Ajinomoto GX92R Package Substrate Manufacturer
Ajinomoto GX92R Package Substrate Manufacturer,Ajinomoto GX92R package substrates represent a cutting-edge solution for semiconductor packaging needs. Engineered with precision and innovation, these substrates offer exceptional thermal conductivity, ensuring efficient heat dissipation to maintain optimal performance of semiconductor devices. Their superior electrical properties facilitate reliable signal transmission and power distribution within electronic systems, enhancing overall functionality and performance. With a focus on durability and mechanical stability, Ajinomoto GX92R substrates provide a robust platform for mounting and interconnecting semiconductor components, ensuring long-term reliability in demanding applications. These substrates are versatile and adaptable, suitable for a wide range of electronic devices, including integrated circuits, microprocessors, and power modules. With Ajinomoto GX92R package substrates, manufacturers can achieve higher levels of integration, improved reliability, and enhanced performance in their electronic products, meeting the evolving demands of modern technology.
What is Ajinomoto GX92R package substrate?
Ajinomoto GX92R is a type of package substrate used in electronic components, particularly in semiconductor devices like integrated circuits (ICs). Package substrates are essentially the base layers upon which semiconductor chips are mounted and interconnected to create functional electronic components.
The specific details of Ajinomoto GX92R package substrate would likely include its material composition, electrical properties, thermal conductivity, and other characteristics important for the performance and reliability of the electronic device it’s used in. However, without specific documentation or access to technical specifications, I can’t provide detailed information on GX92R.
Ajinomoto is a Japanese company known for various products, including food ingredients and chemicals. They may have developed GX92R as a specialized substrate material for electronic applications. If you need more detailed information, you might want to consult technical documentation from Ajinomoto or reach out to them directly.
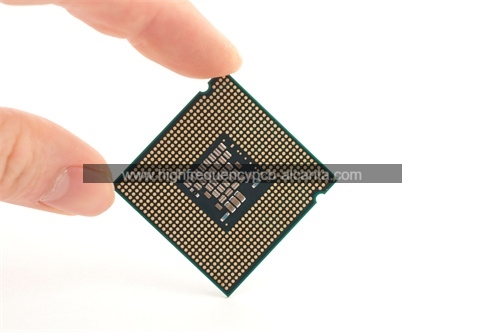
Ajinomoto GX92R Package Substrate Manufacturer
What are the design guidelines for Ajinomoto GX92R package substrate?
Design guidelines for Ajinomoto GX92R package substrates would typically encompass a range of factors crucial for their performance and compatibility with semiconductor packaging applications. Here’s an extended outline covering various aspects of these guidelines:
- Material Composition: Ajinomoto GX92R package substrates are likely composed of advanced materials optimized for thermal management, electrical conductivity, and mechanical stability. Design guidelines would specify the composition and properties of these materials to ensure reliability and performance.
- Dimensional Stability: The substrate design should ensure dimensional stability under different thermal and mechanical stresses encountered during the assembly and operation of semiconductor devices. Guidelines would outline maximum allowable dimensional changes to prevent warping or distortion.
- Thermal Management: Effective heat dissipation is critical for maintaining semiconductor device performance and reliability. Design guidelines would include specifications for thermal conductivity, heat capacity, and thermal expansion coefficient to facilitate efficient heat transfer away from the chip.
- Electrical Performance:Substrate designs must meet stringent electrical performance requirements to ensure signal integrity and power distribution within the semiconductor package. Guidelines would cover parameters such as impedance control, signal routing, and power delivery network design.
- Signal Integrity: High-speed semiconductor devices demand careful consideration of signal integrity to minimize signal degradation and timing errors. Design guidelines would include recommendations for controlled impedance routing, signal return paths, and noise isolation techniques.
- Manufacturability: Design guidelines should account for manufacturability considerations to ensure cost-effective production and high yield rates. This may involve recommendations for panelization, fiducial marker placement, and design for assembly (DFA) principles.
- Reliability and Durability: Substrate designs must exhibit robustness and durability to withstand harsh operating environments and mechanical stresses. Guidelines would address factors such as material fatigue, solder joint reliability, and resistance to moisture and chemical exposure.
- Compatibility with Assembly Processes: Guidelines should ensure compatibility with various assembly processes, including surface mount technology (SMT), flip-chip bonding, and wire bonding. This may involve recommendations for solder mask design, pad layout, and component placement.
- Compliance and Standards: Design guidelines may reference industry standards and compliance requirements relevant to semiconductor packaging, such as JEDEC standards for package outlines, thermal characterization, and reliability testing.
