Aluminum Nitride PCB Manufacturing
Aluminum Nitride PCB Manufacturing,Aluminum Nitride (AlN) PCBs represent a cutting-edge solution in electronic engineering, leveraging the exceptional properties of this advanced ceramic material. Renowned for its high thermal conductivity, AlN PCBs excel in efficiently dissipating heat from electronic components, ensuring optimal performance and reliability even in demanding applications. With excellent electrical insulation properties and mechanical strength, AlN PCBs offer a robust platform for high-power electronics, RF/microwave circuits, and other high-frequency devices. Their precise manufacturing process involves depositing conductive layers, defining circuit patterns through photolithography, and incorporating vias for multi-layer connectivity. AlN PCBs are revered for their ability to withstand high temperatures and harsh environments, making them indispensable in industries such as automotive, aerospace, and telecommunications. As a leading provider of AlN PCB solutions, our company combines expertise, innovation, and quality to deliver customized solutions that meet the stringent demands of modern electronic designs.
What is an Aluminum Nitride PCB?
An Aluminum Nitride (AlN) PCB (Printed Circuit Board) is a type of electronic substrate used for manufacturing high-performance electronic devices, particularly in applications where thermal management is critical. Unlike traditional FR-4 (Flame Retardant 4) PCBs, which are made from fiberglass-reinforced epoxy, AlN PCBs are constructed using aluminum nitride as the substrate material.
Aluminum nitride is a ceramic material known for its excellent thermal conductivity, high electrical insulation properties, and good mechanical strength. These properties make it an ideal material for use in PCBs where efficient heat dissipation is essential to maintain the performance and reliability of electronic components.
AlN PCBs are commonly used in applications such as high-power LEDs, RF/microwave circuits, power electronics, and other high-frequency and high-temperature environments. They offer better thermal management compared to traditional PCB materials, allowing for improved performance and reliability of electronic devices, especially in demanding operating conditions.
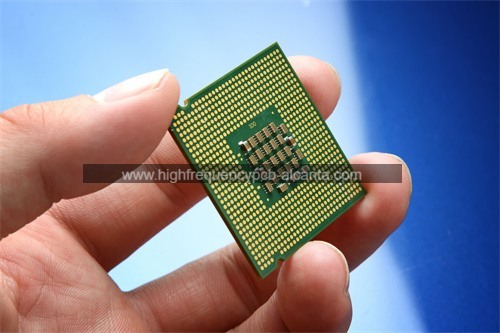
Aluminum Nitride PCB Manufacturing
What are the Aluminum Nitride PCB Design Guidelines?
Here are some general design guidelines for Aluminum Nitride (AlN) PCBs:
- Thermal Management: AlN PCBs excel in thermal conductivity, so it’s essential to design the layout to efficiently dissipate heat from high-power components. Ensure proper thermal vias and thermal pads are incorporated into the design to conduct heat away from heat-generating components to the board’s outer layers.
- Dielectric Layer: AlN PCBs typically have a thin dielectric layer. Designers should ensure that the dielectric layer thickness and material properties meet the electrical insulation requirements of the application.
- Component Placement: Place heat-generating components strategically to optimize thermal dissipation. Keep high-power components away from sensitive components to prevent thermal damage.
- Via Design: Use thermal vias to conduct heat away from heat-generating components to the outer layers of the PCB. Properly distribute thermal vias to minimize thermal resistance and ensure efficient heat dissipation.
- Trace Width and Spacing: Ensure appropriate trace widths and spacing to handle high current densities without causing excessive heating. Follow standard PCB design guidelines for trace width and spacing based on the current-carrying capacity of the traces.
- Ground Plane Design: Incorporate a solid ground plane on one or both sides of the PCB to provide a low impedance return path for signals and to help dissipate heat. This aids in reducing electromagnetic interference (EMI) and improving signal integrity.
