3D Ceramic Packages Substrate Manufacturing
3D Ceramic Packages Substrate Manufacturing,3D Ceramic Packages Substrate refers to a sophisticated packaging solution utilized in electronic devices, particularly those requiring compactness and high thermal performance. These substrates are constructed from ceramic materials and designed to accommodate multiple layers of circuitry within a three-dimensional space. By stacking circuits vertically, 3D Ceramic Packages Substrates enable increased functionality and performance while minimizing the footprint of the device. The ceramic material provides excellent thermal conductivity and mechanical strength, making it ideal for applications where heat dissipation is crucial. Additionally, the 3D design allows for efficient signal routing and reduced interconnect lengths, thereby improving signal integrity and reducing electromagnetic interference. This innovative packaging technology finds widespread use in various industries, including telecommunications, automotive electronics, and consumer electronics, where the demand for smaller, more powerful devices continues to grow. Overall, 3D Ceramic Packages Substrates represent a significant advancement in packaging technology, offering enhanced performance and miniaturization for modern electronic devices.
What is a 3D Ceramic Packages Substrate?
A 3D Ceramic Packages Substrate refers to a type of substrate used in electronic packaging, particularly in the semiconductor industry. It’s designed to provide a platform for mounting and interconnecting semiconductor chips, facilitating the assembly of complex integrated circuits.
Here’s a breakdown of its components and features:
- Ceramic Material: The substrate is typically made of ceramic material such as alumina (Al2O3) or aluminum nitride (AlN). Ceramic substrates offer excellent thermal conductivity, mechanical strength, and electrical insulation, making them suitable for high-performance electronic applications.
- 3D Architecture: The term “3D” indicates that the substrate is designed to accommodate multiple layers of circuitry and components, stacked vertically to optimize space utilization and enhance performance. This vertical stacking allows for increased functionality and miniaturization of electronic devices.
- Interconnection Features: The substrate includes various interconnection features such as vias, traces, and pads, which facilitate the electrical connections between different layers of the substrate and the mounted semiconductor chips. These interconnections enable signal transmission, power distribution, and thermal management within the packaged device.
- Embedded Components: In some cases, the substrate may also incorporate embedded passive components such as resistors, capacitors, and inductors, further enhancing the integration density and reducing the overall footprint of the electronic system.
- Thermal Management: Given the importance of thermal management in high-performance electronic devices, 3D ceramic packages often incorporate features such as thermal vias, heat spreaders, and thermal interface materials to efficiently dissipate heat generated by the semiconductor chips.
Overall, 3D ceramic packages substrates are essential components in the development of advanced semiconductor devices, enabling higher levels of integration, improved performance, and enhanced reliability in a compact form factor.
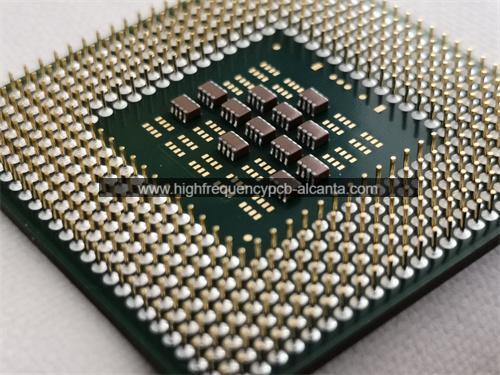
3D Ceramic Packages Substrate Manufacturing
What are the Design Guidelines for 3D Ceramic Packages Substrates?
Here are some design guidelines for 3D ceramic packages substrates:
- Dimensions and Stacking: Determine the dimensions and thickness of the substrate to accommodate the required number of components and stacking layers. Balancing size with performance is crucial in 3D structures to ensure the desired functionality within limited space.
- Material Selection: Choose suitable ceramic materials such as alumina or aluminum nitride to meet performance requirements, particularly considering the thermal conductivity for effective heat management.
- Interconnect Design: Design effective interconnect structures including vias, traces, and pads to ensure reliable electrical connections and signal transmission. Optimize interconnect layouts to minimize signal delay and crosstalk.
- Thermal Management: Consider heat transfer and dissipation paths, design thermal vias, heat spreaders, or other thermal management structures to efficiently remove heat generated by the chips, preventing temperature rise that could affect performance and reliability.
- Component Layout: Optimize component layout and stacking sequence to minimize signal path lengths and current loops, reducing power consumption and crosstalk.
