Advanced BT BGA PCB Manufacturer
Advanced BT BGA PCB Manufacturer,Advanced BT BGA PCBs, based on Bismaleimide Triazine (BT) resin, are cutting-edge substrates designed for Ball Grid Array (BGA) packaging applications. These PCBs offer superior thermal and mechanical properties, including high thermal conductivity, low coefficient of thermal expansion (CTE), and excellent electrical insulation. Advanced BT BGA PCBs support high-density interconnects with fine pitch components, ensuring reliable signal transmission and thermal management. They are crucial in modern electronics for their ability to withstand high temperatures and harsh environments, making them suitable for telecommunications, computing, and automotive electronics. These substrates facilitate compact and efficient designs while maintaining high performance and reliability standards.
What is an Advanced BT BGA PCB?
Advanced BT BGA PCB (Advanced Build-up Technology Ball Grid Array Printed Circuit Board) is a high-performance circuit board widely used in modern electronic devices, especially in high-speed and high-density applications. This type of PCB utilizes advanced build-up technology, allowing for complex circuit designs across multiple layers, with lower inductance and resistance characteristics, thereby enhancing signal integrity and transmission speed.
The “BT” in BT BGA PCB stands for “Bismaleimide-Triazine,” a high-temperature, low-dielectric constant resin material known for its excellent thermal stability and chemical resistance. This makes BT BGA PCBs particularly suitable for demanding environments such as high-frequency communications, computing, and consumer electronics.
Compared to traditional FR-4 PCBs, Advanced BT BGA PCBs offer significant performance advantages, including better thermal management and higher signal transmission efficiency. Additionally, the low dielectric constant of BT materials helps reduce signal delay, resulting in more stable high-speed signal transmission.
In the manufacturing process, BT BGA PCBs are typically constructed using multilayer stacking, with precise process control to ensure the quality of connections between layers. This structural design not only enhances the reliability of the PCB but also provides greater flexibility for miniaturized designs.
In summary, Advanced BT BGA PCBs are essential tools for achieving high-performance and high-density designs in the electronics industry, and their applications continue to expand with technological advancements.
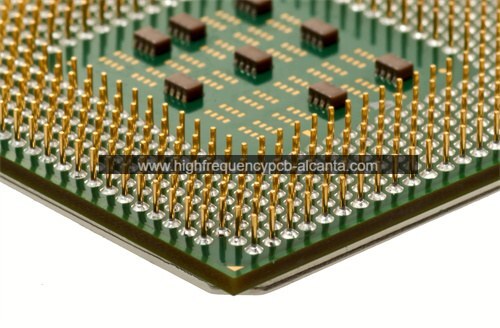
Advanced BT BGA PCB Manufacturer
What are the Design Guidelines for Advanced BT BGA PCB?
Designing Advanced BT BGA PCBs involves specific guidelines to ensure performance, reliability, and manufacturability. Here are some key design guidelines:
- Layer Stackup: Optimize the layer stackup for signal integrity. Use sufficient ground and power planes to minimize noise and improve thermal performance.
- Trace Width and Spacing: Determine appropriate trace widths and spacing based on current carrying capacity and impedance requirements. Follow IPC-2221 standards for guidance.
- Via Design: Utilize microvias for high-density interconnections. Design blind/buried vias as needed to reduce layer count and improve routing efficiency.
- Impedance Control:Maintain controlled impedance for high-speed signals. Calculate and define impedance requirements based on the dielectric materials and trace dimensions.
- Thermal Management:Incorporate thermal relief features and ensure adequate heat dissipation for high-power components. Use thermal vias and consider copper pour for heat spreading.
- Component Placement: Strategically place components to minimize signal path lengths, particularly for high-speed signals. Keep sensitive components away from noisy ones.
- Grounding Practices: Implement solid grounding practices, including ground stitching vias and minimizing ground loop areas to reduce electromagnetic interference (EMI).
- Manufacturability: Consider manufacturability during design. Avoid overly complex geometries and ensure features meet fabrication tolerances.
- DFM and DFT: Engage in Design for Manufacturability (DFM) and Design for Testability (DFT) practices to facilitate easier assembly and testing.
- Simulation and Analysis: Use simulation tools for signal integrity, thermal analysis, and electromagnetic compatibility (EMC) to predict performance before prototyping.
Following these guidelines helps in optimizing the performance of Advanced BT BGA PCBs, ensuring they meet the rigorous demands of modern electronic applications.
What is the Fabrication Process for Advanced BT BGA PCB?
The fabrication process for Advanced BT BGA PCBs involves several key steps, ensuring high performance and reliability. Here’s an overview of the typical process:
- Design and Layout:Begin with the design using specialized PCB design software. This includes defining the layer stackup, component placement, trace routing, and via placements, adhering to design guidelines.
