Advanced Semiconductor Glass Substrates Manufacturer
Advanced Semiconductor Glass Substrates Manufacturer,Advanced Semiconductor Glass Substrates (ASGS) represent a pivotal innovation in the realm of semiconductor manufacturing. Crafted from meticulously selected high-purity glass materials, ASGS serves as the foundation for a myriad of cutting-edge electronic components, including integrated circuits, microprocessors, sensors, and display technologies. Renowned for their exceptional thermal stability, electrical insulation, and optical transparency, ASGS substrates offer a robust platform for the realization of high-performance semiconductor devices. The manufacturing process of ASGS entails precise melting, shaping, and surface treatment techniques, culminating in substrates with low thermal expansion coefficients and superior mechanical properties. With their ability to withstand rigorous semiconductor fabrication processes and facilitate advanced manufacturing technologies, ASGS plays a pivotal role in driving innovation and enhancing the efficiency, reliability, and functionality of electronic devices. From powering next-generation microelectronics to revolutionizing display technologies, ASGS continues to push the boundaries of possibility in the semiconductor industry, ushering in a new era of technological advancement.
What is Advanced Semiconductor Glass Substrates (ASGS)?
Advanced Semiconductor Glass Substrates (ASGS) refer to specialized materials used in the semiconductor industry for manufacturing electronic components like integrated circuits (ICs), microprocessors, and other semiconductor devices. These substrates are typically made from high-purity glass with specific properties tailored to meet the demanding requirements of semiconductor fabrication processes.
ASGS offer several advantages over traditional silicon substrates, including better thermal stability, excellent electrical insulation, and improved optical properties. These substrates enable the development of advanced semiconductor devices with higher performance, enhanced reliability, and reduced power consumption.
One key application of ASGS is in the production of advanced display technologies such as OLED (Organic Light Emitting Diode) and MicroLED displays. The superior optical clarity and thermal management properties of ASGS make them ideal for use as the substrate material in these displays, resulting in brighter, more energy-efficient, and higher-resolution screens.
Additionally, ASGS find applications in the manufacturing of MEMS (Micro-Electro-Mechanical Systems) devices, photovoltaic cells, and various optoelectronic components. The continuous innovation in ASGS technology plays a crucial role in driving advancements in the semiconductor industry and enabling the development of next-generation electronic devices with improved performance and functionality.
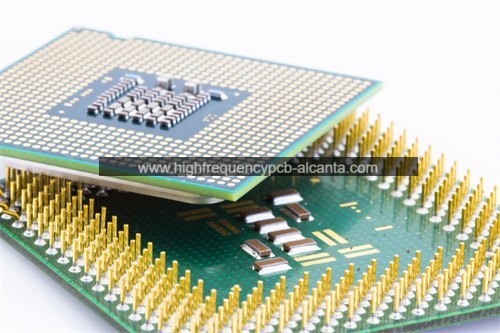
Advanced Semiconductor Glass Substrates
What are the ASGS Design Guidelines?
ASGS (Advanced Semiconductor Glass Substrates) design guidelines encompass a set of principles and criteria that define the specifications, requirements, and best practices for designing semiconductor devices utilizing ASGS materials. These guidelines aim to ensure optimal performance, reliability, and manufacturability of semiconductor devices. While specific design guidelines may vary depending on the application and the manufacturer, some common aspects typically included in ASGS design guidelines are:
- Material Specifications: Define the required properties of the ASGS material, such as thermal expansion coefficient, electrical insulation properties, optical transparency, and chemical resistance.
- Dimensional Tolerances: Specify the acceptable variations in dimensions, thickness, and flatness of the ASGS substrate to ensure compatibility with the manufacturing processes and device requirements.
- Surface Finish Requirements: Outline the surface quality standards, including smoothness, roughness, and cleanliness, to facilitate proper bonding, deposition, and patterning processes during device fabrication.
- Alignment and Registration: Define alignment marks and registration features to ensure accurate positioning and alignment of layers, patterns, and components during fabrication processes such as lithography and etching.
- Heat Dissipation and Thermal Management: Provide guidelines for optimizing the design of the ASGS substrate to enhance heat dissipation and thermal stability, crucial for high-performance semiconductor devices.
- Electrical Connectivity: Specify requirements for integrating electrical interconnects, vias, and bonding pads on the ASGS substrate to facilitate electrical connections and signal routing within the semiconductor device.
- Packaging Considerations: Address packaging requirements and considerations to ensure compatibility with assembly processes, reliability standards, and environmental conditions.
- Testing and Quality Control:Define testing procedures, criteria, and acceptance criteria to evaluate the quality, reliability, and performance of ASGS-based semiconductor devices.
