Ajinomoto GZ41R2H Package Substrate Manufacturer
Ajinomoto GZ41R2H Package Substrate Manufacturer,Ajinomoto GZ41R2H package substrate represents a cutting-edge solution in electronic packaging, meticulously engineered by Ajinomoto Fine-Techno Co., Ltd. This substrate boasts exceptional thermal conductivity, ensuring efficient heat dissipation, crucial for high-performance semiconductor devices. Its robust construction provides mechanical stability, safeguarding against mechanical stresses during assembly and operation. The substrate’s precise dimensional accuracy and compatibility with advanced packaging techniques enable seamless integration into various electronic applications. Moreover, its superior electrical insulation properties guarantee reliable performance and signal integrity. Designed with the latest advancements in materials and manufacturing processes, the Ajinomoto GZ41R2H substrate offers unparalleled quality and reliability, meeting the demanding requirements of the electronics industry. Whether powering cutting-edge electronics or enabling innovative technologies, this substrate stands as a testament to Ajinomoto’s commitment to excellence in electronic packaging.
What is Ajinomoto GZ41R2H package substrate?
The Ajinomoto GZ41R2H package substrate is a type of substrate used in electronic packaging, particularly in semiconductor devices. It’s commonly utilized in the manufacturing of integrated circuits (ICs) and other electronic components. The substrate serves as a foundation for mounting and interconnecting various electronic elements within a semiconductor device.
The GZ41R2H substrate, produced by Ajinomoto Fine-Techno Co., Ltd., likely features specific characteristics tailored for high-performance applications. These may include excellent thermal conductivity, electrical insulation properties, mechanical strength, and compatibility with different manufacturing processes such as flip-chip bonding or wire bonding.
The substrate’s composition and design are crucial for ensuring the reliability and functionality of the final electronic product. Engineers and designers select substrates based on factors such as the intended application, operating conditions, and performance requirements.
For example, in high-power applications or those requiring efficient heat dissipation, substrates with enhanced thermal conductivity are preferred to prevent overheating and ensure the stability of the semiconductor device. On the other hand, for applications where miniaturization and lightweight design are priorities, substrates with high mechanical strength and compatibility with advanced packaging techniques are essential.
Overall, the Ajinomoto GZ41R2H package substrate represents a specialized component in the realm of semiconductor manufacturing, contributing to the development of advanced electronic devices with improved performance, reliability, and functionality.
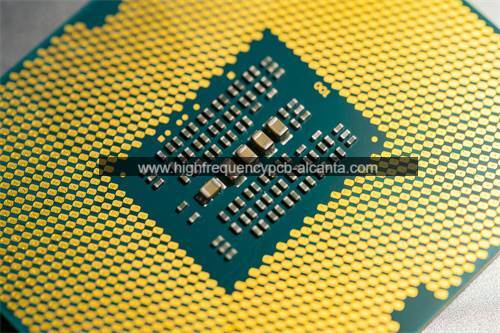
Ajinomoto GZ41R2H Package Substrate Manufacturer
What are the Ajinomoto GZ41R2H package substrate Design Guidelines?
Specific design guidelines for the Ajinomoto GZ41R2H package substrate may vary depending on the requirements of a particular application and the recommendations provided by Ajinomoto Fine-Techno Co., Ltd. However, there are some general design considerations that engineers typically adhere to when working with package substrates:
- Thermal Management: Efficient heat dissipation is crucial for the reliability and performance of electronic devices. Designers need to ensure that the substrate allows for effective thermal management, which may involve the use of thermal vias, heat spreaders, or other thermal management techniques.
- Electrical Performance: The substrate should provide reliable electrical connections between different components of the electronic device. Designers must consider factors such as signal integrity, impedance control, and power distribution to ensure optimal electrical performance.
- Mechanical Stability: Mechanical stability is essential to prevent mechanical failures during handling, assembly, and operation of the electronic device. The substrate should have adequate mechanical strength and rigidity to withstand mechanical stresses and environmental factors.
- Dimensional Accuracy: Precise dimensional control is necessary to ensure compatibility with other components and manufacturing processes. Designers need to carefully specify the dimensions and tolerances of the substrate to avoid assembly issues and ensure proper fit within the overall device package.
- Material Selection: The choice of substrate material can significantly impact the performance and reliability of the electronic device. Designers should select materials with appropriate properties such as thermal conductivity, electrical insulation, and compatibility with manufacturing processes.
- Manufacturability: Designers should consider the manufacturability of the substrate design, including factors such as ease of fabrication, assembly, and testing. Design guidelines may include recommendations for design features that facilitate manufacturing processes and minimize production costs.