- Encapsulation and Protection: Consider encapsulating the PCB or providing protective coatings to enhance reliability and prevent damage from environmental factors such as moisture, chemicals, and mechanical stress.
- Compatibility with Manufacturing Processes: Ensure that the design is compatible with the manufacturing processes for AlN PCB fabrication, including laser drilling for vias and appropriate surface finish for solderability.
- Testing and Validation: Perform thorough testing and validation of the PCB design to ensure that it meets the performance and reliability requirements of the intended application, especially regarding thermal management and electrical performance.
By following these guidelines, designers can optimize the performance, reliability, and thermal management of Aluminum Nitride PCBs for their specific applications.
What is the Aluminum Nitride PCB Fabrication Process?
The fabrication process for Aluminum Nitride (AlN) PCBs involves several steps. Here’s a general overview of the process:
- Substrate Preparation: The process begins with preparing the Aluminum Nitride substrate material. AlN substrates are typically available in the form of sheets or wafers. The sheets are inspected for defects and then cut to the required size for the PCB.
- Cleaning: The AlN substrate undergoes thorough cleaning to remove any contaminants or residues that may affect the adhesion of subsequent layers or the performance of the PCB.
- Deposition of Conductive Layers: The next step involves depositing conductive layers on the AlN substrate. This can be done using techniques such as sputtering or evaporation to deposit thin layers of metals like copper or gold, which will serve as the conductive traces and pads on the PCB.
- Photolithography: Photolithography is used to define the circuit pattern on the conductive layers. A photoresist material is applied to the substrate, exposed to UV light through a photomask with the desired circuit pattern, and then developed to remove the unexposed photoresist, leaving behind the patterned areas.
- Etching: The exposed conductive layers are etched away using chemical etchants, leaving behind the desired circuit pattern on the substrate.
- Dielectric Layer Deposition: A dielectric layer is deposited over the entire surface of the substrate to insulate the conductive traces and provide mechanical support. This layer can be deposited using techniques such as physical vapor deposition (PVD) or chemical vapor deposition (CVD).
- Via Formation: Vias are created to establish electrical connections between different layers of the PCB. This is typically done using laser drilling or mechanical drilling, followed by metallization of the vias to make them conductive.
- Surface Finish: Surface finish is applied to the exposed metal surfaces of the PCB to improve solderability and protect against oxidation. Common surface finishes for AlN PCBs include immersion gold, immersion silver, or OSP (Organic Solderability Preservatives).
- Inspection and Testing: The fabricated PCB undergoes thorough inspection and testing to ensure that it meets the required specifications and quality standards. This may include visual inspection, electrical testing, and dimensional measurements.
- Assembly: After fabrication, the AlN PCB is ready for component assembly. Surface mount or through-hole components are soldered onto the PCB according to the design requirements.
- Final Testing: The assembled PCB undergoes final testing to verify functionality and performance before it is deployed in the intended application.
By following these steps, manufacturers can produce high-quality Aluminum Nitride PCBs suitable for various high-performance electronic applications.
How do you manufacture Aluminum Nitride PCBs?
Manufacturing Aluminum Nitride (AlN) PCBs involves several steps, including substrate preparation, deposition of conductive layers, photolithography, etching, dielectric layer deposition, via formation, surface finish, inspection, and assembly. Here’s a detailed explanation of the manufacturing process:
- Substrate Preparation: AlN substrate material is prepared by cutting it into the desired size and shape. AlN substrates are typically available in the form of sheets or wafers. The sheets are inspected for defects, and any imperfections are removed.
- Cleaning: The AlN substrate undergoes thorough cleaning to remove any contaminants or residues that may affect subsequent processing steps or the performance of the PCB. This cleaning process typically involves solvent cleaning, followed by rinsing with deionized water and drying.
- Deposition of Conductive Layers: Thin layers of conductive material, such as copper or gold, are deposited onto the AlN substrate using techniques like sputtering or evaporation. These conductive layers will serve as the traces and pads on the PCB.
