Advanced BT BGA Substrates Manufacturer
Advanced BT BGA Substrates Manufacturer,Advanced BT BGA substrates are cutting-edge components used in electronic packaging, renowned for their exceptional thermal performance, reliability, and signal integrity. These substrates leverage bismaleimide triazine (BT) resin, renowned for its high glass transition temperature (Tg) and low coefficient of thermal expansion (CTE), ensuring stable operation under challenging conditions. Reinforced with high-quality fibers, BT substrates offer excellent mechanical strength and durability. Their multilayer design accommodates complex circuitry, providing ample space for signal routing and power distribution. With precision manufacturing processes such as laser drilling and advanced surface finishes like electroless nickel immersion gold (ENIG), BT BGA substrates ensure reliable solderability and robust electrical connections. Ideal for high-frequency applications in telecommunications, automotive, aerospace, and consumer electronics, these substrates meet the demands of modern electronic systems, delivering outstanding performance and longevity.
What is an Advanced BT BGA Substrate?
An Advanced BT (Bismaleimide Triazine) BGA (Ball Grid Array) Substrate is a sophisticated component used in electronic packaging. It’s a type of substrate material designed to provide high performance and reliability in semiconductor packaging applications. The term “Advanced BT” refers to the specific composition of the substrate material, which typically consists of a combination of bismaleimide and triazine resins.
These substrates offer several advantages over traditional materials. They have excellent thermal stability, which is crucial for handling the heat generated by modern semiconductor devices. This stability helps prevent warping or delamination of the substrate during the manufacturing process or under operating conditions. Additionally, Advanced BT substrates have low coefficients of thermal expansion (CTE), meaning they expand and contract minimally when exposed to temperature variations, reducing the risk of mechanical stress on the integrated circuits mounted on them.
Furthermore, Advanced BT BGA substrates often feature enhanced electrical properties, such as low signal loss and improved signal integrity, making them suitable for high-speed and high-frequency applications. They also exhibit good mechanical strength, allowing them to withstand the rigors of assembly, testing, and use.
In summary, an Advanced BT BGA Substrate represents a cutting-edge solution for semiconductor packaging, offering superior thermal, electrical, and mechanical properties compared to traditional materials. Its adoption can lead to more reliable and high-performance electronic products.
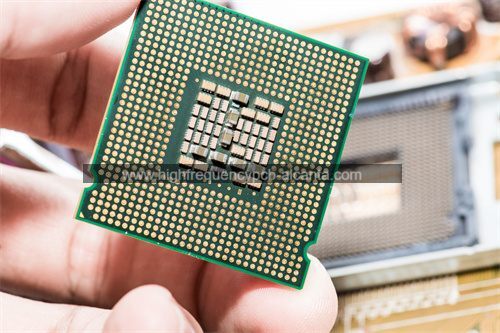
Advanced BT BGA Substrates Manufacturer
What are the Advanced BT BGA Substrate Design Guidelines?
Designing with Advanced BT BGA substrates involves adhering to specific guidelines to ensure optimal performance and reliability. Here are some key design considerations:
- Thermal Management: Advanced BT substrates have excellent thermal stability, but effective thermal management is still essential. Design your layout to facilitate efficient heat dissipation, ensuring that hot spots are minimized and thermal gradients across the substrate are controlled.
- Routing and Signal Integrity: Follow best practices for high-speed signal routing to maintain signal integrity. Minimize signal crosstalk, impedance mismatches, and transmission line effects. Pay attention to signal return paths and minimize vias to reduce signal discontinuities.
- Power Distribution: Design robust power distribution networks to ensure consistent and stable power delivery to the integrated circuits. Use multiple power and ground planes to minimize voltage drops and noise.
- Component Placement: Carefully place components on the substrate to minimize signal path lengths, reduce parasitic effects, and optimize thermal performance. Consider the location of critical components, such as high-speed interfaces and power delivery components.
- Pad and Via Design: Optimize pad and via designs to minimize impedance discontinuities and facilitate reliable connections. Use appropriate pad and via sizes, shapes, and spacing to meet electrical and manufacturing requirements.
- Manufacturability: Design with manufacturability in mind, considering the capabilities and limitations of the fabrication processes used for Advanced BT substrates. Ensure that the design is compatible with manufacturing processes such as drilling, plating, and solder mask application.