- Compatibility with Manufacturing Processes: Ensure that the ASGS design is compatible with the specific manufacturing processes, equipment, and technologies used in semiconductor fabrication facilities.
- Cost-effectiveness and Scalability: Consider cost-effectiveness and scalability factors in the ASGS design to enable efficient mass production and commercialization of semiconductor devices.
By adhering to these ASGS design guidelines, semiconductor designers and manufacturers can optimize the performance, reliability, and manufacturability of devices using advanced semiconductor glass substrates.
What is the ASGS Fabrication Process?
The ASGS (Advanced Semiconductor Glass Substrates) fabrication process involves several steps to transform raw glass material into finished substrates suitable for use in semiconductor device manufacturing. While specific fabrication processes may vary depending on the desired substrate characteristics and manufacturer’s capabilities, the following are general steps typically involved in ASGS fabrication:
- Raw Material Selection: High-purity glass materials with specific properties tailored to semiconductor applications are selected as the starting material. These glasses often have low thermal expansion coefficients, excellent optical transparency, and superior mechanical properties.
- Glass Forming: The selected glass material is melted in a high-temperature furnace to form a molten glass batch. The molten glass is then shaped into the desired form, typically through processes such as rolling, pressing, or drawing, to achieve the desired substrate thickness and dimensions.
- Surface Preparation: The surfaces of the glass substrates are cleaned and polished to remove any contaminants, imperfections, or roughness that could affect subsequent processing steps or device performance. This step is crucial for ensuring good adhesion and uniformity in subsequent deposition processes.
- Pattern Definition: In some cases, patterns or features may be defined on the glass substrates using techniques such as photolithography, where a photosensitive resist material is applied to the substrate surface, exposed to UV light through a mask, and developed to create the desired pattern.
- Deposition Processes: Thin film deposition techniques are used to deposit various semiconductor materials, such as silicon, silicon dioxide, or metal layers, onto the glass substrates. Common deposition methods include physical vapor deposition (PVD), chemical vapor deposition (CVD), sputtering, and evaporation.
- Etching and Patterning: Etching processes, such as wet etching or plasma etching, are employed to selectively remove material from the deposited layers, defining patterns and features according to the device design. Photolithography masks may be used to protect certain areas from etching.
- Doping and Annealing: Dopants may be introduced into the semiconductor layers through processes such as ion implantation or diffusion to modify their electrical properties. Annealing steps are often performed to activate dopants and improve the crystalline structure of the semiconductor layers.
- Surface Passivation: Surface passivation layers, typically made of materials like silicon nitride or silicon oxide, are deposited onto the semiconductor layers to protect them from contamination, moisture, and electrical leakage.
- Final Inspection and Testing: Finished ASGS substrates undergo rigorous inspection and testing to ensure they meet the required specifications for dimensional accuracy, electrical performance, optical properties, and reliability.
- Packaging and Shipping: Once inspected and approved, the ASGS substrates are packaged securely to protect them during transport and storage before being shipped to semiconductor device manufacturers for further processing.
Overall, the ASGS fabrication process requires precise control and optimization of various parameters to produce substrates with the desired properties and performance characteristics for use in semiconductor device manufacturing.
How do you manufacture ASGS?
Manufacturing Advanced Semiconductor Glass Substrates (ASGS) involves a series of intricate processes aimed at creating high-quality glass substrates tailored for semiconductor device fabrication. Below are the key steps involved in manufacturing ASGS:
- Raw Material Selection: High-purity raw materials are chosen based on the desired properties of the final glass substrate. These materials typically include silica (SiO2), boron oxide (B2O3), sodium oxide (Na2O), and other additives to achieve specific characteristics such as low thermal expansion coefficient, high optical transparency, and excellent chemical resistance.
- Batch Preparation: The raw materials are carefully weighed and mixed to create a homogeneous glass batch. This batch is then melted in a high-temperature furnace, typically operating at temperatures exceeding 1,000 degrees Celsius.
- Glass Forming: The molten glass is shaped into the desired form, usually through techniques like rolling, drawing, or floating. This process helps achieve the desired thickness and dimensions of the glass substrate.
- Surface Treatment: The surfaces of the glass substrates are polished and cleaned to remove any impurities, defects, or surface irregularities. This step is crucial for ensuring proper adhesion and uniformity in subsequent processing steps.
- Doping and Coating: Depending on the application, dopants may be introduced into the glass to modify its properties. Additionally, coatings such as anti-reflective coatings or conductive layers may be deposited onto the glass substrate to enhance its functionality.
- Annealing: The glass substrates undergo an annealing process to relieve internal stresses and improve their mechanical strength and stability. Annealing involves heating the glass to a specific temperature and then slowly cooling it to room temperature.
