Ajinomoto GXT31R2 Package Substrate Manufacturer
Ajinomoto GXT31R2 Package Substrate Manufacturer,Ajinomoto GXT31R2 package substrate represents the pinnacle of electronic packaging technology, offering unparalleled performance and reliability for semiconductor devices. Engineered with precision and expertise, this substrate combines advanced materials, precise conductor patterns, and optimized thermal management to meet the most demanding requirements of modern electronics.
At its core, the Ajinomoto GXT31R2 substrate ensures seamless electrical connectivity between integrated circuits and the system board, enabling smooth data transmission and efficient power distribution. Its robust construction and innovative design mitigate signal interference, enhance signal integrity, and optimize heat dissipation, ensuring optimal performance even in the most challenging environments.
With its versatility and compatibility with various packaging technologies, the Ajinomoto GXT31R2 substrate serves a wide range of applications, from consumer electronics to automotive systems and industrial equipment. Whether it’s powering your smartphone, enabling autonomous vehicles, or driving industrial automation, this substrate stands as a testament to Ajinomoto’s commitment to excellence in electronic packaging.
What is the Ajinomoto GXT31R2 package substrate?
The Ajinomoto GXT31R2 package substrate is a type of substrate used in electronic packaging, particularly in semiconductor devices. It’s a high-performance substrate designed to provide electrical connectivity between the integrated circuits (ICs) and the system board.
This substrate is typically made of advanced materials such as fiberglass-reinforced epoxy resin or polyimide, which offer excellent thermal and electrical properties. These materials ensure efficient heat dissipation and reliable electrical connections, crucial for the performance and longevity of electronic devices.
The GXT31R2 substrate features a specific layout of conductive traces and vias, optimized for signal integrity and power distribution within the IC package. It also incorporates advanced manufacturing techniques such as precision etching and plating processes to achieve tight tolerances and high reliability.
One notable aspect of the Ajinomoto GXT31R2 substrate is its compatibility with advanced packaging technologies like flip-chip and wire bonding. This versatility allows it to be used in a wide range of semiconductor applications, from consumer electronics to industrial and automotive systems.
Overall, the Ajinomoto GXT31R2 package substrate represents a sophisticated solution for demanding electronic packaging requirements, offering a balance of performance, reliability, and manufacturability essential for modern semiconductor devices.
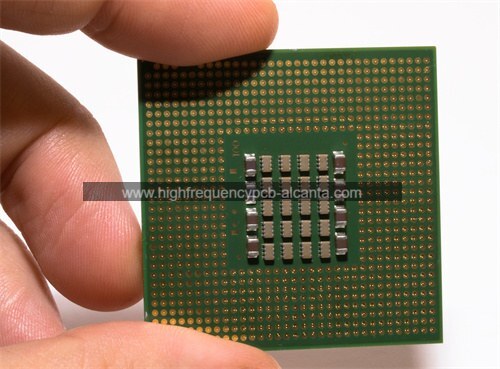
Ajinomoto GXT31R2 Package Substrate Manufacturer
What are the Ajinomoto GXT31R2 package substrate Design Guidelines?
Design guidelines for the Ajinomoto GXT31R2 package substrate are typically provided by Ajinomoto itself or through their technical documentation. While specific guidelines may vary based on the application and requirements, here are some general design principles that are commonly followed:
- Substrate Dimensions: Ensure that the substrate dimensions (length, width, thickness) are compatible with the requirements of the semiconductor device and the overall system.
- Layer Stackup: Define the layer stackup configuration, including the number of layers, dielectric materials, and conductor thickness. Consider factors such as signal integrity, power distribution, and thermal management.
- Signal Routing: Follow best practices for signal routing to minimize signal degradation and electromagnetic interference (EMI). Maintain appropriate trace widths, spacing, and impedance control for high-speed signals.
- Power Distribution: Design an effective power distribution network (PDN) to deliver stable and clean power to the semiconductor device. Use low impedance power planes and carefully distribute decoupling capacitors.
- Thermal Management: Incorporate features such as thermal vias, thermal pads, and metal heat spreaders to facilitate efficient heat dissipation from the semiconductor device to the substrate and system board.
- Component Placement: Optimize the placement of semiconductor components, passive components, and connectors on the substrate to minimize signal path lengths, reduce parasitic effects, and improve system reliability.
