Advanced Glass Package Substrates Manufacturer
Advanced Glass Package Substrates Manufacturer,Advanced Glass Package Substrates (AGPS) revolutionize electronic packaging with superior thermal conductivity, electrical insulation, and dimensional stability. Crafted from borosilicate or quartz glass, AGPS offers miniaturization and compatibility with advanced manufacturing processes. Ideal for microelectronics and optoelectronics, AGPS ensures reliable heat dissipation and signal integrity. Its design guidelines emphasize material selection, interconnection layout, and thermal management for optimal performance. Leading manufacturers like Corning and Schott employ cutting-edge fabrication techniques to produce high-quality AGPS, driving innovation in modern electronic systems.
What is an Advanced Glass Package Substrate (AGPS)?
An Advanced Glass Package Substrate (AGPS) is a specialized type of substrate used in electronic packaging, particularly in the semiconductor industry. It serves as a foundation or base for mounting and interconnecting various electronic components such as integrated circuits (ICs), chips, and other microelectronic devices.
AGPS typically consists of a glass material that offers several advantages over traditional substrates like ceramic or organic materials. Some benefits of AGPS include:
- Thermal Performance: Glass substrates often have superior thermal conductivity compared to other materials, allowing for efficient heat dissipation from the electronic components.
- Electrical Properties: Glass substrates can be engineered to provide excellent electrical insulation, preventing signal interference and crosstalk between components.
- Dimensional Stability:Glass exhibits low coefficients of thermal expansion, meaning it maintains its shape and size over a wide range of temperatures, ensuring the reliability and longevity of the electronic package.
- Miniaturization: AGPS can enable the design of smaller and more compact electronic devices due to its excellent dimensional stability and high-density interconnection capabilities.
- Compatibility with Advanced Manufacturing Processes: Glass substrates can be manufactured using advanced fabrication techniques such as laser micromachining, photolithography, and thin-film deposition, allowing for the integration of complex features and functionalities.
Overall, AGPS represents a significant advancement in electronic packaging technology, offering improved performance, reliability, and manufacturability for a wide range of applications, including microelectronics, optoelectronics, and photonics.
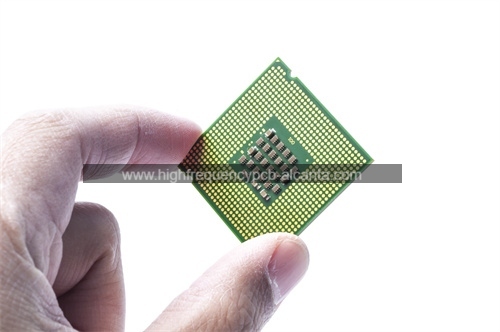
Advanced Glass Package Substrates Manufacturer
What are the AGPS Design Guidelines?
Design guidelines for Advanced Glass Package Substrates (AGPS) vary depending on the specific application, desired performance characteristics, and manufacturing capabilities. However, some common guidelines include:
- Material Selection: Choose a glass material with suitable properties for the intended application, such as thermal conductivity, electrical insulation, coefficient of thermal expansion (CTE), and mechanical strength.
- Substrate Dimensions: Determine the size and thickness of the AGPS based on the dimensions of the electronic components to be mounted, as well as considerations for thermal management and mechanical stability.
- Interconnection Layout: Design the layout of interconnects (such as vias, traces, and pads) to ensure reliable electrical connections between the electronic components and minimize signal interference and crosstalk.
- Thermal Management: Incorporate features such as thermal vias, heat spreaders, and thermal pads to facilitate efficient heat dissipation from the electronic components and maintain optimal operating temperatures.
- Package Integration: Consider the integration of additional components, such as passive components (resistors, capacitors) or active components (sensors, actuators), into the AGPS design to enhance functionality and performance.
- Manufacturability:Optimize the AGPS design for manufacturability by considering factors such as process compatibility, yield, scalability, and cost-effectiveness.
- Reliability and Durability: Ensure that the AGPS design meets reliability and durability requirements for the intended application, including resistance to mechanical stress, thermal cycling, moisture ingress, and other environmental factors.
- Electromagnetic Compatibility (EMC): Implement design features to mitigate electromagnetic interference (EMI) and ensure compliance with EMC standards and regulations.
- Testing and Quality Control: Develop testing procedures and quality control measures to verify the performance and reliability of AGPS prototypes and mass-produced units.