- Cutting and Shaping: The large glass sheets or ingots are cut into smaller pieces and shaped according to the desired dimensions. Precision cutting techniques ensure uniformity and accuracy in substrate size and shape.
- Quality Control: Throughout the manufacturing process, rigorous quality control measures are implemented to ensure the glass substrates meet the required specifications for dimensional accuracy, surface finish, optical clarity, and other critical parameters.
- Packaging and Shipping: Once the glass substrates pass inspection, they are carefully packaged to protect them from damage during transport and storage. Proper packaging helps maintain the integrity of the substrates until they reach semiconductor device manufacturers for further processing.
By following these manufacturing steps with precision and attention to detail, producers can create ASGS substrates optimized for various semiconductor applications, including integrated circuits, sensors, displays, and photovoltaic devices.
How much should ASGS cost?
The cost of Advanced Semiconductor Glass Substrates (ASGS) can vary depending on several factors including the type of glass used, manufacturing processes involved, substrate size and thickness, surface quality requirements, and volume of production. Additionally, market demand, competition, and supplier pricing strategies also influence the cost of ASGS.
As of my last update in January 2022, specific pricing information for ASGS may not be readily available due to the proprietary nature of pricing models used by manufacturers and suppliers in the semiconductor industry. However, it’s possible to provide some general estimates based on industry trends and considerations:
- Material Costs: The cost of raw materials, including high-purity glass compositions and any dopants or coatings used, plays a significant role in determining the overall cost of ASGS.
- Manufacturing Processes: Complex manufacturing processes such as glass melting, shaping, coating, annealing, and quality control contribute to production costs. Advanced manufacturing techniques or specialized equipment may incur higher operational expenses.
- Quality and Performance: ASGS with superior quality, precision, and advanced features may command higher prices in the market due to increased production costs and added value for semiconductor device manufacturers.
- Economy of Scale: Larger production volumes typically result in lower per-unit costs due to economies of scale. High-volume orders may qualify for bulk discounts or pricing agreements with suppliers.
- Market Dynamics: Supply and demand dynamics, competitive pressures, and industry trends influence pricing strategies adopted by ASGS manufacturers and suppliers. Market conditions and customer requirements may fluctuate over time, affecting pricing levels.
For accurate pricing information, it’s advisable to consult directly with ASGS manufacturers or authorized distributors, as they can provide quotes based on specific requirements, order quantities, and market conditions. Additionally, negotiating pricing terms and exploring potential cost-saving measures may help mitigate the overall cost of ASGS procurement for semiconductor device manufacturing.
What is ASGS base material?
The base material used in Advanced Semiconductor Glass Substrates (ASGS) typically consists of high-purity glass compositions tailored to meet the stringent requirements of semiconductor device fabrication. The specific composition of the base material can vary depending on the desired properties and performance characteristics of the ASGS, as well as the requirements of the semiconductor applications it will be used for.
Common materials used as the base for ASGS include:
- Silica (SiO2): Silica is one of the primary components of glass and is renowned for its excellent optical transparency, thermal stability, and chemical resistance. It serves as the backbone of many ASGS formulations.
- Boron Oxide (B2O3): Boron oxide is often added to glass compositions to lower the glass transition temperature and thermal expansion coefficient, which helps improve the thermal stability and compatibility of ASGS with semiconductor manufacturing processes.
- Sodium Oxide (Na2O): Sodium oxide is another common additive used in glass formulations to modify its properties. It can help lower the melting temperature of glass and improve its workability during the fabrication process.
- Lithium Oxide (Li2O): Lithium oxide is sometimes included in ASGS compositions to further reduce the thermal expansion coefficient and enhance the mechanical strength and durability of the glass substrate.
- Aluminum Oxide (Al2O3): Aluminum oxide can be incorporated into ASGS formulations to increase the glass’s chemical resistance and hardness, making it more suitable for demanding semiconductor applications.
These base materials are carefully selected and combined in precise proportions to achieve the desired characteristics such as low thermal expansion coefficient, high optical transparency, excellent flatness, and chemical inertness required for ASGS used in semiconductor manufacturing. The exact formulation and composition of the base material may vary depending on the specific requirements of the semiconductor devices and the manufacturing processes involved.
Which company makes ASGS?
Currently, there are several companies producing Advanced Semiconductor Glass Substrates (ASGS), some of which are leading global manufacturers of semiconductor materials and equipment. These companies play a significant role in the semiconductor industry through innovative technologies and high-quality products. Our company is one of them, focusing on the research, development, production, and sales of ASGS.
As a manufacturer of ASGS, our company has advanced production facilities and a skilled technical team dedicated to providing high-performance and reliable glass substrate products to meet the needs of customers in the semiconductor device manufacturing field.
