Aluminum Nitride Ceramic PCB Manufacturing
Aluminum Nitride Ceramic PCB Manufacturing,Aluminum Nitride Ceramic PCBs represent a cutting-edge solution for electronic circuitry demanding superior thermal management and reliability. Utilizing aluminum nitride ceramic as a substrate material, these PCBs offer exceptional thermal conductivity, ensuring efficient heat dissipation even in high-power applications. The ceramic substrate provides excellent electrical insulation and mechanical strength, contributing to the durability and longevity of the PCBs. With their ability to operate at elevated temperatures without compromising performance, Aluminum Nitride Ceramic PCBs find widespread use in power electronics, RF/microwave circuits, LED lighting, and semiconductor packaging. The manufacturing process involves depositing conductive layers onto the ceramic substrate, carefully designing the circuit layout, and mounting electronic components with precision. These PCBs require meticulous attention to design and manufacturing processes to achieve optimal thermal performance and reliability, making them a preferred choice for demanding electronic applications where heat dissipation is critical.
What is an Aluminum Nitride Ceramic PCB?
An Aluminum Nitride Ceramic PCB (Printed Circuit Board) is a type of circuit board that utilizes aluminum nitride ceramic as its substrate material instead of traditional materials like fiberglass epoxy. Aluminum nitride (AlN) is a ceramic material known for its excellent thermal conductivity, high electrical insulation, and mechanical strength, making it an ideal choice for applications requiring efficient heat dissipation and reliability.
In an Aluminum Nitride Ceramic PCB, conductive traces are typically deposited onto the surface of the aluminum nitride substrate using methods such as thick film or thin film deposition techniques. Components such as integrated circuits, resistors, capacitors, and other electronic devices can then be mounted onto the PCB using soldering or other attachment methods.
The primary advantage of using aluminum nitride ceramic for PCBs is its superior thermal performance compared to traditional materials like FR-4. This allows for better heat dissipation, enabling the PCB to operate at higher temperatures without compromising performance or reliability. As a result, Aluminum Nitride Ceramic PCBs are often used in high-power and high-frequency applications where thermal management is critical, such as power electronics, RF/microwave circuits, LED lighting, and semiconductor device packaging.
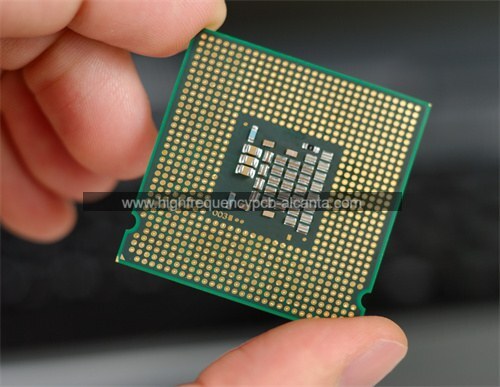
Aluminum nitride ceramic PCB manufacturing
What are the Aluminum Nitride Ceramic PCB Design Guidelines?
Designing a PCB with aluminum nitride ceramic substrate involves considerations to ensure optimal performance and reliability. Here are some guidelines:
- Thermal Management: Aluminum nitride ceramic PCBs excel in thermal conductivity, but proper design for effective heat dissipation is still crucial. Ensure adequate space for heat sinks, thermal vias, and thermal pads to efficiently transfer heat away from critical components.
- Material Selection: Choose appropriate thickness and quality of aluminum nitride ceramic substrate based on the specific application requirements. Also, consider the dielectric constant and thermal expansion coefficient of the material.
- Trace Layout: Design traces with sufficient width and spacing to accommodate the required current levels while maintaining impedance control. Avoid sharp corners and acute angles in trace routing to minimize signal reflections and impedance mismatch.
- Component Placement: Strategically place components to minimize heat concentration and ensure uniform thermal distribution across the PCB. Locate high-power components closer to heat sinks or areas with better thermal dissipation.
- Via Design: Implement thermal vias to enhance heat dissipation from the PCB surface to inner layers or heat sinks. Optimize via placement and size to maximize thermal conductivity while minimizing signal interference.
- Dielectric Layers: Consider using multiple dielectric layers to enhance insulation and thermal management. Choose dielectric materials with compatible thermal properties to ensure reliable performance under thermal cycling.
- Encapsulation and Sealing: Encapsulate critical components or sensitive areas to protect them from environmental factors such as moisture, dust, and mechanical stress. Use compatible sealing materials to maintain the integrity of the PCB.
- Testing and Validation: Perform thorough testing and validation procedures, including thermal cycling, thermal shock testing, and electrical testing, to ensure the reliability and performance of the aluminum nitride ceramic PCB under various operating conditions.
By following these guidelines, designers can optimize the performance, reliability, and thermal management of aluminum nitride ceramic PCBs for a wide range of applications.