- Manufacturability: Ensure that the substrate design is manufacturable within the capabilities of the chosen fabrication process. Consider factors such as minimum feature size, aspect ratio, and registration accuracy.
- Reliability: Design the substrate to meet reliability requirements such as mechanical strength, solder joint integrity, and resistance to environmental stress factors like temperature and humidity.
- Electrical Testing: Define test points and access features to facilitate electrical testing and debugging of the semiconductor device during manufacturing and assembly.
- Documentation: Document the substrate design thoroughly, including schematics, layout files, fabrication drawings, and assembly instructions, to ensure proper communication with manufacturing partners and compliance with industry standards.
By following these design guidelines, engineers can develop Ajinomoto GXT31R2 package substrates that meet the performance, reliability, and manufacturability requirements of their specific semiconductor applications.
What is the Ajinomoto GXT31R2 package substrate Fabrication Process?
The fabrication process for the Ajinomoto GXT31R2 package substrate involves several steps, each crucial for achieving the desired performance and reliability. While specific details may vary depending on the manufacturer and facility, here is a general overview of the fabrication process:
- Substrate Preparation: The fabrication process begins with the preparation of the base substrate material, typically fiberglass-reinforced epoxy resin or polyimide. This material is cleaned and pre-treated to ensure proper adhesion of subsequent layers.
- Layer Stackup Design: Engineers design the layer stackup according to the substrate’s requirements, including the number of layers, dielectric materials, and conductor patterns. This design phase also involves determining the placement of vias and any additional features such as thermal pads or signal shielding.
- Substrate Lamination: The individual layers of the substrate are laminated together using heat and pressure to form a single, multi-layered structure. This process ensures proper adhesion between layers and creates a solid foundation for the conductor patterns.
- Conductor Pattern Formation: Conductor patterns, including signal traces, power planes, and ground planes, are created on each layer of the substrate using techniques such as photolithography, etching, and metal deposition. These patterns define the electrical connectivity of the substrate and are critical for signal routing and power distribution.
- Via Formation: Vias, which are small holes drilled or etched through the substrate layers, are created to establish electrical connections between different layers of the substrate. Techniques such as laser drilling or mechanical drilling may be used depending on the substrate material and design requirements.
- Surface Finish Application: The substrate surface is coated with a surface finish material to protect the conductor patterns from oxidation and facilitate soldering during component assembly. Common surface finishes include electroless nickel immersion gold (ENIG) and organic solderability preservatives (OSP).
- Final Inspection and Testing: Once the fabrication process is complete, the substrate undergoes thorough inspection and testing to ensure it meets the specified quality standards. This may include visual inspection, dimensional measurements, electrical continuity testing, and reliability testing under various environmental conditions.
- Packaging and Shipping: Finished substrates are packaged according to industry standards to protect them during transit and storage. They are then shipped to semiconductor manufacturers or assembly facilities for integration into electronic devices.
Throughout the fabrication process, strict quality control measures are implemented to ensure consistency, reliability, and performance uniformity across all produced substrates. Collaboration between design engineers, manufacturing specialists, and quality assurance teams is essential to achieving successful fabrication outcomes for Ajinomoto GXT31R2 package substrates.
How do you manufacture an Ajinomoto GXT31R2 package substrate?
Manufacturing an Ajinomoto GXT31R2 package substrate involves a series of specialized steps and processes aimed at creating a high-performance substrate for semiconductor devices. Here’s a detailed overview of the manufacturing process:
- Material Selection and Preparation: The manufacturing process begins with the selection of appropriate base materials such as fiberglass-reinforced epoxy resin or polyimide. These materials are cleaned and pre-treated to ensure optimal adhesion and compatibility with subsequent manufacturing steps.
- Layer Stackup Design: Engineers design the layer stackup configuration based on the specific requirements of the substrate, including the number of layers, thickness of dielectric materials, and placement of conductive layers. This design phase is crucial for defining the electrical and mechanical properties of the substrate.
- Substrate Lamination: The individual layers of the substrate are laminated together using heat and pressure. This process creates a solid, multi-layered structure with well-defined electrical and mechanical properties.
