96AL2O3 Ceramic Pcb Manufacturing
96AL2O3 Ceramic Pcb Manufacturing,The 96AL2O3 Ceramic PCB is a high-performance printed circuit board made from 96% alumina oxide ceramic material. This type of PCB boasts excellent thermal conductivity, high mechanical strength, and outstanding insulation properties, making it suitable for various high-temperature and high-power electronic applications. Its unique ceramic substrate enables exceptional performance in high-frequency circuits, along with excellent corrosion resistance and chemical stability. Widely used in industries such as power electronics, LED lighting, aerospace, and medical equipment, 96AL2O3 Ceramic PCBs are the preferred solution due to their superior performance and reliability. The manufacturing process involves forming and shaping the ceramic material, printing conductive traces and components, and high-temperature sintering. Customized designs are available to meet specific application requirements, providing customers with high-performance and reliable solutions.
What is a 96AL2O3 Ceramic PCB?
A 96AL2O3 ceramic PCB, or Printed Circuit Board, is a type of circuit board made from a material called alumina (Al2O3), which is a type of ceramic. The “96” in the name refers to the alumina’s purity, typically indicating that it is 96% pure alumina.
These ceramic PCBs are known for their excellent thermal conductivity, high mechanical strength, and good electrical insulation properties. They are often used in high-power electronic applications where heat dissipation is critical, such as in power amplifiers, LED modules, high-frequency circuits, and other applications where traditional FR4 or epoxy-based PCBs might not suffice.
The use of alumina ceramic PCBs can help in improving the reliability and performance of electronic devices, particularly in environments with high temperatures or where there are stringent requirements for thermal management.
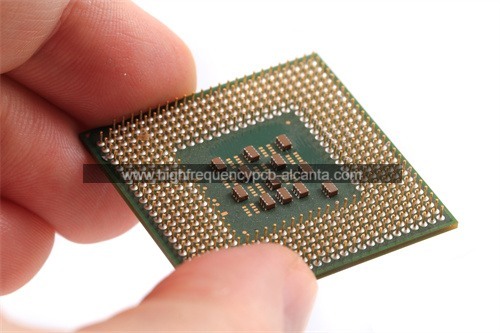
96AL2O3 Ceramic Pcb Manufacturing
What are the 96AL2O3 Ceramic PCB Design Guidelines?
Designing with 96AL2O3 ceramic PCBs involves considering several guidelines to ensure optimal performance and reliability. Here are some key considerations:
- Thermal Management: Alumina ceramic PCBs are renowned for their excellent thermal conductivity. Ensure proper heat dissipation by incorporating thermal vias, thermal pads, or heatsinks into the design. Proper thermal management helps in preventing overheating and ensures stable operation of the components.
- Mechanical Strength: Alumina ceramic is known for its high mechanical strength. However, avoid sharp corners or edges in the design to prevent stress concentration, which could lead to cracking or fractures during manufacturing or operation.
- Dielectric Properties: Alumina ceramic has good electrical insulation properties. Maintain appropriate spacing between conductive traces and components to prevent electrical short circuits. Follow standard PCB design practices for signal integrity and impedance control.
- Surface Finish: Choose surface finishes compatible with alumina ceramic, such as gold plating or thick-film metallization. Ensure the surface finish provides good solderability and reliability under operating conditions.
- Component Mounting: Consider the compatibility of component mounting techniques with ceramic PCBs. Surface mount technology (SMT) is commonly used, but through-hole components may also be suitable depending on the application requirements.
- Environmental Considerations: Evaluate the operating environment of the PCB, including temperature extremes, humidity, and potential exposure to corrosive substances. Select materials and design features that can withstand these conditions for long-term reliability.
- Manufacturability:Work closely with PCB manufacturers experienced in handling ceramic substrates. Considerations such as drilling, routing, and assembly processes may differ from standard FR4 PCBs and require specialized expertise.
