Advanced Glass Substrates Manufacturer
Advanced Glass Substrates Manufacturer,Advanced Glass Substrates (AGS) represent the pinnacle of glass engineering, meticulously crafted to deliver unparalleled performance across a myriad of applications. Engineered with precision and innovation, AGS offers superior optical clarity, exceptional mechanical strength, and precise dimensional accuracy. From cutting-edge display technologies to high-performance optical components, AGS serves as the backbone of advanced electronics, optics, automotive, aerospace, and medical devices. Its versatility knows no bounds, seamlessly integrating into diverse industries where reliability and performance are paramount. AGS is not merely glass; it’s a testament to human ingenuity, pushing the boundaries of what’s possible and unlocking new frontiers in technology. With AGS, the future becomes clearer, brighter, and more attainable, empowering industries to innovate and inspire the world.
What are Advanced Glass Substrates (AGS)?
Advanced Glass Substrates (AGS) are specialized materials used in various industries, particularly in electronics and optics, due to their exceptional properties and versatility. AGS refers to a class of glass substrates that have undergone advanced processing techniques to achieve specific characteristics tailored for demanding applications.
One of the key features of AGS is their high level of precision and uniformity. These substrates are manufactured using advanced manufacturing processes such as chemical vapor deposition (CVD), physical vapor deposition (PVD), or float glass methods, which ensure consistent thickness, smoothness, and optical quality across the substrate surface. This uniformity is crucial for applications where precise optical or electrical performance is required, such as in display technologies, photovoltaics, and semiconductor manufacturing.
AGS also exhibit excellent thermal and mechanical properties, making them highly resistant to thermal shock, mechanical stress, and environmental factors like humidity and corrosion. This resilience makes AGS suitable for use in harsh operating conditions, including automotive displays, aerospace components, and medical devices.
Furthermore, AGS can be engineered with specific optical properties, such as high transparency, low reflectance, and tailored refractive indices, to meet the requirements of specialized optical applications like lenses, mirrors, and waveguides. These optical enhancements enable AGS to play a crucial role in advanced imaging systems, laser technologies, and telecommunications infrastructure.
In addition to their optical and mechanical properties, AGS can also be optimized for electrical conductivity and insulation, depending on the application requirements. This versatility makes AGS suitable for use in electronic devices such as touch panels, OLED displays, and printed circuit boards, where both optical clarity and electrical performance are essential.
Overall, Advanced Glass Substrates represent a cutting-edge class of materials that offer exceptional performance and versatility across a wide range of applications in electronics, optics, and beyond. Their precision engineering, combined with tailored properties, makes them indispensable in various industries where high-performance materials are paramount.
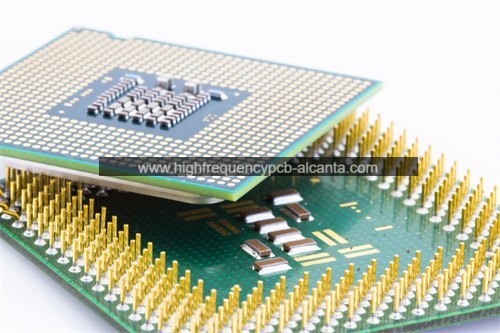
Advanced Glass Substrates Manufacturer
What are the AGS Design Guidelines?
AGS (Advanced Glass Substrates) design guidelines encompass a set of principles and recommendations for the development and implementation of products and systems utilizing AGS. These guidelines typically cover several key aspects to ensure optimal performance, reliability, and manufacturability. While specific design guidelines may vary depending on the application and industry, here are some common considerations:
- Material Selection: Choose the appropriate type of AGS based on the requirements of the application, considering factors such as transparency, thermal properties, mechanical strength, and chemical resistance.
- Dimensional Tolerance: Specify dimensional tolerances for the AGS to ensure compatibility with other components and subsystems in the final product. Tight tolerances may be necessary for precise optical alignment or interfacing with other mechanical parts.
- Surface Quality: Define surface quality requirements, including smoothness, flatness, and absence of defects such as scratches, pits, or bubbles. Surface imperfections can degrade optical performance or affect the integrity of coatings and adhesives.
- Coating Compatibility: Consider the compatibility of AGS with coatings, films, and other surface treatments that may be applied for specific functionalities such as anti-reflection, anti-glare, or scratch resistance. Ensure that the substrate material and coating materials have compatible thermal expansion coefficients to prevent delamination or cracking.
