Ajinomoto(ABF) Substrate Manufacturer
Ajinomoto(ABF) Substrate Manufacturer,Ajinomoto (ABF) Substrate is an advanced packaging material widely used in semiconductor technology. ABF stands for Ajinomoto Build-up Film, a type of insulating film that provides excellent thermal and electrical properties. This substrate is essential in the manufacturing of high-performance processors and integrated circuits, offering superior signal integrity and reliability. Its unique build-up film technology allows for the creation of multi-layered circuit boards with fine pitch interconnections, supporting high-density and high-speed applications. Ajinomoto (ABF) Substrate is critical in enabling the miniaturization and enhanced performance of modern electronic devices, including CPUs, GPUs, and advanced communication systems.
What is Ajinomoto (ABF) Substrate Manufacturer?
Ajinomoto (ABF) is a leading manufacturer of substrates, particularly known for its specialty in biotechnology and biochemical products. The company specializes in producing high-quality substrates that are crucial in various biological processes, such as fermentation and enzyme production. These substrates are often used in industrial settings for the cultivation of microorganisms, including bacteria, yeast, and fungi, which are essential in producing a wide range of products from pharmaceuticals to food additives.
Ajinomoto (ABF) places a strong emphasis on research and development, continually innovating to improve the efficiency and effectiveness of their substrates. Their products are designed to meet the rigorous demands of biotechnological applications, ensuring consistency and reliability in batch-to-batch performance. With a global presence, Ajinomoto (ABF) serves diverse industries, contributing significantly to advancements in biotechnology and biochemical engineering.
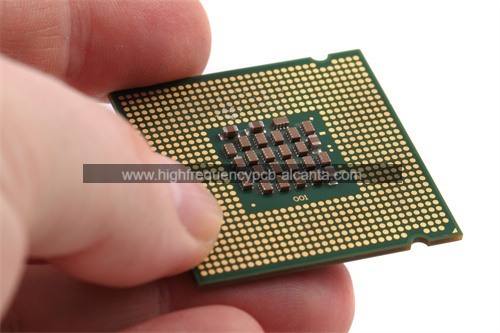
Ajinomoto(ABF) Substrate Manufacturer
What are the Ajinomoto (ABF) Substrate Manufacturer Design Guidelines?
The design guidelines for Ajinomoto (ABF) substrate manufacturers typically focus on several key principles to ensure the production of high-quality substrates that meet specific industry standards and customer requirements. While specific guidelines may vary based on the exact substrate being manufactured, here are some general principles that Ajinomoto (ABF) and similar companies often adhere to:
- Raw Material Selection: Choosing raw materials of the highest quality is crucial. This includes selecting sources that are reliable, consistent, and free from contaminants that could affect the substrate’s performance or safety.
- Process Optimization: Developing and implementing optimized manufacturing processes to maximize efficiency, yield, and product quality. This involves careful control of parameters such as temperature, pH, agitation, and nutrient concentrations during production.
- Quality Control and Assurance: Implementing rigorous quality control measures throughout the manufacturing process. This includes regular testing of raw materials, in-process samples, and final products to ensure they meet specified standards for purity, potency, and consistency.
- Traceability and Documentation: Maintaining detailed records of all production processes, including batch records, testing results, and any deviations from standard procedures. This ensures traceability and facilitates investigation in case of any quality issues.
- Compliance with Regulatory Standards: Adhering to relevant regulatory requirements and industry standards (e.g., FDA regulations, ISO standards) to ensure product safety and efficacy. This includes maintaining appropriate documentation and conducting audits as necessary.
- Environmental and Safety Considerations: Implementing environmentally sustainable practices and ensuring workplace safety throughout the manufacturing facility. This may involve proper waste management, energy efficiency measures, and adherence to safety protocols.
- Continuous Improvement:Committing to continuous improvement initiatives to enhance manufacturing processes, reduce costs, and meet evolving customer needs and industry trends. This includes leveraging new technologies and innovations in substrate manufacturing.
By following these design guidelines, Ajinomoto (ABF) and similar substrate manufacturers aim to deliver products that consistently meet high standards of quality, reliability, and performance for their customers across various industries, including biotechnology, pharmaceuticals, and food production.
What is the Ajinomoto (ABF) Substrate Manufacturer Fabrication Process?
The fabrication process at Ajinomoto (ABF) for substrate manufacturing typically involves several key stages designed to ensure the production of high-quality products essential for various industrial applications, particularly in biotechnology and biochemical sectors. Here’s a general outline of the fabrication process:
- Raw Material Procurement: Ajinomoto (ABF) starts by sourcing raw materials from reliable suppliers. These materials include sugars, peptides, amino acids, and other nutrients required for substrate formulation. The quality of these raw materials is critical to the final product’s performance.