- Packaging and Assembly Techniques: Choose appropriate packaging techniques such as Ball Grid Array (BGA) or Chip Scale Package (CSP) to meet specific product requirements and ensure good soldering and packaging quality.
- Electromagnetic Compatibility (EMC): Take measures to reduce electromagnetic interference (EMI) and improve immunity to interference, including EMC analysis of wiring layouts and the use of shielding structures.
- Reliability: Consider environmental factors and stress during the design process, perform reliability analysis and simulations to ensure long-term stability and reliability of the product under various conditions.
In summary, designing 3D ceramic packages substrates requires considering multiple factors including dimensions, materials, interconnects, thermal management, component layout, packaging techniques, EMC, and reliability to achieve optimal performance and reliability.
What is the Fabrication Process for 3D Ceramic Packages Substrates?
The fabrication process for 3D ceramic packages substrates typically involves several key steps:
- Substrate Preparation: This step involves preparing the ceramic material to be used for the substrate. The ceramic material, such as alumina or aluminum nitride, is often in the form of sheets or blocks. These materials may undergo processes such as cutting, grinding, and polishing to achieve the desired dimensions and surface finish.
- Layer Deposition: Multiple layers of ceramic material may be deposited to create the substrate’s structure. This can be done through various techniques such as screen printing, tape casting, or chemical vapor deposition (CVD). Each layer may have specific features such as vias, traces, and pads, which are defined through patterning processes.
- Patterning: Patterning involves defining the features of the substrate layers, such as vias for interconnections and pads for component attachment. Techniques such as photolithography, laser ablation, or mechanical drilling may be used to create these features with high precision.
- Metallization: After patterning, the substrate layers are often metallized to provide conductive pathways for electrical connections. Metal layers, typically composed of materials like copper or gold, are deposited onto the substrate’s surface through techniques such as sputtering or electroplating. These metallized layers form the conductive traces and pads necessary for interconnecting components.
- Bonding and Stacking: Once the individual layers are prepared and metallized, they are bonded together to form the 3D structure of the substrate. This bonding process may involve techniques such as lamination, adhesive bonding, or brazing. The layers are stacked in the desired configuration, with interconnects aligned to facilitate electrical connections between them.
- Component Attachment: After the substrate structure is formed, electronic components such as semiconductor chips, resistors, capacitors, and inductors are attached to the substrate’s surface. This attachment may be achieved through techniques such as soldering, wire bonding, or flip-chip bonding, depending on the specific requirements of the application.
- Encapsulation: In some cases, the assembled substrate may be encapsulated to protect it from environmental factors such as moisture, dust, and mechanical stress. Encapsulation materials such as epoxy resins or molding compounds are applied to cover the substrate and its components, providing additional protection and mechanical support.
- Testing and Inspection: Finally, the fabricated 3D ceramic package substrate undergoes testing and inspection to ensure that it meets the required specifications and quality standards. Various tests may be conducted, including electrical testing, visual inspection, and reliability testing, to verify the substrate’s functionality, performance, and reliability.
Overall, the fabrication process for 3D ceramic packages substrates is complex and involves several sequential steps to create a functional and reliable substrate for electronic packaging applications.
How do you Manufacture a 3D Ceramic Package Substrate?
Manufacturing a 3D ceramic packages substrate involves several steps in the fabrication process. Here’s a general overview of the manufacturing process:
- Material Preparation: The process begins with the preparation of ceramic material, typically alumina (Al2O3) or aluminum nitride (AlN). Raw ceramic powders are mixed with binders and additives to form a slurry or paste.
- Green Forming: The prepared ceramic paste is then shaped into the desired substrate form using various techniques such as tape casting, screen printing, or injection molding. This step creates a “green” substrate with the desired dimensions and features.
- Drying: The green ceramic substrate is dried to remove moisture and solvents, leaving behind a solid green body.
- Lamination (for multilayer substrates): If the substrate requires multiple layers, individual green sheets are stacked and laminated together under pressure to form a multilayer structure. Each layer may contain conductor patterns, vias, and other features.
- Firing (Sintering): The green ceramic substrate or multilayer stack is then fired in a high-temperature furnace through a process called sintering. During sintering, the ceramic particles fuse together, and the organic binders and additives burn off, leaving behind a dense and rigid ceramic structure. The firing process also helps to define the final dimensions of the substrate.