- Environmental Considerations: The substrate should be designed to withstand environmental conditions such as temperature variations, humidity, and exposure to chemicals or contaminants. Designers may incorporate protective coatings or encapsulation materials to enhance the substrate’s durability and reliability in harsh environments.
These are some general design guidelines that engineers typically follow when working with package substrates like the Ajinomoto GZ41R2H. However, for specific design recommendations and guidelines, it’s essential to consult the manufacturer’s documentation or technical support resources.
What is the Ajinomoto GZ41R2H package substrate Fabrication Process?
The fabrication process for the Ajinomoto GZ41R2H package substrate likely involves several steps to create a substrate with the desired properties and dimensions. While specific details may vary depending on the manufacturer’s processes and equipment, here is a general overview of the typical fabrication process for package substrates:
- Material Selection: The fabrication process begins with the selection of suitable substrate materials. These materials are chosen based on their properties, such as thermal conductivity, electrical insulation, mechanical strength, and compatibility with the intended application.
- Substrate Preparation: The substrate material is prepared for processing by cutting it into the desired size and shape. This may involve techniques such as sawing, laser cutting, or chemical etching to achieve precise dimensions.
- Surface Preparation: The substrate surfaces are prepared for subsequent processing steps, such as metallization and bonding. This may involve cleaning the surfaces to remove contaminants and applying surface treatments or coatings to enhance adhesion and conductivity.
- Metallization: Metal layers are deposited onto the substrate surfaces to create conductive pathways for electrical connections. This may be done using techniques such as physical vapor deposition (PVD), chemical vapor deposition (CVD), or electroplating.
- Etching and Patterning: The metal layers are patterned and etched to create the desired circuitry and interconnects on the substrate. This typically involves photolithography processes, where a photoresist is patterned and used as a mask for selective etching of the metal layers.
- Dielectric Layer Deposition: Insulating dielectric layers are deposited onto the substrate to provide electrical insulation between conductive traces and to protect the underlying layers. These dielectric layers may be deposited using techniques such as spin coating, chemical vapor deposition, or plasma-enhanced chemical vapor deposition.
- Via Formation: Vias, or holes, are created in the substrate to allow for vertical interconnects between different layers of the substrate. This may involve drilling or laser ablation followed by metal deposition and filling to create conductive pathways through the substrate.
- Surface Finish: Surface finishes are applied to the substrate to improve solderability and prevent oxidation of the metal surfaces. Common surface finishes include immersion tin, immersion silver, electroless nickel immersion gold (ENIG), and organic solderability preservatives (OSP).
- Quality Control and Testing: Throughout the fabrication process, quality control measures are implemented to ensure the integrity and reliability of the substrate. This may involve visual inspection, dimensional measurements, electrical testing, and other quality assurance techniques.
- Packaging and Shipping:Once fabrication is complete and the substrates have passed quality control checks, they are packaged and prepared for shipping to customers or assembly facilities for further processing into electronic devices.
This is a general overview of the fabrication process for package substrates like the Ajinomoto GZ41R2H. Actual processes and techniques may vary depending on factors such as substrate material, desired features, and manufacturing capabilities.
How do you manufacture Ajinomoto GZ41R2H package substrate?
- Substrate Preparation: The manufacturing process begins with the preparation of the substrate material. This may involve cutting the material into the desired size and shape using techniques such as sawing, laser cutting, or chemical etching.
- Surface Cleaning and Treatment: The substrate surfaces are thoroughly cleaned to remove any contaminants that could affect subsequent processing steps. Surface treatments may also be applied to enhance adhesion and promote uniform deposition of subsequent layers.
- Metallization: Metal layers are deposited onto the substrate surfaces to create conductive pathways for electrical connections. This can be achieved through techniques such as physical vapor deposition (PVD), chemical vapor deposition (CVD), or electroplating.
- Patterning and Etching: The metal layers are patterned and etched to define the circuitry and interconnects on the substrate. This typically involves photolithography processes, where a photoresist is patterned and used as a mask for selective etching of the metal layers.
- Dielectric Layer Deposition: Insulating dielectric layers are deposited onto the substrate to provide electrical insulation between conductive traces and to protect the underlying layers. This can be done using techniques such as spin coating, chemical vapor deposition, or plasma-enhanced chemical vapor deposition.
- Via Formation: Vias, or holes, are created in the substrate to allow for vertical interconnects between different layers of the substrate. This may involve drilling or laser ablation followed by metal deposition and filling to create conductive pathways through the substrate.
- Surface Finishing: Surface finishes are applied to the substrate to improve solderability and prevent oxidation of the metal surfaces. Common surface finishes include immersion tin, immersion silver, electroless nickel immersion gold (ENIG), and organic solderability preservatives (OSP).