- Material Selection: Choose appropriate BT resin materials with desired dielectric properties for signal integrity and thermal performance.
- Layer Preparation: Start with copper-clad laminates. The layers are prepared by applying a photosensitive coating that will define the circuit patterns.
- Imaging: Expose the coated laminate to ultraviolet (UV) light through a photomask, transferring the circuit pattern onto the surface. This step defines the areas where copper will remain.
- Etching: After developing the imaged layer, the unexposed areas are etched away using chemical solutions, leaving behind the desired copper traces.
- Layer Lamination: Multiple layers are bonded together using heat and pressure. This lamination process is crucial for creating the multilayer structure typical in Advanced BT BGA PCBs.
- Via Formation: Drill holes for vias (through-hole, blind, or buried). These are then plated with copper to create electrical connections between layers.
- Solder Mask Application: A solder mask is applied to protect the copper traces and prevent solder bridges during assembly. This is typically applied through a screen-printing process.
- Surface Finishing: Apply a surface finish (such as ENIG, HASL, or OSP) to enhance solderability and protect the copper pads.
- Testing and Inspection: Perform electrical testing (e.g., flying probe testing) and visual inspection to ensure the PCB meets specifications.
- Assembly: Finally, the PCBs are sent for assembly, where components are mounted using techniques such as surface mount technology (SMT) or through-hole soldering.
These steps together ensure that Advanced BT BGA PCBs are fabricated to meet the high standards required for modern electronics applications.
How do you Manufacture an Advanced BT BGA PCB?
Manufacturing an Advanced BT BGA PCB involves several detailed steps to ensure high quality and performance. Here’s an overview of the manufacturing process:
- Design and Preparation: Utilize specialized PCB design software to create the layout, including trace routing, component placement, and via design. Ensure compliance with design guidelines.
- Material Selection: Choose BT resin materials known for their thermal stability and low dielectric constant, suitable for high-frequency applications.
- Layer Formation: Start with copper-clad laminate sheets. Apply a photosensitive coating to define the circuit patterns.
- Photolithography: Use a photomask to expose the coated laminate to UV light, transferring the design onto the surface.
- Developing: Develop the exposed laminate to remove the unexposed areas, leaving the desired copper traces.
- Etching: Apply chemical etching to remove unwanted copper, revealing the circuit patterns.
- Layer Lamination: Bond multiple layers together through heat and pressure, creating the multilayer structure essential for Advanced BT BGA PCBs.
- Via Drilling: Drill holes for vias, including blind and buried vias, as required. Plate these holes with copper to establish connections between layers.
- Solder Mask Application: Apply a solder mask to protect the copper traces and pads, preventing solder bridging during assembly.
- Surface Finishing: Choose and apply a surface finish (e.g., ENIG, HASL, or OSP) to improve solderability and protect copper pads.
- Electrical Testing: Conduct electrical tests, such as flying probe testing, to verify the integrity of the PCB design.
- Final Inspection: Perform visual inspection and automated optical inspection (AOI) to ensure the PCB meets quality standards.
- Assembly Preparation: Prepare the PCB for assembly by providing necessary documentation and specifications for component placement.
- Assembly: Components are mounted using techniques like surface mount technology (SMT) or through-hole soldering, completing the manufacturing process.
These steps ensure the successful manufacture of Advanced BT BGA PCBs, tailored for high-performance electronic applications.
How much should an Advanced BT BGA PCB cost?
The cost of an Advanced BT BGA PCB can vary significantly based on several factors:
- Layer Count: More layers typically increase costs due to complexity in manufacturing.
- Material Type: BT materials are generally more expensive than standard FR-4 materials, affecting the overall price.
- Complexity: Designs with high-density interconnections, microvias, or intricate layouts can lead to higher manufacturing costs.
- Quantity: Larger production runs often reduce the per-unit cost due to economies of scale.
- Finishing Options: Different surface finishes (like ENIG or OSP) can have varying costs.
- Testing and Inspection: Additional testing requirements can increase the overall cost.
As a rough estimate, Advanced BT BGA PCBs can range from $50 to several hundred dollars per unit, depending on these factors. For precise pricing, it’s best to request quotes from manufacturers based on specific design requirements.
What is the Base Material for Advanced BT BGA PCB?
The base material for Advanced BT BGA PCBs is typically Bismaleimide-Triazine (BT) resin, which is favored for its excellent thermal stability, low dielectric constant, and high-performance characteristics. This material is specifically designed to meet the demands of high-frequency applications, offering superior electrical properties and reliability in harsh environments.
BT materials provide several advantages, including:
- Thermal Stability: Withstand high temperatures without significant degradation, making them suitable for high-performance electronics.
