Alumina PCB |Al2O3 PCB Manufacturer
Alumina PCB |Al2O3 PCB Manufacturer,Alumina PCBs, also known as Alumina Printed Circuit Boards, are a type of circuit board with a base material composed of alumina, or aluminum oxide (Al2O3). Renowned for their exceptional thermal conductivity, mechanical strength, and electrical insulation properties, these PCBs find extensive application in various high-power and high-frequency electronic systems.
Engineered to withstand demanding conditions, Alumina PCBs offer superior heat dissipation capabilities, making them ideal for devices prone to overheating. Their robust construction ensures durability and reliability, crucial for applications requiring consistent performance. From power electronics and RF/microwave circuits to LED modules and high-power semiconductor devices, Alumina PCBs play a pivotal role in numerous industries.
Manufactured with precision and adhering to stringent quality standards, Alumina PCBs undergo a meticulous fabrication process, including substrate preparation, circuit design, conductive trace formation, component assembly, and testing. These PCBs embody the fusion of advanced materials and cutting-edge technology, delivering solutions that meet the evolving demands of modern electronic applications.
What is an Alumina PCB?
An Alumina PCB (Printed Circuit Board) is a type of circuit board where the base material is made of alumina, also known as aluminum oxide (Al2O3). Alumina is a ceramic material with excellent thermal conductivity, mechanical strength, and electrical insulation properties, which makes it suitable for various high-power and high-frequency electronic applications.
Alumina PCBs are often used in electronic devices and systems that require high thermal performance and reliability, such as power electronics, RF/microwave circuits, LED modules, and high-power semiconductor devices like RF power amplifiers and laser diodes.
Due to its high thermal conductivity, alumina PCBs can efficiently dissipate heat generated by electronic components, helping to prevent overheating and ensure the reliability and longevity of the device or system. Additionally, alumina’s excellent electrical insulation properties allow for reliable isolation between circuit elements, reducing the risk of electrical shorts or interference.
Overall, alumina PCBs are valued for their combination of thermal performance, mechanical robustness, and electrical insulation, making them suitable for demanding electronic applications where reliability and performance are critical.
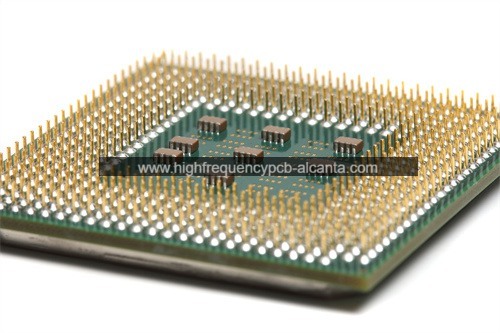
Alumina PCB |Al2O3 PCB Manufacturer
What are the Alumina PCB Design Guidelines?
Designing with alumina PCBs requires attention to several key guidelines to ensure optimal performance and reliability. Here are some common design guidelines for alumina PCBs:
- Thermal Management: Alumina PCBs are known for their excellent thermal conductivity, so it’s essential to design the layout with efficient heat dissipation in mind. Place high-power components strategically to maximize heat transfer and minimize temperature gradients across the board.
- Component Placement: Position components on the PCB to minimize thermal gradients and ensure adequate spacing for heat dissipation. High-power components should be spaced apart to prevent localized heating. Consider the thermal characteristics of each component when placing them on the board.
- Trace Width and Spacing: Design traces with appropriate widths and spacing to accommodate the current requirements of the circuit. Use wider traces for high-current paths to reduce resistance and prevent overheating. Maintain adequate clearance between traces to avoid signal interference and ensure electrical isolation.
- Via Design: Vias are used for routing signals between different layers of the PCB. When designing with alumina PCBs, consider the thermal conductivity of the substrate. Ensure that vias are properly placed to facilitate heat transfer and minimize thermal resistance between layers.
- Ground Plane: Utilize a solid ground plane on one or more layers of the PCB to provide low-impedance return paths for signals and enhance EMC (Electromagnetic Compatibility) performance. A solid ground plane also helps to improve thermal management by spreading heat evenly across the board.
- Signal Integrity: Pay attention to signal integrity principles, such as controlled impedance routing and minimizing signal reflections. Maintain consistent trace widths and impedance matching to prevent signal degradation and ensure reliable communication between components.
- Mounting and Attachment: Consider the method of mounting and attachment for the PCB, especially in high-temperature environments. Use appropriate mounting techniques, such as soldering or epoxy bonding, to ensure mechanical stability and thermal performance.