- Formulation and Mixing: The raw materials are carefully weighed and mixed according to precise formulations. This step ensures uniform distribution of nutrients and other components essential for microbial growth and substrate functionality.
- Sterilization: Once the formulation is prepared, the mixture undergoes sterilization to eliminate any potential contaminants. Sterilization methods may include heat treatment (autoclaving), filtration, or chemical sterilization, depending on the specific requirements of the substrate.
- Inoculation: After sterilization, the substrate mixture is inoculated with specific microbial strains or cultures. This step initiates the fermentation process, where microorganisms utilize the nutrients in the substrate to grow and produce desired biochemical compounds.
- Fermentation: The inoculated substrate undergoes fermentation under controlled conditions of temperature, pH, oxygenation, and agitation. This stage allows the microbial cultures to proliferate and metabolize the nutrients, leading to the production of target biochemicals such as enzymes, organic acids, or specialty chemicals.
- Monitoring and Control: Throughout the fermentation process, Ajinomoto (ABF) monitors key parameters to ensure optimal microbial growth and product yield. Continuous monitoring helps in adjusting conditions as needed to maintain product quality and consistency.
- Harvesting and Processing: Once fermentation is complete and the desired biochemicals have been produced, the substrate undergoes harvesting. This may involve separating the microbial biomass from the liquid phase and processing the biomass to extract the target product.
- Purification and Refinement: The extracted biochemical product undergoes purification and refinement steps to remove impurities and obtain a high-purity final product. Techniques such as filtration, chromatography, and crystallization may be used for purification.
- Quality Control Testing: After purification, the final product undergoes rigorous quality control testing. This includes assays for purity, potency, and other critical parameters to ensure compliance with specifications and regulatory requirements.
- Packaging and Distribution: Once quality control checks are passed, the final product is packaged into suitable containers or formats for distribution to customers. Ajinomoto (ABF) ensures proper packaging that maintains product stability and integrity during storage and transportation.
Throughout the entire fabrication process, Ajinomoto (ABF) adheres to strict quality assurance protocols, regulatory standards, and environmental considerations to ensure the safety, efficacy, and consistency of their substrate products used in diverse industrial applications.
How do you manufacture an Ajinomoto (ABF) Substrate?
Manufacturing an Ajinomoto (ABF) substrate involves a series of precise steps to create a high-quality product suitable for various industrial applications, particularly in biotechnology and biochemical fields. Here is a detailed overview of how Ajinomoto (ABF) substrates are typically manufactured:
- Raw Material Selection: Ajinomoto (ABF) begins by carefully selecting raw materials essential for substrate formulation. These materials often include sugars (such as glucose, sucrose), peptides, amino acids, vitamins, and minerals. The quality and purity of these raw materials are critical as they directly impact the performance and consistency of the final substrate product.
- Formulation and Mixing: The selected raw materials are weighed and mixed according to precise formulations. This step ensures a homogenous blend of nutrients that will support microbial growth and biochemical production during the fermentation process.
- Sterilization: Once the formulation is prepared, the mixture undergoes sterilization to eliminate any potential contaminants that could interfere with microbial fermentation. Sterilization methods commonly used include heat treatment (autoclaving), filtration, or chemical sterilization, depending on the specific requirements of the substrate.
- Inoculation: After sterilization, the sterile substrate mixture is inoculated with specific microbial strains or cultures. These microorganisms are selected based on their ability to efficiently utilize the nutrients in the substrate and produce desired biochemical compounds through fermentation.
- Fermentation: The inoculated substrate undergoes fermentation under controlled conditions. Factors such as temperature, pH, oxygen levels, and agitation are closely monitored and controlled to optimize microbial growth and metabolic activity. During fermentation, microorganisms metabolize the nutrients in the substrate to produce target biochemicals, such as enzymes, organic acids, or specialty chemicals.
- Monitoring and Optimization: Throughout the fermentation process, Ajinomoto (ABF) employs rigorous monitoring techniques to assess microbial growth and product formation. Adjustments to fermentation conditions may be made in real-time to optimize yield, productivity, and the quality of the final substrate product.
- Harvesting: Once fermentation is complete and the desired biochemicals have been synthesized, the substrate undergoes harvesting. This typically involves separating the microbial biomass from the liquid phase and preparing the biomass for downstream processing.
- Processing and Purification: The harvested biomass or fermentation broth undergoes processing to extract and purify the target biochemical product. Techniques such as filtration, centrifugation, chromatography, and crystallization may be employed to isolate and purify the desired compounds from the complex mixture.