- Testing and Quality Assurance: Implement thorough testing protocols to ensure the quality and reliability of the ceramic PCBs. Perform electrical testing, thermal cycling, and other reliability tests to validate the design under various conditions.
By adhering to these guidelines, designers can leverage the unique properties of 96AL2O3 ceramic PCBs to create robust and high-performance electronic systems.
What is the 96AL2O3 Ceramic PCB Fabrication Process?
The fabrication process for a 96% alumina ceramic PCB involves several steps:
- Material Selection: High-purity alumina ceramic powder with a purity of 96% is selected as the base material for the PCB.
- Powder Preparation: The alumina powder is mixed with binders and additives to form a slurry with the desired properties for shaping.
- Shaping: The slurry is shaped into the desired form using methods such as tape casting, injection molding, or dry pressing. This step forms the green ceramic substrate.
- Green Machining: If necessary, the green ceramic substrate may undergo machining processes to achieve the desired dimensions and surface finish.
- Drying: The shaped green ceramic substrate is dried to remove moisture and organic binders, leaving behind a porous ceramic structure.
- Firing: The dried green ceramic substrate is subjected to high-temperature firing in a kiln. During firing, the ceramic particles bond together, and the organic binders are completely burned off, resulting in a dense and solid ceramic material.
- Surface Preparation: After firing, the ceramic substrate’s surfaces may be polished or treated to achieve the required surface finish and flatness.
- Metallization: Metal traces and pads are applied to the ceramic substrate using methods such as thick film printing, thin film deposition (e.g., sputtering or evaporation), or screen printing. These metal layers provide the conductive pathways for electrical connections.
- Firing (Metallization): The metallized ceramic substrate undergoes a second firing process to bond the metal layers securely to the ceramic surface.
- Through-Hole Formation (Optional): If through-holes are required for component mounting or electrical connections, they may be drilled or laser machined into the ceramic substrate.
- Metallization of Through-Holes: Metal is deposited into the through-holes using processes such as electroplating or conductive paste filling to establish electrical connections between layers.
- Final Finishing: The ceramic PCB may undergo additional processes such as laser trimming, surface coating, or solder mask application to finalize its features and protect its surfaces.
- Testing and Inspection: The finished ceramic PCB undergoes rigorous testing and inspection to ensure its electrical performance, dimensional accuracy, and reliability meet the required specifications.
Overall, the fabrication process for a 96AL2O3 ceramic PCB involves a combination of ceramic processing techniques and conventional PCB manufacturing methods to produce a high-performance and reliable circuit board suitable for demanding applications.
How do you manufacture a 96AL2O3 Ceramic PCB?
Manufacturing a 96% aluminum oxide (Al2O3) ceramic printed circuit board (PCB) involves several steps, typically including material preparation, shaping, firing, and finishing. Here’s a general overview of the process:
- Material Selection: Start with high-purity aluminum oxide powder (typically 96% purity). Other additives may be included depending on the specific properties desired in the final product.
- Formulation: Mix the aluminum oxide powder with any desired additives such as binders, plasticizers, and solvents to create a slurry or paste.
- Shaping: Apply the slurry onto a substrate using various methods such as screen printing, doctor blading, or tape casting. This creates a green sheet with the desired thickness and pattern.
- Drying: Dry the green sheets to remove the solvent and form a solid green body. This step is crucial to prevent cracking during subsequent processing.
- Layering: Stack multiple green sheets with conductive layers (usually made of metals like silver or copper) in between to form the desired circuit pattern. This may involve several layers depending on the complexity of the PCB.
- Lamination: Press the layered green sheets together under high pressure to ensure good adhesion between the layers.
- Firing: Heat the laminated green body in a kiln to sinter the ceramic particles and burn off any remaining organic materials. This process typically involves high temperatures (over 1500°C) in a controlled atmosphere to achieve full densification and desired material properties.
- Metallization: After firing, apply metal conductors to the ceramic surface by techniques such as screen printing, vapor deposition, or sputtering. This creates the conductive traces necessary for the PCB.