What is the Aluminum Nitride Ceramic PCB Fabrication Process?
The fabrication process of Aluminum Nitride Ceramic PCBs typically involves several steps including substrate preparation, deposition of conductive and dielectric layers, photolithography, etching, drilling, plating, and final surface finish.
How do you manufacture an Aluminum Nitride Ceramic PCB?
Manufacturing an Aluminum Nitride Ceramic PCB involves several key steps:
- Substrate Preparation: The process begins with preparing the aluminum nitride ceramic substrate. This involves cutting the substrate to the desired size and shape using precision cutting tools. The substrate may also undergo surface treatment to ensure proper adhesion of the conductive layers.
- Conductive Layer Deposition: Next, conductive layers are deposited onto the surface of the ceramic substrate to create the circuitry. This can be done using techniques such as thick film or thin film deposition methods like sputtering, screen printing, or chemical vapor deposition (CVD). The conductive layers form the traces, pads, and other circuit elements of the PCB.
- Photoresist Application and Exposure: A layer of photoresist is applied onto the conductive layers. Photoresist is a light-sensitive material that will be used to define the circuit pattern. The PCB is then exposed to ultraviolet (UV) light through a mask containing the desired circuit pattern. This exposure causes the photoresist to harden in the areas where the circuit pattern is to be defined.
- Development and Etching: After exposure, the PCB is submerged in a developing solution that removes the unexposed areas of the photoresist, leaving behind the desired circuit pattern. The exposed conductive layers are then etched away using an appropriate chemical solution, leaving the defined circuitry on the substrate.
- Cleaning and Inspection: Once the etching process is complete, the PCB undergoes thorough cleaning to remove any remaining photoresist and etching residues. The PCB is then inspected for defects or irregularities in the circuit pattern using visual inspection or automated inspection equipment.
- Component Attachment: Electronic components such as integrated circuits, resistors, capacitors, and other devices are then mounted onto the PCB using soldering or other attachment methods. This can be done manually or using automated pick-and-place equipment.
- Testing: After component attachment, the PCB undergoes testing to ensure that all circuit connections are intact and that the components function as intended. This may include electrical testing, functional testing, and sometimes environmental testing to verify reliability under various conditions.
- Finishing: Finally, the PCB may undergo finishing processes such as coating or encapsulation to protect the circuitry from environmental factors such as moisture, dust, and mechanical stress. The finished PCB is then ready for use in various electronic applications.
Overall, manufacturing an Aluminum Nitride Ceramic PCB requires careful attention to detail and specialized equipment to ensure the precise deposition of conductive layers and the reliable performance of the finished PCB.
How much should an Aluminum Nitride Ceramic PCB cost?
The cost of an Aluminum Nitride Ceramic PCB can vary depending on several factors, including the size and complexity of the board, the quantity ordered, the quality of materials used, and the manufacturing processes involved. Generally, Aluminum Nitride Ceramic PCBs tend to be more expensive than traditional PCBs due to the higher cost of ceramic substrates and specialized manufacturing processes.
As a rough estimate, the cost of an Aluminum Nitride Ceramic PCB can range from tens to hundreds of dollars per square inch, with larger and more complex boards typically costing more. Ordering larger quantities may lead to volume discounts, reducing the cost per unit. Additionally, factors such as the thickness of the ceramic substrate, the number of layers, the complexity of the circuit design, and any additional features (such as surface finishing or special coatings) can also impact the overall cost.
It’s essential to obtain quotes from multiple PCB manufacturers to get a better idea of the specific cost for your project, as prices can vary significantly between suppliers. Additionally, keep in mind that while Aluminum Nitride Ceramic PCBs may have a higher upfront cost, they can offer advantages such as superior thermal performance and reliability, which may justify the investment for certain applications.
What is the Aluminum Nitride Ceramic PCB base material?
The base material of an Aluminum Nitride Ceramic PCB is aluminum nitride ceramic. Aluminum nitride (AlN) is a ceramic material that exhibits excellent thermal conductivity, high electrical insulation, and mechanical strength. These properties make it an ideal substrate material for applications requiring efficient heat dissipation and reliability, such as high-power electronics and RF/microwave circuits.
Aluminum nitride ceramic PCBs typically consist of a thin layer of aluminum nitride ceramic as the substrate onto which conductive traces and electronic components are deposited or attached. This ceramic substrate provides the structural support for the circuitry while also facilitating efficient heat transfer away from critical components.
Which company makes Aluminum Nitride Ceramic PCBs?
Currently, there are many companies that manufacture Aluminum Nitride Ceramic PCBs, some of which are well-known enterprises specialized in high-performance ceramics and electronics manufacturing. These companies typically possess advanced production equipment, technology, and experience to meet the requirements of various applications.
