ABF(Ajinomoto) Package Substrate Manufacturer
ABF(Ajinomoto) Package Substrate Manufacturer,ABF Package Substrates, short for Ajinomoto Build-up Film Package Substrates, represent a cutting-edge solution in the realm of semiconductor packaging. Composed of polyimide film layers integrated with thin copper foil, these substrates serve as the backbone for semiconductor devices, offering a blend of high-performance characteristics essential for modern electronics.
Renowned for their exceptional thermal stability, ABF Package Substrates excel in efficiently dissipating heat generated by semiconductor components, ensuring optimal operation even in demanding environments. Moreover, their superior electrical insulation properties facilitate reliable signal transmission, crucial for maintaining the integrity of electronic systems.
ABF Package Substrates cater to a diverse array of applications, spanning from smartphones and tablets to automotive electronics and telecommunications equipment. Their ability to support high-density interconnects and fine-pitch features makes them indispensable in enabling the miniaturization and enhanced functionality of electronic devices.
In essence, ABF Package Substrates embody the convergence of advanced materials and precision engineering, empowering the semiconductor industry to push the boundaries of innovation and deliver next-generation electronic solutions.
What is an ABF (Ajinomoto) Package Substrate?
The ABF (Ajinomoto Build-up Film) package substrate is a type of advanced substrate used in semiconductor packaging. It’s a high-performance material developed by Ajinomoto Fine-Techno Co., Inc. It serves as a crucial component in the construction of semiconductor packages, providing both electrical connectivity and mechanical support.
ABF substrates are typically made of polyimide films with thin layers of copper foil bonded to them. These substrates offer excellent thermal stability, electrical insulation, and mechanical strength, making them suitable for use in a wide range of semiconductor applications, including advanced packaging technologies like flip-chip and chip-on-flex.
The use of ABF substrates allows for miniaturization and higher integration levels in semiconductor devices, which is essential for meeting the demands of modern electronics, such as smartphones, tablets, and other portable gadgets. Additionally, ABF substrates enable high-speed signal transmission and efficient heat dissipation, contributing to the overall performance and reliability of semiconductor packages.
In summary, ABF package substrates play a vital role in the semiconductor industry by providing a reliable foundation for assembling and connecting semiconductor chips, enabling the production of advanced electronic devices with enhanced functionality and performance.
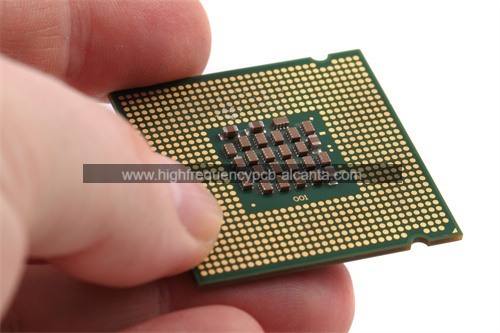
ABF(Ajinomoto) Package Substrate Manufacturer
What are the ABF Package Substrate Design Guidelines?
Design guidelines for ABF (Ajinomoto Build-up Film) package substrates are crucial to ensure the reliability and performance of semiconductor packages. Here are some common design guidelines:
- Layer Stackup:Define the layer stackup including the number of signal layers, power and ground planes, and any additional layers required for specific functionality like impedance control or heat dissipation.
- Dielectric Material Selection: Choose appropriate dielectric materials with suitable electrical, thermal, and mechanical properties to meet the requirements of the application.
- Copper Trace Width and Spacing: Design copper traces with appropriate width and spacing to ensure signal integrity, impedance control, and manufacturability. Consider factors like signal speed, current carrying capacity, and fabrication capabilities.
- Via Design: Optimize via placement and design to minimize signal distortion, reduce crosstalk, and provide efficient power delivery. Use blind and buried vias where necessary to achieve high-density interconnects.
- Thermal Management: Incorporate features like thermal vias, heat sinks, or thermal pads to facilitate heat dissipation from the semiconductor devices mounted on the substrate. Ensure adequate thermal conductivity of the substrate material.
- Component Placement and Routing: Place components strategically to minimize signal path lengths, reduce parasitic effects, and optimize signal integrity. Route critical signals carefully to avoid impedance mismatches, signal coupling, and other signal integrity issues.
- Electrical Performance: Perform simulations and analyses to verify electrical performance parameters such as signal integrity, power distribution, and impedance matching. Ensure compliance with industry standards and specifications.
- Mechanical Durability: Design the substrate to withstand mechanical stresses, including thermal cycling, shock, and vibration, to ensure long-term reliability in various operating conditions.
