What is ABF Substrate?
ABF Substrate,ABF Substrate (Anisotropic Conductive Film Substrate) is a critical component for integrated circuit packaging, featuring anisotropic conductive film properties. It provides electrical connections in both vertical and horizontal directions via fine conductive particles, enabling high-density, high-performance packaging. Typically composed of multiple layers of thin films including insulation, metal, and conductor layers, ABF Substrate ensures reliable electrical connections and effective thermal management. Its design supports miniaturization, facilitating high integration in small electronic devices while maintaining performance and reliability.
ABF Substrate, in most scenarios, alludes to the bonding mediums known as Anisotropic Conductive Film (ACF) or Anisotropic Conductive Adhesive (ACA). This material plays a pivotal role in the domain of electronics manufacturing, specifically in affixing components such as semiconductor chips or flexible printed circuits onto a substrate.
Anisotropic Conductive Film is essentially a slender film featuring conductive particles meticulously aligned in a specific direction. Its primary purpose lies in establishing precise electrical connections between components with fine pitches. The distinctive anisotropic attributes of the film facilitate the conduction of electricity in one direction while ensuring insulation in other directions.
This avant-garde technology sees extensive application in the assembly of electronic devices, encompassing LCD displays, flexible displays, and various electronic components necessitating intricate connections. The integration of ABF Substrate contributes to the formation of dependable and spatially efficient connections in these sophisticated applications.
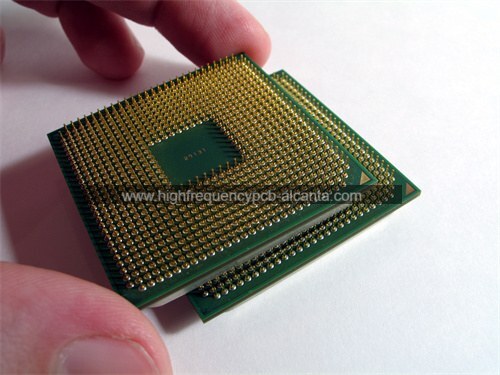
ABF Substrate
What functions does ABF Substrate serve?
Enter the ABF substrate, a silent powerhouse in the intricate dance of semiconductor packaging. This versatile player takes on an array of vital roles:
Electric Symphony: The ABF substrate steps into the spotlight as the maestro of electrical connections, weaving a seamless tapestry between the semiconductor die (the brains of the integrated circuit) and the package. It crafts the pathways that let electrical signals waltz between the chip and its external companions.
Heat Choreography: With finesse, the ABF substrate choreographs the thermal ballet during the semiconductor device’s performance. It pirouettes in the art of heat dissipation, a crucial act in preventing the device from breaking into an overheated sweat, ensuring a performance of reliability.
Structural Ballet: Beyond its electrical prowess, the ABF substrate takes center stage as a structural virtuoso, providing a sturdy ballet barre for the semiconductor die. This support dance shields the chip from mechanical stresses, vibrations, and external duets, fortifying the package’s overall resilience.
Signal Waltz: Imbued with carefully crafted material notes, the ABF substrate leads a graceful waltz, preserving the harmony of signal integrity. This dance ensures a precise and dependable transmission of electrical signals, a vital movement in applications that demand a high-speed and high-frequency performance ballet.
Svelte Design Elegance: ABF substrates gracefully pirouette in the realm of advanced packaging technologies, adding an elegant touch to the pursuit of compactness. Their slender and nimble composition contributes to the overall reduction in the dimensions of semiconductor packages, a design pas de deux.
Flip-Chip Choreography: Tailored for the flip-chip stage, ABF substrates execute a flawless dance routine. In this choreography, the semiconductor die takes a direct plunge onto the substrate with the active side facing downward, a graceful move that shortens the electrical path and enhances the overall performance pirouette.
In essence, the ABF substrate emerges not just as a player but as a lead dancer, orchestrating electrical symphonies, conducting thermal ballets, leading structural performances, safeguarding signal waltzes, and elegantly participating in the dance of miniaturization, particularly within the enchanting world of flip-chip technology.
What are the different types of ABF Substrate?