- Testing and Validation: Perform thorough testing and validation of the PCB design to ensure it meets the desired performance criteria. Conduct thermal analysis, impedance measurements, and functional testing to verify the reliability and functionality of the design.
By adhering to these guidelines, designers can create alumina PCBs that offer optimal thermal performance, signal integrity, and reliability for various high-power and high-frequency electronic applications.
What is the Alumina PCB Fabrication Process?
The fabrication process for alumina PCBs involves several steps, including substrate preparation, circuit design and layout, fabrication of conductive traces, component assembly, and testing. Here’s an overview of the typical fabrication process:
- Substrate Preparation: The process begins with preparing the alumina substrate. Alumina ceramic sheets are typically used as the base material. These sheets are cleaned and inspected for any defects before proceeding to the next step.
- Circuit Design and Layout: The circuit design is created using PCB design software. Designers lay out the components, traces, and vias on the substrate according to the circuit requirements and design guidelines. Special attention is given to thermal management, signal integrity, and mechanical stability.
- Conductive Traces Formation: Conductive traces are formed on the alumina substrate using various methods, including thick film printing, screen printing, or thin film deposition techniques such as sputtering or evaporation. The choice of method depends on factors such as trace width, thickness, and resolution requirements.
- Etching: In the case of thick film printing, the substrate is then subjected to an etching process to remove excess conductive material and define the desired trace patterns. This step helps to create the conductive pathways that connect different components on the PCB.
- Via Formation: Vias, which are used to connect traces between different layers of the PCB, are created using drilling or punching techniques. The vias are then filled with conductive material to establish electrical connections between the layers.
- Component Assembly: Once the conductive traces and vias are formed, electronic components such as resistors, capacitors, and integrated circuits are assembled onto the PCB using surface mount technology (SMT) or through-hole technology (THT). Precision is crucial during this step to ensure proper alignment and soldering of components.
- Soldering: The assembled PCB undergoes soldering to secure the components in place and establish electrical connections between them and the conductive traces. Solder paste is applied to the component pads, and then the PCB is heated to melt the solder and create strong bonds.
- Testing and Inspection: After soldering, the PCB is subjected to rigorous testing and inspection to verify its functionality, electrical performance, and reliability. This may include electrical testing, thermal testing, and visual inspection to identify any defects or issues.
- Finishing and Packaging: Once the PCB passes testing and inspection, it undergoes finishing processes such as cleaning, coating, or surface treatment to enhance its durability and protect it from environmental factors. Finally, the PCB is packaged and prepared for shipment to the end user.
Throughout the fabrication process, strict quality control measures are implemented to ensure that the alumina PCB meets the required specifications and standards for the intended application.
How do you manufacture an Alumina PCB?
Manufacturing an alumina PCB involves several intricate steps to ensure precise fabrication and reliable performance. Here’s a detailed overview of the manufacturing process:
- Material Selection: Begin by selecting high-quality alumina ceramic sheets as the substrate material. Alumina is chosen for its excellent thermal conductivity, mechanical strength, and electrical insulation properties.
- Substrate Preparation:
– Cleaning: The alumina ceramic sheets are thoroughly cleaned to remove any contaminants or impurities that could affect the fabrication process.
– Cutting: The sheets are then cut into the desired size and shape using precision cutting tools or techniques.
- Circuit Design and Layout:
– PCB Design Software: Designers use specialized PCB design software to create the circuit layout based on the specific requirements of the electronic device or system.
– Component Placement: Components are strategically placed on the substrate according to the circuit design, taking into account factors such as thermal management, signal integrity, and mechanical stability.
- Conductive Traces Formation:
– Thick Film Printing: One common method for forming conductive traces on alumina substrates is thick film printing. Conductive paste is deposited onto the substrate using a screen printing process.
– Thin Film Deposition: Alternatively, conductive traces can be deposited using thin film deposition techniques such as sputtering or evaporation. This method allows for higher precision and finer trace features.
- Etching (if applicable):
– If thick film printing is used, the substrate may undergo an etching process to remove excess conductive material and define the desired trace patterns.
- Via Formation:
– Vias are created to establish electrical connections between different layers of the PCB. This is typically done using drilling or punching techniques followed by filling the vias with conductive material.
- Component Assembly:
– Electronic components such as resistors, capacitors, and integrated circuits are assembled onto the PCB using surface mount technology (SMT) or through-hole technology (THT).
– Precision placement and soldering techniques are crucial to ensure proper alignment and electrical connections.