- Manufacturability: Consider manufacturability aspects such as panelization, registration accuracy, solder mask design, and assembly processes to facilitate efficient fabrication and assembly of the substrate.
- Reliability Testing: Perform thorough reliability testing, including thermal cycling, solder joint reliability, and electrical testing, to validate the design and ensure compliance with reliability requirements.
By following these design guidelines, engineers can develop ABF package substrates that meet the performance, reliability, and manufacturability requirements of semiconductor packaging applications.
What is the ABF Package Substrate Fabrication Process?
The fabrication process for ABF (Ajinomoto Build-up Film) package substrates involves several steps to create the necessary layers and features required for semiconductor packaging. Here’s a general overview of the fabrication process:
- Substrate Preparation: The process begins with the preparation of the base substrate material, typically a polyimide film. The film is cleaned and treated to ensure proper adhesion of subsequent layers.
- Lamination of Copper Foil: Thin layers of copper foil are laminated onto the polyimide film using a combination of heat, pressure, and adhesive materials. These copper layers will serve as the conductive traces and planes in the substrate.
- Photoimaging:A layer of photoresist material is applied onto the copper-clad substrate. A photomask containing the desired circuit patterns is then aligned and exposed onto the photoresist using ultraviolet light. After exposure, the unexposed photoresist is removed, leaving behind the patterned areas for subsequent processing.
- Etching: The exposed copper areas are etched away using chemical etchants, leaving behind the desired copper traces and features defined by the photoresist pattern.
- Dielectric Layer Deposition: Dielectric materials, such as epoxy-based resins or polyimides, are deposited onto the substrate surface to insulate the copper traces and provide additional structural support.
- Via Formation: Via holes are drilled or laser-ablated through the dielectric layers to establish electrical connections between different copper layers. These vias may be filled with conductive materials to enhance electrical conductivity.
- Conductor Plating: Additional layers of copper may be plated onto the substrate surface to build up conductive features or increase the thickness of copper traces.
- Surface Finishing: Surface finishing processes such as solder mask application, surface planarization, and final copper surface treatment are performed to protect the substrate and facilitate subsequent assembly processes.
- Laser Drilling and Routing: Laser drilling may be employed to create fine vias and micro-features in the substrate. Routing processes are used to define the outer dimensions and shape of the substrate.
- Inspection and Testing: The fabricated substrate undergoes rigorous inspection and testing to ensure dimensional accuracy, electrical continuity, and reliability. Various tests, including electrical continuity tests, impedance measurements, and visual inspections, are conducted to verify the quality of the substrate.
- Panelization and Packaging: The individual substrates may be panelized for efficient handling during subsequent assembly processes. Finally, the substrates are packaged and prepared for integration into semiconductor devices.
Overall, the fabrication process for ABF package substrates involves a combination of material deposition, patterning, and assembly techniques to create complex multi-layer structures with high precision and reliability.
How do you manufacture an ABF Package Substrate?
Manufacturing an ABF (Ajinomoto Build-up Film) package substrate involves several key steps, from material selection to final inspection. Here’s a comprehensive overview of the manufacturing process:
- Material Selection: Choose appropriate materials for the substrate, including polyimide film for the base substrate, copper foil for conductive layers, and dielectric materials for insulation and structural support.
- Cleaning and Surface Treatment: Clean the polyimide film to remove any contaminants and treat its surface to ensure proper adhesion of subsequent layers.
- Copper Cladding: Laminate thin layers of copper foil onto the polyimide film using heat, pressure, and adhesives. This forms the conductive layers for the substrate.
- Laser Ablation or Chemical Etching: Use laser ablation or chemical etching techniques to define the circuit patterns on the copper-clad substrate. This involves applying a photoresist, exposing it to a pattern using a photomask, and then removing the exposed or unexposed photoresist to create the desired copper features.
- Dielectric Layer Deposition: Deposit dielectric materials, such as epoxy-based resins or polyimides, onto the substrate surface to insulate the copper traces and provide mechanical support. This can be done using techniques like spin coating, screen printing, or vacuum deposition.
- Via Formation: Create vias (electrical connections between different copper layers) by drilling or laser ablation through the dielectric layers. Optionally, fill the vias with conductive materials like copper to enhance electrical conductivity.
- Conductor Plating: Plate additional layers of copper onto the substrate surface to build up conductive features or increase the thickness of copper traces. This can be done using electroplating or electroless plating processes.
- Surface Finishing: Apply surface finishing processes such as solder mask application, surface planarization, and final copper surface treatment to protect the substrate and facilitate subsequent assembly processes.
- Laser Drilling and Routing: Use laser drilling and routing processes to create fine vias, micro-features, and define the outer dimensions and shape of the substrate.