- Low Dielectric Constant: Helps minimize signal loss and delay, which is crucial for high-speed applications.
- Chemical Resistance: Resistant to various chemicals, enhancing durability in different environments.
- Good Mechanical Strength: Provides structural integrity, supporting complex multilayer designs.
These properties make BT resin an ideal choice for the advanced requirements of modern electronic devices, particularly in applications such as telecommunications, computing, and consumer electronics.
Which companies manufacture Advanced BT BGA PCBs?
Several companies manufacture Advanced BT BGA PCBs, including:
- Shin-Etsu Chemical:As a global leader in high-performance materials, Shin-Etsu provides a variety of high-quality BT materials widely used in advanced PCB manufacturing.
- Luxshare Precision: This company enjoys a strong reputation in the electronics manufacturing industry, focusing on providing high-density and high-performance PCB products, including BT BGA PCBs.
- Huihong: Huihong specializes in PCB manufacturing and is committed to offering high-performance BT BGA PCBs to meet diverse application needs.
- AT&S: A leading PCB manufacturer in Europe, AT&S is known for its high technological standards and innovative capabilities, providing multilayer and high-frequency PCB solutions, including Advanced BT BGA PCBs.
- JCET: JCET is a leading semiconductor packaging and testing company in China, dedicated to the research and production of high-performance PCBs, particularly excelling in the BT BGA PCB sector.
Our company also has the capability to produce Advanced BT BGA PCBs, equipped with advanced manufacturing equipment and processes to meet high-performance and high-density PCB demands. We use premium BT resin materials to ensure excellent thermal stability, signal integrity, and chemical resistance in our products.
Our manufacturing process strictly adheres to international standards, with rigorous quality control at every stage, from design and material selection to production, ensuring the reliability and performance of the final products. We also offer customization services to tailor designs and manufacturing to specific customer needs, adapting to various application scenarios.
In high-frequency communications, computing, and consumer electronics, our Advanced BT BGA PCB products have been widely used and received high recognition from customers. Through continuous technological innovation and process optimization, we strive to enhance product quality and service levels, aiming to provide better solutions for our clients.
What are the 7 Qualities of Good Customer Service?
Here are seven qualities of good customer service:
- Responsiveness: Timely and effective responses to customer inquiries or issues demonstrate that the company values its customers and prioritizes their needs.
- Empathy:Understanding and acknowledging customers’ feelings and perspectives helps build a rapport and shows genuine care for their concerns.
- Knowledge: Having well-informed staff who can provide accurate information and guidance enhances customer trust and satisfaction.
- Patience:Dealing with frustrated or confused customers requires patience, ensuring that each customer feels heard and understood without being rushed.
- Clarity: Communicating clearly and concisely, avoiding jargon, helps customers understand solutions and instructions, reducing confusion and frustration.
- Personalization: Tailoring service interactions to individual customer preferences and history creates a more engaging and satisfying experience.
- Follow-Up: Checking in with customers after resolving their issues or inquiries shows commitment to their satisfaction and helps build long-term relationships.
These qualities contribute to a positive customer experience, fostering loyalty and encouraging repeat business.
FAQs
What are the advantages of using BT materials?
BT materials offer excellent thermal stability, low dielectric constant, high mechanical strength, and good chemical resistance, making them suitable for demanding electronic applications.
In which applications are Advanced BT BGA PCBs commonly used?
They are commonly used in telecommunications, computing, consumer electronics, automotive electronics, and other high-frequency and high-speed applications.
How do Advanced BT BGA PCBs differ from traditional FR-4 PCBs?
Advanced BT BGA PCBs provide better thermal management, improved signal integrity, and lower loss at high frequencies compared to traditional FR-4 PCBs, making them more suitable for advanced applications.
What is the typical manufacturing process for Advanced BT BGA PCBs?
The manufacturing process includes design and layout, material selection, layer preparation, photolithography, etching, layer lamination, via drilling, solder mask application, surface finishing, and testing.
What factors influence the cost of Advanced BT BGA PCBs?
Factors include layer count, complexity of the design, material costs, quantity ordered, and any special requirements for testing or finishing.
Can Advanced BT BGA PCBs be customized?
Yes, they can be customized based on specific design requirements, including size, layer count, and component placement, to meet the needs of different applications.
What is the lead time for manufacturing Advanced BT BGA PCBs?
Lead times vary based on complexity and quantity but generally range from a few weeks to a couple of months. It’s best to check with manufacturers for specific timelines.
What quality control measures are in place for Advanced BT BGA PCBs?
Quality control measures typically include electrical testing, visual inspection, and automated optical inspection (AOI) to ensure that the boards meet design specifications and performance standards.