Some globally leading companies, such as Rogers Corporation and Ceramic Substrates & Components (CSC) in the United States, as well as Murata Manufacturing Co., Ltd. and Shin-Etsu Chemical Co., Ltd. in Japan, offer production services for Aluminum Nitride Ceramic PCBs.
As a company with advanced technology and rich experience, our company also produces Aluminum Nitride Ceramic PCBs. We have advanced production equipment and a professional technical team to provide high-quality, customized solutions to our customers. Our production process strictly controls every step to ensure that the products meet the requirements and standards of our customers.
Our company’s strengths include:
- Professional Team: We have experienced engineers and technical personnel who can provide comprehensive technical support and customized solutions.
- Advanced Equipment: Equipped with advanced production equipment and processes, we can achieve high precision and efficiency in production.
- Quality Control: We strictly implement a quality management system to ensure that each product meets the highest standards and customer requirements.
- Customization Services: We can customize Aluminum Nitride Ceramic PCBs according to customer requirements, including dimensions, shapes, thicknesses, surface treatments, and other aspects.
In summary, our company has the professional technology and resources required to produce Aluminum Nitride Ceramic PCBs, enabling us to meet various customer needs and provide high-quality customized solutions.
What are the 7 qualities of good customer service?
Good customer service is essential for building strong relationships with customers and fostering loyalty. Here are seven qualities that characterize excellent customer service:
- Responsiveness: Good customer service involves promptly addressing customer inquiries, concerns, and requests. Responding to customers in a timely manner shows that their needs are valued and helps to build trust.
- Empathy: Empathy involves understanding and acknowledging the customer’s feelings, perspective, and situation. It’s important to listen actively, show compassion, and demonstrate genuine concern for the customer’s experience.
- Clear Communication: Effective communication is crucial in customer service. Clearly conveying information, instructions, and solutions helps to avoid misunderstandings and ensures that customers feel informed and supported.
- Knowledgeability: Good customer service representatives possess in-depth knowledge about the products or services they are supporting. They should be able to answer questions, provide guidance, and offer solutions confidently and accurately.
- Problem-Solving Skills: Customers may encounter issues or challenges, and good customer service involves being proactive and resourceful in resolving problems. Customer service representatives should be able to think critically, analyze situations, and find creative solutions to meet customer needs.
- Professionalism: Professionalism encompasses maintaining a positive attitude, remaining courteous and respectful, and upholding company policies and standards. Treating customers with professionalism builds confidence and enhances the overall customer experience.
- Follow-Up and Accountability: After addressing a customer’s issue or inquiry, it’s important to follow up to ensure that the resolution was satisfactory and to offer any additional assistance if needed. Taking ownership of customer issues and ensuring accountability demonstrates commitment to customer satisfaction.
By embodying these qualities, businesses can deliver exceptional customer service that not only meets but exceeds customer expectations, fostering loyalty and positive brand perception.
FAQs
What are Aluminum Nitride Ceramic PCBs?
Aluminum Nitride Ceramic PCBs are printed circuit boards that use aluminum nitride ceramic as the substrate material instead of traditional materials like fiberglass epoxy. They offer excellent thermal conductivity, high electrical insulation, and mechanical strength, making them suitable for high-power and high-frequency applications.
What are the advantages of Aluminum Nitride Ceramic PCBs?
Aluminum Nitride Ceramic PCBs provide superior thermal performance, allowing for efficient heat dissipation and operation at higher temperatures. They also offer excellent electrical insulation, mechanical strength, and reliability, making them ideal for demanding applications.
What are the typical applications of Aluminum Nitride Ceramic PCBs?
Aluminum Nitride Ceramic PCBs are commonly used in power electronics, RF/microwave circuits, LED lighting, semiconductor device packaging, and other applications requiring efficient heat management and reliability.
How are Aluminum Nitride Ceramic PCBs manufactured?
The manufacturing process for Aluminum Nitride Ceramic PCBs involves depositing conductive layers onto the ceramic substrate, defining the circuit pattern, attaching electronic components, and testing for quality and reliability.
What are the design considerations for Aluminum Nitride Ceramic PCBs?
Design considerations include thermal management, material selection, trace layout, component placement, via design, dielectric layers, encapsulation, and testing for optimal performance and reliability.
How much do Aluminum Nitride Ceramic PCBs cost?
The cost of Aluminum Nitride Ceramic PCBs varies depending on factors such as size, complexity, quantity, materials used, and manufacturing processes. They tend to be more expensive than traditional PCBs due to the higher cost of ceramic substrates and specialized manufacturing.
Where can I find manufacturers of Aluminum Nitride Ceramic PCBs?
Several companies specialize in the production of Aluminum Nitride Ceramic PCBs, including Rogers Corporation, Murata Manufacturing Co., Ltd., and others. Additionally, many PCB manufacturers offer Aluminum Nitride Ceramic PCB fabrication services.