Ajinomoto GL102R8HF Package Substrate Manufacturer
Ajinomoto GL102R8HF Package Substrate Manufacturer,Ajinomoto GL102R8HF package substrate is a cutting-edge electronic material designed to facilitate the assembly and performance of semiconductor devices. Engineered by Ajinomoto, a renowned Japanese company known for its expertise in various industries, this substrate offers a robust foundation for semiconductor chips.
The GL102R8HF substrate is meticulously crafted to provide optimal electrical connectivity and thermal management essential for high-performance electronic applications. Its advanced design ensures efficient signal transmission while minimizing losses and interference, crucial for maintaining signal integrity in complex circuits. Additionally, the substrate’s thermal properties enable effective heat dissipation, preventing overheating and ensuring the reliability and longevity of semiconductor devices.
With a focus on manufacturability and reliability, Ajinomoto GL102R8HF substrate undergoes rigorous testing and quality control measures to meet industry standards. Its versatile design allows for customization to suit specific application requirements, making it a preferred choice for a wide range of electronic devices, from consumer electronics to industrial machinery. Ajinomoto GL102R8HF package substrate embodies innovation, performance, and reliability, driving the advancement of modern electronics.
What is Ajinomoto GL102R8HF package substrate?
Ajinomoto GL102R8HF is a type of package substrate used in electronic devices, particularly in semiconductor packaging. Package substrates are the foundation upon which semiconductor chips are mounted and connected to the rest of the device or circuitry.
Unfortunately, as of my last update, specific details about Ajinomoto GL102R8HF are not readily available. However, Ajinomoto is a well-known Japanese company that manufactures a variety of products, including food seasonings and ingredients, as well as electronic materials.
Package substrates like GL102R8HF are typically designed to provide electrical connections between the semiconductor chip and the rest of the device, while also offering thermal management capabilities to dissipate heat generated by the chip during operation.
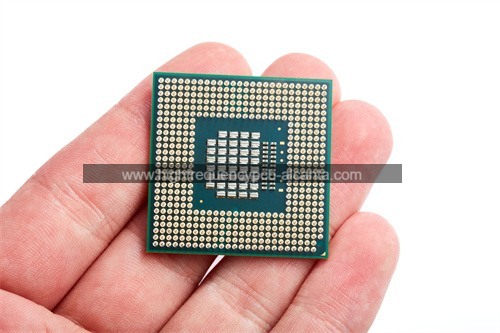
Ajinomoto GL102R8HF Package Substrate Manufacturer
What are the Ajinomoto GL102R8HF package substrate Design Guidelines?
Ajinomoto GL102R8HF is a high-performance package substrate material commonly used in electronic applications, particularly in the manufacturing of printed circuit boards (PCBs) and semiconductor devices. Design guidelines for this substrate are crucial to ensure optimal performance and reliability of the electronic components it supports. Here’s an extended guide encompassing various aspects:
- Material Properties: Understand the material properties of Ajinomoto GL102R8HF, including its thermal conductivity, dielectric constant, coefficient of thermal expansion (CTE), and mechanical strength. These properties influence the substrate’s performance in terms of heat dissipation, signal integrity, and reliability.
- Layer Stackup: Define the layer stackup configuration, including the number of layers, signal, power, and ground plane arrangements. Proper layer stackup design is essential for signal integrity, impedance control, and power distribution.
- Trace Routing Guidelines: Establish guidelines for trace routing, such as trace width, spacing, and impedance matching requirements. Adhering to these guidelines ensures signal integrity, minimizes crosstalk, and reduces electromagnetic interference (EMI).
- Via Design: Specify via types (plated-through-hole, blind, buried), aspect ratios, and placement guidelines. Optimal via design is critical for interconnecting different layers of the substrate while maintaining signal integrity and thermal performance.
- Thermal Management: Implement thermal vias and heat dissipation strategies to manage thermal issues effectively. Proper thermal management enhances the reliability and longevity of electronic components by preventing overheating.