- Reliability: Design for reliability by considering factors such as mechanical stress, thermal cycling, and environmental conditions. Ensure that the design can withstand the rigors of assembly, testing, and use over the product’s lifecycle.
- Documentation: Provide comprehensive documentation detailing the design guidelines, constraints, and specifications for the Advanced BT BGA substrate. This information is crucial for ensuring consistent and accurate manufacturing and assembly.
By following these design guidelines, you can leverage the capabilities of Advanced BT BGA substrates to create high-performance and reliable electronic systems.
What is the Advanced BT BGA Substrate Fabrication Process?
The fabrication process for Advanced BT (Bismaleimide Triazine) BGA (Ball Grid Array) substrates involves several steps to create the intricate layers and patterns required for high-performance semiconductor packaging. Here’s an overview of the typical fabrication process:
- Substrate Preparation:The process begins with the preparation of the base substrate material, which is usually a composite laminate consisting of layers of BT resin and reinforcing materials such as fiberglass or polyimide. The substrate material is typically supplied in large sheets or panels.
- Layer Stacking: Multiple layers of substrate material are stacked together to form a multi-layered structure. Each layer may have different properties, such as signal routing, power distribution, or ground planes. Alignment is critical during this step to ensure precise registration of features across the layers.
- Drilling: Small holes, or vias, are drilled through the stacked substrate layers at specific locations where electrical connections are needed between different layers. These vias will later be filled with conductive material to create inter-layer connections.
- Electroplating: After drilling, the vias are plated with a conductive material, typically copper, to establish electrical continuity between the layers. Electroplating ensures that the vias have a uniform and reliable conductive coating.
- Lamination:The stacked and plated substrate layers undergo lamination under heat and pressure. This process bonds the layers together permanently, forming a solid composite structure. The lamination process also helps to remove any air voids and ensure good adhesion between the layers.
- Circuit Patterning: Photolithography and etching processes are used to define the circuit patterns on the substrate layers. A photoresist material is applied to the substrate surface, exposed to UV light through a photomask containing the desired circuit pattern, and then developed to remove the unexposed areas. The exposed substrate is then etched to remove the underlying material, leaving behind the circuit traces and features.
- Surface Finishing: The substrate surface is finished to prepare it for component attachment. This may involve applying solder mask and surface finish materials such as solder or gold to provide protection, facilitate soldering, and ensure good electrical contact.
- Testing and Inspection: The fabricated substrate undergoes rigorous testing and inspection to verify dimensional accuracy, electrical continuity, and reliability. Various testing methods, such as electrical testing, X-ray inspection, and automated optical inspection (AOI), are used to ensure that the substrate meets quality standards.
- Final Processing: After testing and inspection, the fabricated substrate may undergo additional processing steps, such as laser marking, panelization, or packaging, depending on the specific application requirements.
By following these fabrication steps with precision and attention to detail, manufacturers can produce Advanced BT BGA substrates with the high performance and reliability needed for demanding semiconductor packaging applications.
How do you Manufacture an Advanced BT BGA Substrate?
Manufacturing an advanced BT (bismaleimide triazine) BGA (ball grid array) substrate involves several steps and specialized processes. Here’s a general overview of the manufacturing process:
- Material Selection: Choose high-quality BT resin and reinforce it with glass or other suitable fibers to enhance its mechanical and thermal properties.
- Prepreg Production: Prepare prepreg sheets by impregnating the reinforcement material with the BT resin. This can be done using methods like hot pressing or resin infusion.
- Circuit Formation:Print or etch the desired circuit pattern onto the prepreg sheets using methods like screen printing, photolithography, or laser ablation. This creates the conductive traces on the substrate.
- Layer Stacking: Stack multiple prepreg layers together, interleaving them with conductive foil layers as necessary. This forms a multilayer substrate with alternating layers of prepreg and conductive material.
- Lamination: Apply heat and pressure to the stack of prepreg layers to laminate them together. This process melts the resin and bonds the layers into a single solid substrate.
- Drilling and Plating: Drill holes (vias) through the substrate where connections between layers are needed. Plate these vias with conductive material (such as copper) to create electrical connections between layers.