- Thermal Management: Evaluate thermal management requirements to prevent thermal stress-induced failure in AGS-based systems. Design features such as thermal vias, heat spreaders, or integrated cooling solutions may be necessary to dissipate heat effectively and maintain optimal operating temperatures.
- Mechanical Stability: Assess mechanical stability and rigidity requirements to withstand mechanical stress, shock, and vibration during operation, transportation, and handling. Reinforcement techniques such as lamination, bonding, or mechanical mounting may be employed to enhance structural integrity.
- Electrical Properties: Consider electrical properties such as resistivity, dielectric constant, and impedance for applications involving electrical conductivity, insulation, or signal transmission through the AGS. Ensure compatibility with electrical interfaces and circuitry to minimize signal loss or interference.
- Manufacturability: Design AGS-based systems with manufacturability in mind, optimizing for cost-effective production processes, yield, and scalability. Consider factors such as substrate size, thickness, and compatibility with fabrication techniques such as cutting, drilling, polishing, and coating.
- Environmental Compatibility: Assess environmental compatibility and durability requirements, including resistance to moisture, chemicals, UV radiation, and temperature extremes. Choose AGS materials and coatings that exhibit long-term stability and reliability in the intended operating environment.
- Regulatory Compliance: Ensure compliance with relevant industry standards, regulations, and safety requirements applicable to AGS-based products and systems. Conduct thorough testing and validation to demonstrate performance, reliability, and safety under expected operating conditions.
By adhering to these AGS design guidelines, engineers and designers can develop robust and high-performance products and systems that leverage the unique properties of Advanced Glass Substrates across various applications and industries.
What is the AGS Fabrication Process?
The fabrication process of Advanced Glass Substrates (AGS) involves several steps aimed at transforming raw glass materials into finished substrates with tailored properties and specifications. While specific fabrication processes may vary depending on the desired characteristics and application requirements, here is a general overview of the typical steps involved:
- Raw Material Selection: The fabrication process begins with the selection of high-quality raw glass materials. These materials may include various types of glass compositions, each offering specific optical, thermal, mechanical, and chemical properties suitable for different applications.
- Glass Melting: The selected raw materials are melted in a high-temperature furnace to form a homogeneous molten glass mixture. The melting temperature and duration are carefully controlled to achieve the desired glass composition and eliminate impurities.
- Forming: Once the glass is melted and homogenized, it is formed into a continuous ribbon or sheet using one of several techniques, such as the float glass process or the draw-down method. In the float glass process, molten glass is poured onto a bath of molten tin, forming a smooth and uniform sheet as it floats and cools. Alternatively, the draw-down method involves pulling molten glass through rollers to form a thin sheet.
- Annealing: The formed glass sheet undergoes an annealing process to relieve internal stresses and improve mechanical strength and dimensional stability. The glass is slowly cooled in a controlled manner to prevent thermal shock and ensure uniform properties throughout the substrate.
- Cutting and Shaping: The annealed glass sheet is cut into smaller pieces or shaped into specific dimensions according to the desired size and geometry of the final substrate. Precision cutting techniques such as diamond sawing or laser cutting may be employed to achieve tight dimensional tolerances.
- Surface Treatment: Depending on the application requirements, the surfaces of the glass substrates may undergo various treatments to enhance properties such as smoothness, cleanliness, and adhesion. This may involve processes such as polishing, grinding, or chemical etching to remove surface defects and contaminants.
- Coating Deposition: In some cases, thin film coatings or layers may be deposited onto the surfaces of the glass substrates to impart specific optical, electrical, or mechanical properties. Coating techniques such as physical vapor deposition (PVD), chemical vapor deposition (CVD), sputtering, or spin coating may be used to apply thin films of materials such as metals, oxides, or polymers.
- Quality Control: Throughout the fabrication process, rigorous quality control measures are implemented to ensure that the finished AGS substrates meet the required specifications and performance criteria. This may include visual inspection, dimensional measurement, optical characterization, and testing for mechanical strength and durability.
- Packaging and Shipping: Once the AGS substrates have been fabricated and inspected, they are carefully packaged to protect them from damage during transit and storage. Packaging materials may include foam inserts, protective coatings, or specialized containers designed to minimize the risk of breakage or contamination.