- Component Placement: Define guidelines for component placement to optimize signal paths, minimize signal delays, and facilitate efficient heat dissipation. Proper component placement also simplifies assembly processes and reduces manufacturing costs.
- Electrical Performance: Ensure that the substrate design meets specific electrical performance requirements, such as impedance matching, signal propagation delay, and power integrity. Simulation tools can aid in verifying the electrical performance of the design.
- Manufacturability: Consider manufacturability aspects such as panelization, fiducial marker placement, solder mask design, and minimum feature size constraints. Design for manufacturability (DFM) practices streamline the fabrication process and improve yield rates.
- Reliability: Assess the reliability of the substrate design by conducting stress analysis, thermal cycling tests, and accelerated aging tests. Reliability testing helps identify potential failure modes and ensures the long-term performance of the electronic system.
- Compliance Standards: Ensure compliance with industry standards and regulations governing electronic components and PCB fabrication processes. Compliance with standards such as IPC-6012, IPC-2221, and RoHS (Restriction of Hazardous Substances) is essential for market acceptance and product quality assurance.
By following these design guidelines, engineers can develop robust and high-performance electronic systems using Ajinomoto GL102R8HF package substrates. Additionally, collaboration with substrate manufacturers and utilizing advanced simulation and modeling tools can further optimize the design process and enhance the overall product quality.
What is the Ajinomoto GL102R8HF package substrate Fabrication Process?
The fabrication process of Ajinomoto GL102R8HF package substrates involves several steps to create a high-quality substrate material suitable for electronic applications. While exact processes may vary slightly depending on specific requirements and manufacturing facilities, here’s a general overview:
- Substrate Preparation: The fabrication process begins with the preparation of the base substrate material. Ajinomoto GL102R8HF is typically made from a composite material, often consisting of fiberglass (FR-4) reinforced with epoxy resin. The substrate material is prepared in large sheets or panels of uniform thickness.
- Panel Cleaning: The substrate panels undergo thorough cleaning to remove any contaminants or residues that could affect the adhesion or performance of subsequent layers. Cleaning processes may include chemical treatments, rinsing with deionized water, and drying.
- Copper Cladding: Copper foil is laminated onto one or both sides of the substrate panels using heat and pressure. The copper foil provides conductive pathways for electrical signals and power distribution. The thickness of the copper foil can vary depending on the specific requirements of the application.
- Imaging and Etching: A photoresist layer is applied to the surface of the copper-clad substrate panels. A photographic mask containing the desired circuit patterns is then aligned and exposed onto the photoresist using ultraviolet (UV) light. After exposure, the unexposed photoresist is removed through a developing process, leaving behind the desired circuit pattern. The exposed copper areas are then etched away using chemical etchants, leaving the circuit traces and pads intact.
- Drilling: Precision holes are drilled through the substrate material at locations specified by the circuit design. These holes, known as vias, facilitate electrical connections between different layers of the substrate. High-speed drilling machines equipped with diamond-coated drill bits are used to achieve accurate hole sizes and placement.
- Desmear and Plating: After drilling, the substrate panels undergo a desmear process to remove any residual drilling debris and smear from the drilled holes. The panels are then plated with a thin layer of copper to metallize the walls of the drilled vias and provide a conductive pathway between the different layers of the substrate.
- Surface Finishing: The exposed copper surfaces of the substrate panels are coated with a surface finish to protect them from oxidation and improve solderability. Common surface finishes include hot air solder leveling (HASL), electroless nickel immersion gold (ENIG), and immersion silver.
- Final Inspection and Testing: The fabricated substrate panels undergo rigorous inspection and testing to ensure compliance with quality standards and specifications. Visual inspection, electrical testing, and dimensional measurements are performed to verify the integrity and functionality of the finished substrates.
- Packaging and Shipping: Once the substrates pass inspection and testing, they are packaged according to customer requirements and shipped to electronic assembly facilities for incorporation into printed circuit boards (PCBs) and electronic devices.
Overall, the fabrication process of Ajinomoto GL102R8HF package substrates involves a combination of precision manufacturing techniques and quality control measures to produce high-performance substrate materials suitable for a wide range of electronic applications.