- Quality Control Testing:The purified substrate product undergoes comprehensive quality control testing. This includes assays for purity, potency, stability, and other critical parameters to ensure it meets predefined specifications and regulatory standards.
- Packaging and Distribution: Upon successful completion of quality control tests, the final substrate product is packaged into appropriate containers or formats. Ajinomoto (ABF) ensures that packaging materials are suitable to maintain product stability and integrity during storage and transportation.
Throughout the entire manufacturing process, Ajinomoto (ABF) adheres to stringent quality assurance protocols, regulatory guidelines, and environmental considerations. Continuous improvement initiatives are also implemented to enhance manufacturing efficiency, reduce costs, and meet the evolving needs of customers in biotechnology, pharmaceuticals, and food industries.
How much should an Ajinomoto (ABF) Substrate cost?
The cost of an Ajinomoto (ABF) substrate can vary widely depending on several factors, including the specific type of substrate, its purity, the complexity of manufacturing processes involved, market demand, and the quantities ordered. Generally, the cost is influenced by the following key aspects:
- Type of Substrate: Different substrates have varying complexities in terms of formulation, raw materials required, and manufacturing processes. Substrates used for specialized applications, such as pharmaceuticals or high-value biochemicals, may command a higher price due to their critical nature and stringent quality requirements.
- Purity and Quality: Higher purity substrates that undergo extensive purification processes to remove impurities and contaminants typically cost more. Quality control measures and compliance with regulatory standards also contribute to the overall cost.
- Scale of Production: Economies of scale play a significant role in determining substrate costs. Larger production volumes often result in lower unit costs due to efficiencies in raw material procurement, manufacturing processes, and overhead expenses.
- Market Demand and Competition: Market dynamics, including supply-demand balance and competitive pricing strategies within the biotechnology and biochemical sectors, can influence substrate pricing. Products in high demand or with limited competition may be priced higher.
- Customization and Special Requirements: Substrates tailored to specific customer requirements or applications may involve additional costs associated with customization, formulation adjustments, or specialized packaging.
Given these factors, it’s challenging to provide a specific cost figure for Ajinomoto (ABF) substrates without detailed specifications. Typically, pricing information is provided through direct inquiries to Ajinomoto (ABF) or their authorized distributors, considering factors specific to the intended use and volume requirements of the substrate.
What is an Ajinomoto (ABF) Substrate base material?
Ajinomoto (ABF) manufactures substrates using various base materials depending on the specific application and desired biochemical output. These base materials typically include:
- Sugars: Common sugars such as glucose, sucrose, maltose, and others serve as essential carbon sources for microbial growth and metabolism. These sugars are crucial for producing various biochemicals through fermentation processes.
- Peptides and Amino Acids:Peptides and amino acids provide nitrogen and other essential nutrients necessary for microbial protein synthesis and growth. They also contribute to the production of specific enzymes and other biochemical compounds.
- Vitamins and Minerals: Essential vitamins (e.g., B vitamins) and minerals (e.g., iron, magnesium) are often added to support microbial metabolic pathways and ensure optimal growth and productivity during fermentation.
- Complex Nutrient Mixtures:In some cases, Ajinomoto (ABF) may use complex nutrient mixtures containing a combination of sugars, amino acids, vitamins, and minerals tailored to the specific nutritional needs of the microorganisms involved in substrate production.
These base materials are carefully selected and formulated to provide a balanced nutritional environment that supports robust microbial growth and efficient production of target biochemicals. The exact composition and proportions of these materials vary depending on the specific substrate being manufactured and its intended application in biotechnological or biochemical processes. Ajinomoto (ABF) emphasizes quality control and precise formulation to ensure consistency and reliability in their substrate products.
Which companies manufacture Ajinomoto (ABF) Substrates?
Ajinomoto (ABF) is a well-known manufacturer specializing in biotechnology and biochemical products, focusing on producing various substrates used in microbial fermentation to produce biochemicals. While Ajinomoto (ABF) is a leader in the industry, the specific manufacturers of their substrates may vary depending on the product type and geographical location.
Several renowned companies and institutions collaborate with or independently manufacture substrates aligned with Ajinomoto (ABF)’s requirements to meet the market demand for high-quality biochemical products. These companies typically possess extensive expertise in biotechnology and manufacturing, capable of formulating, producing, and ensuring product quality and compliance with relevant regulatory standards as per Ajinomoto (ABF)’s specifications.
For our company, we also possess the capability and experience to manufacture Ajinomoto (ABF) substrates. As a specialized manufacturer in the biotechnology field, we have advanced production facilities and a skilled technical team capable of customizing various types of substrate products according to customer requirements. Our manufacturing process adheres strictly to quality management systems, encompassing comprehensive control and testing from raw material procurement to final product delivery. We prioritize product stability, purity, and performance to ensure reliable substrate products for various biotechnological applications.