- Etching: Use chemical etching or laser ablation to remove excess metal and define the circuit pattern.
- Finishing: Apply any additional finishing processes such as coating, polishing, or drilling as needed to meet the final specifications of the PCB.
- Testing: Conduct thorough testing to ensure the PCB meets quality standards and functional requirements.
- Packaging: Once the PCBs pass inspection, package them appropriately for shipping or further assembly.
Throughout the manufacturing process, it’s essential to maintain tight quality control measures to ensure consistency and reliability in the final product. Additionally, specific steps and parameters may vary depending on the equipment, materials, and desired specifications of the ceramic PCB.
How much should a 96AL2O3 Ceramic PCB cost?
The cost of a 96AL2O3 ceramic PCB can vary depending on several factors, including:
- Size and Complexity: Larger and more complex PCBs typically cost more to manufacture due to increased material usage and processing time.
- Thickness: Thicker ceramic substrates may incur higher material costs and require more precise machining, impacting the overall cost.
- Quantity: Economies of scale apply in PCB manufacturing. Larger production quantities often result in lower per-unit costs due to bulk discounts and optimized production processes.
- Design Requirements: Specialized features such as tight tolerances, complex geometries, or specific surface finishes may increase the cost of manufacturing.
- Lead Time: Urgent orders or expedited manufacturing may incur additional charges.
- Supplier and Location: Different PCB manufacturers have varying pricing structures and cost structures based on their capabilities, expertise, and geographic location.
As a rough estimate, 96AL2O3 ceramic PCBs tend to be more expensive than traditional FR4 PCBs due to the higher cost of ceramic materials and specialized manufacturing processes. Prices can range from tens to hundreds of dollars per unit, depending on the aforementioned factors.
For an accurate cost estimate, it’s best to consult with multiple PCB manufacturers, provide detailed design specifications, and request quotes based on your specific requirements and desired quantity.
What is the 96AL2O3 Ceramic PCB base material?
The 96AL2O3 ceramic PCB base material refers to a type of ceramic printed circuit board (PCB) substrate primarily composed of alumina (Al2O3) with a purity of 96%. Alumina ceramic PCBs are widely used in various electronic applications due to their excellent thermal conductivity, high electrical insulation properties, and good mechanical strength.
The “96” in 96AL2O3 denotes the percentage of alumina present in the ceramic material, indicating a high purity level. Alumina is chosen for its thermal properties, as it efficiently dissipates heat away from sensitive electronic components, ensuring reliable performance and longevity, especially in high-power or high-frequency applications.
Ceramic PCBs are particularly advantageous in environments where traditional organic substrates might not suffice, such as in high-temperature settings or applications where thermal management is critical. The exceptional thermal conductivity of alumina allows for efficient heat dissipation, reducing the risk of overheating and maintaining the stability of electronic components.
Moreover, alumina ceramic substrates offer high mechanical strength and rigidity, making them suitable for use in harsh operating conditions where vibration, mechanical stress, or thermal cycling are concerns. Their excellent electrical insulation properties also prevent signal interference and leakage, ensuring reliable circuit performance.
The “AL2O3” designation indicates the presence of aluminum oxide, the chemical compound of alumina, which is known for its stability, hardness, and resistance to corrosion.
In summary, the 96AL2O3 ceramic PCB base material is a high-purity alumina ceramic substrate used in electronic applications requiring superior thermal management, electrical insulation, mechanical strength, and reliability. Its properties make it an ideal choice for demanding environments where traditional PCB materials may not meet the performance requirements.
Which company manufactures 96AL2O3 Ceramic PCBs?
One of the manufacturers of 96AL2O3 Ceramic PCBs is specialized ceramic PCB manufacturing companies, such as Hitachi Chemical in Japan, Kyocera in the United States, Ferrotec in Germany, among others. These companies have rich experience and expertise in the manufacturing and application of ceramic materials.