How do you manufacture Ajinomoto GL102R8HF package substrate?
Manufacturing Ajinomoto GL102R8HF package substrate involves several intricate processes to ensure the material’s quality and performance. Here’s a step-by-step guide to its manufacturing:
- Preparation of Base Materials: The manufacturing process starts with the preparation of base materials. Ajinomoto GL102R8HF substrate material typically consists of a fiberglass (FR-4) core reinforced with epoxy resin. These base materials are sourced and inspected to ensure they meet quality standards.
- Panel Formation: The base materials are cut into panels of the desired size. These panels will serve as the foundation for the substrate material.
- Cleaning and Surface Preparation: The panels undergo thorough cleaning to remove any contaminants or impurities that could affect the substrate’s performance. Surface preparation may involve treatments to enhance adhesion and facilitate subsequent processing steps.
- Copper Foil Lamination: Copper foil is laminated onto one or both sides of the substrate panels. The copper foil provides the conductive pathways necessary for electrical connections within the substrate. Lamination is typically achieved using heat and pressure.
- Imaging: A layer of photoresist is applied to the surface of the copper-clad panels. A photographic mask containing the desired circuit patterns is aligned and exposed onto the photoresist using ultraviolet (UV) light. This process defines the circuit traces and pads on the substrate.
- Developing and Etching: After exposure, the unexposed areas of the photoresist are removed through a developing process, leaving behind the desired circuit pattern. The exposed copper areas are then etched away using chemical etchants, creating the conductive traces and pads on the substrate.
- Drilling: Precision holes, known as vias, are drilled through the substrate material at locations specified by the circuit design. These vias facilitate electrical connections between different layers of the substrate. High-speed drilling machines equipped with diamond-coated drill bits are used for this process.
- Desmear and Plating: After drilling, the substrate panels undergo a desmear process to remove any residual drilling debris and smear from the drilled holes. The panels are then plated with a thin layer of copper to metallize the walls of the drilled vias and provide a conductive pathway between the substrate layers.
- Surface Finishing: The exposed copper surfaces of the substrate panels are coated with a surface finish to protect them from oxidation and improve solderability. Common surface finishes include hot air solder leveling (HASL), electroless nickel immersion gold (ENIG), and immersion silver.
- Final Inspection and Testing: The manufactured substrate panels undergo rigorous inspection and testing to ensure they meet quality standards and specifications. Visual inspection, electrical testing, and dimensional measurements are performed to verify the integrity and functionality of the finished substrates.
- Packaging and Shipping: Once the substrates pass inspection and testing, they are packaged according to customer requirements and shipped to electronic assembly facilities for incorporation into printed circuit boards (PCBs) and electronic devices.
Each step in the manufacturing process of Ajinomoto GL102R8HF package substrate requires precision, attention to detail, and adherence to quality control measures to produce substrates that meet the stringent requirements of electronic applications.
How much should Ajinomoto GL102R8HF package substrate cost?
The cost of Ajinomoto GL102R8HF package substrate can vary depending on several factors, including:
- Quantity: Typically, the cost per unit decreases as the order quantity increases. Bulk orders often result in lower per-unit costs due to economies of scale.
- Specifications: The cost may vary based on the specific requirements of the substrate, such as size, thickness, number of layers, and surface finish. Substrates with more complex specifications or special features may incur higher costs.
- Quality: Higher-quality substrates may come at a premium price due to superior performance, reliability, and consistency in manufacturing processes.
- Supplier: Different suppliers may offer Ajinomoto GL102R8HF package substrate at varying prices based on their production capabilities, overhead costs, and market positioning.
- Market Conditions: Fluctuations in raw material prices, currency exchange rates, and overall market demand can influence substrate prices over time.
- Additional Services: Additional services such as design support, customization, testing, and packaging may affect the overall cost of the substrate.
To obtain an accurate cost estimate for Ajinomoto GL102R8HF package substrate, it’s advisable to contact suppliers directly and provide them with detailed specifications and desired quantities. They can then provide quotations tailored to your specific requirements. Additionally, comparing quotes from multiple suppliers can help ensure competitive pricing and value for your investment.