- Surface Finishing: Apply surface finishes to the substrate to protect it from oxidation and improve solderability. Common surface finishes include immersion tin, immersion silver, electroless nickel immersion gold (ENIG), and organic solderability preservatives (OSP).
- Solder Mask Application: Apply a solder mask over the substrate, leaving openings for the solder balls or bumps in the BGA array. The solder mask protects the substrate and defines the soldering areas.
- Solder Ball/Bump Attachment: Attach solder balls or bumps to the substrate using methods like solder ball placement machines or solder paste stenciling followed by reflow soldering.
- Testing and Inspection:Perform electrical testing and visual inspection to ensure the substrate meets quality standards and specifications.
- Packaging and Shipping: Package the substrates securely for transport to customers or assembly facilities.
Throughout the manufacturing process, stringent quality control measures should be implemented to ensure the final product meets the required performance and reliability standards. Advanced manufacturing techniques, such as laser drilling and automated assembly, may also be employed to improve efficiency and precision. Additionally, compliance with relevant industry standards and regulations, such as IPC standards for PCB (printed circuit board) manufacturing, is essential.
How much should an Advanced BT BGA Substrate cost?
The cost of an advanced BT BGA substrate can vary widely depending on several factors, including:
- Materials:The cost of raw materials, including BT resin, reinforcement fibers, conductive materials (such as copper foil), solder mask, surface finishes, and solder balls or bumps, can significantly influence the overall cost.
- Complexity: The complexity of the substrate design, including the number of layers, the density of circuitry, the size and pitch of the BGA array, and the presence of features like blind vias or buried vias, can impact manufacturing costs.
- Manufacturing Process:The manufacturing processes involved, such as circuit formation, lamination, drilling and plating, surface finishing, solder ball attachment, testing, and inspection, contribute to the overall cost. Advanced manufacturing techniques and automation may increase initial investment but can lead to cost savings over time.
- Quality Standards: Meeting stringent quality standards and reliability requirements, such as IPC standards for PCB manufacturing or specific customer specifications, may necessitate additional testing, inspection, and quality assurance measures, affecting costs.
- Volume:Economies of scale typically apply in manufacturing, meaning that higher volumes often result in lower unit costs due to efficiencies in production and procurement. Conversely, lower volumes may incur higher unit costs.
- Supplier Relationships: The relationship between the buyer and the supplier, including factors like negotiation leverage, contractual agreements, and long-term partnerships, can influence pricing.
Without specific details about the substrate’s design, manufacturing requirements, volume, and quality standards, it’s challenging to provide an exact cost. However, advanced BT BGA substrates are generally considered high-end components and can range from tens to hundreds of dollars per unit, especially for custom or specialized applications. Large-scale production runs and standardized designs may yield lower costs per unit compared to small-batch or custom manufacturing. Working closely with suppliers, providing detailed specifications, and exploring various cost-saving strategies can help optimize the overall cost of the substrates.
What is Advanced BT BGA Substrate Base Material?
The base material for an advanced BT (bismaleimide triazine) BGA (ball grid array) substrate typically consists of several layers of prepreg sheets and conductive foil. Here’s a breakdown of the components:
- BT Resin:The primary material in an advanced BT substrate is the bismaleimide triazine (BT) resin. BT resin is chosen for its excellent thermal and mechanical properties, including high glass transition temperature (Tg), low coefficient of thermal expansion (CTE), and good dimensional stability under various operating conditions.
- Reinforcement Fibers: The BT resin is typically reinforced with glass or other suitable fibers to enhance its mechanical strength and dimensional stability. These reinforcement fibers are impregnated with the resin to form prepreg sheets, which are then stacked together to create the substrate.
- Conductive Foil: In multilayer substrates, conductive foil layers, usually made of copper, are interleaved with the prepreg sheets. These foil layers form the conductive traces and signal layers of the substrate. The conductive foil is typically bonded to the prepreg layers during the lamination process.
- Adhesive: Adhesive layers may be used to bond the prepreg sheets and conductive foil layers together during the lamination process. These adhesive layers help ensure strong adhesion between the substrate layers and facilitate the formation of reliable electrical connections.
