Antenna High Frequency Substrate Manufacturer
Antenna High Frequency Substrate Manufacturer,An antenna high-frequency substrate is a specialized material designed to support the performance and efficiency of antennas operating at high frequencies. These substrates are characterized by their low dielectric constant and low loss tangent, which minimize signal loss and enhance signal transmission quality. Commonly used in applications such as satellite communications, radar systems, and wireless networks, these substrates ensure consistent electrical performance and stability. They often feature materials like PTFE, ceramics, or advanced composites that offer excellent thermal management and mechanical durability. The precise engineering of high-frequency substrates is critical for optimizing antenna performance in demanding and high-frequency environments.
What is an Antenna High Frequency Substrate?
Antenna High Frequency Substrates (AHF Substrates) are specialized materials used in the fabrication of antennas that operate at high-frequency ranges, typically from 1 GHz to several hundred GHz. These substrates play a crucial role in ensuring optimal antenna performance by providing the necessary electrical, thermal, and mechanical properties.
The primary function of AHF substrates is to support the antenna elements while minimizing losses and distortion. Key characteristics of these substrates include low dielectric loss, high dielectric constant, and stable thermal properties, which help maintain the antenna’s efficiency and bandwidth. Materials commonly used for AHF substrates include PTFE (Teflon), ceramic composites, and advanced epoxy laminates, each chosen based on specific application needs.
In high-frequency applications, such as microwave communication, radar systems, and satellite communications, the choice of substrate can significantly impact the antenna’s performance, including gain, radiation patterns, and impedance matching. Therefore, engineers often conduct thorough simulations and testing to select the most suitable substrate material for their designs.
Additionally, advancements in substrate technology have led to the development of materials with enhanced properties, such as increased thermal conductivity and reduced weight, further improving the performance of high-frequency antennas. These innovations are essential in meeting the growing demand for compact, efficient, and high-performance communication systems in various industries, including telecommunications, aerospace, and automotive.
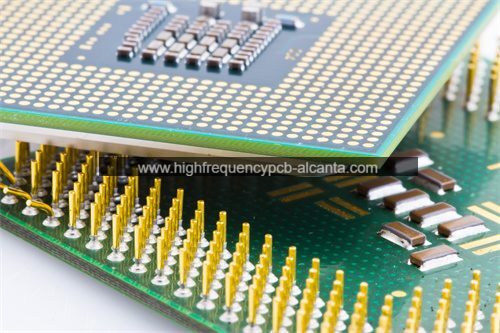
Antenna High Frequency Substrate Manufacturer
What are the Antenna High Frequency Substrate Design Guidelines?
Designing Antenna High Frequency Substrates involves several key guidelines to ensure optimal performance:
- Material Selection: Choose substrates with low dielectric loss (e.g., PTFE, ceramics) to minimize signal attenuation. The dielectric constant should be suitable for the desired frequency range.
- Thickness: The substrate thickness affects impedance and radiation patterns. Thicker substrates can provide better mechanical stability, while thinner substrates may be preferred for compact designs.
- Surface Finish: Ensure a smooth surface finish to reduce surface roughness, which can affect performance, especially at high frequencies.
- Thermal Management: Consider materials with good thermal conductivity to manage heat dissipation, especially in high-power applications.
- Impedance Matching: Design the substrate layout to facilitate impedance matching between the antenna and transmission lines, optimizing signal transmission and minimizing reflections.
- Mechanical Stability: Ensure the substrate provides mechanical stability to withstand environmental stresses (e.g., temperature fluctuations, humidity).
- Fabrication Tolerances: Account for tolerances in the manufacturing process to maintain the accuracy of critical dimensions, such as antenna element spacing and trace widths.
- EM Simulation: Use electromagnetic simulation tools during the design phase to evaluate antenna performance, optimize geometry, and refine substrate parameters.
- Testing and Prototyping: Prototype and test the design under real conditions to validate performance and identify potential issues before full-scale production.
By adhering to these guidelines, engineers can design effective high-frequency antenna substrates that meet the performance requirements of modern communication systems.
What is the Antenna High Frequency Substrate Fabrication Process?
The fabrication process for Antenna High Frequency Substrates typically involves several key steps:
- Material Selection: Choose an appropriate substrate material (e.g., PTFE, ceramics) based on electrical properties, mechanical strength, and thermal stability.
- Material Preparation: Cut the substrate material into sheets of the required size. This may involve precision cutting to ensure uniform thickness.
- Surface Treatment: Depending on the material, the surface may need to be treated to improve adhesion for subsequent layers or coatings. This can include cleaning, etching, or applying a primer.