- Quality Control and Testing:Throughout the manufacturing process, rigorous quality control measures are implemented to ensure the integrity and reliability of the substrate. This may involve visual inspection, dimensional measurements, electrical testing, and other quality assurance techniques.
- Packaging and Shipping: Once manufacturing is complete and the substrates have passed quality control checks, they are packaged and prepared for shipping to customers or assembly facilities for further processing into electronic devices.
This outline provides a general overview of the steps involved in manufacturing package substrates for electronic applications. Actual processes and techniques may vary depending on factors such as substrate material, desired features, and manufacturing capabilities. For specific details on the manufacturing process for the Ajinomoto GZ41R2H package substrate, it’s recommended to consult the manufacturer’s documentation or technical support resources.
How much should an Ajinomoto GZ41R2H package substrate cost?
Determining the exact cost of an Ajinomoto GZ41R2H package substrate would depend on several factors, including:
- Quantity: Generally, purchasing larger quantities of substrates can lead to lower per-unit costs due to economies of scale. Suppliers often offer volume discounts for bulk orders.
- Specifications: The cost may vary depending on the specific requirements of the substrate, such as size, material composition, number of layers, and surface finish. Substrates with more complex features or specialized materials may be more expensive.
- Supplier: Different suppliers may offer the Ajinomoto GZ41R2H package substrate at different prices based on factors such as their production capabilities, overhead costs, and profit margins.
- Market Conditions: Market demand and supply dynamics can also influence substrate prices. Shortages of raw materials or high demand for electronic components may lead to higher prices.
- Customization: If customization or additional processing is required for the substrates, such as specific designs, surface finishes, or testing procedures, this can affect the overall cost.
Without specific pricing information from the manufacturer or a supplier, it’s challenging to provide an exact cost for the Ajinomoto GZ41R2H package substrate. However, as a rough estimate, package substrates for electronic applications can range from a few cents to several dollars per unit, depending on the factors mentioned above.
To obtain accurate pricing information, it’s best to contact suppliers directly and request a quotation based on your specific requirements and order quantity. Additionally, negotiating with suppliers and comparing quotes from multiple sources can help ensure competitive pricing.
What is Ajinomoto GZ41R2H package substrate base material?
The specific base material used for the Ajinomoto GZ41R2H package substrate isn’t readily available in public sources as of my last update. However, package substrates for electronic applications are typically made from materials such as:
- Organic Substrates: Organic substrates, commonly referred to as printed circuit boards (PCBs), are made from materials such as FR-4 (a type of fiberglass-reinforced epoxy laminate) or other organic materials like polyimide (PI) or bismaleimide triazine (BT). These substrates are widely used in various electronic devices due to their relatively low cost, good electrical insulation properties, and ease of manufacturing.
- Ceramic Substrates: Ceramic substrates are made from materials such as alumina (Al2O3) or aluminum nitride (AlN). Ceramic substrates offer excellent thermal conductivity, mechanical stability, and resistance to high temperatures, making them suitable for high-power applications and environments where thermal management is critical.
- Metal Substrates: Metal substrates, such as aluminum or copper, are used in applications requiring high thermal conductivity and heat dissipation. These substrates often feature a layer of dielectric material sandwiched between metal layers to provide electrical insulation and thermal management capabilities.
The choice of base material for a package substrate depends on factors such as the intended application, performance requirements, thermal management needs, and cost considerations. Without specific information on the Ajinomoto GZ41R2H package substrate, it’s challenging to identify the exact base material used. For accurate information, it’s recommended to consult the manufacturer’s documentation or technical support resources.
Which company makes Ajinomoto GZ41R2H package substrate?
The Ajinomoto GZ41R2H package substrate is manufactured by Ajinomoto Fine-Techno Co., Ltd., a subsidiary of Ajinomoto in Japan. The company is a leading manufacturer specializing in electronic packaging substrates, equipped with advanced production facilities and technology. They are committed to providing high-quality, high-performance package substrate products to meet the demands of customers in the electronics industry.
Our company can also produce similar package substrates to meet the needs of customers. We have advanced production equipment and a skilled technical team capable of customizing substrates of various specifications and performance according to customer requirements. We prioritize product quality and reliability, strictly adhering to quality control standards to ensure that each product meets customer requirements and expectations.
Our production process includes material selection, preparation, surface treatment, metallization, patterning, dielectric layer deposition, via formation, surface finishing, quality control, and more. We can adapt flexibly to customer needs, providing customized solutions and ensuring timely delivery at competitive prices.