By following these fabrication steps and employing advanced manufacturing techniques, AGS manufacturers can produce substrates with precise dimensions, tailored properties, and high quality, suitable for a wide range of applications in industries such as electronics, optics, automotive, aerospace, and more.
How do you manufacture AGS?
Manufacturing Advanced Glass Substrates (AGS) involves a series of sophisticated processes to produce high-quality glass substrates with specific properties tailored to various applications. Here’s a step-by-step overview of the typical manufacturing process for AGS:
- Raw Material Selection: The manufacturing process begins with the selection of raw materials. These materials typically include high-purity silica sand, soda ash, limestone, and other additives depending on the desired glass composition and properties.
- Batching and Mixing: The selected raw materials are carefully measured and mixed in precise proportions according to the desired glass composition. This mixture, known as batch, is then fed into a furnace for melting.
- Melting: The batch materials are charged into a high-temperature furnace, where they are melted at temperatures exceeding 1500°C (2732°F). The furnace may operate continuously or intermittently depending on the manufacturing setup. During melting, the raw materials fuse together to form a homogeneous molten glass.
- Refining: After melting, the molten glass undergoes a refining process to remove bubbles, stones, and other impurities. This is typically achieved by subjecting the molten glass to controlled stirring or agitation, as well as by adjusting the chemical composition to optimize clarity and homogeneity.
- Forming: Once the glass is refined, it is formed into a continuous sheet or ribbon using one of several techniques, such as the float glass process or the draw method. In the float glass process, the molten glass is poured onto a bath of molten tin, where it floats and spreads out to form a smooth and uniform sheet. Alternatively, the draw method involves pulling the molten glass vertically through rollers to form a thin sheet.
- Annealing: The formed glass sheet undergoes an annealing process to relieve internal stresses and improve mechanical strength and stability. The glass is gradually cooled in a controlled manner to prevent thermal shock and ensure uniform properties throughout the substrate.
- Cutting and Shaping: After annealing, the glass sheet is cut into smaller pieces or shaped into specific dimensions according to the desired size and geometry of the final AGS substrates. Precision cutting techniques such as diamond sawing or laser cutting may be employed to achieve tight dimensional tolerances.
- Surface Treatment:Depending on the application requirements, the surfaces of the glass substrates may undergo various treatments to enhance properties such as smoothness, cleanliness, and adhesion. This may involve processes such as polishing, grinding, or chemical etching to remove surface defects and contaminants.
- Coating Deposition: In some cases, thin film coatings or layers may be deposited onto the surfaces of the glass substrates to impart specific optical, electrical, or mechanical properties. Coating techniques such as physical vapor deposition (PVD), chemical vapor deposition (CVD), sputtering, or spin coating may be used to apply thin films of materials such as metals, oxides, or polymers.
- Quality Control: Throughout the manufacturing process, rigorous quality control measures are implemented to ensure that the finished AGS substrates meet the required specifications and performance criteria. This may include visual inspection, dimensional measurement, optical characterization, and testing for mechanical strength and durability.
- Packaging and Shipping: Once the AGS substrates have been manufactured and inspected, they are carefully packaged to protect them from damage during transit and storage. Packaging materials may include foam inserts, protective coatings, or specialized containers designed to minimize the risk of breakage or contamination.
By following these manufacturing steps and employing advanced techniques and equipment, AGS manufacturers can produce substrates with precise dimensions, tailored properties, and high quality, suitable for a wide range of applications in industries such as electronics, optics, automotive, aerospace, and more.
How much should AGS cost?
The cost of Advanced Glass Substrates (AGS) can vary significantly depending on various factors including the type of glass, manufacturing processes, dimensions, specifications, and the quantity ordered. AGS is often a premium product due to its specialized properties and manufacturing requirements, so it tends to be more expensive compared to standard glass substrates.
Here are some factors that can influence the cost of AGS:
- Type of Glass: Different types of glass compositions have different costs associated with raw materials and manufacturing processes. Specialty glasses with unique properties may command higher prices compared to standard soda-lime glass.
- Manufacturing Processes: The complexity of the manufacturing processes involved in producing AGS can impact the cost. Processes such as precision cutting, polishing, coating deposition, and quality control measures contribute to the overall manufacturing cost.
