equipment and testing devices, capable of meeting the high requirements of aviation substrates, including reliability, safety, and performance.
Our company can customize aviation substrates according to customer requirements and specifications to meet the requirements of various aviation applications. We can provide a variety of material options, including aluminum alloys, stainless steel, composite materials, etc., as well as various manufacturing processes such as precision machining, chemical etching, laser cutting, etc., to meet the needs of different projects.
Furthermore, our company focuses on quality management and technological innovation, committed to continuously improving product quality and technological level. We have a strict quality control system and quality testing process to ensure that each aviation substrate meets the highest standards and customer requirements. At the same time, we actively explore new materials and manufacturing technologies to provide more advanced and reliable aviation substrate solutions.
In summary, our company has the capability to produce aviation substrates and can provide customized solutions according to customer requirements. We are dedicated to providing high-quality, highly reliable products for the aviation electronics industry and strive for the success and satisfaction of our customers.
What are the 7 qualities of good customer service?
Good customer service is characterized by several key qualities that contribute to positive interactions and satisfaction for customers. Here are seven qualities of good customer service:
- Responsiveness: Good customer service involves being prompt and proactive in addressing customer inquiries, concerns, and requests. Responding to customer needs in a timely manner demonstrates attentiveness and shows customers that their issues are being taken seriously.
- Empathy: Empathy is the ability to understand and share the feelings of others. Good customer service representatives empathize with customers by actively listening to their concerns, acknowledging their emotions, and demonstrating understanding and compassion.
- Clear Communication: Effective communication is essential for good customer service. Customer service representatives should communicate clearly and concisely, using language that is easy to understand. They should provide accurate information, clarify any uncertainties, and avoid misunderstandings.
- Problem-solving Skills:Good customer service involves the ability to resolve customer issues and problems efficiently and effectively. Customer service representatives should possess strong problem-solving skills, be resourceful in finding solutions, and take ownership of resolving customer concerns.
- Professionalism: Professionalism is demonstrated through courteous behavior, respectful interactions, and maintaining a positive attitude, even in challenging situations. Good customer service representatives conduct themselves professionally at all times and strive to uphold the company’s reputation.
- Consistency: Consistency is key to building trust and loyalty with customers. Good customer service involves delivering a consistent level of service across all interactions and touchpoints, ensuring that customers receive the same quality of service every time they engage with the company.
- Follow-up and Follow-through: Following up with customers and following through on commitments demonstrates commitment to customer satisfaction. Good customer service representatives take responsibility for ensuring that customer issues are fully resolved and may follow up with customers to ensure their needs have been met satisfactorily.
By embodying these qualities, organizations can provide exceptional customer service experiences that foster positive relationships with customers and contribute to long-term success and customer loyalty.
FAQs (Frequently Asked Questions)
What is an Aviation Substrate (AS)?
An Aviation Substrate (AS) is a foundational platform used in aviation electronics and systems. It serves as the base upon which various avionics systems, such as flight control, navigation, and communication systems, are built and integrated within an aircraft.
What are the components of an Aviation Substrate?
Aviation substrates typically include components such as processors, memory modules, input/output interfaces, power management circuits, communication protocols, and other electronic components necessary for the operation of avionics systems.
What are the key features of a high-quality Aviation Substrate?
High-quality aviation substrates should exhibit reliability, robustness, compatibility, and adherence to safety standards. They should be capable of withstanding harsh environmental conditions, vibrations, electromagnetic interference, and should incorporate redundancy and fault-tolerant features.
How are Aviation Substrates manufactured?
The manufacturing process of aviation substrates involves several stages, including design, material selection, substrate fabrication, component mounting, wiring, testing, and certification. Advanced machining, assembly, and testing techniques are employed to ensure the quality and reliability of the substrates.
What are the main applications of Aviation Substrates?
Aviation substrates are used in a wide range of applications within aircraft avionics systems, including flight control, navigation, communication, surveillance, and monitoring systems. They provide the necessary infrastructure for integrating and operating these critical systems effectively and safely.
What factors should be considered when selecting an Aviation Substrate?
Factors to consider when selecting an aviation substrate include compatibility with existing avionics systems, reliability, performance, regulatory compliance, environmental ruggedness, and cost-effectiveness.
What are the industry standards and certifications relevant to Aviation Substrates?
Aviation substrates must adhere to industry standards and certifications, such as those set by organizations like RTCA (Radio Technical Commission for Aeronautics) and EUROCAE (European Organization for Civil Aviation Equipment). Additionally, certification from regulatory authorities like the Federal Aviation Administration (FAA) may be required.
Can Aviation Substrates be customized for specific aircraft applications?
Yes, aviation substrates can be customized to meet the specific requirements and specifications of different aircraft applications. Customization may involve modifying the design, materials, components, or features of the substrate to suit the needs of the aircraft and avionics systems.