The combination of these materials forms a robust and reliable substrate for mounting integrated circuits (ICs) in BGA packages. Advanced BT substrates offer excellent thermal performance, high reliability, and precise signal integrity, making them well-suited for demanding applications in industries such as telecommunications, aerospace, automotive, and consumer electronics.
Which Company Makes Advanced BT BGA Substrates?
Some companies have rich experience and expertise in manufacturing advanced BT BGA substrates. Some well-known companies include Hitachi Chemical in Japan, Micron Technology in the United States, Rohm and Haas Electronics Materials in Germany, and Samsung Electronics in South Korea.
As a company specialized in electronic component manufacturing, we possess advanced technology and equipment, with the professional capability to produce advanced BT BGA substrates. Our manufacturing process includes:
- Material Selection and Supply Chain Management: We collaborate with quality suppliers to ensure the use of high-quality BT resin, reinforcement fibers, and industry-standard conductive foil materials.
- Advanced Production Processes: We employ advanced production processes and equipment, including high-precision printing, drilling, copper plating, gold plating, and other process steps to ensure product quality and performance.
- Quality Control and Testing: We strictly adhere to quality control standards, from the inspection of raw materials to the final testing of finished products, ensuring that each stage meets customer requirements and industry standards.
- Customized Services: We can provide customized solutions according to customer needs, including design optimization, process adjustments, and meeting special requirements, to meet the needs of different industries and applications.
As a trusted partner, we are committed to providing customers with high-quality, high-performance Advanced BT BGA substrates. We work collaboratively with customers to explore solutions for mutual benefits. Our professional team is dedicated to providing technical support, customized services, and timely delivery to meet your needs and exceed your expectations.
What are the 7 Qualities of Good Customer Service?
Good customer service is characterized by several key qualities that contribute to a positive customer experience. Here are seven qualities of good customer service:
- Responsiveness: A good customer service team is prompt in addressing customer inquiries, concerns, and requests. They acknowledge customers promptly and provide timely assistance, whether it’s answering questions, resolving issues, or fulfilling requests.
- Empathy: Empathy is essential in understanding and relating to customers’ feelings, concerns, and needs. A good customer service representative listens actively, shows genuine concern for the customer’s situation, and strives to empathize with their perspective.
- Clarity and Communication Skills:Clear communication is crucial for effective customer service. Good customer service representatives communicate clearly and effectively, using language that is easy to understand. They provide accurate information, instructions, and explanations to assist customers efficiently.
- Problem-Solving Skills: Good customer service involves effectively resolving customer problems and addressing their needs. Customer service representatives should be skilled at identifying issues, analyzing situations, and implementing solutions that satisfy the customer and resolve their concerns.
- Professionalism: Professionalism encompasses qualities such as courtesy, respect, and integrity. Good customer service representatives maintain a professional demeanor in their interactions with customers, treating them with respect, courtesy, and fairness at all times.
- Product Knowledge: A good customer service team possesses comprehensive knowledge about the products or services they support. They are well-trained and informed about the features, functions, and benefits of their offerings, enabling them to provide accurate information and guidance to customers.
- Proactivity: Good customer service involves being proactive in anticipating and addressing customer needs before they become problems. Customer service representatives actively seek opportunities to enhance the customer experience, offer assistance, and provide value-added services or recommendations.
By embodying these qualities, businesses can deliver exceptional customer service that fosters loyalty, satisfaction, and positive word-of-mouth referrals.
FAQs
What are the key benefits of using Advanced BT BGA Substrates?
Advanced BT BGA Substrates offer high thermal stability, excellent mechanical strength, and superior electrical performance, making them ideal for high-density and high-speed electronic applications.
How long does it take to manufacture an Advanced BT BGA Substrate?
The manufacturing time can vary, but typically it ranges from a few weeks to a couple of months, depending on the complexity and quantity.
Can you customize Advanced BT BGA Substrates according to specific requirements?
Yes, our company specializes in custom design and manufacturing to meet specific customer requirements.
What testing is performed on Advanced BT BGA Substrates?
We conduct a range of tests, including electrical, thermal, and mechanical testing, to ensure the highest quality and performance of our substrates.
What industries use Advanced BT BGA Substrates?
A: They are used in various industries, including telecommunications, automotive, aerospace, and consumer electronics, where high performance and reliability are critical.