- Size and Thickness: The dimensions and thickness of the AGS substrates can affect the cost. Larger or thicker substrates may require more material and processing time, resulting in higher costs.
- Specifications and Customization: AGS can be customized to meet specific requirements such as optical clarity, surface smoothness, thermal properties, and electrical conductivity. Customization often involves additional processing steps or specialized materials, which can increase the cost.
- Volume and Order Quantity: Volume discounts may be available for larger orders of AGS substrates. Ordering in bulk quantities can help reduce the cost per unit due to economies of scale and efficiency gains in manufacturing.
- Quality and Certification:AGS substrates manufactured to meet stringent quality standards and certifications may command higher prices due to the additional testing, validation, and quality assurance processes involved.
- Packaging and Shipping: Additional costs associated with packaging, handling, and shipping may also contribute to the overall cost of AGS, especially for orders requiring special packaging or expedited shipping methods.
Overall, the cost of AGS can vary widely depending on the specific requirements of the application and the level of customization needed. It’s essential for buyers to consider factors such as performance, reliability, and overall value when evaluating the cost of AGS substrates for their projects.
What is AGS base material?
The base material used for Advanced Glass Substrates (AGS) can vary depending on the desired properties and applications. AGS is typically made from various types of glass compositions, each offering unique characteristics suited to different requirements. Some common types of glass used as base materials for AGS include:
- Soda-Lime Glass: Soda-lime glass is one of the most widely used types of glass due to its low cost and versatility. It consists of silica (silicon dioxide), soda (sodium carbonate), and lime (calcium oxide). Soda-lime glass is suitable for a wide range of applications but may not offer the highest levels of optical clarity or thermal stability compared to other types of glass.
- Borosilicate Glass: Borosilicate glass is known for its excellent thermal shock resistance and low coefficient of thermal expansion. It contains silica and boron trioxide as its primary constituents. Borosilicate glass is often used in applications requiring high durability and resistance to temperature fluctuations, such as laboratory glassware, cooking utensils, and high-performance optics.
- Aluminosilicate Glass: Aluminosilicate glass contains silica, alumina (aluminum oxide), and other additives. It offers exceptional mechanical strength, chemical resistance, and thermal stability, making it suitable for demanding applications in industries such as aerospace, defense, and electronics. Aluminosilicate glass is often used in AGS for its superior strength and durability.
- Quartz Glass: Quartz glass, also known as fused silica, is composed almost entirely of silica (SiO2) and exhibits excellent optical transparency, thermal stability, and chemical resistance. Quartz glass is commonly used in high-precision optical components, semiconductor manufacturing, and laboratory equipment where purity and performance are critical.
- Specialty Glasses: Specialty glasses with tailored compositions and properties are also used as base materials for AGS in certain applications. These glasses may include doped glasses for specific optical or electrical properties, ultra-low expansion glasses for precision optics, or lead-free glasses for environmental sustainability.
The choice of base material for AGS depends on factors such as optical clarity, thermal stability, mechanical strength, chemical resistance, and cost considerations. By selecting the appropriate base material and optimizing the manufacturing process, AGS manufacturers can produce substrates with tailored properties to meet the requirements of diverse applications in industries such as electronics, optics, automotive, aerospace, and more.
Which company manufactures AGS?
Currently, there are many companies globally manufacturing Advanced Glass Substrates (AGS), with some focusing on specific industries or applications while others offer a wide range of product portfolios to meet diverse customer needs. Some well-known AGS manufacturers include Corning, Schott, Asahi Glass Co. (AGC), Nippon Electric Glass (NEG), Ohara Corporation, among others. These companies possess advanced technologies and equipment to produce AGS with excellent performance and quality, widely applied in industries such as electronics, optics, automotive, aerospace, and more.
Our company is also a manufacturer specializing in high-performance glass, with the capability to produce AGS. We have advanced production equipment and a skilled technical team dedicated to providing customized AGS solutions for our customers. Our manufacturing process covers various stages from raw material selection to finished product quality control, ensuring the production of high-quality AGS products that meet customer requirements and industry standards.
As an AGS manufacturer, our advantages include:
- Customization Capability: We can customize AGS according to specific customer requirements, including dimensions, shapes, optical properties, mechanical strength, etc.
- Advanced Technology and Equipment: We possess advanced production equipment and technology to achieve high-precision processing and quality coatings, ensuring the production of AGS products with excellent performance.