The manufacturing process of our ASGS follows strict quality management standards, including:
- Advanced Material Selection: We choose high-purity glass materials and carefully design glass compositions and formulations according to customer requirements and application scenarios to ensure that ASGS has the required excellent performance and characteristics.
- Advanced Manufacturing Processes: We employ advanced manufacturing processes and equipment, including glass melting, shaping, coating, annealing, and more, to ensure that the precision, flatness, and surface quality of ASGS meet the highest standards.
- Strict Quality Control: We implement rigorous quality control measures, including raw material inspection, production process monitoring, and finished product inspection, to ensure the stability and consistency of ASGS quality.
- Customized Services: Our company can customize ASGS according to specific customer requirements, including size, thickness, surface properties, coating selection, etc., to meet the needs of different application scenarios.
As an ASGS manufacturer, we are committed to providing customers with high-quality products and professional services. Our products are widely used in fields such as integrated circuits, display devices, photovoltaic cells, MEMS, etc., providing reliable support and assurance for customer innovation and development.
Feel free to contact us for more information about our company’s ASGS products and customized services. We are dedicated to providing you with the best solutions and achieving win-win cooperation for mutual development!
What are the 7 qualities of good customer service?
Good customer service is essential for maintaining customer satisfaction and loyalty. Here are seven qualities that characterize effective customer service:
- Responsiveness: Responding promptly to customer inquiries, concerns, or issues demonstrates attentiveness and a commitment to meeting customer needs in a timely manner.
- Empathy: Showing empathy involves understanding and acknowledging the customer’s feelings, concerns, and perspectives. Empathetic responses help build rapport and trust with customers, even in challenging situations.
- Clear Communication: Effective communication is key to providing good customer service. Clearly conveying information, instructions, and solutions in a polite and understandable manner helps prevent misunderstandings and ensures that customers feel informed and valued.
- Problem-solving Skills: Customer service representatives should possess strong problem-solving skills to address customer issues efficiently and effectively. This involves identifying the root cause of problems, exploring possible solutions, and taking appropriate actions to resolve issues to the customer’s satisfaction.
- Product Knowledge: Having a deep understanding of the company’s products or services enables customer service representatives to provide accurate information, recommendations, and assistance to customers. Knowledgeable staff can better address customer inquiries and guide them towards suitable solutions.
- Professionalism: Maintaining professionalism in interactions with customers is essential for building credibility and trust. This includes being courteous, respectful, and maintaining a positive attitude, even in challenging situations.
- Follow-up and Accountability: Following up with customers to ensure that their needs have been met and addressing any outstanding issues demonstrates commitment to customer satisfaction. Taking ownership of customer concerns and following through on commitments helps build long-term relationships and fosters customer loyalty.
By embodying these qualities, businesses can deliver exceptional customer service experiences that leave a positive impression and contribute to customer retention and loyalty.
FAQs
What is ASGS?
ASGS stands for Advanced Semiconductor Glass Substrates. They are specialized glass materials used in the semiconductor industry for manufacturing electronic components such as integrated circuits (ICs) and microprocessors.
What are the advantages of ASGS?
ASGS offer several advantages over traditional silicon substrates, including better thermal stability, excellent electrical insulation, improved optical properties, and compatibility with advanced manufacturing processes.
What applications are ASGS used for?
ASGS find applications in various semiconductor devices, including integrated circuits (ICs), microprocessors, sensors, photovoltaic cells, MEMS (Micro-Electro-Mechanical Systems), and advanced display technologies such as OLED and MicroLED displays.
How are ASGS manufactured?
The manufacturing process of ASGS involves selecting high-purity glass materials, melting and shaping the glass into substrates, surface treatment, coating, and quality control measures to ensure the substrates meet the required specifications and performance standards.
What are the key properties of ASGS?
Key properties of ASGS include low thermal expansion coefficient, high optical transparency, excellent electrical insulation, good mechanical strength, and compatibility with semiconductor manufacturing processes.
How do ASGS contribute to semiconductor device performance?
ASGS provide a stable and reliable foundation for semiconductor device fabrication, enabling the development of high-performance devices with improved efficiency, reliability, and functionality.
Where can ASGS be sourced?
ASGS can be sourced from specialized manufacturers and suppliers in the semiconductor industry. These companies typically offer a range of ASGS products tailored to meet specific customer requirements and applications.
Are ASGS cost-effective compared to other substrate materials?
The cost of ASGS may vary depending on factors such as material composition, manufacturing processes, and volume of production. While ASGS may have higher initial costs compared to traditional substrates, their performance benefits and compatibility with advanced technologies can contribute to overall cost-effectiveness in semiconductor device manufacturing.