- Photolithography: A photoresist material is applied to the substrate, and a photomask with the desired circuit pattern is aligned and placed over the substrate. The substrate is then exposed to UV light, which transfers the pattern onto the photoresist. After exposure, the substrate is developed to remove the unexposed photoresist, leaving behind the patterned areas.
- Etching: The exposed conductive layers are etched away using chemical etchants, leaving behind the desired circuit pattern on the substrate. This step removes the unwanted conductive material, defining the traces and pads of the PCB.
- Dielectric Layer Deposition: A dielectric layer is deposited over the entire surface of the substrate to insulate the conductive traces and provide mechanical support. This layer can be deposited using techniques such as physical vapor deposition (PVD) or chemical vapor deposition (CVD).
- Via Formation: Vias are created to establish electrical connections between different layers of the PCB. This is typically done using laser drilling or mechanical drilling, followed by metallization of the vias to make them conductive. The vias are then filled with a conductive material, such as copper, to establish the electrical connections.
- Surface Finish: Surface finish is applied to the exposed metal surfaces of the PCB to improve solderability and protect against oxidation. Common surface finishes for AlN PCBs include immersion gold, immersion silver, or OSP (Organic Solderability Preservatives).
- Inspection and Testing: The fabricated PCB undergoes thorough inspection and testing to ensure that it meets the required specifications and quality standards. This may include visual inspection, electrical testing, and dimensional measurements.
- Assembly: After fabrication, the AlN PCB is ready for component assembly. Surface mount or through-hole components are soldered onto the PCB according to the design requirements.
- Final Testing: The assembled PCB undergoes final testing to verify functionality and performance before it is deployed in the intended application.
By following these steps, manufacturers can produce high-quality Aluminum Nitride PCBs suitable for various high-performance electronic applications.
How much should an Aluminum Nitride PCB cost?
The cost of Aluminum Nitride (AlN) PCBs can vary significantly depending on several factors, including the size, complexity, quantity, and specifications of the PCBs, as well as the chosen manufacturer and their pricing structure. Additionally, other factors such as material costs, fabrication techniques, and assembly processes also contribute to the overall cost.
Generally, AlN PCBs tend to be more expensive compared to traditional PCB materials like FR-4 due to the higher cost of Aluminum Nitride substrate material and the specialized manufacturing processes involved. However, the precise cost can only be determined by obtaining quotes from PCB manufacturers based on your specific requirements.
As a rough estimate, AlN PCBs may cost anywhere from a few hundred to several thousand dollars per square meter, depending on the factors mentioned above. It’s essential to get quotes from multiple manufacturers to compare prices and ensure you’re getting the best value for your specific needs. Additionally, keep in mind that higher quantities often result in lower per-unit costs due to economies of scale.
What is Aluminum Nitride PCB base material?
The base material of an Aluminum Nitride (AlN) PCB is, unsurprisingly, Aluminum Nitride itself. Aluminum Nitride is a ceramic material that possesses excellent thermal conductivity, high electrical insulation properties, and good mechanical strength.
AlN PCBs are manufactured using Aluminum Nitride sheets or wafers as the substrate material. These substrates provide the foundation upon which the conductive traces, components, and other layers are built during the PCB manufacturing process. The high thermal conductivity of Aluminum Nitride makes it an ideal choice for applications where efficient heat dissipation is critical, such as in high-power electronic devices or those operating in high-temperature environments.
Aluminum Nitride PCBs offer superior thermal management capabilities compared to traditional PCB materials like FR-4 (fiberglass-reinforced epoxy), making them suitable for demanding applications where thermal performance is essential.
Which company makes Aluminum Nitride PCBs?
Currently, there are many companies that provide manufacturing services for Aluminum Nitride (AlN) PCBs. Some well-known PCB manufacturers as well as companies specializing in high-performance electronic devices may offer AlN PCB manufacturing services. These companies typically have advanced manufacturing equipment and professional technical teams to meet customers’ demands for high-performance, high-reliability PCBs.