- Documentation and Standards Compliance: Document the AGPS design specifications, fabrication processes, and performance characteristics in accordance with industry standards and regulatory requirements.
By following these design guidelines, engineers and designers can develop AGPS solutions that meet the demanding requirements of modern electronic systems while leveraging the benefits of glass substrates for improved performance, reliability, and manufacturability.
What is the AGPS Fabrication Process?
The fabrication process for Advanced Glass Package Substrates (AGPS) involves several steps, including substrate preparation, patterning, deposition, and packaging. Here’s a general overview of the typical AGPS fabrication process:
- Substrate Selection: Choose a glass material with suitable properties for the intended application, such as thermal conductivity, electrical insulation, CTE, and mechanical strength. The glass substrate is typically made of materials like borosilicate glass or quartz.
- Cleaning and Preparation: Clean the glass substrate thoroughly to remove any contaminants or impurities that could affect subsequent processing steps. Surface treatment techniques such as plasma cleaning or chemical etching may be employed to improve adhesion and surface properties.
- Patterning: Use photolithography or other patterning techniques to define the layout of interconnects, vias, and other features on the glass substrate. A photoresist material is applied to the substrate, exposed to UV light through a mask, and developed to create the desired pattern.
- Etching: Etch away the exposed areas of the glass substrate using wet or dry etching processes. Etching creates cavities or trenches in the glass substrate to form interconnects, vias, and other features according to the pattern defined in the previous step.
- Thin-Film Deposition: Deposit thin-film layers of conductive materials (such as metals like copper, gold, or aluminum) onto the glass substrate using techniques like sputtering, evaporation, or electroplating. These thin-film layers form the conductive traces, pads, and metallization layers required for electrical interconnection.
- Die Attachment and Wire Bonding: Mount the electronic components (such as integrated circuits, chips, and sensors) onto the glass substrate using die attach materials (such as epoxy adhesives or solder). Connect the electronic components to the substrate’s conductive traces using wire bonding or flip-chip bonding techniques.
- Encapsulation and Packaging: Encapsulate the assembled AGPS with protective materials (such as epoxy molding compounds or underfill materials) to provide mechanical support, environmental protection, and insulation. The encapsulated AGPS may be further packaged into a housing or module for additional protection and integration into electronic systems.
- Testing and Quality Control: Perform electrical, mechanical, thermal, and reliability testing on the fabricated AGPS to ensure that it meets the specified performance requirements and quality standards. This may include tests for electrical continuity, insulation resistance, thermal conductivity, and environmental durability.
- Final Inspection and Packaging:Inspect the fabricated AGPS for defects, inconsistencies, or failures using visual inspection, automated testing equipment, or other inspection techniques. Package the validated AGPS units into trays, tubes, or reels for shipment to customers or assembly into final electronic products.
By following these fabrication steps and incorporating advanced manufacturing techniques and quality control measures, manufacturers can produce high-performance AGPS solutions with superior reliability, functionality, and manufacturability for a wide range of electronic applications.
How do you manufacture AGPS?
Manufacturing Advanced Glass Package Substrates (AGPS) involves a series of intricate processes that demand precision, cleanliness, and adherence to stringent quality standards. Here’s an expanded overview of the typical AGPS manufacturing process, elaborating on each step:
- Substrate Selection and Cleaning:High-quality glass substrates, often borosilicate glass or quartz, are selected based on specific application requirements. These substrates undergo thorough cleaning processes to remove contaminants and ensure a pristine surface for subsequent processing steps.
- Surface Preparation: Surface treatment techniques like plasma cleaning or chemical etching are employed to enhance surface properties, promote adhesion, and create a conducive environment for subsequent patterning and deposition processes.
- Patterning:Utilizing photolithography or similar techniques, a photoresist material is applied to the substrate surface. Through exposure to UV light via a photomask, the resist is selectively exposed, creating a pattern that defines the layout of interconnects, vias, and other features.
- Etching: The exposed areas of the substrate are etched away using wet or dry etching processes, creating cavities or trenches as per the defined pattern. This step forms the foundation for the subsequent deposition of conductive materials.
- Thin-Film Deposition: Thin-film layers of conductive materials, such as copper, gold, or aluminum, are deposited onto the substrate using techniques like sputtering, evaporation, or electroplating. These layers form the conductive traces, pads, and metallization required for electrical interconnection.