Diverse iterations of ABF (Ajinomoto Build-up Film) substrates cater to a spectrum of needs in the dynamic realm of semiconductor packaging. Here’s a glimpse into various types:
Solo Harmony – Single-Layer ABF Substrate:
Overview: A fundamental ABF substrate boasting a solo layer, well-suited for straightforward semiconductor packaging needs.
Application: Finds its place in less intricate semiconductor devices.
Layered Complexity – Multi-Layer ABF Substrate:
Overview: This rendition embraces complexity with multiple stacked layers, accommodating intricate circuitry and interconnects.
Application: Ideal for advanced semiconductor devices demanding sophisticated routing.
Frequency Maestro – High-Frequency ABF Substrate:
Overview: Crafted for high-frequency symphonies, minimizing signal loss and distortion.
Application: Takes the stage in applications like high-frequency communication systems.
Silent Transmission – Low-Loss ABF Substrate:
Overview: Whispers minimal loss during signal transmission, prioritizing pristine signal integrity.
Application: Essential in high-speed data communication where signal fidelity is non-negotiable.
Thermal Virtuoso – Thermal-Enhanced ABF Substrate:
Overview: Puts on a thermal performance show, excelling in efficient heat dissipation.
Application: Key player in preventing overheating in semiconductor devices.
Flexibility Ballet – Flexible ABF Substrate:
Overview: Showcasing flexibility as a defining trait, adapting to applications that require a bendable form.
Application: Tailored for devices or systems with flexibility demands.
Embedded Symphony – Embedded Passive Components ABF Substrate:
Overview: Integrates passive components seamlessly, orchestrating a symphony within the substrate.
Application: Optimizes space in semiconductor packages by embedding resistors or capacitors.
Fan-Out Fusion – Fan-Out ABF Substrate:
Overview: Takes center stage in fan-out wafer-level packaging, harmonizing the integration of multiple chips in a single package.
Application: Catalyst for advanced packaging, driving miniaturization and integration.
Choosing the right ABF substrate is akin to composing a symphony, with considerations for semiconductor device complexity, electrical performance, thermal dynamics, and specific application nuances. Each type contributes uniquely to the orchestration of optimal semiconductor package performance.
How is ABF Substrate related to IC packaging?
ABF (Ajinomoto Build-up Film) substrate weaves an intricate tapestry within the domain of integrated circuit (IC) packaging. Its association with IC packaging is profound and versatile:
Conductor of Electrical Harmony: ABF substrate serves as a conductor, orchestrating the electrical connections within the IC package. It establishes pathways for the seamless flow of electrical signals between the semiconductor die and external components like pins or leads.
Die Affixation Ballet: In the choreography of IC packaging, ABF substrate takes center stage in facilitating the secure attachment of the semiconductor die. It provides a steadfast stage for the placement and connection of the die.
Interwoven Connections: ABF substrates intricately interconnect the semiconductor die with other components, be it bonding wires, solder balls, or conductive traces on the substrate. This interconnection forms the backbone of the IC’s functionality.
Thermal Performance Sonata: In the symphony of IC packaging, ABF substrates contribute to thermal dissipation, playing a vital role in maintaining optimal operating temperatures and averting the risk of overheating.
Lilliputian Package Artistry: Often featured in avant-garde packaging technologies, ABF substrates contribute to the art of miniaturization. Their slender profile allows for the reduction in the overall dimensions of the IC package, harmonizing with the pursuit of spatial efficiency.
Technological Tango: ABF substrates elegantly waltz with various advanced packaging techniques. From the intricate steps of flip-chip packaging to the expansive moves of fan-out wafer-level packaging and the three-dimensional dynamics, ABF substrates align seamlessly with these techniques for enhanced performance and compact designs.
Guardian of Signal Purity: In the realm of IC packaging, where signal integrity is paramount, ABF substrates are the vigilant guardians. They are designed to preserve the pristine quality of signals, minimizing losses during transmission, especially crucial in high-speed and high-frequency applications.
Passive Components Pas de Deux: Some ABF substrates engage in a pas de deux by embedding passive components like resistors or capacitors. This integration within the substrate adds a layer of sophistication, contributing to the miniaturization and efficient use of space in IC packages.