- Documentation and Verification: Clear documentation detailing design specifications, tolerances, and performance requirements is essential for successful implementation. Design guidelines should also include recommendations for design verification through simulations, prototyping, and testing.
By adhering to these design guidelines, semiconductor manufacturers can ensure the optimal performance, reliability, and manufacturability of Ajinomoto GX92R package substrates in diverse electronic applications.
What is the fabrication process of Ajinomoto GX92R package substrate?
The fabrication process of Ajinomoto GX92R package substrates likely involves several precise steps to create substrates with the desired properties and performance characteristics. While specific details may vary based on the exact materials and manufacturing techniques employed, here’s an extended overview of a typical fabrication process:
- Substrate Preparation: The fabrication process begins with the preparation of the substrate base material. This material could be a specialized composite, such as epoxy resin reinforced with glass fibers or other additives. The substrate material is typically supplied in the form of sheets or panels.
- Panelization: Large substrate panels are often fabricated to accommodate multiple substrates in a single manufacturing run. Panelization involves cutting the substrate material into smaller individual units, each of which will eventually become a separate package substrate.
- Surface Treatment: Surface treatment processes are applied to the substrate material to improve adhesion and promote uniformity during subsequent manufacturing steps. This may involve processes such as surface roughening, chemical etching, or plasma treatment to activate the substrate surface.
- Circuit Patterning: The substrate material is coated with a thin layer of conductive material, such as copper, using techniques like sputtering or electroplating. Photolithography and etching processes are then used to define the desired circuit patterns on the substrate surface. This step forms the conductive traces and pads that will facilitate electrical connections within the package substrate.
- Dielectric Layer Deposition:After circuit patterning, dielectric layers are deposited onto the substrate surface to insulate the conductive traces and provide mechanical support. Dielectric materials with high thermal conductivity and low coefficient of thermal expansion (CTE) may be chosen to enhance thermal management properties.
- Via Formation: Vias, or plated through-holes, are created in the substrate to facilitate electrical connections between different layers of the package substrate. Via formation typically involves drilling or laser ablation followed by metallization processes to line the vias with conductive material.
- Surface Finishing: Surface finishing processes are applied to the substrate to improve solderability and corrosion resistance. Common surface finishes include electroless nickel immersion gold (ENIG), organic solderability preservatives (OSP), and immersion tin or silver.
- Final Inspection and Testing: Once fabrication is complete, the package substrates undergo rigorous inspection and testing to ensure they meet quality standards and specifications. This may include visual inspection, dimensional measurements, electrical continuity testing, and reliability testing under simulated operating conditions.
- Packaging and Shipping:Finished package substrates are packaged according to industry standards to protect them during transportation and storage. Proper packaging also helps prevent damage and contamination that could compromise substrate performance.
By following these fabrication steps with precision and attention to detail, manufacturers can produce Ajinomoto GX92R package substrates with the desired electrical, thermal, and mechanical properties required for semiconductor packaging applications.
How do you manufacture Ajinomoto GX92R package substrate?
Manufacturing Ajinomoto GX92R package substrates involves a series of intricate processes to produce high-quality substrates suitable for use in semiconductor packaging. While specific details may vary depending on the exact formulation and proprietary techniques used by Ajinomoto, here’s an extended overview of a typical manufacturing process:
- Material Selection and Preparation: Ajinomoto GX92R package substrates are likely composed of advanced composite materials optimized for thermal conductivity, electrical performance, and mechanical stability. The manufacturing process begins with the selection and preparation of these raw materials, which may include epoxy resins, reinforcing fibers, fillers, and additives.
- Formulation and Mixing: The raw materials are carefully measured and mixed according to precise formulations to achieve the desired material properties. Mixing processes may involve mechanical stirring, high-shear mixing, or extrusion to ensure uniform dispersion of additives and reinforcement fibers within the resin matrix.
- Substrate Formation: The mixed material is then processed into substrate sheets or panels using techniques such as compression molding, resin transfer molding (RTM), or lamination. During this stage, the material may be subjected to heat and pressure to facilitate resin curing and consolidation of the composite structure.
- Panelization and Cutting: Large substrate panels are often fabricated to accommodate multiple substrates in a single manufacturing run. Panelization involves cutting the substrate material into smaller individual units, each of which will become a separate package substrate.
- Surface Treatment:Surface treatment processes are applied to the substrate material to improve adhesion and promote uniformity during subsequent manufacturing steps. This may involve processes such as surface roughening, plasma treatment, or chemical etching to activate the substrate surface.