- Die Attachment and Wire Bonding: Electronic components like integrated circuits are mounted onto the substrate using die attach materials, such as epoxy adhesives or solder. Wire bonding or flip-chip bonding techniques are then employed to establish electrical connections between the components and the substrate’s conductive traces.
- Encapsulation and Packaging: The assembled AGPS is encapsulated with protective materials, such as epoxy molding compounds or underfill materials. This encapsulation provides mechanical support, environmental protection, and insulation to the components. Optionally, the encapsulated AGPS may undergo further packaging into housings or modules for additional protection and integration into electronic systems.
- Testing and Quality Control: Rigorous testing is conducted to evaluate the electrical, mechanical, thermal, and reliability performance of the fabricated AGPS. This includes tests for electrical continuity, insulation resistance, thermal conductivity, and environmental durability. Any defects or deviations from specifications are identified and addressed through corrective measures.
- Final Inspection and Packaging: The validated AGPS units undergo final inspection to ensure compliance with quality standards and customer requirements. They are then packaged into trays, tubes, or reels for shipment to customers or assembly into final electronic products.
By meticulously following these manufacturing processes and leveraging advanced techniques and quality control measures, manufacturers can produce AGPS solutions that meet the demanding requirements of modern electronic systems while ensuring exceptional reliability, functionality, and manufacturability.
How much should AGPS cost?
The cost of Advanced Glass Package Substrates (AGPS) can vary significantly depending on various factors such as the complexity of the design, the size and thickness of the substrate, the materials used, the manufacturing processes involved, and the volume of production. Here are some key considerations that can influence the cost of AGPS:
- Material Costs:The cost of the glass substrate itself, as well as any additional materials such as conductive metals for thin-film deposition and encapsulation materials, will impact the overall cost of AGPS.
- Manufacturing Processes: Advanced manufacturing processes such as photolithography, thin-film deposition, and precision etching require specialized equipment and expertise, which can contribute to higher manufacturing costs.
- Design Complexity: The complexity of the AGPS design, including the number of layers, density of interconnects, and size of features, can influence manufacturing complexity and, consequently, cost.
- Volume of Production: Economies of scale play a significant role in determining the cost of AGPS. Higher volumes of production generally lead to lower per-unit costs due to efficiencies in manufacturing and materials procurement.
- Quality and Reliability Standards: Meeting stringent quality and reliability standards may require additional testing, inspection, and quality control measures, which can increase manufacturing costs.
- Customization and Specialized Features: Customized AGPS designs or the inclusion of specialized features such as integrated passive components or advanced thermal management solutions may incur additional costs.
- Market Dynamics: Market demand, competition, and industry trends can also influence the pricing of AGPS products.
Given these factors, it’s challenging to provide a specific cost estimate for AGPS without detailed information about the specific requirements and manufacturing parameters. However, it’s essential for businesses to carefully evaluate these factors and work closely with suppliers and manufacturers to optimize costs while ensuring that the AGPS meets the required performance, quality, and reliability standards for their applications.
What is AGPS base material?
The base material used in Advanced Glass Package Substrates (AGPS) is typically a type of glass that possesses specific properties suitable for electronic packaging applications. The choice of base material depends on various factors such as thermal conductivity, electrical insulation, coefficient of thermal expansion (CTE), mechanical strength, and compatibility with manufacturing processes.
Two common types of glass used as base materials for AGPS are:
- Borosilicate Glass: Borosilicate glass is a type of glass composed of silica and boron trioxide. It is known for its low coefficient of thermal expansion, excellent thermal shock resistance, and high chemical durability. These properties make borosilicate glass well-suited for electronic packaging applications where thermal management and reliability are critical.
- Quartz Glass: Quartz glass, also known as fused silica, is a high-purity form of glass composed of silicon dioxide (SiO2). It exhibits exceptional optical transparency, thermal stability, and resistance to high temperatures. Quartz glass is often used in AGPS applications requiring superior thermal performance and compatibility with harsh environmental conditions.
Both borosilicate glass and quartz glass offer advantages for AGPS, but the choice between them depends on the specific requirements of the application, such as thermal management, electrical insulation, and mechanical stability. Additionally, manufacturers may develop proprietary glass formulations tailored to meet the unique needs of AGPS designs and manufacturing processes.
Which companies manufacture AGPS?