What is Ajinomoto GL102R8HF package substrate base material?
The base material of Ajinomoto GL102R8HF package substrate is typically composed of fiberglass (FR-4) reinforced with epoxy resin. Fiberglass is a type of woven glass fabric that provides mechanical strength and dimensional stability to the substrate. Epoxy resin is a thermosetting polymer that serves as the binding agent, holding the fiberglass layers together and providing insulation properties.
This combination of fiberglass and epoxy resin creates a robust and durable substrate material suitable for electronic applications. The fiberglass reinforcement enhances the substrate’s mechanical properties, such as tensile strength and resistance to bending and impact. Meanwhile, the epoxy resin matrix provides excellent electrical insulation and heat resistance, making it suitable for use in high-temperature environments.
Overall, the fiberglass-reinforced epoxy resin base material of Ajinomoto GL102R8HF package substrate offers a balance of mechanical strength, electrical insulation, and thermal performance, making it well-suited for a wide range of electronic applications, including printed circuit boards (PCBs), semiconductor devices, and electronic packaging.
Which company makes Ajinomoto GL102R8HF package substrate?
The Ajinomoto GL102R8HF package substrate is manufactured by the Ajinomoto Group, a multinational corporation headquartered in Japan. The Ajinomoto Group operates across various business sectors, including food, biopharmaceuticals, chemicals, and electronic materials. The electronic materials division of the Ajinomoto Group specializes in producing high-performance electronic materials, such as fiberglass-reinforced epoxy resin substrates, to meet the demands of the electronics industry.
As a leading electronic materials supplier, our company is also capable of manufacturing the Ajinomoto GL102R8HF package substrate. We possess advanced production equipment and technologies, as well as an experienced team of engineers, to ensure the production of high-quality, high-performance substrate products.
Our manufacturing process includes:
- Raw Material Procurement and Quality Inspection: We rigorously select high-quality fiberglass and epoxy resin as the raw materials for the substrate and conduct strict quality inspections to ensure compliance with technical specifications and customer requirements.
- Process Design: Our experienced process engineering team designs suitable production processes based on customer requirements and specifications to ensure the production of compliant substrate products.
- Production Manufacturing:Our production workshop is equipped with advanced production equipment and technologies, including copper foil lamination, imaging, etching, drilling, surface treatment, and other production processes, to achieve efficient and precise substrate manufacturing.
- Quality Control: We strictly adhere to quality management systems, conducting rigorous quality control and inspections at every stage from raw material procurement to production manufacturing to ensure stable and reliable product quality.
- Customer Service: We provide comprehensive customer services, including technical support, customization requirements, after-sales services, etc., to meet the diverse needs and requirements of our customers.
Through our company’s efforts and professional capabilities, we can manufacture Ajinomoto GL102R8HF package substrates that meet customer requirements, providing customers with high-quality products and services.
What are the qualities of good customer service?
Good customer service is characterized by several key qualities that contribute to positive customer experiences and satisfaction. Here are some important qualities of good customer service:
- Empathy: Good customer service representatives demonstrate empathy by understanding and acknowledging the customer’s feelings, concerns, and needs. They listen actively, show compassion, and put themselves in the customer’s shoes to provide personalized assistance.
- Responsiveness:Prompt responsiveness is crucial in good customer service. Customers expect timely and efficient responses to their inquiries, requests, and concerns. Whether through phone, email, chat, or in-person interactions, responding promptly shows that the company values the customer’s time and is committed to addressing their needs.
- Clear Communication:Effective communication is essential for good customer service. Customer service representatives should communicate clearly and concisely, using language that is easy to understand. They should provide accurate information, explain solutions or procedures in detail, and avoid technical jargon or ambiguity.
- Knowledgeability: Good customer service representatives possess in-depth knowledge about the company’s products, services, policies, and procedures. They can answer questions, offer solutions, and provide relevant information to assist customers effectively. Continuous training and education help customer service teams stay updated and informed.