Our company is capable of producing 96AL2O3 Ceramic PCBs. As a professional electronic manufacturing company, we possess advanced production equipment and a skilled technical team to meet the demand for high-quality ceramic PCBs from our customers. Our production process includes raw material procurement, design and engineering validation, manufacturing processing, quality control, and more, ensuring reliable product quality.
Firstly, we select high-quality 96AL2O3 ceramic material as the substrate, ensuring excellent thermal conductivity, insulation, and mechanical strength. Then, through advanced processing techniques such as CNC machining, laser cutting, etc., we precisely process the ceramic substrate to meet the diverse needs of our customers. Throughout the production process, we strictly control every step to ensure stable and reliable product quality.
In addition to production processes, we also prioritize communication and collaboration with our customers. Our technical team can provide customized solutions based on customer requirements and maintain close communication with customers throughout the entire project process, promptly responding to customer needs and feedback.
In summary, as a professional electronic manufacturing company, we have rich experience and advanced technology to produce high-quality 96AL2O3 Ceramic PCBs and provide customized solutions to meet various customer needs.
What are the 7 qualities of good customer service?
Good customer service is characterized by several key qualities:
- Responsiveness: This involves promptly addressing customer inquiries, concerns, and requests. Whether it’s through phone, email, or in-person interactions, responding quickly shows customers that their needs are valued and important.
- Empathy: Empathizing with customers means understanding their emotions, concerns, and perspectives. It involves actively listening to their issues, showing compassion, and demonstrating a genuine desire to help solve their problems.
- Clear Communication: Effective communication is essential in customer service. It means conveying information clearly and concisely, avoiding jargon, and ensuring that customers understand the solutions or actions being proposed.
- Professionalism: Maintaining professionalism in all interactions is crucial. This includes being polite, courteous, and respectful at all times, regardless of the situation. Professionalism also involves maintaining composure and staying calm, even in challenging or stressful situations.
- Knowledgeability: Customers expect service representatives to be knowledgeable about the products or services offered. Having a deep understanding of the company’s offerings allows representatives to provide accurate information, answer questions, and offer helpful recommendations.
- Problem-Solving Skills: Effective problem-solving is a key aspect of good customer service. It involves identifying issues, analyzing root causes, and finding practical solutions to resolve customer problems in a timely manner.
- Consistency: Consistency is important for building trust and loyalty with customers. Providing consistent service across all channels and interactions ensures that customers receive a reliable and predictable experience every time they engage with the company.
By embodying these qualities, businesses can create positive experiences for their customers and build long-lasting relationships that drive satisfaction and loyalty.
FAQs
What are the advantages of using 96AL2O3 Ceramic PCBs?
96AL2O3 Ceramic PCBs offer excellent thermal conductivity, electrical insulation, and mechanical stability, making them suitable for high-power and high-frequency applications.
Can 96AL2O3 Ceramic PCBs be used in harsh environments?
Yes, 96AL2O3 Ceramic PCBs are known for their durability and can withstand extreme temperatures and environmental conditions, making them suitable for aerospace, automotive, and industrial applications.
What is a 96AL2O3 Ceramic PCB?
A 96AL2O3 Ceramic PCB is a printed circuit board (PCB) made from 96% alumina oxide ceramic material. It offers excellent thermal conductivity, high mechanical strength, and exceptional insulation properties, making it suitable for various high-temperature and high-power electronic applications.
Are 96AL2O3 Ceramic PCBs more expensive than traditional PCBs?
Yes, 96AL2O3 Ceramic PCBs tend to be more expensive due to the cost of ceramic materials and the specialized manufacturing processes involved. However, their unique properties and performance advantages justify the investment in many applications.
Can 96AL2O3 Ceramic PCBs be customized for specific requirements?
Yes, manufacturers often offer customization services to tailor 96AL2O3 Ceramic PCBs to meet specific size, shape, and performance requirements. Customization may include substrate thickness, metallization patterns, and surface finishes.