- Soldering:
– The assembled PCB undergoes soldering to secure the components in place and establish electrical connections between them and the conductive traces.
– Solder paste is applied to the component pads, and then the PCB is heated to melt the solder and create strong bonds.
- Testing and Inspection:
– The PCB is subjected to rigorous testing and inspection to verify its functionality, electrical performance, and reliability.
– This may include electrical testing, thermal testing, and visual inspection to identify any defects or issues.
- Finishing and Packaging:
– After passing testing and inspection, the PCB undergoes finishing processes such as cleaning, coating, or surface treatment to enhance its durability and protect it from environmental factors.
– Finally, the PCB is packaged and prepared for shipment to the end user.
Throughout the manufacturing process, strict quality control measures are implemented to ensure that the alumina PCB meets the required specifications and standards for the intended application.
How much should an Alumina PCB cost?
The cost of an alumina PCB can vary depending on several factors, including the size, complexity, material specifications, quantity, and manufacturing processes involved. Here are some factors that can influence the cost:
- Size and Complexity: Larger PCBs with more complex layouts require more materials and processing time, leading to higher costs. Smaller, simpler PCBs are generally less expensive.
- Material Specifications: The choice of alumina ceramic material and its specific properties can affect the cost. High-purity alumina with precise thermal and electrical properties may be more expensive than standard alumina substrates.
- Quantity: Economies of scale apply in PCB manufacturing, meaning that larger production runs typically result in lower per-unit costs. Ordering larger quantities of alumina PCBs may lead to volume discounts.
- Manufacturing Processes: The fabrication techniques used, such as thick film printing, thin film deposition, or laser processing, can impact the cost. More advanced manufacturing processes may result in higher costs.
- Technical Requirements: PCBs with specialized features or requirements, such as high-frequency RF circuits, high-power applications, or tight tolerances, may incur additional costs due to the need for specialized materials or manufacturing processes.
- Lead Time: Urgent orders or rush production may incur expedited manufacturing costs.
As a rough estimate, the cost of a basic alumina PCB could range from a few dollars for small, simple designs to several hundred dollars for larger, complex designs with specialized features. However, it’s important to obtain quotes from PCB manufacturers based on your specific requirements to get an accurate cost estimate.
What is Alumina PCB base material?
Alumina PCB base material refers to the substrate material used in the fabrication of alumina PCBs (Printed Circuit Boards). Alumina, also known as aluminum oxide (Al2O3), is a ceramic material that serves as the base for these PCBs. Alumina is chosen for its excellent thermal conductivity, mechanical strength, and electrical insulation properties, making it suitable for various high-power and high-frequency electronic applications.
The alumina substrate provides the foundation for the PCB and serves as the platform on which conductive traces, vias, and electronic components are mounted. Alumina PCB base material is typically available in the form of ceramic sheets or panels, which are processed and prepared for circuit fabrication.
Alumina PCB base material offers several key properties that make it ideal for electronic applications:
- Thermal Conductivity: Alumina has high thermal conductivity, allowing it to efficiently dissipate heat generated by electronic components. This helps to prevent overheating and ensures the reliability of the PCB.
- Mechanical Strength: Alumina is a mechanically robust material, providing durability and resistance to mechanical stressors such as vibration and shock. This helps to ensure the long-term reliability of the PCB in various operating conditions.
- Electrical Insulation: Alumina is an excellent electrical insulator, offering high dielectric strength and low dielectric loss. This property allows for reliable isolation between circuit elements and helps to prevent electrical shorts or interference.
- Chemical Stability: Alumina is chemically inert and resistant to corrosion, making it suitable for use in harsh environments and demanding applications where exposure to chemicals or moisture may occur.
Overall, alumina PCB base material provides a stable and reliable platform for the fabrication of high-performance PCBs used in applications such as power electronics, RF/microwave circuits, LED modules, and high-power semiconductor devices.
Which company makes Alumina PCBs?
Many companies produce Alumina PCBs, among which some well-known manufacturers include Rogers Corporation in the United States, Kyocera in Japan, and Jiangsu Xiangfeng Electronic Technology Co., Ltd. in China. These companies specialize in high-performance electronic materials and PCB manufacturing, offering various types of Alumina PCBs to meet the diverse needs of customers.
As for our company, we can also manufacture Alumina PCBs and have extensive experience and expertise in this field. We have advanced manufacturing equipment and a skilled technical team capable of providing high-quality, customized Alumina PCB solutions.