In essence, the relationship between ABF substrate and IC packaging is akin to a symphony conductor guiding a diverse ensemble. ABF substrate assumes a pivotal role, harmonizing electrical connections, providing structural support, managing thermal dynamics, and elegantly participating in the evolution of advanced packaging techniques for integrated circuits.
What are the differences between ABF Substrate and traditional PCBs?
ABF (Ajinomoto Build-up Film) substrates and traditional PCBs (Printed Circuit Boards) stand apart with distinctions in composition, materials, and applications. Let’s delve into the unique characteristics that distinguish them:
Composition:
ABF Substrate: Forged through an intricate build-up process, ABF substrates intricately layer multiple insulating materials and conductive traces. This technique elevates interconnect density, accommodating compact form factors.
Traditional PCBs: Conventional PCBs typically feature a core layer fashioned from rigid materials like FR-4, embellished with copper traces etched onto the surface. Despite potential layers, the construction tends to follow a more straightforward path compared to ABF substrates.
Materials:
ABF Substrate: Tapping into the realm of organic materials like polyimide and other insulating films, ABF substrates offer a flexible canvas. This flexibility renders them apt for applications where a pliable substrate is a prerequisite.
Traditional PCBs: Anchored in rigid materials like FR-4, traditional PCBs prioritize stability and find their stride in applications where rigidity takes precedence.
Flexibility:
ABF Substrate: Celebrated for their suppleness, ABF substrates take the stage in scenarios demanding non-planar shapes or where flexibility emerges as a strategic advantage.
Traditional PCBs: Staying true to their roots, traditional PCBs exude rigidity, fitting seamlessly into applications where a flat and inflexible structure is the need of the hour.
Applications:
ABF Substrate: ABF substrates bask in the spotlight of applications thirsting for high-density interconnects, prevalent in the realms of advanced semiconductor packaging, mobile devices, and flexible electronics.
Traditional PCBs: The stalwart of diverse electronic devices, traditional PCBs find their calling in computers, consumer electronics, and industrial equipment.
Complexity and Cost:
ABF Substrate: The labyrinthine build-up process in ABF substrates allows for sophisticated designs, finer features, but potentially incurs higher manufacturing costs due to heightened complexity.
Traditional PCBs: Defined by simplicity, traditional PCBs with their larger feature sizes may present a more economical manufacturing solution.
In essence, the selection between ABF substrates and traditional PCBs pivots on the bespoke needs of the electronic device or system under scrutiny. Each crafts its narrative, offering tailored solutions in the ever-evolving tapestry of electronic design.
What is the main structure and production technology of ABF Substrate?
ABF Substrate, specifically denoting Anisotropic Conductive Film (ACF) or Anisotropic Conductive Adhesive (ACA), features a slim film structure with unique attributes. The manufacturing journey of ABF Substrate encompasses several pivotal stages:
Structural Configuration:
Formation of the Thin Film:
At the core of ABF Substrate is a thin film crafted from dielectric material, laying the groundwork for its structural foundation.
Integration of Conductive Particles (for ACF):
In the case of ACF, the thin film seamlessly incorporates conductive particles, often metallic or metal-coated. These particles assume a crucial role in fostering electrical conductivity.
Incorporation of Adhesive (for ACA):
For ACA, the film embraces an adhesive composition enriched with conductive particles. This adhesive not only facilitates robust bonding but also nurtures electrical connections.
Anisotropic Alignment:
Deliberate alignment of conductive particles within the film follows an anisotropic pattern. This unique alignment empowers electrical conduction along the specified direction while ensuring effective insulation in other orientations.
Manufacturing Techniques:
Adoption of Film Formation Approaches:
The fabrication of the thin film unfolds through diverse methodologies like coating or lamination. The selection of materials hinges on considerations such as dielectric characteristics, thermal resilience, and flexibility prerequisites.
Implementing Techniques for Conductive Particle Dispersion:
In ACF, achieving a homogenous dispersion of conductive particles within the film involves adept techniques like mixing or coating. This meticulous dispersion is paramount for optimizing electrical performance.