Whatever type of package substrate customers require, we can provide high-quality products and excellent services. We are dedicated to establishing long-term and stable cooperation with customers, growing together to achieve mutual benefits and win-win results.
What are the qualities of good customer service?
Good customer service is characterized by several qualities that contribute to a positive experience for customers. Here are some key qualities:
- Responsiveness: A good customer service team responds promptly to customer inquiries, concerns, and requests. They acknowledge customer communication quickly and work to provide timely resolutions to issues.
- Empathy: Empathy involves understanding and sharing the feelings of customers. Good customer service representatives listen actively to customers, demonstrate compassion, and strive to address their needs with sensitivity and understanding.
- Knowledgeability: Customer service representatives should be knowledgeable about the products or services they are supporting. They should have a thorough understanding of company policies, procedures, and offerings to provide accurate information and assistance to customers.
- Professionalism: Professionalism encompasses maintaining a positive attitude, being courteous and respectful, and presenting oneself in a manner that reflects well on the company. Good customer service representatives remain composed and handle challenging situations with professionalism and diplomacy.
- Problem-solving skills: Effective problem-solving skills are essential for resolving customer issues and concerns efficiently. Customer service representatives should be able to identify root causes of problems, offer creative solutions, and follow through to ensure customer satisfaction.
- Clear communication: Clear communication is crucial for conveying information effectively and ensuring mutual understanding between customers and representatives. Good customer service involves using clear, concise language, active listening, and avoiding jargon or technical terms that may confuse customers.
- Flexibility: Customer service representatives should be adaptable and flexible in their approach to assisting customers. They should be willing to accommodate customer needs, make exceptions when appropriate, and seek creative solutions to meet customer requirements.
- Consistency: Consistency in service delivery builds trust and reliability with customers. Good customer service teams strive to deliver consistent experiences across all interactions, regardless of the channel or representative involved.
- Follow-up: Following up with customers after resolving an issue or completing a transaction shows that the company values their feedback and satisfaction. Good customer service involves proactive follow-up to ensure that customers’ needs have been met and to address any lingering concerns.
- Continuous improvement: Customer service teams should be committed to continuously improving their processes, systems, and skills to better serve customers. Soliciting feedback from customers, monitoring performance metrics, and implementing changes based on insights are essential for delivering exceptional customer service over time.
By embodying these qualities, companies can build strong relationships with customers, enhance brand reputation, and drive customer loyalty and retention.
FAQs
What is the Ajinomoto GZ41R2H package substrate used for?
The Ajinomoto GZ41R2H package substrate is used in electronic packaging, particularly in semiconductor devices such as integrated circuits (ICs) and other electronic components.
What are the key features of the Ajinomoto GZ41R2H package substrate?
Specific features may vary, but the Ajinomoto GZ41R2H substrate likely offers properties such as high thermal conductivity, electrical insulation, mechanical strength, and compatibility with various packaging techniques.
What materials are used in the Ajinomoto GZ41R2H package substrate?
The specific base material used in the Ajinomoto GZ41R2H substrate isn’t readily available. However, typical materials for package substrates include organic substrates (e.g., FR-4), ceramic substrates (e.g., alumina or aluminum nitride), or metal substrates (e.g., aluminum or copper).
Who manufactures the Ajinomoto GZ41R2H package substrate?
The Ajinomoto GZ41R2H package substrate is manufactured by Ajinomoto Fine-Techno Co., Ltd., a subsidiary of Ajinomoto in Japan. They specialize in electronic packaging substrates and offer high-quality products for the electronics industry.
What are the design guidelines for using the Ajinomoto GZ41R2H package substrate?
Design guidelines may include considerations for thermal management, electrical performance, mechanical stability, dimensional accuracy, material selection, manufacturability, and environmental factors. Specific guidelines may be available from the manufacturer.
How much does the Ajinomoto GZ41R2H package substrate cost?
The cost of the Ajinomoto GZ41R2H package substrate can vary depending on factors such as quantity, specifications, supplier, market conditions, and customization requirements. Contacting suppliers directly for a quotation based on specific needs is recommended.
What is the fabrication process for the Ajinomoto GZ41R2H package substrate?
The fabrication process may involve steps such as substrate preparation, surface treatment, metallization, patterning, dielectric layer deposition, via formation, surface finishing, quality control, and packaging. Specific details may be available from the manufacturer.
Where can I purchase the Ajinomoto GZ41R2H package substrate?
The Ajinomoto GZ41R2H package substrate may be available through authorized distributors or directly from Ajinomoto Fine-Techno Co., Ltd. Contacting the manufacturer or authorized distributors for purchasing information is recommended.