Currently, many companies manufacture Advanced Glass Package Substrates (AGPS). These companies include multinational corporations, small and medium-sized enterprises, as well as some specialized in electronic packaging and semiconductor industries. Some well-known multinational corporations such as Corning, Schott, OSRAM, and Dow Corning have rich experience and technical strength in the AGPS field. Additionally, some specialized electronic packaging and semiconductor companies are actively developing and producing AGPS products, such as Taiyo Yuden, Jingmian, Infineon, and Kyocera.
In our company, we have advanced production equipment and a skilled technical team with the essential technologies and experience required for AGPS production. Our production line covers various processes, including glass substrate preparation, surface treatment, pattern definition, thin-film deposition, electronic component packaging, testing, and quality control. We employ advanced processes and a stringent quality management system to ensure the production of high-quality and reliable AGPS products. Moreover, we can customize AGPS products according to customer requirements in terms of specifications, dimensions, and performance, providing personalized solutions to our customers.
Our strengths lie not only in our technical capabilities and production capacity but also in our timely response to customer needs and flexible services. We prioritize communication and collaboration with our customers, striving to provide them with the best products and services, and grow together with them.
What are the 7 qualities of good customer service?
Good customer service is characterized by several key qualities that contribute to positive interactions and relationships between businesses and their customers. Here are seven qualities of good customer service:
- Responsiveness: Good customer service involves promptly addressing customer inquiries, concerns, and requests. Responding in a timely manner demonstrates attentiveness and a commitment to meeting customer needs efficiently.
- Empathy: Empathy involves understanding and acknowledging the customer’s perspective, feelings, and needs. Empathetic customer service representatives listen actively, show compassion, and strive to find solutions that resonate with the customer’s emotions and concerns.
- Clear Communication:Clear communication is essential for conveying information, instructions, and solutions effectively. Good customer service representatives communicate clearly and concisely, using language that is easy to understand and free from ambiguity.
- Problem-solving Skills: Good customer service involves the ability to identify and resolve customer issues and problems effectively. Customer service representatives should be resourceful, proactive, and capable of offering practical solutions that address the root cause of the problem.
- Professionalism: Professionalism encompasses maintaining a courteous and respectful demeanor at all times, regardless of the situation or customer behavior. Good customer service representatives exhibit professionalism through their tone of voice, body language, and interactions with customers.
- Flexibility: Good customer service requires adaptability and flexibility to accommodate customer preferences, requests, and changing circumstances. Customer service representatives should be willing to adjust their approach and offer personalized solutions that meet the unique needs of each customer.
- Follow-up and Feedback: Good customer service extends beyond the initial interaction to include follow-up and feedback mechanisms. Following up with customers after resolving an issue or fulfilling a request demonstrates commitment and ensures customer satisfaction. Additionally, soliciting feedback from customers allows businesses to gather valuable insights and continuously improve their service delivery.
By embodying these qualities, businesses can cultivate positive customer experiences, build trust and loyalty, and differentiate themselves in the competitive marketplace.
FAQs
What are the advantages of AGPS?
AGPS offers advantages such as superior thermal performance, excellent electrical insulation, dimensional stability, miniaturization capabilities, and compatibility with advanced manufacturing processes.
What are the typical applications of AGPS?
AGPS is commonly used in microelectronics, optoelectronics, photonics, and other high-performance electronic devices requiring reliable and efficient packaging solutions.
What types of glass are used in AGPS?
Borosilicate glass and quartz glass are commonly used as base materials for AGPS due to their desirable properties such as thermal stability, low coefficient of thermal expansion, and mechanical strength.
How is AGPS manufactured?
The manufacturing process for AGPS involves steps such as substrate preparation, patterning, thin-film deposition, die attachment, encapsulation, testing, and quality control. Advanced fabrication techniques such as photolithography and thin-film deposition are employed.
What are the design guidelines for AGPS?
Design guidelines for AGPS include considerations such as material selection, substrate dimensions, interconnection layout, thermal management, package integration, manufacturability, reliability, and compliance with standards.
Who are the manufacturers of AGPS?
Several companies, including multinational corporations and specialized electronic packaging firms, manufacture AGPS. Some well-known manufacturers include Corning, Schott, OSRAM, Dow Corning, Taiyo Yuden, and Infineon.
What are the cost factors for AGPS?
The cost of AGPS depends on factors such as material costs, manufacturing processes, design complexity, volume of production, quality and reliability standards, customization, and market dynamics.