- Conductor Pattern Formation: Conductor patterns, including signal traces, power planes, and ground planes, are created on each layer of the substrate using advanced techniques such as photolithography, etching, and metal deposition. These patterns define the electrical connectivity of the substrate and are critical for signal routing and power distribution.
- Via Formation: Vias, which are small holes drilled or etched through the substrate layers, are created to establish electrical connections between different layers. Techniques such as laser drilling or mechanical drilling may be used depending on the substrate material and design requirements.
- Surface Finish Application: The substrate surface is coated with a surface finish material to protect the conductor patterns from oxidation and facilitate soldering during component assembly. Common surface finishes include electroless nickel immersion gold (ENIG) and organic solderability preservatives (OSP).
- Final Inspection and Testing: Once the manufacturing process is complete, the substrate undergoes thorough inspection and testing to ensure it meets the specified quality standards. This may include visual inspection, dimensional measurements, electrical continuity testing, and reliability testing under various environmental conditions.
- Packaging and Shipping: Finished substrates are packaged according to industry standards to protect them during transit and storage. They are then shipped to semiconductor manufacturers or assembly facilities for integration into electronic devices.
Throughout the manufacturing process, stringent quality control measures are implemented to ensure consistency, reliability, and performance uniformity across all produced substrates. Collaboration between design engineers, manufacturing specialists, and quality assurance teams is essential to achieving successful manufacturing outcomes for Ajinomoto GXT31R2 package substrates.
How much should an Ajinomoto GXT31R2 package substrate cost?
The cost of an Ajinomoto GXT31R2 package substrate can vary widely depending on several factors including:
- Size and Complexity: Larger substrates with more layers and complex designs typically cost more to manufacture due to increased material and production costs.
- Material: The choice of substrate material can significantly impact the cost. Higher performance materials may be more expensive than standard materials but offer improved electrical and thermal properties.
- Manufacturing Process:The specific manufacturing processes and technologies used can affect the cost. For example, advanced fabrication techniques may require specialized equipment and expertise, leading to higher production costs.
- Volume:Economies of scale play a significant role in determining the cost of substrate production. Higher volume orders typically result in lower unit costs due to efficiencies in material procurement, manufacturing, and overhead.
- Customization: Customized features such as unique layer stackups, special surface finishes, or additional testing requirements can increase the cost of the substrate.
- Supplier and Market Dynamics: Prices can vary between different suppliers and may fluctuate due to market conditions, supply chain disruptions, or changes in material costs.
As such, it’s challenging to provide an exact cost without specific details about the substrate’s size, design complexity, material specifications, and production volume. Companies interested in purchasing Ajinomoto GXT31R2 package substrates would typically need to request a quote from Ajinomoto or their authorized distributors based on their specific requirements.
What is the Ajinomoto GXT31R2 package substrate base material?
The base material used for the Ajinomoto GXT31R2 package substrate can vary depending on the specific requirements of the application and the customer’s preferences. However, Ajinomoto typically offers substrates made from advanced materials such as fiberglass-reinforced epoxy resin (FR-4) or polyimide.
- Fiberglass-Reinforced Epoxy Resin (FR-4): FR-4 is a widely used substrate material in the electronics industry due to its excellent electrical insulation properties, mechanical strength, and cost-effectiveness. It consists of layers of woven fiberglass fabric impregnated with epoxy resin, providing good dimensional stability and reliability.
- Polyimide: Polyimide substrates offer exceptional thermal stability, chemical resistance, and flexibility, making them ideal for applications requiring high temperature and harsh environment operation. Polyimide substrates are often used in aerospace, automotive, and military applications where reliability and durability are paramount.
Both FR-4 and polyimide substrates can be manufactured with various thicknesses, copper foil weights, and surface finishes to meet specific performance requirements. The choice between these materials depends on factors such as operating conditions, signal integrity requirements, and cost considerations.
Which company manufactures Ajinomoto GXT31R2 package substrates?
The Ajinomoto GXT31R2 package substrate is manufactured by Ajinomoto Fine-Techno, a Japanese company renowned in the field of electronic packaging. Ajinomoto Fine-Techno specializes in developing and producing high-performance package substrates, providing reliable electrical connections and thermal performance for semiconductor devices. With advanced manufacturing equipment, technologies, and an experienced engineering team, the company is committed to delivering customized solutions that meet customer needs.