- Circuit Patterning: A thin layer of conductive material, such as copper, is deposited onto the substrate surface using techniques like sputtering, electroplating, or chemical vapor deposition (CVD). Photolithography and etching processes are then employed to define the desired circuit patterns on the substrate surface, forming the conductive traces and pads.
- Dielectric Layer Deposition:Dielectric layers are deposited onto the substrate surface to insulate the conductive traces and provide mechanical support. Dielectric materials with high thermal conductivity and low coefficient of thermal expansion (CTE) may be chosen to enhance thermal management properties.
- Via Formation: Vias, or plated through-holes, are created in the substrate to facilitate electrical connections between different layers of the package substrate. Via formation typically involves drilling or laser ablation followed by metallization processes to line the vias with conductive material.
- Surface Finishing: Surface finishing processes are applied to the substrate to improve solderability and corrosion resistance. Common surface finishes include electroless nickel immersion gold (ENIG), organic solderability preservatives (OSP), and immersion tin or silver.
- Final Inspection and Testing: Once manufacturing is complete, the package substrates undergo thorough inspection and testing to ensure they meet quality standards and specifications. This may include visual inspection, dimensional measurements, electrical continuity testing, and reliability testing under simulated operating conditions.
- Packaging and Shipping: Finished package substrates are packaged according to industry standards to protect them during transportation and storage. Proper packaging also helps prevent damage and contamination that could compromise substrate performance.
By following these manufacturing processes with precision and adherence to quality standards, Ajinomoto produces GX92R package substrates with the necessary properties and performance characteristics for use in semiconductor packaging applications.
How much should an Ajinomoto GX92R package substrate cost?
Determining the exact cost of an Ajinomoto GX92R package substrate can be challenging without specific pricing information from Ajinomoto or its authorized distributors. The cost of package substrates can vary significantly depending on factors such as:
- Materials: The cost of raw materials used in the substrate, including resin, reinforcement fibers, conductive materials, and dielectric layers, can influence the overall cost.
- Manufacturing Process: The complexity of the manufacturing process, including fabrication techniques, surface treatments, and quality control measures, can impact production costs.
- Volume: Purchasing larger quantities of package substrates typically leads to volume discounts, with lower per-unit costs for larger orders.
- Customization: Customized features or specialized requirements may incur additional costs compared to standard off-the-shelf substrates.
- Quality and Performance: Substrates designed for high-performance applications with stringent quality and reliability requirements may command higher prices compared to standard substrates.
- Market Demand: Market demand and competition within the semiconductor packaging industry can influence pricing dynamics.
To obtain an accurate cost estimate for Ajinomoto GX92R package substrates, it’s best to contact Ajinomoto directly or consult with authorized distributors for pricing information based on your specific requirements, including desired quantities, customization needs, and performance specifications.
What is the base material for Ajinomoto GX92R package substrate?
As of my last update, specific information regarding the base material for Ajinomoto GX92R package substrates isn’t readily available. However, package substrates are typically composed of composite materials optimized for their electrical, thermal, and mechanical properties.
Common base materials for package substrates include:
- Epoxy Resin: Epoxy resins are frequently used as the matrix material in composite substrates due to their excellent adhesion, mechanical strength, and thermal stability.
- Reinforcement Fibers: Various types of reinforcement fibers, such as glass fibers, aramid fibers, or carbon fibers, may be incorporated into the epoxy resin matrix to enhance mechanical properties like stiffness and tensile strength.
- Fillers and Additives: Fillers and additives may be included in the substrate formulation to modify properties such as thermal conductivity, coefficient of thermal expansion (CTE), and flame retardancy.
- Copper Foil: Copper foil layers are typically used to create the conductive traces and pads on the substrate surface through processes like etching or lithography.
- Dielectric Materials: Dielectric layers are applied to insulate the conductive traces and provide mechanical support. These dielectric materials may include thermoset resins, ceramics, or specialized polymers with high thermal conductivity and low CTE.
- Surface Finishes: Surface finishes, such as electroless nickel immersion gold (ENIG) or organic solderability preservatives (OSP), are applied to improve solderability and corrosion resistance.
While the specific formulation of Ajinomoto GX92R package substrates remains proprietary, they are likely engineered to offer a balance of electrical performance, thermal management, and mechanical reliability tailored to semiconductor packaging applications. For detailed information on the base material composition and properties of Ajinomoto GX92R package substrates, it’s recommended to consult directly with Ajinomoto or refer to their technical documentation.
Which company manufactures Ajinomoto GX92R package substrate?