- Inspection and Testing: Conduct rigorous inspection and testing of the fabricated substrate to ensure dimensional accuracy, electrical continuity, and reliability. Various tests, including electrical continuity tests, impedance measurements, and visual inspections, are performed.
- Panelization and Packaging: Panelize the individual substrates for efficient handling during subsequent assembly processes. Finally, package and prepare the substrates for integration into semiconductor devices.
Throughout the manufacturing process, strict quality control measures are implemented to ensure that the fabricated ABF package substrates meet the required specifications and standards for performance and reliability.
How much should an ABF Package Substrate cost?
The cost of an ABF (Ajinomoto Build-up Film) package substrate can vary significantly depending on various factors such as:
- Size and Complexity: Larger substrates with complex designs or multiple layers will generally cost more to manufacture compared to smaller, simpler substrates.
- Materials:The cost of materials used in the substrate, including polyimide film, copper foil, dielectric materials, and surface finishes, can impact the overall cost. High-performance materials may come at a higher price point.
- Manufacturing Process: The complexity of the manufacturing process, including the number of fabrication steps, level of precision required, and use of specialized equipment, will influence the cost.
- Volume: Economies of scale play a significant role in determining the cost of ABF package substrates. Higher production volumes typically lead to lower per-unit costs due to efficiencies in manufacturing and materials sourcing.
- Supplier and Location: The choice of supplier and their location can affect the cost. Suppliers in regions with lower labor and overhead costs may offer more competitive pricing.
- Customization and Special Requirements: Additional customization, such as specific design features, special surface finishes, or stringent quality control requirements, can increase the cost.
- Market Demand: Fluctuations in market demand and supply chain factors can impact substrate pricing. High demand or supply chain disruptions may lead to price increases.
It’s essential to consider these factors when estimating the cost of ABF package substrates. Prices can range from a few dollars to several hundred dollars per substrate, depending on the specifics of the project. For accurate pricing, it’s recommended to consult with substrate manufacturers or suppliers and provide detailed specifications for the desired substrate.
What is ABF Package Substrate base material?
The base material of an ABF (Ajinomoto Build-up Film) package substrate primarily consists of a high-performance polymer, typically a type of epoxy resin reinforced with glass fibers or a similar material. Here are the key components and characteristics of the base material used in ABF package substrates:
- Epoxy Resin: The core material is usually an epoxy-based resin. Epoxy resins are favored for their excellent electrical insulating properties, chemical resistance, mechanical strength, and thermal stability. These properties are essential for protecting the delicate semiconductor components and maintaining the integrity of the electrical connections.
- Glass Fiber Reinforcement: To enhance the mechanical strength and dimensional stability of the substrate, the epoxy resin is often reinforced with glass fibers. This reinforcement helps the substrate withstand the stresses of thermal cycling, mechanical handling, and the assembly process.
- Build-Up Film Layers:The ABF substrates are characterized by their build-up layers, which are formed by sequentially adding layers of dielectric material and copper foil. These layers are laminated together to create the multilayer structure required for advanced semiconductor packaging. The dielectric layers typically consist of modified epoxy resins, optimized for low dielectric constant and high thermal performance.
- Copper Foil: Thin copper foils are used to form the conductive traces and planes within the substrate. These copper layers are essential for providing electrical connectivity between the semiconductor die and the external circuitry.
- Other Additives and Fillers: Depending on the specific requirements of the application, other additives and fillers may be incorporated into the base material to improve properties such as thermal conductivity, moisture resistance, and adhesion.
The combination of these materials results in a substrate that can support the high-density interconnects and fine pitch features necessary for modern semiconductor packages, such as flip-chip BGA (Ball Grid Array) and CSP (Chip Scale Package). The ABF substrate’s ability to provide excellent electrical performance, mechanical robustness, and thermal management is crucial for the reliable operation of advanced electronic devices.
Which company makes ABF Package Substrates?
ABF Package Substrates are manufactured by Ajinomoto Fine-Techno Co., Inc. in Japan. As a leading company specializing in semiconductor packaging technology, Ajinomoto Fine-Techno Co., Inc. has extensive experience and expertise in the field of ABF Package Substrates.
The ABF Package Substrates produced by Ajinomoto Fine-Techno Co., Inc. exhibit excellent performance and reliability, suitable for various advanced semiconductor packaging applications. Their ABF base material features outstanding electrical insulation, mechanical strength, and thermal stability, meeting the requirements of modern electronic devices for high-density interconnection, miniaturization, and high-speed signal transmission.