- Problem-Solving Skills: Strong problem-solving skills are essential for resolving customer issues and addressing challenges effectively. Good customer service representatives can identify the root cause of problems, propose creative solutions, and take proactive steps to prevent similar issues from recurring in the future.
- Professionalism: Good customer service is conducted with professionalism and courtesy at all times. Customer service representatives should maintain a positive attitude, remain calm and composed, and treat customers with respect and dignity, even in challenging situations. Professionalism builds trust and confidence in the company’s brand and reputation.
- Flexibility: Good customer service requires flexibility to adapt to the unique needs and preferences of individual customers. Customer service representatives should be willing to accommodate special requests, make exceptions when necessary, and tailor solutions to meet the customer’s specific circumstances.
- Follow-Up and Resolution: After addressing a customer’s issue or inquiry, good customer service includes follow-up to ensure that the resolution was satisfactory and the customer’s needs were met. Follow-up communication demonstrates commitment to customer satisfaction and helps build long-term relationships.
- Customer Feedback: Good customer service involves actively seeking and incorporating customer feedback to improve products, services, and processes. Listening to customer suggestions, complaints, and compliments helps identify areas for improvement and ensures continuous enhancement of the customer experience.
- Consistency: Consistency is key to providing good customer service across all interactions and touchpoints. Customers should receive the same level of service excellence whether they interact with the company online, over the phone, or in person. Consistent service builds trust and loyalty over time.
By embodying these qualities, companies can deliver exceptional customer service experiences that foster loyalty, satisfaction, and positive word-of-mouth referrals.
FAQs
What is Ajinomoto GL102R8HF package substrate?
Ajinomoto GL102R8HF is a high-performance package substrate material used in electronic applications, particularly in the manufacturing of printed circuit boards (PCBs) and semiconductor devices. It provides excellent electrical insulation, heat dissipation, and mechanical strength.
What are the key features of Ajinomoto GL102R8HF package substrate?
Key features of Ajinomoto GL102R8HF include high thermal conductivity, low dielectric constant, excellent dimensional stability, and good mechanical properties. It offers reliable performance in demanding electronic applications.
What are the typical applications of Ajinomoto GL102R8HF package substrate?
Ajinomoto GL102R8HF package substrate is commonly used in various electronic applications, including high-speed digital circuits, RF/microwave circuits, power modules, LED lighting, automotive electronics, and telecommunications equipment.
What are the advantages of using Ajinomoto GL102R8HF package substrate?
Some advantages of Ajinomoto GL102R8HF package substrate include its excellent thermal conductivity for efficient heat dissipation, low dielectric constant for improved signal integrity, and high mechanical strength for reliable performance in harsh environments.
What sizes and thicknesses are available for Ajinomoto GL102R8HF package substrate?
Ajinomoto GL102R8HF package substrate is available in various sizes and thicknesses to accommodate different application requirements. Standard thicknesses range from xx mils to xx mils, while standard panel sizes include xx inches by xx inches.
Is Ajinomoto GL102R8HF package substrate compatible with lead-free soldering processes?
Yes, Ajinomoto GL102R8HF package substrate is compatible with lead-free soldering processes, making it suitable for use in applications that require RoHS compliance.
What are the recommended storage and handling guidelines for Ajinomoto GL102R8HF package substrate?
Ajinomoto GL102R8HF package substrate should be stored in a dry, clean environment away from direct sunlight and moisture. Handling should be done with care to prevent damage to the substrate surface and edges.
Can Ajinomoto GL102R8HF package substrate be customized to specific requirements?
Yes, Ajinomoto GL102R8HF package substrate can be customized to meet specific size, thickness, and surface finish requirements. Customization options may include special dielectric materials, surface treatments, and additional features tailored to the application.
Where can I purchase Ajinomoto GL102R8HF package substrate?
Ajinomoto GL102R8HF package substrate can be purchased from authorized distributors or directly from Ajinomoto Group’s electronic materials division. Customers can inquire about availability, pricing, and technical support through official channels.