Ajinomoto GX92R package substrates are manufactured by Ajinomoto, a company based in Japan. Ajinomoto is a global corporation known for its food, chemical, and biotechnology products. While it is commonly recognized for its food additives and seasoning manufacturing, it also ventures into the chemical and materials sectors.
Our company can produce Ajinomoto GX92R package substrates because we possess advanced manufacturing equipment, extensive experience, and a professional team. As a manufacturer specializing in the semiconductor packaging industry, we are committed to providing high-quality, high-performance substrate products to meet customer demands.
Our production process covers material selection, process optimization, quality control, and more. We employ advanced materials and manufacturing technologies to ensure our products have excellent electrical performance, thermal performance, and mechanical stability. Furthermore, we prioritize communication and collaboration with customers to ensure our products meet their specific technical and application requirements.
We strive to provide customized solutions to adapt to different needs and challenges. Through continuous improvement and innovation, we aim to enhance production efficiency and product quality to meet the needs of customers in the semiconductor packaging field.
In summary, our company has the technical capabilities, production capacity, and professional experience to manufacture Ajinomoto GX92R package substrates. We are dedicated to providing customers with high-quality products and services, aiming for mutual development and success.
What are the 7 qualities of good customer service?
Good customer service is characterized by several key qualities that contribute to positive interactions and customer satisfaction. Here are seven important qualities:
- Responsiveness: Customers appreciate prompt responses to their inquiries, whether through phone calls, emails, live chat, or in-person interactions. Being responsive shows that you value their time and concerns.
- Empathy: Empathy involves understanding and acknowledging the customer’s feelings, needs, and concerns. It’s essential to listen actively, show compassion, and demonstrate genuine interest in resolving their issues.
- Clarity: Providing clear and concise information helps customers understand your products, services, policies, and solutions to their problems. Avoiding jargon and communicating in a straightforward manner fosters transparency and trust.
- Professionalism: Professionalism encompasses courtesy, politeness, and professionalism in all customer interactions. This includes maintaining a positive attitude, remaining calm under pressure, and resolving conflicts respectfully.
- Knowledgeability:Customers expect representatives to be knowledgeable about the products or services offered, as well as company policies and procedures. Being well-informed enables you to answer questions accurately and provide valuable assistance.
- Flexibility: Flexibility involves adapting to the unique needs and preferences of each customer. Being flexible may include offering personalized solutions, accommodating special requests, or adjusting policies when appropriate to ensure customer satisfaction.
- Consistency: Consistency is key to building trust and loyalty with customers. Providing a consistently high level of service across all touchpoints and interactions reinforces your commitment to customer satisfaction and reinforces your brand reputation.
By embodying these qualities, businesses can deliver exceptional customer service experiences that leave a lasting positive impression and foster customer loyalty.
FAQs
What are Ajinomoto GX92R package substrates?
Ajinomoto GX92R package substrates are advanced materials used in semiconductor packaging. They provide a platform for mounting and interconnecting semiconductor devices within electronic systems.
What are the key features of Ajinomoto GX92R package substrates?
Ajinomoto GX92R package substrates are engineered to offer excellent thermal conductivity, electrical performance, and mechanical stability. They are designed to meet the demanding requirements of modern semiconductor devices and electronic applications.
What applications are Ajinomoto GX92R package substrates suitable for?
Ajinomoto GX92R package substrates are commonly used in a wide range of electronic applications, including integrated circuits (ICs), microprocessors, memory modules, power modules, and more. They are particularly well-suited for high-performance and high-density electronic devices.
What materials are used in Ajinomoto GX92R package substrates?
The specific materials used in Ajinomoto GX92R package substrates may vary, but they typically include advanced composite materials optimized for their electrical, thermal, and mechanical properties. These materials may include epoxy resins, reinforcement fibers, conductive materials, and dielectric layers.
What are the benefits of using Ajinomoto GX92R package substrates?
Some benefits of using Ajinomoto GX92R package substrates include improved thermal management, enhanced electrical performance, increased reliability, and reduced size and weight compared to traditional packaging solutions. They also enable higher levels of integration and functionality in electronic devices.
Where can I purchase Ajinomoto GX92R package substrates?
Ajinomoto GX92R package substrates may be available through authorized distributors or directly from Ajinomoto. Customers can inquire about purchasing options and availability by contacting Ajinomoto or its authorized representatives.
Are Ajinomoto GX92R package substrates customizable?
Yes, Ajinomoto GX92R package substrates can often be customized to meet specific customer requirements. Customization options may include substrate size and shape, material composition, surface finishes, and electrical properties. Customers can discuss their customization needs with Ajinomoto or its authorized representatives.