Our company also manufactures ABF Package Substrates. We have advanced production equipment and a skilled technical team capable of customizing ABF substrates to meet specific customer requirements. Our production processes strictly adhere to international standards and industry specifications, ensuring the highest level of product quality.
Our strengths include:
- Customized Production: We can customize ABF Package Substrates according to customer-specific requirements, including dimensions, layer stackup, electrical performance, and more.
- Flexible Production Capacity: We possess flexible production lines and responsive manufacturing capabilities to meet orders of various scales and timelines.
- Quality Control System: We have established a comprehensive quality management system, from raw material procurement to production manufacturing and product inspection, strictly adhering to quality standards to ensure stable and reliable product quality.
- Technical Support and Services: Our professional technical team and after-sales service team can provide technical support, solution design, and after-sales service to ensure timely fulfillment of customer needs.
With our production capabilities and professional expertise, we can provide high-quality, customized ABF Package Substrates to help customers achieve success in the market.
What are the 7 qualities of good customer service?
Good customer service is characterized by several key qualities that contribute to a positive customer experience and build customer loyalty. Here are seven qualities of good customer service:
- Responsiveness: Good customer service involves being prompt and responsive to customer inquiries, requests, and concerns. Customers appreciate timely assistance and solutions to their problems, whether it’s through phone calls, emails, or live chat support.
- Empathy: Empathy is the ability to understand and relate to the customer’s emotions, concerns, and perspectives. Good customer service representatives demonstrate empathy by actively listening to customers, acknowledging their feelings, and showing genuine concern for their well-being.
- Clear Communication: Effective communication is essential for providing good customer service. Customer service representatives should communicate clearly and concisely, using language that is easy for customers to understand. They should also ensure that information regarding products, services, policies, and procedures is communicated accurately.
- Knowledgeability: Good customer service requires having a thorough understanding of the products or services offered, as well as company policies and procedures. Customer service representatives should be knowledgeable enough to answer customer questions, provide relevant information, and offer solutions to problems.
- Professionalism: Professionalism encompasses various qualities such as politeness, courtesy, respectfulness, and integrity. Customer service representatives should maintain a professional demeanor at all times, regardless of the customer’s behavior or attitude. They should also uphold ethical standards and company values in their interactions with customers.
- Problem-Solving Skills: Good customer service involves the ability to effectively resolve customer issues and address their concerns. Customer service representatives should be skilled at identifying problems, analyzing situations, and finding appropriate solutions that meet the needs of the customer while aligning with company policies.
- Follow-Up and Follow-Through: Providing good customer service doesn’t end with resolving a customer’s immediate issue. It also involves following up to ensure that the customer’s needs have been met and following through on any commitments made. Customer service representatives should take proactive steps to ensure customer satisfaction and foster long-term relationships.
By embodying these qualities, businesses can deliver exceptional customer service experiences that leave a lasting positive impression on their customers.
FAQs
What is an ABF Package Substrate?
An ABF Package Substrate is a type of advanced substrate used in semiconductor packaging. It consists of layers of polyimide film with thin copper foil layers bonded to them, providing electrical connectivity and mechanical support for semiconductor devices.
What are the advantages of ABF Package Substrates?
ABF Package Substrates offer several advantages, including high thermal stability, excellent electrical insulation, mechanical strength, and the ability to support high-density interconnects and fine pitch features. They are also suitable for advanced packaging technologies like flip-chip and chip-on-flex.
What applications are ABF Package Substrates used for?
ABF Package Substrates are used in a wide range of semiconductor packaging applications, including mobile devices, consumer electronics, automotive electronics, and telecommunications equipment. They are particularly well-suited for applications requiring miniaturization, high-speed signal transmission, and efficient heat dissipation.
What are the design considerations for ABF Package Substrates?
Design considerations for ABF Package Substrates include layer stackup, copper trace width and spacing, via design, thermal management, component placement and routing, electrical performance, mechanical durability, manufacturability, and reliability testing.
How are ABF Package Substrates manufactured?
The manufacturing process for ABF Package Substrates involves several key steps, including substrate preparation, copper cladding, photoimaging, etching, dielectric layer deposition, via formation, conductor plating, surface finishing, laser drilling and routing, inspection, and testing.
What is the cost of ABF Package Substrates?
The cost of ABF Package Substrates can vary depending on factors such as size, complexity, materials, manufacturing process, volume, supplier, and customization requirements. It’s recommended to consult with substrate manufacturers or suppliers for accurate pricing based on specific project needs.
Who manufactures ABF Package Substrates?
ABF Package Substrates are manufactured by companies specializing in semiconductor packaging technologies, including Ajinomoto Fine-Techno Co., Inc. and other semiconductor packaging companies worldwide.