- Quality Control: We strictly control every aspect of the production process and utilize advanced quality inspection equipment and techniques to ensure that each batch of products meets customer requirements and industry standards.
- Professional Team: We have an experienced and skilled team capable of providing customers with professional technical support and solutions.
In summary, as an AGS manufacturer, we are committed to providing customers with high-performance, high-quality customized AGS products to meet the needs of various industries and applications. We will continue to enhance our technical capabilities and production capacity to provide customers with better products and services.
What are the 7 qualities of good customer service?
Good customer service is essential for building strong customer relationships and fostering loyalty. Here are seven qualities that characterize excellent customer service:
- Responsiveness: Good customer service involves being prompt and responsive to customer inquiries, requests, and concerns. Responding quickly to customer needs demonstrates attentiveness and shows that their satisfaction is a priority.
- Empathy:Empathy is the ability to understand and relate to the feelings and experiences of customers. Good customer service representatives demonstrate empathy by listening actively, showing understanding, and expressing genuine concern for the customer’s situation.
- Clarity and Communication Skills: Effective communication is crucial in customer service. Good customer service representatives communicate clearly and effectively, using language that is easy to understand and avoiding jargon or technical terms. They also actively listen to customers, ask clarifying questions, and provide relevant information or solutions.
- Problem-Solving Skills:Good customer service involves being proactive and resourceful in addressing customer issues and resolving problems. Customer service representatives should be able to analyze problems, identify root causes, and implement effective solutions to meet customer needs and expectations.
- Professionalism:Professionalism encompasses qualities such as courtesy, respect, and integrity. Good customer service representatives maintain a positive and professional demeanor at all times, regardless of the situation. They treat customers with respect, address their concerns with tact and diplomacy, and uphold ethical standards in their interactions.
- Product Knowledge: Good customer service requires a thorough understanding of the products or services being offered. Customer service representatives should possess comprehensive product knowledge to provide accurate information, answer questions, and offer relevant recommendations or solutions to customers.
- Follow-Up and Follow-Through: Excellent customer service doesn’t end with the initial interaction. Good customer service representatives follow up with customers to ensure that their needs have been met satisfactorily and that any issues have been resolved to their satisfaction. They also follow through on promises or commitments made during the interaction, demonstrating reliability and accountability.
By embodying these qualities, businesses can deliver exceptional customer service experiences that leave a positive impression on customers and contribute to long-term relationships and loyalty.
FAQs
What are Advanced Glass Substrates (AGS)?
AGS refers to specialized glass substrates that have undergone advanced manufacturing processes to achieve specific properties tailored for demanding applications in industries such as electronics, optics, automotive, and aerospace.
What are the applications of AGS?
AGS are used in a wide range of applications, including display technologies (LCD, OLED), photovoltaics (solar panels), semiconductor manufacturing, optical components (lenses, mirrors), automotive displays, aerospace components, medical devices, and more.
What are the advantages of AGS over standard glass substrates?
AGS offer several advantages over standard glass substrates, including higher precision, uniformity, optical clarity, thermal stability, mechanical strength, and chemical resistance. These properties make AGS ideal for applications requiring superior performance and reliability.
What types of glass are used to manufacture AGS?
Various types of glass compositions can be used as base materials for AGS, including soda-lime glass, borosilicate glass, aluminosilicate glass, quartz glass, and specialty glasses with tailored properties for specific applications.
What are the fabrication processes involved in manufacturing AGS?
The fabrication process of AGS typically includes steps such as raw material selection, glass melting, forming (e.g., float glass process), annealing, cutting and shaping, surface treatment, coating deposition (optional), quality control, and packaging.
What factors affect the cost of AGS?
The cost of AGS can vary depending on factors such as the type of glass, manufacturing processes, dimensions, specifications, order quantity, customization requirements, quality standards, and shipping logistics.
Where can AGS be purchased?
AGS can be purchased from specialized glass manufacturers, suppliers, or distributors that offer custom fabrication services tailored to specific customer requirements. Major glass manufacturers and suppliers may also provide AGS as part of their product portfolio.
What are the environmental and safety considerations associated with AGS?
AGS manufacturers strive to adhere to environmental regulations and safety standards in the production process. Depending on the composition and coatings used, AGS may have specific disposal or recycling requirements to minimize environmental impact.