Execution of Alignment Processes:
The anisotropic alignment of conductive particles takes shape through mechanical or magnetic processes. Mechanical alignment entails controlled stretching of the film, while magnetic forces guide particle orientation.
Application of Adhesive (for ACA):
In ACA, the adhesive embedded with conductive particles is judiciously applied to the targeted bonding surfaces. The adhesive selection revolves around factors like adhesion strength, flexibility, and thermal attributes.
Commencement of Curing or Setting Phase:
Subsequent to the application phase, a curing or setting process ensues to solidify the material, ensuring steadfast adhesion to the designated surfaces.
Manufacturers often leverage proprietary methodologies tailored to specific applications, aiming to fine-tune the performance of ABF Substrate across a spectrum of electronic devices and packaging scenarios.
Frequently Asked Questions about ABF Substrate
How does ABF Substrate function?
ABF Substrate operates by utilizing conductive particles (ACF) or conductive adhesive (ACA) to create electrical connections. The anisotropic alignment of particles enables conduction in one direction while insulating in others.
What are the primary applications of ABF Substrate?
ABF Substrate is commonly applied in assembling electronic devices like LCD displays, flexible displays, and semiconductor packaging. It is especially suitable for scenarios demanding fine-pitch connections and flexibility.
How does ABF Substrate differ from traditional PCBs?
ABF Substrate, with a focus on fine-pitch connections and flexibility, differs from traditional PCBs that serve as standard platforms for mounting electronic components. ABF Substrate, particularly ACF or ACA, introduces unique electrical connectivity features.
What is the production technology behind ABF Substrate?
The production of ABF Substrate involves thin film formation, dispersion of conductive particles (for ACF), alignment processes, and the application of adhesive with conductive particles (for ACA). Manufacturing processes may vary based on specific applications.
Can ABF Substrate be used in flexible electronics?
Yes, ABF Substrate, particularly in flexible ACF or ACA form, is well-suited for flexible electronics. It facilitates connections in devices requiring flexibility or bending, such as flexible displays.
What advantages does ABF Substrate offer?
ABF Substrate provides advantages such as fine-pitch connections, reliability in electronic assemblies, and adaptability to advanced packaging technologies. It is also suitable for applications where flexibility is essential.
Is ABF Substrate suitable for high-density interconnects?
Certainly, ABF Substrate, especially ACF, is suitable for high-density interconnects. Its capability to establish fine-pitch connections is valuable in applications with densely packed components.
How does ABF Substrate contribute to thermal management?
ABF Substrate contributes to thermal management by efficiently dissipating heat from semiconductor dies, preventing overheating. The choice of ABF Substrate can impact thermal conductivity and overall package reliability.
Conclusion
To sum up, ABF Substrate, encapsulating Anisotropic Conductive Film (ACF) and Anisotropic Conductive Adhesive (ACA), emerges as a cornerstone in the realm of electronics manufacturing. Its slender film structure, whether integrating conductive particles or adhesive, assumes a pivotal role in fostering component bonding and establishing meticulous electrical connections.
The distinctive attributes of ABF Substrate, characterized by fine-pitch connections and flexibility, delineate its departure from traditional Printed Circuit Boards (PCBs). Its utility spans a broad spectrum, encompassing the assembly of LCD displays, flexible electronics, and semiconductor packaging, rendering it a versatile solution for diverse electronic devices.
The manufacturing technology underpinning ABF Substrate entails intricate procedures, including thin film formation, dispersion of conductive particles or application of adhesive, and anisotropic alignment. These processes contribute to the distinctive electrical properties and dependability that ABF Substrate bestows upon electronic assemblies.
In responding to frequently asked questions, we have delved into its functionality, applications, advantages, and differentiation from traditional PCBs. ABF Substrate, with its adeptness in accommodating high-density interconnects, playing a role in thermal management, and adapting to flexible electronics, emerges as a pivotal player in propelling advancements in electronic device technologies.
In essence, ABF Substrate embodies innovation in electronics manufacturing, providing a foundation for exacting and dependable connections in the dynamic landscape of electronic devices and integrated circuits.