Our company also has the capability to produce similar package substrates. Equipped with advanced production lines and process technologies, we can meet various requirements for Ajinomoto GXT31R2 package substrates. Our manufacturing process strictly adheres to industry standards and customer specifications to ensure stable and reliable product quality. We can select appropriate substrate materials (such as FR-4 or polyimide), design suitable layer stackups, control circuit layout and characteristics accurately, implement high-quality manufacturing processes, and conduct comprehensive quality inspections and testing to produce high-performance package substrates that meet customer expectations.
We prioritize technological innovation and quality management, striving to provide customers with the highest quality products and services. With a passionate and professional team, we are dedicated to supporting and collaborating with customers to drive the development and advancement of electronic packaging technology.
What are the 7 qualities of good customer service?
Good customer service is essential for building strong relationships with customers and fostering loyalty. Here are seven qualities that contribute to providing excellent customer service:
- Responsive: Good customer service involves promptly addressing customer inquiries, concerns, and requests. Being responsive means acknowledging customers’ needs in a timely manner and providing assistance or information promptly.
- Empathetic: Empathy is key to understanding customers’ perspectives and feelings. Good customer service representatives listen actively, show understanding, and demonstrate compassion when dealing with customers’ issues or complaints.
- Knowledgeable: Providing accurate and relevant information is crucial for resolving customer inquiries and concerns effectively. Good customer service representatives possess in-depth knowledge about the products or services they offer, as well as company policies and procedures.
- Professionalism: Professionalism encompasses maintaining a courteous and respectful demeanor, even in challenging situations. Good customer service representatives communicate clearly and professionally, maintaining composure and addressing issues with diplomacy and tact.
- Problem-Solving Skills: Good customer service involves identifying and resolving customer issues efficiently and effectively. Customer service representatives should possess strong problem-solving skills, including the ability to analyze situations, propose solutions, and follow through to ensure customer satisfaction.
- Adaptability: Every customer interaction is unique, and situations may vary widely. Good customer service representatives are adaptable and flexible, able to adjust their approach to meet the specific needs and preferences of each customer.
- Consistency:Consistency is important for building trust and reliability. Good customer service involves delivering a consistent level of service quality across all customer interactions, regardless of the channel or touchpoint. Consistent service helps establish a positive reputation and fosters long-term customer relationships.
By embodying these qualities, businesses can provide exceptional customer service experiences that enhance customer satisfaction, loyalty, and retention.
FAQs (Frequently Asked Questions)
What is Ajinomoto GXT31R2 package substrate?
The Ajinomoto GXT31R2 package substrate is a high-performance substrate used in electronic packaging, particularly in semiconductor devices. It provides electrical connectivity between integrated circuits (ICs) and the system board.
What are the key features of Ajinomoto GXT31R2 package substrate?
The Ajinomoto GXT31R2 substrate typically features advanced materials, precise conductor patterns, and optimized thermal management capabilities. It offers excellent electrical performance, reliability, and compatibility with various packaging technologies.
What are the applications of Ajinomoto GXT31R2 package substrate?
Ajinomoto GXT31R2 package substrates are used in a wide range of semiconductor applications, including consumer electronics, telecommunications, automotive systems, industrial equipment, and medical devices.
What are the benefits of using Ajinomoto GXT31R2 package substrate?
Some benefits of using Ajinomoto GXT31R2 package substrate include enhanced electrical performance, improved thermal management, increased reliability, and compatibility with advanced packaging technologies.
How is Ajinomoto GXT31R2 package substrate manufactured?
The manufacturing process for Ajinomoto GXT31R2 package substrate involves several steps, including substrate preparation, layer stackup design, conductor pattern formation, via formation, surface finish application, final inspection, and testing.
Where can I purchase Ajinomoto GXT31R2 package substrate?
Ajinomoto GXT31R2 package substrates are typically available through authorized distributors or directly from Ajinomoto Fine-Techno, the manufacturer of the substrate. Customers can contact Ajinomoto or its distributors for inquiries and purchases.
What are the customization options for Ajinomoto GXT31R2 package substrate?
Ajinomoto GXT31R2 package substrate can be customized based on specific customer requirements, including substrate material, layer stackup configuration, conductor patterns, surface finishes, and testing specifications.