- Circuit Patterning: Employ photolithography or direct laser writing to define the antenna patterns on the substrate. This involves applying a photoresist layer, exposing it to UV light through a mask, and developing the pattern.
- Etching: Remove unwanted substrate material using chemical or plasma etching techniques to create the desired antenna structure. This step can define features such as traces and slots.
- Deposition: Apply metal layers (e.g., copper) for the antenna elements through processes like sputtering, electroplating, or lamination. Ensure a uniform thickness to maintain consistent electrical properties.
- Curing: If using polymer-based substrates, a curing step may be necessary to harden the material, improving durability and thermal stability.
- Trimming and Finishing: Cut the substrate to the final dimensions and apply any additional finishes, such as surface coatings to enhance performance or protect against environmental factors.
- Testing: Perform electrical testing (e.g., impedance matching, radiation pattern analysis) to verify the antenna’s performance and make adjustments if necessary.
- Final Inspection: Conduct a quality control inspection to ensure all specifications are met before packaging and delivery.
This process ensures that the antenna high-frequency substrate meets the specific performance requirements for applications in telecommunications, radar, and other high-frequency systems.
How do you manufacture an Antenna High Frequency Substrate?
Manufacturing an Antenna High Frequency Substrate involves several key steps:
- Material Selection: Choose a high-frequency substrate material, such as PTFE, ceramic, or advanced epoxy composites, based on required electrical properties like low dielectric loss and high thermal stability.
- Cutting and Shaping: Cut the selected material into sheets of desired dimensions. Precision cutting ensures uniform thickness and size.
- Surface Preparation: Clean and prepare the surface to enhance adhesion for any metal layers or coatings applied later. This may include mechanical abrasion or chemical cleaning.
- Circuit Patterning: Utilize photolithography or laser direct writing to create the antenna pattern. Apply a photoresist layer, expose it to UV light through a mask, and develop the pattern to define the antenna elements.
- Etching: Employ chemical or plasma etching to remove excess material and achieve the desired antenna structure, including traces and slots.
- Metal Deposition: Apply metal layers (usually copper) through processes like sputtering or electroplating to form the antenna conductors.
- Curing (if applicable): For polymer-based substrates, cure the material as necessary to enhance its mechanical and thermal properties.
- Trimming and Finishing: Cut the substrate to final dimensions and apply any necessary surface finishes or coatings for protection and improved performance.
- Electrical Testing:Conduct testing to verify antenna performance metrics, such as impedance matching and radiation patterns.
- Quality Control: Perform final inspections to ensure the substrate meets design specifications and performance criteria before packaging for delivery.
These steps create a high-quality substrate optimized for high-frequency applications in telecommunications, radar, and other advanced technologies.
How much should an Antenna High Frequency Substrate cost?
The cost of an Antenna High Frequency Substrate can vary widely based on several factors, including:
- Material Type: High-frequency materials like PTFE, ceramics, or specialized composites generally have different pricing structures, with ceramics typically being more expensive.
- Thickness and Size: Custom sizes or thicker substrates can increase costs. Standard sizes are often more economical.
- Complexity of Design: More intricate designs that require precise manufacturing processes (like photolithography) will typically cost more due to additional labor and technology involved.
- Quantity:Bulk orders usually lead to lower per-unit costs. Small quantities or prototypes tend to be more expensive on a per-piece basis.
- Supplier and Manufacturing Location: Costs can vary based on the supplier’s reputation, manufacturing location, and any additional services (like testing or certification) offered.
As a rough estimate, basic AHF substrates can range from $50 to several hundred dollars per unit, while specialized or high-performance substrates could exceed $1,000. It’s best to consult specific manufacturers for accurate pricing based on your requirements.
What is an Antenna High Frequency Substrate Base Material?
An Antenna High Frequency Substrate Base Material is the foundational material used in the construction of high-frequency antennas, designed to support the antenna structure while optimizing performance characteristics such as signal integrity, thermal stability, and mechanical strength.
Common base materials include:
- PTFE (Teflon): Known for its low dielectric loss and excellent thermal stability, making it ideal for microwave applications.
- Ceramic Materials: Provide high thermal conductivity and low loss, suitable for high-power and high-frequency applications.
- Epoxy Composites: Advanced epoxy materials offer good mechanical properties and can be engineered for specific dielectric characteristics.
- Liquid Crystal Polymer (LCP):These materials exhibit low loss and high thermal resistance, making them suitable for compact, high-performance designs.