- Surface Finishing: After sintering, the ceramic substrate may undergo additional processing steps such as polishing, grinding, or metallization. These steps help to achieve the desired surface finish and prepare the substrate for subsequent assembly processes.
- Metallization: Conductive metal traces, pads, and vias are added to the ceramic substrate surface through techniques such as thick-film or thin-film deposition, screen printing, or plating. These metallization layers provide electrical interconnections between components mounted on the substrate.
- Assembly: Semiconductor chips, passive components, and other electronic devices are mounted onto the ceramic substrate using soldering, bonding, or other assembly techniques. The substrate may also incorporate thermal management features such as heat spreaders, heat sinks, or thermal vias to dissipate heat generated by the components.
- Testing and Quality Control: The assembled substrate undergoes rigorous testing to ensure electrical connectivity, reliability, and performance. Various electrical, thermal, and mechanical tests may be conducted to verify the substrate’s functionality and adherence to specifications.
By following these steps, manufacturers can produce high-quality 3D ceramic packages substrates suitable for use in various electronic applications, including microprocessors, memory modules, sensors, and high-frequency devices.
How much should a 3D Ceramic Packages Substrate cost?
The cost of a 3D ceramic packages substrate can vary significantly depending on various factors such as the complexity of the design, materials used, manufacturing processes involved, and quantity ordered. Generally, 3D ceramic packages substrates tend to be more expensive compared to traditional substrates due to their advanced features and specialized manufacturing techniques.
Here are some factors that can influence the cost of a 3D ceramic packages substrate:
- Design Complexity: Substrates with intricate designs, multiple layers, and advanced features such as embedded components or high-density interconnects may incur higher manufacturing costs.
- Materials: The type and quality of ceramic materials used in the substrate can affect its cost. Higher-performance ceramics such as aluminum nitride (AlN) may be more expensive than alumina (Al2O3).
- Manufacturing Processes: The fabrication processes involved in producing the substrate, including shaping, firing, metallization, and assembly, contribute to the overall cost. Complex processes or specialized equipment may increase manufacturing expenses.
- Quantity: Economies of scale apply in manufacturing, so larger production quantities generally result in lower per-unit costs. Ordering larger volumes can lead to discounts from suppliers.
- Customization: Customized substrates tailored to specific requirements may involve additional engineering and setup costs, which can impact the overall price.
- Supplier and Location: Different suppliers may offer substrates at varying prices, and manufacturing costs can also differ based on factors like labor costs and overhead expenses in different regions.
- Quality and Reliability: Substrates manufactured to meet stringent quality standards and reliability requirements may command a higher price due to additional testing and quality control measures.
Given these factors, it’s challenging to provide a precise cost without specific details about the substrate’s specifications and intended application. Typically, prices for 3D ceramic packages substrates can range from a few dollars to several hundred dollars per unit, depending on the aforementioned factors. For accurate pricing, it’s advisable to consult with substrate manufacturers or suppliers and provide detailed specifications for a customized quote.
What is the base material for a 3D Ceramic Packages Substrate?
The base material for a 3D ceramic packages substrate is typically a ceramic compound. Two common ceramic materials used for this purpose are:
- Alumina (Al2O3): Alumina ceramic substrates offer excellent thermal conductivity, mechanical strength, and electrical insulation properties. They are widely used in electronic packaging applications due to their reliability and cost-effectiveness.
- Aluminum Nitride (AlN): Aluminum nitride ceramic substrates exhibit even higher thermal conductivity compared to alumina, making them particularly suitable for applications where efficient heat dissipation is critical. AlN substrates also offer good electrical insulation and mechanical stability.
Both alumina and aluminum nitride are chemically stable materials that can withstand high temperatures, making them ideal for use in semiconductor devices where thermal management is essential. The choice between these materials depends on specific application requirements such as thermal performance, electrical properties, and cost considerations.
Which company manufactures 3D Ceramic Packages Substrates?
Currently, many companies manufacture 3D ceramic packages substrates. Some of the major manufacturers include Kyocera, Murata, NGK Insulators, TDK, and Samsung Electro-Mechanics. These companies have extensive experience and advanced manufacturing technologies in the semiconductor industry, enabling them to produce high-quality 3D ceramic packages substrates to meet various electronic application needs.