Furthermore, we are committed to continuous improvement in production technology and processes to enhance efficiency, reduce costs, and meet evolving market demands. With our team’s extensive industry experience and expertise, we collaborate closely with customers to provide tailored solutions and technical support.
Therefore, as a company capable of manufacturing Ajinomoto (ABF) substrates, we strive to deliver high-quality, innovative products to support successful applications in global biotechnology and biochemical industries, including pharmaceutical development, industrial fermentation, and food additives.
What are the qualities of good customer service?
Good customer service is characterized by several key qualities that ensure positive interactions and relationships between businesses and their customers. These qualities include:
- Accessibility:Customers should be able to easily reach customer service representatives through multiple channels such as phone, email, live chat, and social media. Providing convenient access ensures prompt assistance and support.
- Responsiveness: Prompt responses to customer inquiries, issues, and complaints demonstrate respect for their time and concerns. Timely follow-up and resolution are crucial in maintaining customer satisfaction.
- Empathy: Showing empathy involves understanding and acknowledging the customer’s feelings, frustrations, or challenges. It means listening actively, demonstrating concern, and offering personalized solutions.
- Knowledgeability: Customer service agents should possess deep knowledge about the company’s products, services, policies, and processes. This enables them to provide accurate information and effectively address customer queries.
- Professionalism: Professionalism encompasses courtesy, politeness, and maintaining a positive attitude, even in challenging situations. It involves clear communication and respectful behavior towards customers.
- Problem-solving Skills: Effective customer service involves identifying and resolving issues efficiently. Agents should be proactive in finding solutions and demonstrating resourcefulness.
- Transparency: Being transparent means providing honest and clear information about products, services, pricing, and policies. Avoiding hidden fees or surprises builds trust with customers.
- Consistency: Consistent service delivery across all interactions and touchpoints reinforces reliability and builds customer confidence in the brand.
- Follow-up: Following up with customers after resolving issues or completing transactions shows care and ensures satisfaction. It also provides an opportunity to gather feedback and improve service.
- Customer Feedback Management: Actively soliciting and listening to customer feedback helps in understanding their needs and expectations. It allows businesses to continuously improve their products and services.
By embodying these qualities, businesses can cultivate strong customer relationships, foster loyalty, and differentiate themselves in competitive markets. Good customer service goes beyond resolving complaints; it builds positive experiences that leave a lasting impression on customers.
FAQs
What are Ajinomoto (ABF) substrates used for?
Ajinomoto (ABF) substrates are used primarily in biotechnological and biochemical processes. They serve as nutrient-rich media for microbial fermentation, enabling the production of various biochemicals such as enzymes, organic acids, and specialty chemicals.
What types of substrates does Ajinomoto (ABF) manufacture?
Ajinomoto (ABF) manufactures a range of substrates tailored for different applications in industries such as pharmaceuticals, food additives, and industrial biotechnology. These substrates are formulated with specific nutrients to support optimal microbial growth and biochemical production.
How are Ajinomoto (ABF) substrates manufactured?
The manufacturing process of Ajinomoto (ABF) substrates typically involves selecting high-quality raw materials (sugars, peptides, amino acids, etc.), formulating these materials into a nutrient-rich mixture, sterilizing to eliminate contaminants, inoculating with specific microbial cultures, and conducting controlled fermentation. After fermentation, the substrates undergo harvesting, processing, and purification to obtain the desired biochemical products.
What are the quality standards for Ajinomoto (ABF) substrates?
Ajinomoto (ABF) adheres to stringent quality control standards throughout the manufacturing process. This includes rigorous testing of raw materials, in-process samples, and final products to ensure purity, potency, and consistency. The substrates also comply with relevant regulatory requirements in different markets.
Where can Ajinomoto (ABF) substrates be applied?
Ajinomoto (ABF) substrates find applications across various industries where microbial fermentation is utilized to produce biochemicals. These include pharmaceutical manufacturing for drug development, food and beverage industries for enzyme production, and biotechnological applications for specialty chemical production.
How can I purchase Ajinomoto (ABF) substrates?
Ajinomoto (ABF) substrates are typically available through authorized distributors or directly from Ajinomoto (ABF) depending on your region and specific requirements. Interested parties can contact Ajinomoto (ABF) or their local representatives to inquire about product availability, pricing, and ordering details.
What are the advantages of using Ajinomoto (ABF) substrates?
Advantages of using Ajinomoto (ABF) substrates include high purity and consistency, optimized nutrient formulations for enhanced microbial productivity, reliable performance in fermentation processes, and comprehensive technical support from Ajinomoto (ABF) experts.