As for our company, we also offer manufacturing services for AlN PCBs. As a professional PCB manufacturer, we possess advanced production equipment and extensive experience to meet various demands for high-performance, high-reliability PCBs. Our production process strictly adheres to international standards to ensure stable and reliable product quality.
Our company can produce AlN PCBs of various specifications and complexities, providing customized solutions according to customer requirements. Our technical team can work closely with customers to provide professional design advice and technical support, ensuring that the PCB design meets customer requirements and achieves optimal performance.
Furthermore, we place great emphasis on quality control and customer service. We strictly control every production process, from raw material procurement to finished product delivery, to ensure product quality and on-time delivery. Our customer service team is available to provide support and assistance to customers at any time, ensuring customer satisfaction.
In summary, as a professional PCB manufacturer, our company has the equipment, technology, and experience required to produce AlN PCBs. We are committed to providing customers with high-quality, highly reliable AlN PCB products to meet various demands and requirements.
What are the 7 qualities of good customer service?
Good customer service is essential for building strong relationships with customers and ensuring their satisfaction. Here are seven qualities that characterize good customer service:
- Responsive: Good customer service is prompt and responsive to customer inquiries, concerns, and feedback. Customers appreciate timely assistance and expect their questions or issues to be addressed in a timely manner.
- Empathetic: Empathy is crucial in understanding and relating to customers’ needs and emotions. Good customer service representatives listen attentively, show understanding, and demonstrate empathy towards customers’ concerns and situations.
- Knowledgeable: Good customer service requires having a thorough understanding of the products or services offered by the company. Customer service representatives should be knowledgeable and able to provide accurate information, guidance, and solutions to customers’ inquiries and issues.
- Courteous: Courtesy and politeness go a long way in providing good customer service. Customer service representatives should maintain a friendly and respectful demeanor when interacting with customers, regardless of the situation.
- Patient: Patience is key when dealing with customers, especially those who may be frustrated or upset. Good customer service representatives remain calm, patient, and composed, even in challenging situations, and strive to resolve issues effectively without rushing the customer.
- Proactive:Good customer service is proactive in anticipating and addressing customers’ needs and concerns before they escalate. Proactive customer service involves reaching out to customers to offer assistance, providing relevant information, and ensuring their satisfaction proactively.
- Professionalism: Professionalism is essential in all customer interactions. Good customer service representatives maintain professionalism by adhering to company policies and procedures, maintaining confidentiality, and conducting themselves with integrity and honesty.
By embodying these qualities, businesses can deliver exceptional customer service experiences that foster loyalty, trust, and satisfaction among their customer base.
FAQs (Frequently Asked Questions)
What are the advantages of Aluminum Nitride PCBs?
Aluminum Nitride PCBs offer excellent thermal conductivity, electrical insulation, and mechanical strength, making them ideal for high-power and high-frequency electronic applications.
Can Aluminum Nitride PCBs be used in LED lighting?
Yes, Aluminum Nitride PCBs are commonly used in LED lighting systems due to their superior thermal management capabilities, which help dissipate heat generated by LEDs effectively.
Are Aluminum Nitride PCBs environmentally friendly?
Aluminum Nitride is a non-toxic and recyclable material, making Aluminum Nitride PCBs an environmentally friendly choice compared to some other substrate materials.
What are the limitations of Aluminum Nitride PCBs?
Aluminum Nitride PCBs may be more expensive compared to traditional PCBs due to the cost of the material and specialized fabrication processes involved. Additionally, Aluminum Nitride is brittle compared to some other substrate materials, requiring careful handling during manufacturing and assembly.
Can Aluminum Nitride PCBs be used in high-frequency applications?
Yes, Aluminum Nitride PCBs are suitable for high-frequency applications due to their low dielectric loss and excellent thermal conductivity properties, which help minimize signal loss and manage heat effectively.