Each base material is selected based on the specific requirements of the antenna application, such as frequency range, environmental conditions, and desired performance metrics. The choice of material significantly influences the antenna’s efficiency, bandwidth, and overall effectiveness in various communication systems.
Which company makes Antenna High Frequency Substrates?
In the field of high-frequency antenna substrates, there are several well-known companies that provide specialized solutions. These companies typically focus on the research and production of high-frequency materials to ensure their products meet the demands of high-frequency communications, radar systems, and other related applications.
First, ROGERS Corporation is a leading materials supplier specializing in high-frequency circuit materials and substrates. Their product range includes various low-loss PTFE and ceramic substrates that are widely used in microwave and RF technologies. ROGERS materials are recognized in the industry for their excellent electrical performance and thermal stability.
Secondly, Taconic is also an influential company in the high-frequency antenna substrate sector. They offer a variety of PTFE and other synthetic materials, particularly suitable for stringent high-frequency applications. Taconic’s products are known for their low dielectric loss and good mechanical properties, making them ideal for high-frequency circuits and antenna designs.
Additionally, Arlon provides a range of high-performance materials, especially thermoset epoxy substrates suitable for use in high-frequency environments. Arlon’s materials are commonly used in aerospace and military applications, known for their exceptional electrical and thermal performance.
Moreover, Isola is another prominent PCB materials supplier that offers specialized epoxy substrates and composite materials designed for high-frequency applications. Their products are widely utilized in communications and automotive electronics.
Our company can also manufacture high-frequency antenna substrates. We have advanced manufacturing equipment and technology to provide various types of high-frequency substrates, including PTFE, ceramic composites, and high-performance epoxy. Our products undergo strict quality control during the design and manufacturing process to meet the high standards required for high-frequency applications.
Our high-frequency antenna substrates feature low dielectric loss, high thermal stability, and excellent mechanical strength, making them suitable for a wide range of applications in communications, radar, and other high-frequency systems. Whether for large-scale production or small-batch customization, we can offer flexible solutions to meet specific customer needs.
During the research and development process, we work closely with customers to understand their application requirements and ensure the final product’s performance through electromagnetic simulation and prototype testing. Our goal is to provide the highest quality high-frequency antenna substrates, helping our customers achieve success in a competitive market.
What are the 7 qualities of good customer service?
Good customer service is essential for fostering customer loyalty and satisfaction. Here are seven key qualities that define excellent customer service:
- Empathy: Understanding and relating to the customer’s feelings and experiences. This helps in building a connection and making the customer feel valued.
- Responsiveness: Timely and effective responses to customer inquiries and issues. Quick resolution of problems demonstrates commitment and respect for the customer’s time.
- Knowledge: Having a deep understanding of the products or services offered. This enables staff to provide accurate information and helpful solutions to customer queries.
- Communication Skills: Clear, concise, and friendly communication is vital. Good customer service representatives should be able to listen actively and convey information effectively.
- Patience: Remaining calm and understanding, especially when dealing with difficult customers or complex issues. Patience helps to diffuse tense situations and leads to more positive outcomes.
- Consistency: Providing the same high level of service across all customer interactions. Consistency builds trust and reliability in the brand.
- Problem-Solving Skills: The ability to identify issues and find effective solutions promptly. Good customer service representatives should be proactive in addressing concerns and ensuring customer satisfaction.
These qualities contribute to a positive customer experience, enhancing brand reputation and customer loyalty.
FAQs
What are Antenna High Frequency Substrates?
Antenna High Frequency Substrates are specialized materials used to support high-frequency antennas, providing necessary electrical and thermal properties to optimize performance in applications like telecommunications and radar.
What materials are commonly used for these substrates?
Common materials include PTFE (Teflon), ceramics, epoxy composites, and liquid crystal polymers (LCP), each chosen for their low dielectric loss and thermal stability.
How do I choose the right substrate for my antenna design?
Consider factors such as frequency range, dielectric properties, thermal management, mechanical strength, and specific application requirements. Consulting with manufacturers or experts can also help.
What is the typical thickness for high-frequency substrates?
The thickness can vary depending on the design requirements but typically ranges from 0.5 mm to 2 mm, with specific applications possibly needing different dimensions.
What is the significance of dielectric loss in these substrates?
Low dielectric loss is crucial for high-frequency applications as it minimizes signal attenuation, ensuring better antenna efficiency and performance.
Can these substrates be customized?
Yes, many manufacturers offer customization options based on specific design needs, including size, shape, and material properties.
What are the key benefits of using high-frequency substrates?
They offer improved signal integrity, reduced heat generation, enhanced bandwidth, and overall better performance in high-frequency applications.pecific questions or need further details!