Our Alumina PCB manufacturing process strictly adheres to international standards and customer requirements, ensuring stable and reliable product quality and performance. We can provide Alumina PCBs in various sizes, thicknesses, and with special requirements according to customer design specifications and technical requirements, including but not limited to:
- High Thermal Conductivity Alumina PCBs: Suitable for high-power electronic applications requiring excellent heat dissipation performance, such as power amplifiers, LED heat dissipation modules, etc.
- High-Frequency Alumina PCBs: Specifically designed for radio frequency (RF) and microwave applications, with excellent electrical performance and signal transmission characteristics.
- Special Process Alumina PCBs: Customized Alumina PCBs tailored to customer-specific requirements, including thick or thin substrate materials, special processing techniques, etc.
We are committed to providing comprehensive Alumina PCB solutions to our customers, from design and engineering support to production and quality control, ensuring that we meet the needs and expectations of our customers. Our team is dedicated to providing professional technical support and high-quality service. Please feel free to contact us at any time for more information about our Alumina PCB manufacturing capabilities.
What are the 7 qualities of good customer service?
Good customer service is characterized by several key qualities that contribute to positive interactions and satisfaction for customers. Here are seven essential qualities of good customer service:
- Responsiveness: Good customer service involves being prompt and proactive in responding to customer inquiries, requests, and concerns. This includes acknowledging messages or inquiries promptly, providing timely assistance, and addressing issues in a timely manner.
- Empathy: Empathy involves understanding and acknowledging the customer’s perspective, emotions, and needs. Good customer service representatives demonstrate empathy by listening actively, showing understanding, and expressing genuine concern for the customer’s situation.
- Professionalism: Professionalism entails maintaining a courteous, respectful, and professional demeanor when interacting with customers. This includes using polite language, maintaining composure, and representing the company in a positive light.
- Knowledgeability: Good customer service representatives possess comprehensive knowledge about the company’s products, services, policies, and procedures. They can effectively answer questions, provide accurate information, and offer helpful recommendations or solutions to customers.
- Problem-solving skills: Good customer service involves being able to identify and resolve customer issues effectively. This requires strong problem-solving skills, the ability to think critically, and the willingness to take ownership of problems until they are resolved to the customer’s satisfaction.
- Adaptability: Good customer service representatives are adaptable and flexible in their approach to different customer situations and preferences. They can adjust their communication style, problem-solving strategies, and service delivery to meet the unique needs of each customer.
- Follow-up and accountability: Good customer service includes following up with customers to ensure that their needs have been met and that any issues have been resolved satisfactorily. It also involves taking accountability for mistakes or shortcomings and taking proactive steps to rectify them.
By embodying these qualities, companies can deliver exceptional customer service experiences that foster loyalty, satisfaction, and positive brand perception.
FAQs
What is an Alumina PCB?
An Alumina PCB, or Alumina Printed Circuit Board, is a type of circuit board where the base material is made of alumina, also known as aluminum oxide (Al2O3). It is commonly used in electronic applications requiring high thermal conductivity, mechanical strength, and electrical insulation.
What are the advantages of Alumina PCBs?
Alumina PCBs offer several advantages, including excellent thermal conductivity, mechanical robustness, and electrical insulation properties. They are suitable for high-power and high-frequency electronic applications where reliability and performance are critical.
What are the typical applications of Alumina PCBs?
Alumina PCBs are used in various electronic devices and systems, including power electronics, RF/microwave circuits, LED modules, high-power semiconductor devices, and other applications requiring high thermal performance and reliability.
How are Alumina PCBs manufactured?
The manufacturing process for Alumina PCBs involves substrate preparation, circuit design and layout, fabrication of conductive traces, component assembly, soldering, testing, and finishing. Specialized techniques such as thick film printing or thin film deposition may be used to create the conductive traces.
What are the key design guidelines for Alumina PCBs?
Design guidelines for Alumina PCBs include considerations for thermal management, component placement, trace width and spacing, via design, ground plane configuration, signal integrity, mounting, and testing/validation.
What are the cost factors associated with Alumina PCBs?
The cost of Alumina PCBs can vary depending on factors such as size, complexity, material specifications, quantity, manufacturing processes, and lead time. Larger quantities and simpler designs may result in lower per-unit costs.
Where can I purchase Alumina PCBs?
Alumina PCBs can be purchased from various PCB manufacturers and suppliers specializing in high-performance electronic materials. Companies such as Rogers Corporation, Kyocera, and others offer Alumina PCBs tailored to specific customer requirements.