Our company is also one of these manufacturers. We possess advanced technology and equipment, focusing on the research and development, as well as production of high-performance 3D ceramic packages substrates. As a leading manufacturer, we emphasize quality control and customer satisfaction, committed to providing customized solutions to meet specific application requirements.
Our manufacturing process strictly adheres to international standards and industry best practices, from raw material procurement to finished product delivery, all undergo stringent quality control. With an experienced team, we offer professional technical support and customized solutions to meet various needs for 3D ceramic packages substrates.
Whether in electronic communications, automotive electronics, medical devices, or industrial control fields, our company can provide high-quality 3D ceramic packages substrates, offering reliable support and solutions for our customers’ products. We are dedicated to establishing long-term partnerships with customers, driving the development and innovation of electronic technology together.
What are the 7 qualities of good customer service?
Good customer service is characterized by several key qualities that contribute to a positive experience for customers. Here are seven qualities of good customer service:
- Responsiveness: Good customer service involves being prompt and proactive in addressing customer inquiries, concerns, or requests. Responding promptly to customer queries shows that their needs are valued and helps to build trust and satisfaction.
- Empathy: Empathy is essential in understanding and relating to customers’ emotions, concerns, and situations. Good customer service representatives demonstrate empathy by actively listening to customers, showing understanding, and offering appropriate support and solutions.
- Professionalism: Professionalism entails maintaining a courteous and respectful demeanor when interacting with customers, regardless of the situation. This includes being knowledgeable about products or services, communicating clearly and effectively, and resolving issues efficiently.
- Reliability: Reliability involves consistently delivering on promises and commitments made to customers. Whether it’s meeting deadlines, providing accurate information, or resolving issues effectively, reliable customer service builds trust and confidence in the company.
- Flexibility: Good customer service requires flexibility to adapt to the unique needs and preferences of individual customers. This may involve offering personalized solutions, accommodating special requests, or being open to feedback and suggestions for improvement.
- Problem-solving skills: Effective problem-solving skills are crucial for resolving customer issues and concerns in a timely and satisfactory manner. Good customer service representatives are resourceful, creative, and proactive in finding solutions that meet customers’ needs and expectations.
- Consistency: Consistency in the quality of service provided is key to building long-term customer relationships and loyalty. Good customer service is consistent across all touchpoints and interactions with the company, ensuring a positive and cohesive experience for customers each time they engage with the brand.
By embodying these qualities, businesses can deliver exceptional customer service that enhances customer satisfaction, fosters loyalty, and contributes to overall success.
FAQs
What are 3D ceramic packages substrates?
3D ceramic packages substrates are specialized substrates used in electronic packaging, particularly in semiconductor devices. They provide a platform for mounting and interconnecting semiconductor chips in a three-dimensional structure.
What materials are used in 3D ceramic packages substrates?
Common materials used in 3D ceramic packages substrates include alumina (Al2O3) and aluminum nitride (AlN). These ceramic materials offer excellent thermal conductivity, mechanical strength, and electrical insulation properties.
What are the advantages of 3D ceramic packages substrates?
Some advantages of 3D ceramic packages substrates include high thermal conductivity, excellent electrical insulation, mechanical stability, and the ability to integrate multiple layers of circuitry and components in a compact form factor.
What applications are 3D ceramic packages substrates used for?
3D ceramic packages substrates are used in various electronic applications, including microprocessors, memory modules, sensors, RF/microwave devices, power modules, and LED packaging, among others.
What is the manufacturing process for 3D ceramic packages substrates?
The manufacturing process typically involves steps such as material preparation, green forming, drying, firing (sintering), surface finishing, metallization, assembly, and testing. Each step is crucial for producing high-quality substrates.
What are the design considerations for 3D ceramic packages substrates?
Design considerations include substrate dimensions, material selection, interconnect design, thermal management, component layout, packaging techniques, electromagnetic compatibility (EMC), and reliability.
Which companies manufacture 3D ceramic packages substrates?
Several companies manufacture 3D ceramic packages substrates, including Kyocera, Murata, NGK Insulators, TDK, Samsung Electro-Mechanics, and others.
What are the cost factors associated with 3D ceramic packages substrates?
The cost of 3D ceramic packages substrates depends on factors such as materials used, substrate dimensions, manufacturing complexity, volume production, and additional features such as embedded components or advanced thermal management structures.